航空齿轮是发动机中重要的传动元件,它的质量和性能严重影响发动机的使用寿命。齿轮性能是由材料的热处理和机械加工共同决定的,齿轮热处理是一项复杂的金相组织不断发生变化的过程,热处理的淬火温度、回火次数等对齿轮性能有着至关重要的影响,故以12Cr2Ni4A材料的航空齿轮为研究对象,基于deform有限元软件分析热处理参数对航空齿轮性能的影响规律,优化航空齿轮的热处理工艺,最后基于理论分析进行热处理试验,得到在满足使用要求的条件下,当淬火温度为800℃、回火2次时齿轮材料的各项性能达到最佳,验证了热处理分析的正确性,优化了齿面残余应力分布与微观组织分布,降低了磨削裂纹的发生几率。
01
引言
齿轮工作时转速高、传递功率大,承受着交变和冲击载荷,齿和齿之间互相啮合而产生齿面接触应力、齿根弯曲应力。对齿轮一般有以下几方面的要求:齿型面有足够的强度、抗磨损性能、硬度、接触疲劳性能、高的耐磨性以及良好的综合力学性能。上述要求通过热处理来实现,12Cr2Ni4A材料热处理的主要工艺,如表1所示。渗碳前的工艺可以改善零件的性能,渗碳是提高工件表面层含碳量的常用手段,渗碳后材料表层的硬度和耐磨性大幅提高,而芯部的韧性不受影响。深冷处理可以获得稳定的组织,提高材料的使用性能。
表1 12Cr2Ni4A材料热处理主要工艺
理想中的齿轮金相组织应为细针状马氏体、少量奥氏体与粒状碳化物的组合,在热处理时要避免发生碳化物的偏析。这是因为碳化物的偏析可使齿轮形成裂纹源,使材料横向和纵向力学性能差异增大,影响齿轮的工作性能。此外,要严格控制齿轮淬火后的残余奥氏体含量,使其维持在一个合理的水平,因为奥氏体属于不稳定的金相组织,齿轮在工作过程中,残余奥氏体会逐渐产生相变,转变为马氏体或其他组织。奥氏体与其他金相组织的体积密度不同会引发齿轮微观尺寸上的变化,齿轮体积的变化则会引起材料内部残余应力也随之发生变化,从而影响齿轮的寿命。文献以deform为研究工具,分析了均匀传热系数对SCr420H材料的齿轮应变分布的影响,能够对碳层和应变进行预测,文献通过deform有限元模拟热处理过程分析得到了减少工件和模具变形的锻造工艺,文献通过有限元分析了温度、应力等对材料组织的影响,文献通过试验分析了回火次数及温度等参数对不同材料的性能的影响,指出回火温度与次数对SKD61钢组织的影响规律,指出回火是导致材料高延展性的重要因素,文献研究了淬火温度对齿面硬度的影响规律,文献通过实验研究了不同的热处理对纳米结构氧化物弥散强化钢和42CrMoS4钢的晶粒尺寸的影响。他们虽然研究了热处理参数对各种钢材料性能的影响,但是并未涉及到齿面残余应力分布和微观组织分布,也并没有研究热处理工艺对磨削过程的影响,因此以12Cr2Ni4A材料的航空齿轮为研究对象,拟对航空齿轮的热处理工艺进行系统分析,研究淬火、回火工艺对齿面硬度、残余应力以及组织结构的影响规律,优化热处理工艺,提高齿轮的使用性能。
02
淬火工艺对齿轮性能的影响
12Cr2Ni4A材料的淬火温度在(780~840℃范围内,利用DE-FORM-3D建立了不同淬火温度下的齿轮热处理仿真模型,在其余工艺不变的前提下,研究淬火温度对齿面残余应力和硬度的影响规律。
在齿面随机选择若干组点,取其残余应力的平均值作为研究对象。不同淬火温度下残余应力沿齿厚方向的变化情况,如图1所示。随着淬火温度的升高,残余压应力有逐渐下降的趋势,到达820℃之后,变化趋于平缓。原因在于,随着淬火温度不断升高,齿轮中的热应力不断增加,由于热应力会导致材料表面产生拉应力,因此随着淬火温度的不断提高,材料表面的残余压应力逐渐下降。当淬火温度继续升高,材料的相变应力随之增加,与热应力发生中和,使得材料表面的残余应力趋于平稳。
图1 淬火温度对硬度和残余应力的影响
在齿面上随机选择若干组点,取其硬度的平均值作为研究对象。图 1 显示了不同淬火温度下齿轮硬度沿齿厚方向的变化情况。随着淬火温度的升高,齿轮的硬度不断增加,在 820℃时表面硬度达到了最大值 HRC 62.1,随后齿面硬度变化趋于平稳。原因在于,随着淬火温度的升高,材料内部合金元素的碳化物逐渐溶解,碳在奥氏体中的均匀度也慢慢提高。淬火后,马氏体中碳的饱和度也不断增大,因此随着淬火温度的不断升高齿轮的硬度不断增大,此后随着马氏体中碳的逐渐饱和,齿面硬度的变化也趋于平缓。
03
回火工艺对齿轮性能的影响
回火工艺主要是消除或减小残余应力,使材料组织细化,提高材料使用性能。回火后的组织以回火马氏体为主,硬度较淬火马氏体稍小。回火工艺中,相比于回火时间,回火次数、回火温度对于材料组织性能的影响更明显。文中建立了不同回火工艺下的齿轮热处理仿真模型,研究回火工艺对齿面硬度和组织性能的影响。
固定其余工艺不变,12Cr2Ni4A材料在不同回火温度下的齿面硬度变化分布,如图2所示。随着回火温度的提高,齿面硬度有所上升,在 400℃时齿面硬度达到最大值 HRC 61.1。随着回火温度继续提高,齿面硬度有所下降,550℃时,齿面硬度下降到为 HRC 54.3。出现上述现象的原因在于:随着温度上升,组织中马氏体分解,但此时残余奥氏体向下贝氏体转变,而下贝氏体的硬度要高于残余奥氏体,材料硬度反而有所上升;当温度超过 400℃时,马氏体分解的速度大于下贝氏体生成的速度,材料的硬度明显下降。
图2 回火温度对于硬度的影响
选择原有热处理工艺,研究回火次数对齿面残余应力的影响规律。12Cr2Ni4A材料在不同回火次数下的齿面残余应力曲线,如图3所示。随着回火次数的增加,材料结构变形逐渐恢复,齿面残余压应力有所下降,齿轮内部的残余应力得到了有效释放,说明材料组织结构的稳定性得到增强,对于提高齿轮的力学性能有一定的帮助。
图3 回火次数对于残余应力的影响
04
热处理工艺优化试验
试验方案与设备:从淬火温度对齿面硬度、回火次数对材料金相组织的影响规律出发,建立热处理优化方案的验证试验。结合仿真分析与生产经验,设置3个淬火温度,分别为800℃、820℃和840℃,回火次数设置为 0、1、2次,其余热处理工艺参数维持不变,试验方案, 如表2所示。
表2 试验方案设计
工件材料选择 12Cr2Ni4A,尺寸为60mm(长)×40mm(宽)× 30mm(高)。热处理试验是在石家庄科鑫齿轮加工厂进行的。部分样件和硬度检测装置,如图4所示。
图4 热处理试验样件和硬度检测装置
试验结果分析:淬火温度对试件表面硬度的影响: 取试件 5、2、8(淬火温度分别为 800℃、820℃、840℃,回火次数均为1次)进行显微硬度的检测,每个试件表面测量3个点,取其硬度的平均值作为该试件表面的硬度值,测量结果分别,如图5所示。
图5 试件5、试件2、试件8表面硬度及淬火温度与表面硬度间的关系
从图6可以看到,随着淬火温度的提高,试件表面的显微硬 度呈逐渐上升的趋势,试验结果与仿真分析得到的结果是一致的。试验样件的表面硬度值要高于对应淬火温度下的仿真数据,最大相对误差为 5.6%。
图6 试件1、试件5、试件9的金相组织
回火次数对金相组织的影响:对试件 1、5、9(回火次数分别为 0、1、2 次,淬火温度 800℃)进行金相组织检测。首先对试件进行线切割处理,再依次进行研磨、抛光、化学腐蚀,完成金相样件的制备。
在金相显微镜下对试件进行组织观测,如图6(×100)所示。
随着回火次数的增加,材料组织的均匀度逐渐提高,组织更加细化。具体来讲:0次回火的材料组织为板状马氏体+残余奥氏体+颗粒状碳化物,1次、2次回火的组织为针状马氏体+少量残余奥氏体+颗粒状碳化物。2次回火后的组织分布更加均匀,马氏体细化程度更高。板条状马氏体的组织性能较差,降低了材料的力学性能,在工件的磨削过程中,很容易产生磨削裂纹。而针状马氏体组织性能良好,均匀分布的针状马氏体可以很好地提升材料的力学性能,从而有效防止磨削裂纹的发生。
05
结论
(1)淬火温度由原有的 820℃降至 800℃,回火后,材料表面的残余压应力由15.5MPa提高至21MPa,齿面硬度由HRC 65下降至HRC 64。在硬度满足使用要求的前提下,提高齿面残余压应力,可有效预防磨削裂纹的产生;
(2)回火温度与回火时间保持不变,回火次数在原有1次的基础上增加到2次,2次回火后,齿面残余压应力略有下降,但回火后材料的组织分布更加均匀,材料的力学性能得到加强,提高材料的抗疲劳能力。
免责声明:本网站所转载的文字、图片与视频资料版权归原创作者所有,如果涉及侵权,请第一时间联系本网删除。
相关文章
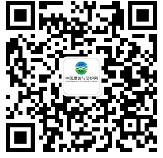
官方微信
《腐蚀与防护网电子期刊》征订启事
- 投稿联系:编辑部
- 电话:010-62316606-806
- 邮箱:fsfhzy666@163.com
- 腐蚀与防护网官方QQ群:140808414
点击排行
PPT新闻
“海洋金属”——钛合金在舰船的
点击数:8148
腐蚀与“海上丝绸之路”
点击数:6486