截至目前,国内外石油、天然气、输水矿浆等长输管线一般都采用碳钢钢管,但是碳钢易发生腐蚀,这不仅会造成巨大的资源浪费,还会给管线运营带来安全风险。
1953年,美国将环氧树脂涂敷于钢管内壁,这是世界上最早将涂层应用于输送管线的案例。之后,日本及一些欧洲国家也陆续开发了多种防腐蚀涂层和技术,钢管的防腐蚀技术得到了很好的发展。
20世纪80年代中期,曼内斯曼公司和巴斯夫化学工业公司共同推出挤压聚烯烃三层结构防腐蚀涂层,并逐步推广应用至今。
20世纪70年代,我国开始在部分城市管道上应用环氧煤沥青涂层,80年代才开始引进环氧树脂涂料技术并逐步推广使用。
碳钢的防腐蚀研究和施工技术从环氧煤焦油、环氧沥青、液态环氧树脂等逐渐发展为现在的熔结环氧树脂涂层、多层环氧涂层、三层聚乙烯涂层、三层聚丙烯涂层、五层聚丙烯涂层、七层聚丙烯涂层等等。目前,国内外大型输油输气管线如西气东输长输管线、陕京天然气管线、中俄天然气管线等,均采用环氧涂层。
不管是单、多层环氧体系的涂层,还是三层聚乙烯涂层、聚丙烯涂层,起到防腐蚀作用的都是与钢管基材直接作用的由熔结环氧粉末形成的涂层,即熔结环氧涂层。
1 熔结环氧涂层
熔结环氧涂料的主要成分为含有环氧基和羟基的酚醛环氧树脂或酚醛改性环氧树脂,以及胺类、酚类或醇类固化剂,它是一种通过混合、挤出、研磨得到的无挥发性有机物的固体粉末,能够以空气为载体进行输送和分散。将熔结环氧涂料施涂于已预热的金属基材表面,经熔化、流平、固化后会形成一道或多道均匀、致密的涂层,因此它也是一种热固性材料。熔结环氧涂层是环氧树脂和固化剂吸热发生加成反应后,形成的均匀致密、且连续稳定的涂层。
熔结环氧涂层的涂装工艺流程为:光管表面预清→光管中频预热→光管喷砂除锈→光管内吹扫→表面处理→中频加热→环氧涂料喷涂→涂层管冷却→管端预留处理→包装出厂。
对金属基材进行表面处理主要是去除基材表面的污染物,同时使表面呈粗糙状态,有助于涂层的附着。常用的表面处理工艺有化学预处理和机械预处理。其中,化学预处理包括溶剂清洗、磷酸化学预处理、铬酸盐处理等,机械预处理包括喷砂除锈、冲洗清理等。涂料喷涂前,对基材进行表面处理保证其达到良好的表面状态,达到除锈等级Sa2.5级以上,表面锚纹深度70 μm左右,表面灰尘度不超过1级的水平。
环氧涂料经过流化床充分流化,再通过专用喷枪,采用高压静电喷涂的方式喷涂至提前预热(预热温度为190~230 ℃)的基材表面,此时的基材已经过前文所述表面处理。环氧粉末粒子附着在基材表面,熔融结合固化后形成连续致密且有一定厚度的涂层。
2 钢质基材的腐蚀机理
金属腐蚀指金属与环境发生反应出现退化的现象,金属发生电化学腐蚀必须满足四要素,即整个腐蚀过程有阴极、阳极、反应回路以及电解液。从微观来看,在金属内部,电流从阴极流向阳极,在电解液中,电流从阳极流向阴极,形成了闭合回路,金属作为阳极流出电子,发生腐蚀。综上,抑制任一环节都可以使腐蚀减缓或趋于停止。
由上可见,隔绝金属材料与水和空气接触,避免金属表面形成阴极、阳极、反应回路和电解液,可有效防止腐蚀或者延缓腐蚀,这也是防腐蚀涂层的主要防护机理。因此,涂层和基材之间的有效结合是涂层具有防腐蚀性能的关键,故涂层与基材的附着力是评价涂层防腐蚀性能的重要指标。
3 熔结环氧涂层附着力的评价方法
01 热特性分析
热特性分析是评价熔结环氧涂层附着力的基本方法之一,主要目的是评价环氧粉末材料涂装后是否有效固化,若固化不完全将直接导致涂层附着力变差。
热特性分析是通过涂层的吸热特性分析其玻璃化转变温度的变化值(ΔTg)或固化度(C,又称为固化百分率)。通常来说,材料不可能百分百固化,一般当玻璃化转变温度的变化值不超过5 ℃或固化度不小于95%时,即可认为涂层已经固化完全。表1是不同标准中关于涂层的热特性要求。可以看出,各标准的取样方法以及升温降温程序基本一样。GB/T 23257-2017、CSA Z245.20-2014以及ISO 21809-2-2014标准中关于ΔTg的要求基本一致,但这些标准都没有对涂层固化度提出要求,在AS/NAZ 3862:2002标准中,除了对ΔTg提出了更加严格的要求外,对涂层固化百分率也提出了相应要求。
表1 各种标准中关于涂层热特性的要求
取同种粉末材料,分别于150 ℃和210 ℃下将其涂敷于基材表面(每个条件取3块平行试样),固化3 min后冷却,环氧涂层干膜厚度均为200~300 μm,分别进行热特性分析和环境暴露试验,热特性分析方法参照AS/NAZ 3862:2002标准,环境暴露试验是将试样置于大气环境中,每隔7天观察涂层腐蚀情况,结果如表2所示。
表2 不同涂敷温度下制得涂层的热分析结果和环境暴露试验结果
由表2可见:满足固化要求的涂层,其附着力的保持时间越长,防腐蚀性能越好。
02 热水煮浸泡
热水煮浸泡法也是评价环氧涂层附着力的重要方法之一,一般试验周期为24小时,试验温度为75 ℃或98 ℃,表3为不同标准中关于涂层热水煮浸泡法的具体要求。
表3 不同标准中关于涂层热水煮浸泡法的要求
矩型法(试样尺寸30 mm×15 mm)的具体评价标准为:
1级-涂层明显不能被撬剥;
2级-被撬离的涂层小于等于50%;
3级-被撬离的涂层大于50%但有明显的抗撬剥性;
4级-涂层很容易被撬剥成条状或大块碎屑;
5级-涂层成一整片被剥离。
V型法(试样尺寸20 mm×20 mm)的具体评价标准为:
1级-在“V”形划线的任意点上涂层没有明显的剥离,表面锚纹上完全附着涂层;
2级-涂层比较困难地出现小的碎屑状剥落,表面锚纹上附着涂层;
3级-涂层在刀尖撬剥的地方有碎屑状剥落,但面积范围不太大,表面锚纹上附着部分涂层;
4级-涂层成块状剥落,有很小的抗剥离性;
5级-在“V”形划线区域钢管表面涂层完全脱落。
国家标准、加拿大标准及国际标准中均规定热水煮浸泡法的温度为75 ℃,且均采用矩形方法评价,3级或4级均可视为合格。但澳大利亚标准则要求环氧涂层耐98 ℃的水,接近沸水浸泡,且评价采用V型方法,3级就视为不合格,评价标准更加严格。
热浸泡试验主要考察涂层在服役过程中的耐水渗透能力,耐水渗透是一个长期过程,一般随着温度升高,水分子运动越剧烈,扩散渗透能力越强,水浸泡时间越长,渗透能力也越强。进一步说,水浸泡时间越长,对涂层的耐水渗透能力的评估结果越稳定全面,因此,在很多项目的设计或涂层施工技术规范中,增加了28天或更长时间的水煮,浸泡温度不变,评价标准也不变。这是因为管线一旦服役,涂层耐水渗透就不会停止。
另外,在线或者现场对涂层附着力进行评价时,可以直接采用矩形法或V型法,不需要进行水煮试验,以方便快速对涂层进行初步评价。
03 阴极剥离法
阴极剥离也是评价环氧涂层附着力的重要方法之一,用来检验涂层的附着力性能及其在阴极保护系统中抗阴极剥离的能力,各标准中关于阴极剥离试验的具体试验方法及评价要求见表4。
表4 各标准中关于阴极剥离试验的具体试验方法及评价要求
管线在服役过程中,周围环境等都可能会为杂散电流或腐蚀电池的形成提供条件,管线铺设完成后大都采用阴极保护措施,这就需要涂层具有良好的抗阴极剥离性能。因此各标准中的试验方法都是模拟阴极保护过程,以观察和评价涂层的附着力和抗阴极剥离性能。
通常要求采用短期和长期的试验以完整评价涂层的这项性能,短期试验的电压高于长期试验,但某些标准中则采用控制电流来进行试验。但附着力的好坏最终都是根据距离中心漏点边缘的剥离宽度来评价的。根据具体的项目要求,试验温度等条件也可以依次改变。
笔者曾经完成的项目,要求环氧涂层厚度300 μm时,在98 ℃,48 h,1.5 V电压后涂层阴极剥离宽度最大值不超过3 mm,以及在98 ℃,28 d,1.5 V电压后的涂层阴极剥离宽度平均不超过7 mm,这是非常严格的要求,对涂层材料以及施工技术等都是很大的挑战。
综上所述,阴极剥离性能可以作为熔结环氧涂层的主要评价指标,评价涂层附着力的主要方法之一。
04 拉拔法
拉拔法也是评价环氧涂层附着力的常用方法之一,主要通过机械拉脱的方法,评价涂层和基材之间能够承受多少兆帕的强度,以及涂层是否有内聚破坏现象。
现在,多采用蘑菇头方法,参照GB/T 5210或者ISO 4624以及ASTM D4541等标准要求,在实际评价过程中,除了试验设备显示的拉脱强度读数值外,还应当评价拉脱后涂层的状态,包括涂层与基材分开、涂层与涂层分开、涂层与胶分开以及分开程度。
熔结环氧涂层与基材具有很好的附着力才能使熔结环氧涂层对基材起到防腐蚀作用。附着力评价方法包括热差分析法、热水煮、阴极剥离法和拉拔法等。那为什么熔结环氧材料能在碳钢表面良好附着呢?
4 熔结环氧涂层附着力的影响因素
01基材表面结构
附着氧化皮或锈蚀的金属基材表面在进行防腐蚀涂层施工前需预处理,其目的主要有二:一是去除基材表面的锈蚀或其他附着物,二是形成粗糙的表面轮廓。基材表面经过喷砂除锈后,通过除锈等级标准评价基材表面锈蚀或附着物的去除质量,完全去除表面锈蚀和附着物即为Sa3级或SSPC SP5级金属。通过锚纹深度检测标准评价基材表面粗糙度,包括纵向锚纹深度指标和横向峰数指标,传统复印胶带不能检测峰数指标,各标准或行业规范一般只侧重于锚纹深度指标,峰数指标很难实际测量。
表5是基于某电子测量仪测得的采用不同表面预处理方式处理后基材表面的锚纹深度和峰数,可以看出,同样的锚纹深度情况下,峰数值越高,基材表面轮廓越粗糙。即单位长度上不规则峰越多,单位面积上与涂层的附着面积越大,涂层的附着力越高。
表5 不同表面预处理方式处理后基材表面的情况
02 涂层和基材界面的表面能/次表面能
熔结环氧粉末在金属基材上的应用,最终体现于固体-固体界面,即环氧涂层固体界面与金属基材固体界面,主要指标是表面能和次表面能。
表面能是指产生(或扩张)单位表面积所需做的可逆功。粉末熔融附着于基材的过程中,粉末熔融,且由固态转变为熔融状态,金属基材的表面能远远高于环氧树脂材料,理论上,熔融状态的环氧粉末在胶化过程中,能够充分润湿基材。金属基材表面的附着物清理得越干净,其表面能越高,环氧粉末的熔融浸润越彻底,涂层的附着力越高。
比表面通常用来表述物质分散的程度,即单位体积(或质量)固体所具有的表面积。这也印证了上述,金属基材表面经过预处理后,表面轮廓质量越高,即锚纹深度越深,峰密度越大,基材的比表面越大,涂层的附着力越强。
03 材料的物理结构
熔结环氧树脂材料的种类很多,本工作以双酚A环氧树脂为例分析其对附着力的影响。
根据双酚A环氧树脂分子通式:
其中的环氧基和羟基具有高极性和活性和极强的反应性,这使固化物具有优良的黏接力和内聚力,这为环氧材料在金属表面形成化学键提供了可能,也有助于增强环氧材料固化后的附着力。同时,因为醚键和羟基等高极性基团的存在,环氧材料的浸润性和黏附能力得到提高,粗糙表面的润湿和浸润能力进一步增强。
04 基材显微组织的影响
长输管线一般多采用X45~X70级钢管,以西气东输管线用X70钢为例,其显微组织为针状铁素体,它们彼此咬合,相互交错分布,基体上分布着高密度缠结位错,这些微观因素赋予了针状铁素体钢管优良的强韧性能。那么,是否可以认为这种不规则的内部组织结构有利于环氧树脂粉末涂层的附着呢?
关于这一点,笔者以碳钢钢管和不锈钢光管为例进行研究,结果表明:碳钢钢管表面组织不规则排列,彼此咬合,高密度缠结位错;不锈钢钢管表面组织排列明显有差别,较碳钢基材组织缠结位错程度轻,相比于不锈钢管碳钢钢管更有利于涂层的附着。
前期实践经验表明:普通熔结环氧粉末材料并不能应用于不锈钢管或双相不锈钢管表面,但是改性环氧粉末能够很好地附着在双相不锈钢管表面。即能在碳钢钢管上良好应用的的熔结环氧粉末材料不能应用于不锈钢基材上,这与基材的显微组织有关,显微组织观察结果也印证了这一观点。
05 涂层+基材整体微观结构的影响
熔结环氧粉末在预热的基材上吸热,熔融、胶化、交联、固化形成一层高分子涂层,即防腐蚀涂层。
熔结环氧粉末在与基材结合的过程中,官能团如羧基具有极强的反应性,具有明显的电负性,非常容易与基材表面形成极性键。同时一般基材的预热温度为220~230 ℃,材料与基材接触的部位更有利于化学键合,粉末在固化过程中与基材接触界面形成化学键,更有利于熔结环氧树脂材料与基材的附着力的提高。
由图1可见:涂层与金属基材的结合面紧密无气孔,附着良好,两层间紧密附着无疏松多孔、缝隙、气泡等存在,涂层与基材结合紧密。
(a)200×
(b)500×
图1 涂层和基材结合处微观形貌
如果极性键和化学键存在,说明熔结环氧树脂与金属基材之间形成了分子与分子的结合,具有范德华力,这也是熔结环氧粉末涂层的附着力普遍高于液态环氧树脂涂层的重要原因。
结论
(1) 熔结环氧粉末材料应用于金属碳钢基材上,有优良附着力和防金属碳钢基材腐蚀的性能;
(2) 熔结环氧粉末材料本身的结构有助于在金属碳钢基材上良好附着。
免责声明:本网站所转载的文字、图片与视频资料版权归原创作者所有,如果涉及侵权,请第一时间联系本网删除。
相关文章
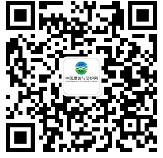
官方微信
《腐蚀与防护网电子期刊》征订启事
- 投稿联系:编辑部
- 电话:010-62316606-806
- 邮箱:fsfhzy666@163.com
- 腐蚀与防护网官方QQ群:140808414
点击排行
PPT新闻
“海洋金属”——钛合金在舰船的
点击数:8148
腐蚀与“海上丝绸之路”
点击数:6486