曹学文1,王凯1,尹鹏博1,秦思思1,李玉浩2
(1.中国石油大学(华东)储运与建筑工程学院,山东 青岛 266580;2.滨州学院 化工与安全学院,山东 滨州 256600)
摘 要:目的 通过研究美国腐蚀工程师协会(NACE)于2016年提出的适用于多相流管线的内腐蚀直接评价标准 SP0116-Multiphase flow internal corrosion direct assessment methodology for pipelines(以下简称MP-ICDA),探究该评价方法在国内的现场应用步骤,为国内内腐蚀直接评价方法提供参考。方法 以我国东海某海底管线的实际运行工况为基础,建立Norsok M506内腐蚀预测模型,利用流体动力学理论,模拟分析管线内腐蚀状况,结合评价标准的预评价、间接检测、详细检查及后评估四个步骤进行内腐蚀直接评价。结果 管线整体内腐蚀速率超过0.25 mm/a,腐蚀程度较严重。管道1.5~2.5 km低洼处及两侧立管处腐蚀速率明显增大,其腐蚀高危点与段塞流动状态、高持液率等流动参数有关。现场在线检测数据与模型预测结果基本一致,由此证明了模型的可靠性。根据腐蚀程度等级及标准规定的内腐蚀再次评估周期,确定管线再评估时间间隔为1年。结论 ICDA能够准确预测管线内腐蚀状态与风险大小,为无法实施内检测的管线提供了有效的内腐蚀评估方法,其对预测多相流管道腐蚀发生的位置与风险等级具有一定的指导作用与借鉴意义。流体的动力学参数对腐蚀速率影响较大,应用MP-ICDA方法时应选取合适的内腐蚀预测模型及管线运行参数。在海底管线正常运行期间,可对ICDA的结果进行多次循环校核,从而提高腐蚀预测的准确程度。
关键词:多相流;内腐蚀;直接评价;海管;MP-ICDA;Norsok M506
海底油气输送管道因具有输量大、方便快捷等特点,已成为海上油气田开发与生产不可或缺的生命线。在油气输送过程中,天然气中含有的CO2气体与凝析水或液膜结合,具有较强的腐蚀性,易导致管壁腐蚀,甚至引起油气输送管线腐蚀失效,进而引发危险事故[1-2]。Jepson等[3]阐述了段塞流型对油气输送管线的腐蚀机理,探究了段塞流动状态对腐蚀的影响规律。Muhammadu等[4]和Majed等[5]相继讨论了数值计算在腐蚀研究中的应用,分析了CO2腐蚀预测模型,对比了实验数据与数值模拟的可靠性。国内学者路民旭教授通过高温高压反应釜和电化学工作站,探究了高温高压状态下 CO2的腐蚀规律[6-7]。李悦钦教授采用壁厚检测与数值模拟结合的方法,讨论了CO2腐蚀-冲蚀共同作用对多相流管线的影响[8]。管道内部的腐蚀状况需要通过智能内检测的方式辨别管内缺陷和管壁变形,但许多在役管线因受管道设施、工艺条件及智能内检测器的适用性等方面影响,无法实施内检测作业。因此,需通过内腐蚀直接评价(ICDA)的方法对管线内部腐蚀状况进行合理预测,对管道的完整性进行评价,判别腐蚀程度等级,并提出针对腐蚀缺陷的控制与预防措施。美国腐蚀工程师协会(NACE)于 2016年提出了适用于多相流管线的内腐蚀直接评价标准:SP0116-Multiphase flow internal corrosion direct assessment methodology for pipelines(以下简称 MP-ICDA)[9]。该方法已在国外取得现场成功应用[10-12],但在国内还缺乏现场的应用经验。文中结合我国东海某混输海底管道的实际运行状况,对MP-ICDA进行了系统的研究与应用,重点分析了ICDA的关键环节——间接检测,为国内内腐蚀直接评价方法的实施提供一定的参考与指导作用。
1 MP-ICDA步骤
内腐蚀直接评估方法用于评定管道内部腐蚀敏感位置的原理在于,假设积液的存在是腐蚀存在的首要条件[13],对于某些起伏较明显的管道,水相在重力和气相流体带动两方面的作用下,无法被携带走而积聚,与介质中的酸性气体反应,导致金属腐蚀。采用内腐蚀直接评估方法推荐的多相流模型[14],可通过评估积水优先位置,判断内腐蚀发生的敏感位置。如图1所示,内腐蚀直接评价方法主要包括预评价、间接检测、详细检测与后评价四个步骤:
1)预评价。该环节需对多相流管线的基本信息进行收集,筛选出有效、可利用的部分,并对ICDA进行可行性分析。
2)间接检测。间接检测是 MP-ICDA方法的核心步骤,其目的是通过多相流模拟、腐蚀速率预测以及影响腐蚀分布的因素,来识别每个MP-ICDA区域中最可能发生内腐蚀或者已经发生内腐蚀的MP-ICDA子区域。
3)详细检测。采用无损检测(NDE)技术[15-16]对腐蚀预测模型预测的腐蚀高危点进行现场检测,验证模型预测结果的可靠性。
4)后评价。该环节主要分析 MP-ICDA方法对管线实际应用的有效性,并确定再次评估的最小时间间隔。
图1 多相流内腐蚀直接评价流程
2 案例分析
以我国东海某油气水多相混输海管为研究对象,应用MP-ICDA方法,具体分析海管内腐蚀情况。
2.1 预评价
该油气水混输管道于2006年投产,设计寿命20年,全长约6 km。管道钢级为API 5L X52,外径为219.1 mm,壁厚为12.7 mm,单层不保温,设计腐蚀裕量为3 mm。设计压力为3 MPa,最大进口压力为1.9 MPa,管线无内涂层。图2为管道沿线高程。管线实际运行参数见表1,外输气质分析见表2。
图2 管道沿线高程
表1 运行参数
表2 气体组分
经管道预评价分析,该管线的气液比 GLR=40<5000,属于MP-ICDA标准适用范围,因此采用MPICDA对该条管道进行评价。除满足气液比条件之外,在应用MP-ICDA标准时,应该符合表3所示的要求。
表3 可行性分析
2.2 间接检测
MP-ICDA间接检测阶段关键部分是腐蚀速率预测。通过多相流模拟得到管段沿线温度、压力、气液表观流速、持液率及流型等参数,在分析管道水动力特征的基础上,结合腐蚀发生机理,计算子区域腐蚀速率,以确定腐蚀倾向最为严重的位置。MP-ICDA标准推荐了包括 Norsok M506模型在内的多种腐蚀预测模型(ICPM),本文采用多相流仿真OLGA软件[17-18]腐蚀模块(Corrosion module)的 Norsok M506[19]模型来模拟分析管线运行状况,评估管道内腐蚀状态。
2.2.1 Norsok M506模型
Norsok M506腐蚀预测模型是目前国际上使用最广泛的经验模型。该模型综合考虑了温度、pH值、表观流速与剪切力等多方面因素对腐蚀的影响,适用于预测 5~150 ℃温度范围内 CO2腐蚀环境下的管道腐蚀速率。
当温度为5 ℃时:
当温度为15 ℃时:
当温度为 20、40、60、80、90、120、150 ℃时:
式中: f C O2为修正后的 CO2分压(由式(4)算得),Pa;S为壁面剪切力,Pa;Kt为与温度有关的常数(见表4);f (pH)t为温度t时的pH影响因子;CRt为腐蚀速率,mm/a。
式中:T为温度,K;p为系统总绝对压力,Pa;PC O 2为CO2分压,Pa。
表4 Norsok M506模型中Kt取值
2.2.2 流体动力学分析
根据管道基础数据输入模型涉及的各项参数:管道入口温度设置为21 ℃,海床温度为18 ℃,管线出口压力设置为1.05 MPa,输气量为1340 m3/d,输油量为35 m3/d,含水率设为0.4%。Norsok M506模型中的CO2摩尔分数(CO2 fraction)设置为2.04%,单相液流中的最大CO2分压设为1 MPa。根据现场水质检测数据,HCO3-含量(Bicarbonate)设置为0.0074 mol/L。由于现场实际运行中未加注缓蚀剂,因此模拟时缓蚀剂效率(Inhibitor efficiency)设置为0。
从图3可以看出,管道沿线温度、压力在两侧立管处波动较为明显,在海底平管处,随管线里程的增加而缓慢降低,在1.5~2.5 km陡坡处降低减缓。从图4中可知,管内气相表观流速在两侧立管处变化较大,在海底平管处,随管线里程的增加而缓慢增大,这主要是由地形起伏和流型引起。管内液相表观流速在平管处波动缓慢,在入口立管段上升较快,这是由于液相重力势能转换为动能的缘故。
图3 管道沿线温度、压力的变化
图4 管道沿线气液相表观流速的变化
从图5可以看出,管内气液相流型在管道多处出现了段塞流和气泡流流型,其余位置均为分层流。在管道低洼处,由于液体积聚较多,气体较少,气体进入液体之中形成气泡流;当气体较多时,也会形成段塞流。管内介质液相pH值在两侧立管处变化较明显,平管处基本维持在4左右。因CO2的存在,使得流体酸性较强,对管线具有较强的腐蚀性。从图6中可以看出,管内持液率在出入口立管处以及1.5~2.5 km陡坡处出现剧烈的变化,其余位置持液率较为稳定。水膜速度变化与管内持液率趋势大致相反。
结合仿真得到的管道沿线腐蚀速率变化(见图7)可知,水膜速度与管道腐蚀速率变化趋势基本一致,水膜速度增大,管道腐蚀速率亦随之增大。管道沿线腐蚀速率在1.5~2.5 km陡坡段出现峰值,这与此处流型、持液率以及气液相表观流速等因素均有关。整体来看,在管线地势由高到低时,腐蚀速率增大,且管道低洼处腐蚀风险较高。在分层流条件下,流速较低,气相在上,液相在下,只发生电化学反应,腐蚀速率较低,呈轻度腐蚀。在段塞流条件下,气液流速变化较大,对管道的腐蚀严重,在管道低洼处有积液,CO2腐蚀速率较大。因此,管道低洼处及两侧立管处腐蚀风险较高。由于管内介质有腐蚀性,未采取防腐措施,管道整体腐蚀速率大于0.25 mm/a。根据GB/T 23258—2009《钢制管道内腐蚀控制规范》[20],该海管腐蚀程度处于严重腐蚀。
图5 管道沿线流型、液相pH的变化
图6 管道沿线持液率、液膜速度的变化
图7 管道沿线腐蚀速率的变化
2.3 详细检查
依据间接检测阶段确定的腐蚀速率分析可知,海管详细检查点依次为海管立管段及 1.5~2.5 km陡坡处。受工艺条件限制,平管不能实施内检测作业,因此采用立管检测的方法进行局部腐蚀检测。采用国际先进的远程涡流(RFT)智能检测器带缆检测立管,发现立管存在多处腐蚀缺陷导致的壁厚减薄,如图8所示。检测数据显示出有12处发生壁厚减薄,其中有7处中等壁厚减薄(20% WL~39% WL),5处高程度壁厚减薄(40% WL~59% WL),缺陷点平均剩余壁厚为63%。从管道投产至今,经计算得出立管段平均腐蚀速率约为0.44 mm/a,与模拟结果基本一致。
图8 立管内检测结果
2.4 后评估
MP-ICDA方法的有效性取决于详细检测的结果与腐蚀预测结果的相关程度。图7与图8数据的对比结果表明,内腐蚀预测模型结果与立管内检测结果基本一致,在MP-ICDA标准规定的误差允许范围内。因此该模型是有效的,也再次验证了MP-ICDA的可靠性。该海管腐蚀程度较为严重,建议加强评估频率,再评估间隔为1年。
3 结论
1)通过Norsok M506内腐蚀预测模型对海底管线进行内腐蚀模拟仿真与高腐蚀风险点预测,结果表明,该海底管线整体腐蚀程度较为严重,腐蚀高危点与段塞流动状况、高持液率等流动参数有关,立管段与低洼段腐蚀速率较大。因此应及时采取通球清管作业与加注缓蚀剂的措施清除管道积液,控制管壁内腐蚀。
2)根据现场立管在线检测数据可知,间接检测的结果与模型预测结果基本一致。由此证明了模型的可靠性,进而表明MP-ICDA方法能够较准确地反映管线实际内腐蚀状态,这对预测海底多相流管道腐蚀发生的位置与风险等级具有一定的指导作用与借鉴意义。
3)MP-ICDA方法的关键环节是间接检测阶段的腐蚀速率预测,流体的动力学参数对腐蚀速率影响较大。因此应用MP-ICDA方法时应选取合适的内腐蚀预测模型及管线运行参数。在海底管线正常运行期间,可对ICDA的结果进行多次循环校核,从而提高腐蚀预测的准确程度。
参考文献:
[1]薛丹,胡敏.陕北气田气井腐蚀速率影响因素及规律[J].表面技术,2016,45(2):169-174.XUE Dan,HU Min.Factors and rules affecting gas well corrosion rate in Shanbei gas field[J].Surface technology,2016,45(2):169-174.
[2]崔铭伟,曹学文.腐蚀缺陷对中高强度油气管道失效压力的影响[J].石油学报,2012,33(6):1086-1092.CUI Ming-wei,CAO Xue-wen.Impact of corrosion defects on failure pressure of medium-high strength oil-gas pipelines[J].Acta petrolei sinica,2012,33(6):1086-1092.
[3]JEPSON W P.Slug flow characteristics and their effect on corrosion rates in horizontal oil and gas pipelines[C]//SPE annual technical conference and exhibition.Washington:[s.n.],1992.
[4]MUHAMMADU M M,SHERIFF D J,HAMZAH E.Effect of flow pattern at pipe bends on corrosion behaviour of low carbon steek and its challenges[J].Science &engineering,2013,63(1):55-65.
[5]MAJED R A,JAWAD A H,JOMAA D M.Experimental and numerical study of CO2 corrosion in carbon steel[J].Eng &Tech Journal,2013,31(15):99-112.
[6]蔡峰,柳伟,路民旭,等.高温高压喷射湍流区中 X70管线钢 CO2腐蚀电化学特征[J].物理化学学报,2013,29(5):1003-1012.CAI Feng,LIU Wei,LU Min-xu,et al.Electrochemical corrosion behavior of X70 pipeline steel in turbulence zone under jet impingement at high temperature and high pressure CO2 environment[J].Acta physico-chimica sinica,2013,29(5):1003-1012.
[7]林学强,柳伟,路民旭,等.含O2高温高压CO2环境中3Cr钢腐蚀产物膜特征[J].物理化学学报,2013,29(11):2405-2414.LIN Xue-qiang,LIU Wei,LU Min-xu,et al.Characteristics of corrosion scale of 3Cr steel at high temperature and pressure in an O2 and CO2 environment[J].Acta physicochimica sinica,2013,29(11):2405-2414.
[8]李悦钦,古丽,王亚丽,等.高温高压含 CO2气田碳钢管线腐蚀-冲刷作用定量分析[J].腐蚀与防护,2013,34(10):909-913.LI Yue-qin,GU Li,WANG Ya-li,et al.Quantitative analysis of steel pipeline corrosion-erosion in high temperature and high pressure environments containing CO2[J].Corrosion &protection,2013,34(10):909-913.
[9]NACE SP0208—2008,Multiphase flow internal corrosion direct assessment methodology for pipelines:SP0116[S].
[10]OLIVER M,PHIL D,LEE N,et al.Internal corrosion direct assessment of gas transmission pipelines[J].Corrosion &protection,2002,234(33):31-35.
[11]OLIVER M,BRUCE C,LAURIE P,et al.Internal corrosion direct assessment of gas transmission pipelines application[C]// Corrosion 2007.Houston:NACE International,2007.
[12]OLIVER M,DEANNA B,RICK E,et al.Internal corrosion direct assessment for pipelines carrying wet gasmethodology[C]// Corrosion 2007.Houston:NACE International,2007.
[13]郭秋月,刘磊,郭新锋.天然气管道内腐蚀直接评价方法原理与范例[J].焊管,2011,34(3):65-70.GUO Qiu-yue,LIU Lei,GUO Xin-feng.Principle and exemplification of the direct assessment on the internal corrosion of dry gas pipeline[J].Welded pipe and tube,2011,34(3):65-70.
[14]张国安,陈长风,路民旭,等.油气田中 CO2腐蚀预测模型[J].中国腐蚀与防护学报,2005,25(2):35-37.ZHANG Guo-an,CHEN Chang-feng,LU Min-xu,et al.Prediction model of CO2 corrosion in oil and gas field[J].Journal of Chinese society for corrosion and protection,2005,25(2):35-37.
[15]赵国权,王国栋,谭吕,等.非接触式磁力扫描技术在渤海油田海管检测中的应用[J].航海工程,2015,44(6):141-143.ZHAO Guo-quan,WANG Guo-dong,TAN Lv,et al.Application of the non-contact magnetic scanning technology in detection of sea tube in Bohai oil field[J].Navigation engineering,2015,44(6):141-143.
[16]杨巍,马洪新,郭斌,等.基于远场涡流检测技术的海管立管内检测方案[J].油气储运,2015,34(7):768-770.YANG Wei,MA Hong-xin,GUO Bin,et al.Inline inspection on riser of submarine pipeline based on remote field eddy current detection technique[J].Oil &gas storage and transportation,2015,34(7):768-770.
[17]周晴.油气田开发中的 CO2腐蚀与控制[J].油气田地面工程,2005,24(11):46.ZHOU Qing.CO2 corrosion and control in oil and gas field[J].Oil and gas field surface engineering,2005,24(11):46.
[18]赵学清.WC19-1B至WC19-1A海底混输管道内腐蚀状态评估技术研究[D].成都:西南石油大学,2014.ZHAO Xue-qing.The research on internal corrosion state evaluation technology of WC19-1B to WC19-1A subsea mix pipeline[D].Chengdu:Southwest Petroleum University,2014.
[19]Norsok standard M-506,CO2 corrosion rate calculation model[S].
[20]GB/T 23258—2009,钢制管道内腐蚀控制规范[S].GB/T 23258—2009,Code for internal corrosion control of steel pipeline[S].
免责声明:本网站所转载的文字、图片与视频资料版权归原创作者所有,如果涉及侵权,请第一时间联系本网删除。
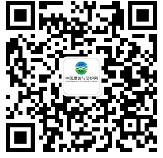
官方微信
《中国腐蚀与防护网电子期刊》征订启事
- 投稿联系:编辑部
- 电话:010-62316606-806
- 邮箱:fsfhzy666@163.com
- 中国腐蚀与防护网官方QQ群:140808414