7N01铝合金具有比强度高、密度低的优点,在高速列车制造业的车体轻量化中得到广泛应用。7N01铝合金时效过程中析出物的析出顺序依次为过饱和固溶体、GP区、η‘相和η相。在国内目前的高速列车车体生产中,常采用钨极惰性气体保护焊(TIG)、熔化极惰性气体保护焊(MIG)、激光焊(LW)和搅拌摩擦焊(FSW)等焊接方法对7N01铝合金进行焊接。MIG因具有操作相对简单、成本低的优点,被广泛用于不同尺寸结构的焊接中。
对于高强度铝合金,其焊接接头的疲劳行为和疲劳裂纹萌生、扩展等微观机理成为近年来的研究热点。目前,国内已有许多学者对7N01铝合金焊接接头的疲劳性能进行了研究,但大多数研究都集中于薄板及中薄板(厚度t小于6mm) ,关于中等厚度(6mm<t<40mm)7N01铝合金焊接接头疲劳性能的研究较少。国内外高速列车承力构件大都采用7XXX系铝合金来制造,且会用到中等厚度的7N01铝合金。关于铝合金焊接接头疲劳损伤的研究,大多集中于裂纹起源阶段,对于裂纹扩展阶段二次微裂纹的成因对整体疲劳性能影响的研究较少。来自上海工程技术大学材料工程学院的范聪、杨尚磊等人在7N01铝合金MIG焊接参数研究的基础上,对12mm厚的7N01-T5铝合金板进行焊接,观测其焊接接头的显微组织,再对MIG焊接接头进行拉伸及疲劳测试,结果可为中厚7N01铝合金中厚板MIG焊接接头的疲劳性能研究提供试验依据及参考。
Part 01
试验材料与试验方法
1.1 试验材料
母材为12mm厚的7N01-T5铝合金板。焊丝选用的是直径为1.6mm 的ER5356铝合金,该焊丝的主要成分为镁元素。
1.2 试验方法
图1 焊接试验过程示意
焊接试验过程如图1所示,焊接试样为两块12mm厚的7N01铝合金板,采用MIG以X形坡口的对接方式焊接,单边角度为35°。焊接工艺参数如表1所示,为保证焊接质量,进行焊接时环境的相对湿度小于70%,焊前去除板材表面油污和氧化膜。
表1 焊接工艺参数
采用线切割的方式从焊接接头中截取金相试样,先对试样进行打磨,随后使用抛光机进行抛光,直至表面光滑,最后使用Keller试剂腐蚀试样表面,使用超景深显微镜观察焊接接头显微组织。根据标准GB/T 2651—2008 《焊接接头拉伸试验方法》和GB/T 24176—2009 《金属材料疲劳试验数据统计方案与分析方法》对焊接接头进行拉伸和疲劳试验,拉伸及疲劳试验试样尺寸示意如图2所示。
图2 拉伸及疲劳试验试样尺寸示意
所有拉伸及疲劳试验均在温度为23℃,相对湿度为40%的环境下,采用伺服液压万能试验机进行试验,其中拉伸试验以0.1kN/s的加载速率进行3次试验,结果取平均值,疲劳试验施加拉-拉正弦波形载荷,频率为140Hz,应力比为0.1。
拉伸及疲劳试验结束后,立即在干燥环境下采用扫描电子显微镜(SEM)观察疲劳断口,避免断口氧化带来的影响。
Part 02
试验结果与讨论
2.1 7N01铝合金显微组织形貌
焊缝中心、熔合区显微组织形貌和等轴晶形成过程示意如图3所示,焊缝中心金属主要由ER5356填充材料熔化而成,形成了粗大的等轴状组织,呈雪花状。等轴晶的存在说明在焊缝中心发生了自由结晶。焊缝中心的温度梯度小,受边缘散热条件的影响较小,液相中能形成较宽的成分过冷区,在随后的冷却过程中,新生成的晶粒能够自由生长,从而呈现等轴状。
图3 焊缝中心、熔合区显微组织形貌和等轴晶形成过程示意
由图3b)可知,靠近焊缝边缘有一条很窄的熔合线,其中分布着许多细小的组织。焊缝边缘近熔合线的焊缝组织为取向明显的柱状晶,这是因为液态金属依附于金属间化合物的表面形核,析出与母材未熔化晶粒取向相同的柱状晶。在熔合线的左侧可以发现存在明显的联生结晶现象。
图4 焊接热影响区及母材的微观形貌
图4为焊接热影响区及母材的微观形貌。由图4a)可知,靠近焊缝部位的固溶区组织的晶粒尺寸细小,约为45μm。在焊接热源作用下,位于焊缝的热影响区内的镁、锌元素固溶到铝基体中,并在随后的快速冷却过程中形成过饱和固溶体,镁、锌元素在铝基固溶体的一定结晶面上偏聚并有序化,从而形成固溶区。软化区内晶粒尺寸粗大,约为75μm。图4c)为接头母材的显微组织,母材组织为细长的轧制态晶粒,沿着轧制方向伸长。
2.2 7N01铝合金MIG焊接接头拉伸性能分析
焊接接头、热影响区和母材的拉伸试验结果如图5所示。由图5可知,焊接接头的抗拉强度远低于母材的抗拉强度,焊接接头的抗拉强度为259MPa,屈服强度为137MPa,延伸率为11.4%,接头塑性较好。
图5 焊接接头、热影响区和母材的拉伸试验结果
图6为焊接接头拉伸断口微观形貌,从图中可以观察到大量形状较为规则,形貌差别不大的韧窝,这些韧窝的尺寸约为10μm,为标准的等轴韧窝。焊接接头在拉伸正应力下,试样总变形与局部区域变形的不一致使材料内部分离形成显微孔洞,并在正应力的作用下逐渐长大。在随后的拉伸过程中,显微孔洞受到横向的剪切应力并发生滑移,相邻孔洞之间的基体横截面积不断缩小,出现颈缩现象,最后断开使得孔洞相连。当越来越多的孔洞彼此相连后,试样便发生断裂。
图6 焊接接头拉伸断口微观形貌
在图6中还可以观察到一些二次裂纹,这些二次裂纹的萌生位置集中在断口的解理台阶处,由于拉应力的大部分能量都提供给主裂纹扩展,因此这些二次裂纹在萌生之后没有扩展。由图6可知,接头断口分布着大量的韧窝,其中还掺杂着部分解理台阶和二次裂纹,解理台阶为脆性断裂的典型特征,由此可以判断7N01铝合金MIG焊接接头的拉伸断裂形式为韧窝为主的韧性断裂和兼有少量脆性断裂的韧脆混合形式。
2.3 7N01铝合金MIG焊接接头疲劳性能分析
图7 焊接接头疲劳试验断裂截面宏观形貌
图7为焊接接头疲劳试验断裂截面宏观形貌。由图7可知,裂纹位于焊缝区域,说明焊缝为接头的最薄弱处,这与硬度试验结果相符。疲劳寿命N与应力幅S之间的联系,可用式(1)来表达。
图8 母材和焊接接头的应力幅-疲劳寿命拟合曲线
根据得到的疲劳试验数据,利用ORIGIN软件对疲劳试验数据进行拟合,拟合曲线如图8所示,所得曲线对应的拟合公式分别如式(3)和式(4)所示。
由图8可知,随着应力幅的降低,7N01铝合金母材及焊接接头的疲劳寿命明显增加。母材的k值小于焊接接头的,这说明随着应力幅的增加,焊接接头疲劳寿命下降得更快。
图9 7N01铝合金焊接接头疲劳断口微观形貌
图9为7N01铝合金焊接接头疲劳断口的微观形貌。由图9a)可知,接头裂纹源区无明显导致裂纹萌生的缺陷,根据其放射性条纹可以推断,疲劳裂纹萌生于表面处,并向内部扩展。在试样断口表面有很多较为平坦的准解理面,小平面之间以撕裂方式相接,因此判断接头的断裂方式以准解理断裂为主。
从图9可以观察到疲劳条带表面光滑且相互平行,疲劳条带间分布着较多二次相和微裂纹,二次相形貌呈白色颗粒状,直径约为2.5μm。对图9c)中的二次相进行能谱分析,结果表明该相为含Fe相。LIN等认为含Fe相为硬脆易碎相,在疲劳裂纹扩展过程中易发生破碎,从而诱发微裂纹的萌生,微裂纹会增大疲劳裂纹的扩展速率,从而缩短试样的疲劳寿命。图9d)为瞬断区的微观形貌,可以清晰地观察到大小不一的等轴韧窝。韧窝底部存在二次相,这些二次相是产生韧窝的主要原因。
2.4 疲劳裂纹稳定扩展区微裂纹萌生及扩展分析
疲劳条带间围绕二次相的微裂纹形貌如图10所示,该微裂纹的长度约为2μm。根据图中单个疲劳条带的宽度和式(5)可以推断出疲劳裂纹扩展速率。
图10 疲劳条带间围绕二次相的微裂纹形貌
在循环载荷的作用下,二次相对位错运动具有一定的钉扎作用,当钉扎作用超过一定范围时,二次相与周围基体产生裂纹。
图11 二次相所致裂纹的萌生机理
二次相所致裂纹的萌生机理如图11所示。在第一阶段,位错线在循环载荷的作用下不断运动;在第二阶段,由于二次相对位错运动的钉扎作用,位错线遇到二次相时发生部分弯曲;在第三阶段,位错线与二次相刚开始接触时,位错线在二次相周围仅发生部分变形。随着循环载荷的加载,位错线发生剧烈弯曲,最后位错线在二次相周围首尾相接,形成一个包围二次相的位错环。
Part 03
结论
(1) 中厚板7N01铝合金MIG焊接接头焊缝区的显微组织以等轴晶为主;熔合区的显微组织为取向明显的柱状晶;热影响区晶粒尺寸较为粗大,形貌与母材轧制态组织相似。
(2) 12mm厚7N01铝合金MIG焊接接头、热影响区及母材的抗拉强度分别为259,356,402MPa。其中接头的延伸率为11.4%,塑性较好。通过拉伸断口分析可以判断接头拉伸断裂形式为韧脆混合形式。
(3) 通过对疲劳试验拟合曲线的分析,发现随着应力幅的降低,中厚板7N01铝合金母材及焊接接头的疲劳寿命明显增加,随着应力幅的增加,焊接接头疲劳寿命下降得更快。
(4) 微裂纹会加速疲劳裂纹的扩展。在疲劳断口的裂纹稳定扩展区,疲劳条带间存在二次相,进而提出了因二次相导致的微裂纹萌生模型。当位错环聚集所引起的应力超过一定范围时,会在二次相与材料基体交接的应力集中处产生微裂纹。
免责声明:本网站所转载的文字、图片与视频资料版权归原创作者所有,如果涉及侵权,请第一时间联系本网删除。
相关文章
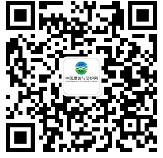
官方微信
《中国腐蚀与防护网电子期刊》征订启事
- 投稿联系:编辑部
- 电话:010-62316606-806
- 邮箱:fsfhzy666@163.com
- 中国腐蚀与防护网官方QQ群:140808414
点击排行
PPT新闻
“海洋金属”——钛合金在舰船的
点击数:7966
腐蚀与“海上丝绸之路”
点击数:6355