铝是现代工业体系中应用十分广泛的金属元素,在金属材料中的使用量仅次于钢铁[1]。铝合金具有高比强度、低密度、低熔点、优良的加工性能及耐腐蚀性能等特点[2],随着全球能源和环境问题日益突出,其在机械、建筑、电器、交通运输、复合材料、涂层材料等领域发挥着愈加重要的作用[3-4],尤其是在防腐喷涂材料方面,铝合金具有得天独厚的优势,热喷铝涂层被广泛应用到结构钢的防腐工程中。
铝合金因其表面会形成一层非常致密的氧化膜,隔绝了铝基体和外界环境的直接接触,因此其有着良好的耐腐蚀性能。但是在某些环境状况较差,频繁出现酸雨、大雾等极端天气的地区,环境中的SO42- 、Cl-等具有一定腐蚀性的阴离子破坏铝合金表面的氧化膜,导致其出现点腐蚀等多种形式的腐蚀现象[5]。目前,对铝合金暴露在不同环境中的腐蚀行为的研究已有很多报道,杨敏杰[6]对7075 铝合金在3.5%NaCl 溶液中的腐蚀规律随时间的变化进行了探究,发现在腐蚀初期,由于7075 铝合金氧化膜的阻隔,其腐蚀速度非常缓慢,而在氧化膜被破坏后,基体暴露在腐蚀坏境中,腐蚀速度加快。侯丹丹[7]研究了6082 铝合金的晶间腐蚀行为,结果显示,腐蚀初期,纵向腐蚀深度逐步增加,随着腐蚀时间的延长,纵向腐蚀深度的增加幅度变得很小,横向腐蚀范围和腐蚀程度会逐渐加大。Zhao 等[8]探究了7A85铝合金在青岛工业-海洋大气环境中的腐蚀行为及机理,结果表明,裸露的7A85 铝合金在工业-海洋大气环境中会发生点腐蚀和晶间腐蚀,其力学性能随着腐蚀时间延长逐步恶化。目前国内外对于铝合金在高腐蚀性环境中的腐蚀行为研究报道很少,对铝合金在高腐蚀性条件下的腐蚀机制研究也比较少[9],缺乏对高腐蚀性环境铝合金的腐蚀规律的认识。因此,笔者将多种铝合金在高腐蚀性环境中长时间浸泡腐蚀,通过研究铝合金在高腐蚀性环境中表征和力学性能的变化来探究铝合金在高腐蚀性环境中的腐蚀规律,为选择耐腐蚀性能良好的热喷涂材料提供依据。
1 实验材料与方法
1.1 实验材料
腐蚀实验所采用的材料为某公司提供的6 mm 板厚的6061 铝合金、7075 铝合金及2195铝锂合金板材,其中6061 铝合金为6XXX 系列铝合金,其主要合金元素有Al、Mg、Si 等3 种元素。7075 铝合金和2195 铝锂合金为高强铝合金,2195 铝锂合金主要合金元素为Al、Cu、Li、Mg、Ag 等5 种元素,7075 铝合金主要合金元素有Al、Zn、Mg、Cu 等4 种元素。3 种合金的成分表1~3 所示。
1.2 实验过程
参照GB/T 19745-2018,本次腐蚀试验所选用的腐蚀溶液的配比为1 L 5%NaCl 溶液+2 mL 硝酸(HNO3, ρ=1.42 g/mL)+5 mL 硫酸(H2SO4,ρ=1.84 g/mL),然后加入适量的NaOH 溶液来调节溶液的PH 值到规定值3.5。分别选取10 mm?10 mm?6 mm(板厚)6061铝合金、2195 铝锂合金和7075 铝合金的块状试样及特定尺寸的拉伸试样进行浸泡腐蚀试验,试验时间为0,6,12,24,48,96,168 h。实验前依次用600#、1000#和1200#砂纸打磨块状试样和拉伸试样,然后对块状试样特定面进行抛光处理,并用乙醇清洁,吹干。
1.3 表征与性能分析
采用TESCAN MIRA3 场发射扫描电子显微镜观察腐蚀后的铝合金的微观形貌,分析其腐蚀层厚度。用能谱仪(EDS)分析腐蚀区的化学成分。采用Rigaku D/max 2500PC X 射线衍射仪(XRD)测试分析腐蚀区域的物相组成。分别对不同腐蚀时间的3 种铝合金拉伸试样进行室温拉伸实验,测试其拉伸性能随着腐蚀时间的变化规律。拉伸实验所选取的样品腐蚀时间和表征样品腐蚀时间一一对应,分别为6,12,24,48,96,168 h。为了保证实验结果的准确性,每一组拉伸试样的平行试样为3 个,取平均值作为最后的实验结果。室温拉伸实验样品如图1 所示,采用SANS-CMT5105 型微机控制电子万能试验机进行拉伸实验,样品两端夹紧,拉伸速率为1 mm/min。
图1 室温拉伸样品图(单位:mm)
2 铝合金腐蚀过程中表面微观形貌与成分演变
经过不同腐蚀时间腐蚀的3 种铝合金试样表面的腐蚀形貌如图2 所示。从图中可以观察到,6061 铝合金在腐蚀介质中的腐蚀速度非常快,仅腐蚀6 h 后就出现了大面积的腐蚀凹坑,这些腐蚀凹坑大小不一,形状不规则,遍布试样表面。这是铝合金点蚀的典型形貌,其形成原因可用氧化膜破坏理论和吸附理论两种理论来解释[10]。随着腐蚀时间推移,样品表面的原始的平整面积逐步减少,腐蚀凹坑面积逐步增大,可以观察到,腐蚀48 h 后样品原始表面已经完全被腐蚀,呈现出高低起伏的腐蚀坑洞。腐蚀凹坑的快速增加是因为在腐蚀坑形成后,其内外部的电化学条件发生显著变化[11],坑内发生铝合金的溶解反应,坑外部发生耗氧腐蚀反应[12],氧化铝在坑外不断堆积,使腐蚀坑内部形成闭塞区域,加速了腐蚀坑的加深与扩展[13],大面积的腐蚀凹坑就是由于各个点蚀坑在持续腐蚀过程中不断扩大,最后连接在一起形成的腐蚀样貌。从6061 铝合金腐蚀形貌中还观察到腐蚀坑具有形状规则的方形结构,这种结构比较松散,加大了材料与腐蚀介质之间的接触面积,腐蚀液可以穿过这些松散的结构孔洞,对基体进行持续大面积的腐蚀,因此腐蚀速度非常快。对腐蚀48 h 后6061铝合金样品表面点扫描(如图3 所示)发现表面仍然是基体元素,未发现S、N 和Cl 等腐蚀性元素。这可能是由于这些腐蚀性元素在腐蚀过程中起催化作用,并未参与到腐蚀反应中。相比之下,2195 铝锂合金在酸性腐蚀液中的腐蚀速度比较慢,其SEM 图像显示腐蚀6 h后的2195 基体上仅存在少量鼓泡,没有出现其它明显的腐蚀形貌。少数鼓泡的出现是由于铝合金表面发生了轻微的点腐蚀,这些点腐蚀优先在富铜相的位置形成,因为富铜相与周围铝基体存在电位差[14],极易在其位置发生电化学反应而引起腐蚀。腐蚀24 h 的2195 铝锂合金试样表面的点腐蚀情况也不明显,仅有少数点腐蚀坑出现,这可能是因为本次浸泡实验腐蚀的诱导因素是带有腐蚀性的氯离子(Cl–)和硫酸根离子(SO42-),这些离子对铝合金表面生成的致密氧化膜造成了破坏,Cl– 离子因其半径小而具有非常强的穿透能力,容易被吸附在铝合金表面氧化膜破损、材质不均匀等活性位置,腐蚀性阴离子与表面氧化膜发生化学反应,随着时间延长,氧化膜变薄、破裂,直到铝合金基体裸露而后发生溶解[15-17]。由于腐蚀前期铝合金表面仅仅出现少量鼓泡,大部分表面致密的氧化膜还比较完整,所以腐蚀坑的形成进展缓慢。随着腐蚀时间继续延长,在腐蚀48 h 后,点蚀坑在长大过程中不断与其它点蚀坑合并,形成非常大的腐蚀坑。我们还观察到2195 铝锂合金在腐蚀过程中,随腐蚀时间增加,其表面覆盖的一层黑色的薄膜越来越黑,这层薄膜非常薄并且极易掉落,可能是表面被腐蚀留下的腐蚀产物。通过对腐蚀48 h 的样品表面进行EDS 点扫描(图4),发现腐蚀48 h 后2195 铝合金表面基本上还是以Al 为主,未见S、N 和Cl 等腐蚀性元素,这可能是由于生成的腐蚀产物掉落溶解到腐蚀液中了。
7075 铝合金腐蚀行为类似于2195 铝锂合金,在腐蚀初期就出现一些零散的絮状腐蚀产物覆盖在样品表面。这是由于7075 铝合金表面的氧化膜被破坏后,其铝基体与腐蚀介质中的Cl-发生电化学反应,在铝合金表面生成一层比较粗糙和疏松的腐蚀产物[18]。腐蚀24 h 后覆盖在样品表面的腐蚀产物越来越多,腐蚀48 h 后覆盖在样品表面的腐蚀产物进一步增多,并出现龟壳状裂纹,这是晶间腐蚀的典型特征。用EDS 能谱分析腐蚀48 h 后的7075 铝合金表面特征点,所得点谱图如图5 所示。腐蚀48 h 后7075 铝合金表面主要存在Al 元素和O 元素,说明覆盖在基体上的腐蚀产物为氧化铝。S、N、Cl 等腐蚀性元素并未参与腐蚀反应,可能只起到了腐蚀催化作用。
图2 三种铝合金腐蚀形貌随腐蚀时间变化图
图3 腐蚀48h 后6061 铝合金表面EDS 点谱图
图4 不同腐蚀时间2195 铝合金腐蚀层深度变化
图5 腐蚀48h 后7075 铝合金表面EDS 点谱图
图6 为3 种铝合金腐蚀层厚度形貌图,图7 为3 种铝合金腐蚀层厚度随腐蚀时间的变化曲线图。从图中可以看出,3 种铝合金腐蚀层深度随腐蚀时间延长在不断增加,在腐蚀6 h后6061、2195、7075 铝合金的腐蚀层深度分别为8.34 μm、0 μm 和0.81 μm;6061 铝合金的腐蚀速度最快,7075 铝合金次之,2195 铝锂合金还未见明显腐蚀。在腐蚀48 h 后,6061、2195、7075 铝合金的腐蚀层厚度分别为21.6,2.25,12.8μm;6061 铝合金腐蚀速度最快,2195铝锂合金腐蚀最慢,这也比较符合3 种铝合金表面腐蚀形貌的结果。
图6 不同腐蚀时间3 种铝合金腐蚀层厚度
图7 三种铝合金腐蚀层深度变化
3 铝合金腐蚀过程中的力学性能演变
对6061 铝合金母材(BM)和经过不同腐蚀时间腐蚀的样品进行室温拉伸实验,所得工程应力应变曲线如图8 所示。图9 为其强度和塑性的变化统计图,图中sb 为抗拉强度,s0.2为屈服强度,d为延伸率。未经过腐蚀的6061 铝合金抗拉强度为215 MPa 左右,延伸率为14.6%。随着腐蚀时间延长,其强度并未发生比较大变化,腐蚀1 周(168 h)后的样品仍然保持在214 MPa 左右,而塑性在经过腐蚀后出现了轻微的下降,从母材的14.6%降至腐蚀1周后的12.6%。从扫描电镜中,我们观察到6061 铝合金经过腐蚀后,其表面被腐蚀得很严重,但强度和塑性并没有特别剧烈的改变,因此,在腐蚀环境中6061 铝合金的性能具有比
图8 6061 不同腐蚀时间的6061 铝合金工程应力应变曲线
图9 不同腐蚀时间6061 铝合金强度和塑性变化图
2195 铝锂合金作为第三代高强铝锂合金,具有比较高的强度和良好的塑性,图10 为2195铝锂合金母材和腐蚀不同时间后的样品的工程应力应变曲线,其强度和塑性的变化见图11。在被腐蚀后2195 铝锂合金的强度和塑性都明显地降低了,2195 铝锂合金母材强度为490 MPa,延伸率为22.5%,随着被腐蚀时间延长,强度逐步降低,腐蚀1 周后的样品强度仅为310 MPa,延伸率降低至3.5%,强度和塑性相比母材分降低了180 MPa 和19%,这说明2195 铝锂合金在被腐蚀后性能变动大,耐腐蚀性能相对较差。
图10 不同腐蚀时间的2195 铝锂合金工程应力应变曲线
图11 不同腐蚀时间2195 铝锂合金强度和塑性变化图
图12 为7075 铝合金母材与经过不同腐蚀时间腐蚀后的样品的工程应力应变曲线,其强度和塑性的变化见图13。被腐蚀后7075 铝合金的强度和塑性随时间延长逐步降低,7075铝合金母材抗拉强度为558 MPa,屈服强度为534 MPa,延伸率为11.3%,腐蚀时间延长至24 h 后,其抗拉强度为524 MPa,屈服强度为500 MPa,延伸率为8.3%,分别降低了34MPa、34MPa 和3%。当腐蚀时间延长至1 周后,其抗拉强度降低至460 MPa,屈服轻度降低至430 MPa,延伸率仅为3.1%。这说明在高腐蚀性环境中7075 铝合金的耐腐蚀性能也比较差。
图12 不同腐蚀时间的7075 铝合金工程应力应变曲线
图13 不同腐蚀时间7075 铝合金强度和塑性变化图
4 结 论
1) 3 种铝合金的腐蚀行为不尽相同,6061 铝合金和2195 铝锂合金在高Cl-、NO3-、SO42-的腐蚀液中的腐蚀方式是由点腐蚀向面腐蚀的转变,而7075 腐蚀方式是逐步出现大面积龟甲状裂纹,并且7075 铝合金和2195 铝锂合金腐蚀后表面会覆盖一层腐蚀产物薄膜,而6061铝合金的腐蚀产物溶解到腐蚀液中。
2) 在被腐蚀后6061 铝合金的强度和塑性都没有明显的变化,而2195 铝合金和7075铝合金随着被腐蚀时间延长,其强度和延伸率都明显地降低,说明6061 铝合金的力学性能具有比较好的腐蚀稳定性,2195 和7075 铝合金铝锂合金的耐腐蚀性能不佳。
参考文献:
[1] 钟掘.轻合金加工技术,2002,30(05):1.
[2] 叶浩. 2024铝合金的熔铸及形变热处理工艺研究[D].湖南大学,2012.
[3] 白志玲.铝合金的研究现状及应用[J].科技广场,2015(12):18-20.
[4] 宋海林,高萌,邢娜,王成龙,陈永斌.2种盐雾环境下6061车用铝合金的加速腐蚀行为研究[J].材料保护,2020,53(11):21-25+31.
[5] Yang Minjie.Study on corrosion property and mechanism of sprayformed 7055 aluminum alloy[D].Lanzhou: Lanzhou University of Technology, 2014.
[6] H-Y Ding, G-H Zhou, D Hui. Friction and wear performance of an aluminium alloy in artificial seawater[J]. Proceedings of the Institution of Mechanical Engineers, 2011, 225(1): 43–49. doi: 10.1243/09544070JAUTO1462.
[7] 陶永奇, 刘刚, 黎业生, 等. 海水环境下2024铝合金腐蚀磨损性能研究[J]. 中国腐蚀与防护学报, 2016, 36(6): 587–594.
[8] 李琳琳. 6×××系铝合金中第二相Mg_2Si的局部腐蚀机理研究[D].沈阳工业大学,2017.
[9] 李晓刚.材料腐蚀与防护概论[M].北京:机械工业出版社,2017.
[10] 徐火平,刘慧丛,朱立群,刘建中,叶序彬,胡本润.盐雾环境中高强铝合金点腐蚀行为与暴露面积的关系[J].航空材料学报,2010,30(04):59-64.
[11] 李亚萍,曲鸣飞.机械装备用6xxx系铝合金在氯盐溶液中的腐蚀行为及其防护[J].电镀与环保,2019,39(06):42-44.
[12] 魏立艳. 微观组织结构对铝及铝合金腐蚀行为的影响[D].哈尔滨工程大学,2009.
[13] 殷士焜. 2198铝锂合金激光焊接接头的腐蚀行为及机理研究[D].北京工业大学,2016.
[14] 李云涛,李晓宁,包俊成,周世杰.2024铝合金盐雾腐蚀评估及腐蚀形貌分析[J].腐蚀与防护,2015,36(09):864-868.
[15] 张仁群,王斌,岳涛,赵晓林.浅析国军标GJB150与美军标MIL-STD-810F盐雾试验[J].环境技术,2008(05):42-45+26.
[16] 程文礼,杨慧,任德杰,何二锋,李玉峰.表面处理对铝合金盐雾环境下的腐蚀特性试验研究[J].航空制造技术,2020,63(12):92-96.
[17] Zhang Y, Yin X, Wang J, et al. Influence of microstructureevolution on tribocorrosion of 304SS in artificial seawater[J].Corrosion Science, 2014, 88(11): 423–433.
免责声明:本网站所转载的文字、图片与视频资料版权归原创作者所有,如果涉及侵权,请第一时间联系本网删除。
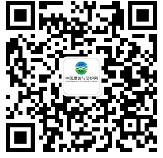
官方微信
《中国腐蚀与防护网电子期刊》征订启事
- 投稿联系:编辑部
- 电话:010-62316606-806
- 邮箱:fsfhzy666@163.com
- 中国腐蚀与防护网官方QQ群:140808414