钛及钛合金具有强度高、密度小、耐腐蚀等优点,因此被广泛应用于航空航天、海军装备、船舶、海洋资源开发和石油化工等领域。目前,钛及钛合金的加工方法主要为机械加工,与传统的金属材料相比,钛及钛合金的机械加工性能较差,如导热系数低导致磨削温度高,磨削比很低,弹性模量低,化学活化性强,表面质量不易保证,容易出现零件变形、应力集中,无法保证尺寸要求等,机械加工性能较差是长期以来困扰钛合金加工的主要问题之一。
化学铣切是一种腐蚀加工方法,它依靠化学溶液腐蚀溶解金属表面实现加工目的,为飞机及船舶用钛合金结构和零件的加工及维修提供了一种有效的方法。也有研究者采用化学铣切来减轻发动机钛合金叶片、机匣等结构件的质量。
从19世纪60年代开始,前苏联、美国、法国和英国等国家陆续开展了钛及钛合金化学铣切加工、维修研究。1978年,COGGINS等公开了一种由氢氟酸、硝酸、羧酸衍生物及苯甲酸钠组成的钛合金化学铣切的加工溶液(化学铣切液),用该溶液进行化学铣切时,吸氢量很少且铣切均匀。
在早期钛及钛合金化学铣切加工中,常采用HNO3-H2CrO4型化学铣切液,后来采用HF-H2CrO4型化学铣切液,但是由于H2CrO4具有成本高、污染严重、加工件易产生氢脆等缺点,逐渐被弃用。国内研究人员开发了HF型化学铣切液,该化学铣切液适用于加工过程中含氢量几乎不发生明显变化的金属材料,如商业用纯钛、Ti-25Cu等。HF-HNO3型化学铣切液是目前应用比较普遍的化学铣切液,硝酸作为化学铣切中的氧化剂,在提高金属表面光亮度的同时,也能避免氢脆。
化学铣切液的成分与作用
钛合金化学铣切液主要由腐蚀剂、氧化剂、添加剂、缓蚀剂和表面活性剂等组成。以常用的HF-HNO3型化学铣切液为例进行说明:由于钛及钛合金与空气接触会生成具有良好耐腐蚀性能的氧化层,故以具有强腐蚀性的HF为腐蚀剂;HNO3作为氧化剂可氧化氢气,防止氢脆对基体造成伤害,同时可以降低化学铣切面的表面粗糙度。
01 添加剂
在钛合金化学铣切过程中,除了必要的腐蚀剂和氧化剂之外,还需要添加必要的添加剂。添加剂可以起到降低钛合金的吸氢量、提高化学铣切表面质量、抑制有毒气体等作用。如化学铣切过程中会产生有毒的氮氧化物气体,一般要添加酰胺类化合物如尿素,尿素与氮氧化物反应,使氮氧化物分解成无毒的氮气和二氧化碳。添加剂应不影响基材的力学性能,也不与化学铣切液中其他成分反应。
02 缓蚀剂
具有一定黏度的缓蚀剂溶于化学铣切液后可以降低溶液中离子的扩散速率,使得化学铣切表面反应更加均匀,从而提高表面的平整度。化学铣切液中常用的缓蚀剂有磷酸二氢钠、磷酸氢钠、磷酸钠、偏磷酸钠、多聚磷酸钠、六氟磷酸铵、六次甲基四胺、苯甲酸、三羟基苯甲酸、硫脲、吖啶、吡啶、糠醛等,可使用一种或同时使用多种。
03 表面活性剂
表面活性剂的添加,能够降低反应界面张力,使化学铣切液与基体表面充分润湿,从而增大反应面积,提高腐蚀速率;同时,由于基体与化学铣切液充分接触,基体反应面产生的气体可以呈小气泡状排出,提高化学铣切面的表面粗糙度。化学铣切中的表面活性剂有苯甲酸钠、直链烷基苯磺酸钠、十二烷基硫酸钠、十二烷基磺酸钠、二辛基琥珀酸磺酸钠、甘胆酸钠、十二烷基苯磺酸、十二烷基苯磺酸钠、硬脂酸、硬脂酸钠、烷基醇酰胺、脂肪醇聚氧乙烯醚、烷基酚聚氧乙烯醚,可使用一种或同时使用多种。
化学铣切的机理
钛合金中不同的合金成分和组成相在腐蚀加工过程中有不同的溶解行为,因此钛合金表面各区域出现腐蚀差异。LIM等在化学铣切溶液中对经过不同退火处理的α+β钛合金进行腐蚀,研究了钛合金表面微观结构。结果发现,在腐蚀过程中,形成了以β相为阴极、α相为阳极的微电池,α相优先溶解,腐蚀以局部溶解的方式进行。
现阶段,关于钛合金化学铣切加工机理的研究主要集中在钛合金化学铣切过程中的扩散行为以及微观区部溶解行为方面。林翠等通过在不同成分和温度下的Ti-6Al-4V钛合金化学铣切液中测得的电位-时间曲线和极化曲线,分析了化学铣切过程的动力学规律。结果表明:钛合金的化学铣切是一个不断重复“浸蚀-溶解-钝化”的过程。在硝酸、氢氟酸体积比为2:1、3:1情况下,由阳极溶解速率随时间的变化曲线可知(如图1所示),在不同温度的腐蚀初期,腐蚀速率均快速上升,这是由于钛合金表面氧化膜在氢氟酸的强还原性作用下快速溶解;之后腐蚀进入平稳阶段,在该阶段去除氧化膜后的基体与硝酸直接接触生成耐蚀性较强的钝化膜,同时钝化膜会被氢氟酸破坏,钝化膜的生成和破环达到动态平衡,所以腐蚀速率也趋于平缓。
(a) 2:1
(b) 3:1
图1 不同硝酸、氢氟酸体积比下Ti-6Al-4V合金在化学铣切液中阳极溶解速率随时间的变化曲线
化学铣切的工艺流程
化学铣切的工艺流程为:预处理→水洗→干燥→涂保护涂层→刻型→装挂→化学铣切→水洗→干燥→去保护胶→质量检查。
01 预处理
化学铣切的预处理包括零件表面除油、吹砂和预腐蚀等。零件表面油污去除不干净,易出现腐蚀不均匀,甚至出现局部过腐蚀。常用的钛合金化学铣切除油方法为有机溶剂除油和化学除油。如果零件表面存在氧化皮或其他杂质,通过吹砂或预腐蚀可以提高保护涂层与零件基体的结合力。钛合金预腐蚀一般选用含有硝酸和氢氟酸的混合溶液。
02 涂保护涂层
在化学铣切过程中,为保证工件上不需加工的部分不被腐蚀,采用涂保护涂层的方式对该部分进行临时性保护。这种保护涂层是一种可剥性涂层,且涂层均匀,厚度一般在250~300μm。保护涂层的涂覆方式有喷涂、刷涂、浸涂三种,按零件结构的复杂程度、尺寸大小等选用合适的涂覆方法。
化学铣切用可剥性涂层多为国外进口。国内也开始研制这种保护涂层。如李清材等制备了一种新型化学铣切用可剥性保护涂料,该涂层平整均匀,不仅具有较好的附着力及良好的力学性能,还具有使用方便、耐腐蚀,易于手动剥离等特点。
03 刻型
钛合金工件在化学铣切前,必须先去除铣切部分的防护层,该过程称为刻型。传统的手工刻型效率低、协调关系复杂、准确性差,很难保证精度。孙新等采用激光刻型技术对钛合金工件进行刻型,该技术可根据涂层的厚度,调整激光刻型参数,精确有效地去除防护层。
04 装挂
在化学铣切过程中会产生大量的气体和热量,如不及时排除这些气体和热量,将影响化学铣切速率和工件表面的均匀性等。在化学铣切过程中,如果工件静止不动,化学铣切后其表面会出现明显的气流冲刷痕迹。为了消除此流痕,通常采用搅拌溶液的办法,但对于形状复杂工件特别是大工件,单纯的搅拌无法保证工件各个方向的均匀性,因此还需设计专用的装置,使工件在溶液中转动,且定期变换方向,避免由于工件形状带来的遮挡,这个工艺过程称之为装挂。
05 化学铣切
将经过上述处理的工件放入化学铣切液中,除去金属材料,直至厚度达到要求为止。在化学铣切过程中,需要对溶液进行搅拌,以消除工件与化学铣切液反应产生的气体对工件造成冲刷从而产生不均匀的流痕。化学铣切后工件需在冷水槽中彻底清洗,去除表面残留的酸碱液。
化学铣切的影响因素
01 材料状态
材料状态对钛及钛合金化学铣切的影响体现在材料的冶金状态、冷作硬化和表面粗超度等方面。
钛及钛合金的冶金状态对化学铣切有一定影响。通常情况下,与铸造态零件相比,锻压、挤压、轧制态零件的表面更致密、更均匀,经化学铣切后钛及钛合金的表面粗糙度低、光亮度高。
如果冷作硬化后未消除零件内应力,材料腐蚀的倾向会增加。因此,在化学铣切前应对冷作硬化零件进行应力消除。
在其他条件相同的情况下,钛及钛合金零件基体材料的表面粗糙度越低,化学铣切速率越快,且化学铣切后零件的表面粗糙度也越低。
02 化学铣切液温度
化学铣切过程中,钛及钛合金与酸的反应是放热反应,其速率与温度成正比关系。但温度高于46℃后,氢氟酸大量挥发,易对人员造成伤害,且氢氟酸挥发会导致化学铣切液成分改变,降低化学铣切液的使用寿命,同时过高的温度易导致保护涂层起泡失效,因此最合适的温度范围为25~30℃。
03 搅拌速率
在化学铣切过程中需进行搅拌,以保证化学铣切液与金属表面接触充分和反应均匀。一般来讲,搅拌速率对金属表面粗糙度无明显影响,但与化学铣切速率成正比关系。当化学铣切速率过快时,与化学铣切面各部分接触的化学铣切液的流速不同,导致工件的均匀性变差。所以搅拌速率一般选择150~200r/min。
04 HF含量
钛及钛合金对氢非常敏感,随着化学铣切的不断进行,反应生成的氢气不断增加,导致反应面的吸氢量不断增加。氢是一项必须严格控制的指标。一般来讲,钛及钛合金中氢含量一般不得高于0.0125%~0.015%(质量分数),否则会在组织上析出氢化物,出现明显的氢脆现象。为了避免这种现象,可通过添加抑制剂来抑制酸洗过程中产生混合物,从而减少氢含量,改善表面特性。为避免出现氢脆现象,现有化学铣切工艺的铣切深度一般不超过2mm。李庆春对TA12钛合金进行了铣切深度大于2mm的化学铣切,结果发现:当化学铣切深度达到2.4mm时,含氢量有所增加,但未出现氢脆现象,当化学铣切深度超过5mm时,增氢量约为50×10-6%(体积分数)。
05 化学铣切过程的综合评定
钛及钛合金化学铣切过程是可控制过程,为了精准控制钛及钛合金化学铣切深度和化学铣切质量,需综合考虑温度、化学铣切液配比、搅拌等因素。
林翠等利用正交试验法,得出HF是影响腐蚀加工速率的主要因素,HNO3是影响表面粗糙度的主要原因,而添加剂同样对腐蚀加工的表面具有较大影响。
钛及钛合金化学铣切受多因素混合影响。多数研究以单一因素作为变量来确定其影响,而没有考虑到各个因素之间的交叉影响。薛露平等采用均匀设计的试验方法,以化学铣切的4个因素(温度、钛离子含量、HF含量、HNO3含量)作为影响因子,利用Minitab软件得到铣切速率和浸蚀比与4个因素的回归方程,如下式所示,确定了各个因素混合影响程度。
v=-0.0922+0.00189T+0.000735 w(HF)
P=1.21-0.0219 c(Ti)+0.0156 w(HF)-0.0108 w(HNO3)
w(HF)=0.7 w(HNO3)+1.4 c(Ti)-19.8
式中:v为铣切速率;T为热力学温度;P为浸蚀比;c(Ti)为钛离子浓度;w(HF)为HF质量分数;w(HNO3)为HNO3质量分数。
06 化学铣切对基体中应力的影响
虽然化学铣切不会使零件产生变形,但化学反应具有各向同性,在保护涂层保护下,钛及钛合金沿水平方向会不断被浸蚀,边缘形成尖边,随着化学铣切深度的增加,其尖边会变得越来越锋利,造成应力过于集中,如图2所示。
(a) 有保护涂层
(b) 去除保护涂层
图2 化学铣切中尖边形成示意图
去除尖边的方法主要有机械振动法和二次化学铣切法。机械振动法利用三次元振动原理,在特殊装备上使零件与磨削介质相互摩擦,达到去除尖边的目的。王辉等利用氢氟酸、硝酸等配成腐蚀液,对尖边进行二次化学铣切,该方法具有高效、低成本、尖边去除稳定等优点,但同时会导致尺寸的耗损。
结语
钛及钛合金化学铣切作为可控制的加工技术,不仅在钛合金减质和成形方面具有绝对的优势,还可以加工和维修一些轮廓外形复杂的钛合金零部件。另外,化学铣切还可以去除钛合金锻件、铸件等零件表面的油污和氧化皮等,避免了机械加工带来的刀具磨损、切削应力、变形等危害,广泛应用于航天、海工、医疗器械等领域。
近几十年来,钛及钛合金化学铣切加工得到了很大发展,但在以下方面还有待加强:
1 由于钛及钛合金还没有形成完整的体系,现行的化学铣切研究往往只针对单个钛合金,并不能完全体现钛合金整个体系的化学铣切特征。
2 钛合金化学铣切废液具有很强的污染性,为了降低污染,可以选取含氟化合物、氟硅酸等物质来代替氢氟酸。
3 目前对化学铣切工艺的研究,大多考虑单因素的影响,割裂了温度、化学铣切液成分等影响因素之间的相互作用,且缺乏完整的评价体系。
免责声明:本网站所转载的文字、图片与视频资料版权归原创作者所有,如果涉及侵权,请第一时间联系本网删除。
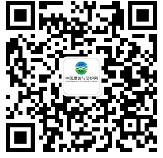
官方微信
《中国腐蚀与防护网电子期刊》征订启事
- 投稿联系:编辑部
- 电话:010-62316606-806
- 邮箱:fsfhzy666@163.com
- 中国腐蚀与防护网官方QQ群:140808414