摘要
针对镁合金的微弧氧化膜,对微缺陷的形成及其影响因素、微缺陷对微弧氧化膜性能及应用的影响、微缺陷的识别技术、后处理手段进行了总结与分析。最后,提出了镁合金微弧氧化膜及其他金属防护层中微缺陷问题的未来研究方向和思路。
关键词: 镁合金 ; 微弧氧化膜 ; 微缺陷 ; 影响 ; 缺陷检测 ; 处理技术
金属材料在制造过程中会产生偏析、夹杂、气孔、热裂纹等缺陷[1,2]。这些缺陷的存在将使金属材料具有偏离理想结构的非均匀性,对其结构及性能都将产生一定影响[3]。为了满足金属材料及其装备在各种复杂服役条件下的环境适应性要求,开发与利用适当的金属防护手段尤为重要。腐蚀防护层作为金属防护的重要手段,广泛应用于各种金属材料的腐蚀控制工程中。然而,在大多数工程应用中,金属材料的防护层也会因缺陷的存在,环境适应性大打折扣,服役寿命显著降低,不但会造成资源浪费,维修维护成本增大;而且会导致环境污染,影响产品质量,增大安全风险,甚至可能成为限制高新技术发展与应用的关键因素[4]。所以,开展金属防护层体系中的微缺陷对材料性能损伤问题的研究,不但有利于促进表面科学与工程技术的发展,而且也将提高金属腐蚀控制工程技术水平,既具有理论价值又具有技术应用价值。
镁合金以其质轻、性能优异、加工成本低、易于回收等优点,成为装备制造业轻量化、环保化、高性能化发展的首选,在机械、航空航天、汽车、电子、生物医疗等领域有着巨大的应用潜力[5]。然而,由于镁合金的耐蚀性较差,其进一步的推广应用也受到了一定限制。在现有的镁合金表面处理技术中,微弧氧化 (MAO) 技术形成的陶瓷膜具有耐磨、耐高温、电绝缘性能好、与镁合金基材结合力强等诸多优点,被誉为最有前景的镁合金表面处理技术。尽管如此,在镁合金微弧氧化膜的加工过程中,难以避免微缺陷的产生。微缺陷的存在大大削减了镁合金微弧氧化膜的耐蚀性,使其难以满足大多数工程应用的需求。镁合金微弧氧化膜的缺陷问题是众多金属防护层中缺陷问题的典型代表。因此,开展镁合金微弧氧化膜中的微缺陷研究,不仅可以为提升镁合金微弧氧化膜质量提供技术支撑,而且有利于认识金属防护层中微缺陷的损伤作用。目前,已有大量针对微弧氧化镁合金的文献综述发表[6-8],但大多聚焦于成膜机理、膜层性能、应用及封孔处理手段等内容。但从镁合金微弧氧化膜的微缺陷问题出发进行探讨与研究的文章较少。
本文基于微缺陷在金属防护层中存在的普遍性,着眼于镁合金微弧氧化膜体系的微缺陷问题,对微缺陷的形成及其影响因素、微缺陷对膜层性能及应用的影响、微缺陷的识别和后处理技术等进行了总结与分析。并对镁合金微弧氧化膜及其他金属防护层的微缺陷研究进行了展望,以期对金属防护层的设计优化及合理使用提供理论与技术支持。
1 微缺陷存在的普遍性
在金属材料冶炼、加工成型过程中,常常会引入杂质、裂纹、气孔等缺陷 (图1)[2]。这些缺陷或引起金属化学成分及组织结构的不均匀,或引起物理状态的不均匀,最终极可能导致金属的电化学不均匀 (电位分布差异),从而构成腐蚀微电池[4]。同样的,金属防护层的制备过程中也会出现微米或纳米尺度的微缺陷。在这里,金属防护层中的微缺陷可划分为物理结构缺陷与化学构造缺陷。其中,物理结构缺陷主要指结构上的不均与缺失,以微孔、微裂纹、粗糙等不同形态存在[9-12]。化学构造缺陷主要指具有高化学活性或电化学活性的非均匀相结构与化学组成[13,14]。这些化学构造缺陷或优先与腐蚀环境中的物质反应,发生化学溶解[13];或与体系其他部分构成腐蚀微电池,发生电化学溶解[14],最终都将导致涂层与保护膜的局部受损。
图1 金属表面的缺陷示意图[2]
虽然微缺陷在金属的防护层中普遍存在,但其并非一定会成为导致防护层失效的最终原因。在实际应用中,具有微缺陷的金属防护层也会出现均匀腐蚀失效或与微缺陷无关的局部腐蚀,这主要与腐蚀环境及防护体系性质有关。即便如此,在环境载荷下,微缺陷作为金属防护层防腐性能的“薄弱环节”,仍具有导致防护层失效的风险,如何提高缺陷防护层的环境适应性也是值得关注的问题。
金属防护层的种类多样,不同防护层体系的作用机理及其防护性能也有较大的差别。金属防护层大致分为钝化膜、转化膜及涂层3类。钝化膜的结构特征与金属及其氧化物的化学性质密切相关[15],比如金属Mg、Fe、Cu表面形成的钝化膜疏松且不连续,具有明显的物理结构缺陷。转化膜主要指通过化学或电化学处理在金属表面形成具有一定厚度的非电子导体膜[16],如阳极氧化膜等。在其成膜过程中,也难免产生微孔、裂纹等微缺陷[17,18]。与钝化膜、转化膜相比,涂层具有较大的厚度,因而在中、大型设备的腐蚀防护中应用十分普遍。通过添加不同的颜料或添加剂,涂层将表现出不同的防护机理:物理屏障、阴极保护、缓蚀剂防护等。同样的,由于材料自身性质、局部反应不均等原因,涂层在制备工艺过程中常常会产生微缺陷,如有机涂层[19,20]、金属涂层[21]、复合涂层[22]等。可见,无论是薄膜还是厚膜,或是具有更大厚度的涂层,都不可避免地存在着微缺陷。这将极大地制约着防护层及其防护体系服役寿命的延长,影响着结构件、装备的运行安全。
微缺陷导致的镁合金微弧氧化膜耐蚀性降低,成为了限制其发展及推广的重要因素,在众多金属防护层缺陷问题中具有典型性与代表性。对镁合金微弧氧化膜的微缺陷问题进行分析讨论,也将有利于加强对金属防护层中这一共性问题的认识。
2 微弧氧化及其微缺陷的形成
微弧氧化又称为等离子体电解氧化 (PEO),是在阳极氧化的基础上发展起来的金属表面处理技术[23]。微弧氧化利用高压放电产生的等离子体放电为驱动力,在金属表面原位形成一层具有一定厚度的氧化陶瓷膜。微弧氧化技术广泛应用于Al、Mg、Ti及其他轻质合金的表面防护处理中[24]。其中,对于镁合金而言,微弧氧化被称为最具有前景的表面处理技术之一。
一般地,镁合金微弧氧化膜的主要化学成分为MgO。MgO的化学稳定性较差,极易在腐蚀环境中发生化学溶解,造成镁合金微弧氧化膜的受损。同时,大量微缺陷存在于镁合金微弧氧化膜中,这些微缺陷将增大腐蚀介质的浸蚀面,同时为腐蚀介质的传递提供短途通道,加速了膜层的提前失效。微缺陷的产生是由材料性质与工艺特征造成的必然结果。一方面,MgO的低PB比 (0.81<1) 决定了微弧氧化膜疏松结构的形成。另一方面,在微弧氧化工艺过程中,高能等离子体放电活动也为微缺陷的形成创造了条件[25]。镁合金微弧氧化膜中的微缺陷属于物理结构缺陷,主要有两种存在形式:微孔与微裂纹。微孔的形成与高压、高温条件下的气体逸出及熔融态氧化物的喷发有关,微裂纹的形成则与熔融氧化物接触冷电解液凝固收缩产生的热应力有关[26,27]。因此,在镁合金微弧氧化膜的生长过程中,微缺陷的形成是难以避免的。
3 镁合金微弧氧化膜中微缺陷的影响因素
3.1 基材的影响
基材对微缺陷的影响主要体现在基材成分及表面状态两个方面。首先,基材成分会参与微弧氧化成膜。因此,基材成分对微弧氧化膜的结构特征及化学组成均会产生显著的影响。一般来说,AZ系列镁合金的微弧氧化成膜致密度优于AM系列[28]。在镁合金中适量引入Ca、Nd、Ce等可以提高微弧氧化膜的致密度,减少微缺陷的生成[29-31]。
除基材的化学成分外,基材的表面状态 (包括粗糙度、晶粒尺寸等) 对微弧氧化膜的结构也具有非常显著的影响[32,33]。研究[32]表明,在微弧氧化过程中,其放电现象与基材的粗糙度密切相关,基材表面粗糙度越高,微弧氧化膜中的微缺陷越多。通过一些预处理手段,如激光表面重熔 (LSR)、表面机械研磨处理 (SMAT)、超声冷锻 (UCFT)、超声滚压预处理 (UIRP) 等技术[34-37],对镁合金表面进行晶粒细化将有利于减少微缺陷的生成,制备出更为致密的微弧氧化膜。
3.2 电参数的影响
在微弧氧化工艺控制过程中,电参数主要包括电源类型、工作模式、电流密度/电压大小、占空比及频率等。不同的电参数将直接影响微弧氧化过程中的放电行为,进而影响膜层的物理结构及化学成分。用于镁合金微弧氧化处理工艺的电源类型通常为脉冲型电源,主要分为单极和双极两种。与单极脉冲电流相比,双极脉冲电流改善了等离子体的热条件,减少了强等离子体放电的发生 (B型放电),从而减少了大尺寸微孔的生成[38]。恒流模式与恒压模式为微弧氧化最普遍使用的电源工作模式。通常情况下,恒流模式下制备的微弧氧化膜微缺陷尺寸小于恒压模式下所得。在恒流模式下,低电流密度制备的微弧氧化膜一般都很薄,致密度高,缺陷少。随着电流密度的升高,放电能量也将升高,最终导致大孔径缺陷的生成。类似的,在恒压模式下,膜层的微孔尺寸会随电压的升高而增加[39]。提高频率能够在一定程度上减小孔隙缺陷的尺寸,从而生成致密的微弧氧化膜[40]。而占空比对微缺陷的影响较小,高占空会在一定程度上降低膜层的致密性[39]。
3.3 溶液参数及氧化时间的影响
微弧氧化的电解液成分不仅可以改变膜层的化学组成,还能通过改变微弧放电行为影响微缺陷的形成。例如,KF的加入能够降低起弧电压,使得氧化膜更容易被击穿,从而在镁合金表面生成更为致密的微弧氧化陶瓷膜[41]。同时,也会在膜层中形成MgF2,提高膜层的化学稳定性[42]。在硅酸盐电解液体系中加入3-氨基丙基三甲氧基硅烷 (APTMS)、甘油、三乙醇胺 (TEA) 等有机化合物,有利于通过改变微弧氧化过程中的放电行为,得到微裂纹更少、微孔尺寸更小的微弧氧化膜[43]。在电解液中加入氧化石墨烯,可以降低体系的击穿电压与放电能量,减少大尺寸微孔的形成[44]。
在其他参数不变的情况下,随着氧化时间的延长,膜层的厚度与致密度均会有上升趋势,但在氧化时间超过最优值后,厚度与致密度将有所下降。如果氧化时间过长,膜层结构可能会被完全破坏,膜层质量显著降低[45]。
4 微缺陷对微弧氧化镁合金性能与应用的影响
在大多数应用条件下,微缺陷的存在会削弱微弧氧化膜的局部防腐性能,最终导致镁合金基材腐蚀的发生,为结构件的正常服役带来安全隐患。但在实际中,也不乏利用镁合金微弧氧化膜中的微缺陷达到科学研究与工程应用目的的实例。
4.1 微缺陷的危害性
4.1.1 降低微弧氧化镁合金体系的防腐性能
在运输、施工、服役过程中,机械损伤或环境载荷作用可能会导致镁合金微弧氧化膜中微缺陷的扩展与新缺陷的生成。比较而言,环境载荷作用较为复杂,一方面,来源于环境中的腐蚀性因素,如高温、紫外辐射、Cl-等;另一方面,来源于环境力学因素,如机械磨损、冲击、压力、拉应力等。在实际服役环境中,可能是腐蚀性因素或者力学因素单独作用,也可能是两者耦合作用。
在环境载荷作用下,微缺陷将成为镁合金微弧氧化膜中的薄弱环节。一方面,微孔与微裂纹为腐蚀介质的传递提供了“传递通道”与更大的接触面积,成为腐蚀介质快速到达基材表面的“捷径”;另一方面,在环境力学因素的作用下,微缺陷处往往能造成应力集中[46],加速镁合金微弧氧化膜的机械损伤,成为膜层过早失效的突破口。此外,研究[47,48]表明,膜层分解与基材腐蚀生成的腐蚀产物Mg(OH)2会在膜层中产生内应力,也会导致固有缺陷的扩展与新缺陷的产生,甚至造成膜层的剥离。鉴于微缺陷的存在导致了微弧氧化膜耐蚀性能的降低,在较为苛刻的服役环境中,微弧氧化膜较少作为镁合金腐蚀防护层单独使用。
4.1.2 降低微弧氧化镁合金体系的力学性能
一旦微缺陷诱发了镁合金基材的局部腐蚀的出现,这些腐蚀区域也可能成为应力集中源,将缩短整个结构体系的疲劳寿命。另一方面,局部腐蚀将削弱材料结构的承载面积,致使体系静强度、疲劳强度、刚度等力学性能下降[49]。最终,造成微弧氧化镁合金结构件,甚至整个材料体系剩余强度与剩余寿命的显著降低。
4.2 微缺陷的可用性
虽然在环境载荷的作用下,微缺陷的存在可能会导致镁合金微弧氧化膜的过早失效,但是并非所有的应用环境都对材料体系的耐蚀性能具有高要求。例如,当微弧氧化镁合金用于骨内植入器械和血管支架时,微缺陷发挥了巨大作用。图2为随植入时间的延长,有无微弧氧化处理的ZX50镁合金植入体分解行为的μCT图像。可见,微弧氧化膜可减缓镁合金植入体在一定时间内的腐蚀,以提供足够的机械强度对血管或受损骨骼进行有效支撑[50]。随后,在微缺陷的作用下,微弧氧化镁合金在体液环境中逐渐无毒降解。这样,避免了植入体取出手术,极大地缓解了病人的生理痛苦和经济负担[51]。
图2 微弧氧化镁合金植入体针随时间的μCT图像 (3D重建)[50]
此外,微缺陷的存在为微弧氧化膜提供了更高的自由表面能和粗糙度,有利于有机物在其表面通过机械咬合结构牢固附着。因此,微弧氧化还被作为镁合金表面有机涂覆的前处理手段,以解决有机涂层与镁合金结合力较低的问题[52]。微弧氧化膜中的微缺陷还被作为承载药物与缓蚀剂的容器,从而制备出具有特殊性能的膜层。例如,Bordbar-Khiabani等[53]将镁合金微弧氧化膜作为倍他米松磷酸钠 (BSP) 的药物载体,实验结果表明所得PEO/BSP涂层具有较好的耐蚀性和药物传递性能。整体看来,由于镁合金微弧氧化膜在耐蚀性方面的局限性,功能膜将逐渐成为其重要发展方向之一。
总的来说,微缺陷具有存在的普遍性、隐蔽性,影响的双重性、潜在性。在涂层与保护膜的工程应用中,微缺陷问题往往被忽略。因此,对微缺陷进行有效识别与分析,将有利于科学避免与合理利用微缺陷。
5 微缺陷的识别技术研究
在金属防护层的研究中,常用的测试手段主要包括物理结构分析技术、化学构造分析技术及电化学测试技术。然而,传统的测试技术大多局限于2D空间或宏观层面上的分析检测,难以满足对微缺陷识别及其引起的膜层性质非均匀性的研究。因此,随着现代分析测试技术的发展,一些新型现代测试与分析技术开始在微缺陷研究方面展开应用。
5.1 物理结构测试技术
传统的扫描电子显微镜 (SEM) 等测试技术很难为研究人员提供微缺陷在3D空间的分布信息。随着数字与图像技术的发展,X-CT技术等3D定量测试技术已在微弧氧化膜的微缺陷研究中得到了应用[48,54,55]。它们可以直接而定量化地表征微弧氧化膜微缺陷在3D空间的尺寸大小、数量及分布特征[56],对微缺陷的识别与研究具有十分重要的意义。
5.2 化学构造测试技术
微缺陷分布的不均匀,也意味着成膜过程中放电现象的不均匀,即能量传输与物质传递的不均匀。因此,微弧氧化膜的化学构造也将存在差异性。利用微区化学测试技术,可以测定微弧氧化膜表面的化学分布,以达到研究微缺陷的目的。此外,这些技术还可应用于其他金属防护层的化学构造缺陷的检测中。常见的微区化学测试技术有电子背散射衍射 (EBSD)[57]、飞行时间二次离子质谱 (TOF-SIMS)[58]、扫描电镜透射模式 (STEM)[59]、Raman光谱[59]等。
5.3 电化学测试技术
近年来,微区电化学技术的发展与应用,为检测微缺陷在介质中的局部电化学行为提供了可能[60],主要包括以下几种。
扫描电化学显微镜 (SECM) 是一种能够同时提供溶液中样品表面的局部形貌、化学构造及电化学信息的测试技术[61],是涂层与保护膜微缺陷研究的有力手段。扫描振动电极技术 (SVET) 可以提供微尺度下电极表面电流密度或电位梯度的信息。近年来,SVET被广泛应用于涂层与保护膜微缺陷的定位、微缺陷的形成和发展的监测等领域[60]。局部电化学阻抗谱 (LEIS) 作为一种相对新颖的局部电化学测量方法,可以通过提供试样上特定位置的阻抗数据来研究非均匀腐蚀[62]。扫描开尔文探针技术 (SKP) 是在真空或大气中测量金属表面接触电位差的方法,以此探索表面的局部电化学状态。扫描开尔文探针力显微镜技术 (SKPFM) 是原子力显微镜 (AFM) 和SKP的结合,通过SKPFM可以观察到局部表面的形貌和Volta电位的变化[63]。丝束电极 (WBE) 技术是一种适用于实际现场监测和高电阻环境的测试手段。目前,WBE已被成功应用于垢下腐蚀、阴极剥离监测以及流动条件下微缺陷的形成与扩展过程。
除WBE技术外,上述电化学局部化技术都是扫描探针技术。探针与测试表面的距离、试样自身的表面高度差、探针的尺寸及其移动时的搅拌作用均会对测试结果的准确性产生影响[64]。此外,作为一种微观测试技术,现有的微区电化学测试仍需要进一步提高测试精度与分辨率,特别是实现纳米尺度的测试,以达到对微缺陷的电化学响应的精确捕捉。
5.4 数值模拟
由于微弧氧化膜加工工艺的复杂性,数值模拟已被广泛用于微弧氧化膜加工过程热力学与动力学的研究中[25,65-67]。而在实际应用中,由于微缺陷体积小、隐蔽性高的特点,现有的监测技术往往难以反映微弧氧化膜中微缺陷的精确信息。在这种情况下,使用数值模拟技术对微缺陷演化行为及其所诱发的微弧氧化膜失效过程进行研究,必将逐渐成为代替微缺陷实际监测的重要手段。然而,由于腐蚀体系的复杂性,如何正确建立数学模型也是数值模拟中的重要难题。
综合上述的测试技术,针对微缺陷的测试技术主要向着3D、微观测试及数值计算的方向发展。在微缺陷问题的研究中,如何选用合适的测试技术也是值得关注的问题。
6 镁合金微弧氧化膜微缺陷后处理技术
在微弧氧化过程中,微缺陷的产生是难以避免的,工艺条件优化仅仅能减少微缺陷的形成,并不能从根本上解决镁合金微弧氧化膜中的缺陷问题。因此,大量研究聚焦于通过后处理技术对微缺陷进行封闭,以提高镁合金微弧氧化膜的环境适应性。
6.1 水热处理
水热处理是一种最简单的微弧氧化膜后处理手段,主要是将微弧氧化样品浸入热水中进行封闭。通过水热处理,微弧氧化膜表面覆盖一层Mg(OH)2膜,对微弧氧化膜中的微缺陷进行封堵[68]。然而,经过水热处理,微弧氧化膜成分MgO也将被消耗,使膜层变薄。另一方面,Mg(OH)2的堆积也会带来膜层内应力的产生,可能会诱发膜层的机械损伤。
6.2 封涂处理
封涂处理是在微弧氧化膜表面形成一层新的防护层,以实现对微弧氧化膜疏松外层的有效封堵。常用的封涂方法包括溶胶-凝胶法、有机涂层封闭、化学镀、离子镀等[69,70]。溶胶-凝胶法具有环境友好、成本低、工艺简单等特点,是一种应用较为广泛的微弧氧化镁合金后处理手段[71]。通过溶胶-凝胶法,可在微弧氧化膜表面形成SiO2-ZrO2膜、SiO2膜、TiO2膜等陶瓷膜。另一种常用的封涂处理方法是有机涂层封闭[72,73]。由于微弧氧化膜外层的多孔性及有机材料的高流动性,有机层会与微弧氧化膜表面的孔隙紧密结合,更加有利于封闭效果的提升。
值得注意的是,大多数封涂技术都会改变镁合金微弧氧化膜原有的表面状态,膜层固有的耐磨、耐高温等性能也可能会由此削减甚至丧失。因此,根据应用需求,对后处理技术进行科学的设计与选用至关重要。
6.3 缓蚀剂浸渍
缓蚀剂浸渍法是镁合金微弧氧化膜后处理的重要手段之一。在微弧氧化膜的腐蚀失效过程中,缓蚀剂也会逐渐流失或被稀释,难以维持理想的缓蚀效果。因此,缓蚀剂浸渍封闭的方法很少被单独使用,一般在完成缓蚀剂浸渍后,需要进行再次的封涂处理,以防止缓蚀剂的过早流失[73,74]。
现有的微弧氧化镁合金后处理技术仍无法满足其大规模工业应用的要求。同时,后处理技术可能会在赋予镁合金微弧氧化膜新性能的同时,削减其原有性能。因此,开发一种保留膜层优秀性能的高效的后处理技术仍是亟待解决的技术问题。
7 结论与展望
微缺陷导致金属防护层过早失效、诱发基材局部腐蚀,是当今金属防护技术开发与应用中面临的共性问题。本文基于微缺陷在金属防护层中存在的普遍性,针对镁合金微弧氧化膜中的微缺陷问题展开了讨论,内容涵盖了微缺陷的形成及其影响因素、微缺陷对膜层性能及应用的影响、微缺陷的识别技术、后处理手段等方面。在镁合金微弧氧化膜及其他金属防护层缺陷问题的未来研究中,开展下列工作具有重要的意义。
(1) 开展微缺陷的多层次、跨尺度的识别与研究。微缺陷的存在会导致微弧氧化膜结构的非均匀性,这种微观性质的非均匀性也会导致膜层宏观性质的变化。因此,对微弧氧化膜物理结构与化学构造展开多层次、跨尺度的识别与研究是基础与关键,有助于从源头揭示微缺陷的作用机制。此外,应联合利用多种现代分析测试技术,全面揭示微缺陷诱发的微弧氧化膜失效和基材局部腐蚀机理。
(2) 加强对微缺陷的合理利用及再处理技术的研究。对于镁合金微弧氧化膜而言,现有的微缺陷处理技术仍无法满足大多数工业应用的要求。因此,有必要进一步加强对微弧氧化膜微缺陷处理技术的开发。另外,如何进一步利用微缺陷以达到某种科学研究与工程应用目的,也是值得研究的问题。
(3) 研发动态感知微缺陷的实时传感技术。微缺陷的形成与微弧氧化工艺参数密切相关,因此,在生产阶段实现对微缺陷的及时调控将有利于从源头实现对微缺陷的控制。研发动态感知微缺陷的实时传感技术,用于微弧氧化膜制备过程中的实时监检测,将有利于在生产阶段实现对微弧氧化膜质量的实时控制与精准调节,也将有利于推动材料智能制造 (如3D打印) 技术水平的提升。
(4) 强化对金属防护层中微缺陷问题的重视程度。镁合金微弧氧化膜是众多金属防护层体系微缺陷问题的典型代表,在其他金属防护层中,微缺陷也普遍存在,且其对防护层体系性质、性能的影响也是不容忽视的。强化对金属防护层中微缺陷的关注,建立相应的微缺陷检测评估及度量标准,完善材料服役过程中微缺陷检测网络的建立,将对金属防护层的设计优化及科学使用带来积极的推动作用。
参考文献
1 Sander G, Tan J, Balan P, et al. Corrosion of additively manufactured alloys: A review [J]. Corrosion, 2018, 74: 1318
2 McCafferty E. Introduction to Corrosion Science [M]. New York: Springer, 2009
3 Hu G X, Cai X, Rong Y H. Fundamental of Materials Science [M]. Shanghai: Shanghai Jiaotong University Press, 2010
3 胡赓祥, 蔡珣, 戎咏华. 材料科学基础 [M]. 上海: 上海交通大学出版社, 2010
4 Lin Y Z, Yang D J. Corrosion and Corrosion Control Principle [M]. Beijing: Sinopec Press, 2007
4 林玉珍, 杨德钧. 腐蚀和腐蚀控制原理 [M]. 北京: 中国石化出版社, 2007
5 Wang Y C, Zhou F, Ge Y F, et al. Recent progress on the surface modification and protection of magnesium alloys [J]. Mater. China, 2020, 39: 100
5 王悦存, 周凡, 葛延峰等. 镁合金表面改性与防护研究进展 [J]. 中国材料进展, 2020, 39: 100
6 Liu Y, Liu S M, Yu L P, et al. Summary on corrosion behavior and micro-arc oxidation for magnesium alloys [J]. J. Chin. Soc. Corros. Prot., 2015, 35: 99
6 刘胤, 刘时美, 于鲁萍等. 镁合金的腐蚀与微弧氧化膜层研究 [J]. 中国腐蚀与防护学报, 2015, 35: 99
7 Cui X J, Ping J. Research progress of microarc oxidation for corrosion prevention of Mg-alloys [J]. J. Chin. Soc. Corros. Prot., 2018, 38: 87
7 崔学军, 平静. 微弧氧化及其在镁合金腐蚀防护领域的研究进展 [J]. 中国腐蚀与防护学报, 2018, 38: 87
8 Darband G B, Aliofkhazraei M, Hamghalam P, et al. Plasma electrolytic oxidation of magnesium and its alloys: Mechanism, properties and applications [J]. J. Magnes. Alloy., 2017, 5: 74
9 Véliz B, Bermejo S, Orpella A, et al. Impedance modeling of silica nanoparticle metal insulator metal capacitors [J]. Electrochim. Acta, 2018, 280: 62
10 Ranade S, Forsyth M, Tan M Y J. The initiation and propagation of coating morphological and structural defects under mechanical strain and their effects on the electrochemical behaviour of pipeline coatings [J]. Prog. Org. Coat., 2017, 110: 62
11 Su Y Y, Li K Z, Hou X H, et al. Surface defects repairing of sprayed Ca-P coating by the microwave-hydrothermal method [J]. Ceram. Int., 2018, 44: 21699
12 Wang H W, Stack M M, Lyon S B, et al. The corrosion behaviour of macroparticle defects in arc bond-sputtered CrN/NbN superlattice coatings [J]. Surf. Coat. Technol., 2000, 126: 279
13 Xu P, Zhang C, Wang W, et al. Pitting mechanism in a stainless steel-reinforced Fe-based amorphous coating [J]. Electrochim. Acta, 2016, 206: 61
14 Zhang C, Chan K C, Wu Y, et al. Pitting initiation in Fe-based amorphous coatings [J]. Acta Mater., 2012, 60: 4152
15 Song G, Atrens A, St John D, et al. The anodic dissolution of magnesium in chloride and sulphate solutions [J]. Corros. Sci., 1997, 39: 1981
16 Cao C N. Principles of Electrochemistry of Corrosion [M]. Beijing: Chemical Industry Press, 2008
16 曹楚南. 腐蚀电化学原理 [M]. 北京: 化学工业出版社, 2008
17 Zhang Y J, Yan C W, Wang F H, et al. Electrochemical behavior of anodized Mg alloy AZ91D in chloride containing aqueous solution [J]. Corros. Sci., 2005, 47: 2816
18 Wang S X, Peng H L, Shao Z S, et al. Sealing of anodized aluminum with phytic acid solution [J]. Surf. Coat. Technol., 2016, 286: 155
19 Deflorian F, Fedrizzi L, Rossi S, et al. Defect dimension evaluation in organic coated galvanized steel by electrochemical impedance spectroscopy [J]. J. Appl. Electrochem., 2002, 32: 921
20 Gupta G, Birbilis N, Cook A B, et al. Polyaniline-lignosulfonate/epoxy coating for corrosion protection of AA2024-T3 [J]. Corros. Sci., 2013, 67: 256
21 Liu M M. The effect of sealing treatment on the corrosion and erosion-corrosion of high-velocity oxy-fuel Fe-based amorphous coating [D]. Shenyang: University of Science and Technology of China, 2019
21 刘明明. 封孔处理对HVOF铁基非晶涂层的腐蚀和冲蚀行为的影响研究 [D]. 沈阳: 中国科学技术大学, 2019
22 Guo J W. Microstructure and corrosion degradation behavior of magnesium alloy with microarc oxidation and hydrothermal process treated [D]. Harbin: Harbin Institute of Technology, 2019
22 郭君巍. 微弧氧化及水热复合改性镁合金的组织与腐蚀降解行为 [D]. 哈尔滨: 哈尔滨工业大学, 2019
23 Wang H B, Fang Z G, Jiang B L. Microarc Oxidation Technology and Its Applications in Sea Environments [M]. Beijing: National Defense Industry Press, 2010
23 王虹斌, 方志刚, 蒋百灵. 微弧氧化技术及其在海洋环境中的应用 [M]. 北京: 国防工业出版社, 2010
24 Walsh F C, Low C T J, Wood R J K, et al. Plasma electrolytic oxidation (PEO) for production of anodised coatings on light weight metal (Al, Mg, Ti) alloys [J]. Trans. IMF, 2009, 87: 122
25 Ma X, Blawert C, H che D, et al. A model describing the growth of a PEO coating on AM50 Mg alloy under constant voltage mode [J]. Electrochim. Acta, 2017, 251: 461
26 Chen H, Wang C C, Kang Y B, et al. Research status of micro-arc oxidation of magnesium alloy [J]. Surf. Technol., 2019, 48(7): 49
26 陈宏, 王成成, 康亚斌等. 镁合金微弧氧化的研究现状 [J]. 表面技术, 2019, 48(7): 49
27 Wang R Q, Wu Y K, Wu G R, et al. An investigation about the evolution of microstructure and composition difference between two interfaces of plasma electrolytic oxidation coatings on Al [J]. J. Alloy. Compd., 2018, 753: 272
28 Cakmak E, Tekin K C, Malayoglu U, et al. The effect of substrate composition on the electrochemical and mechanical properties of PEO coatings on Mg alloys [J]. Surf. Coat. Technol., 2010, 204: 1305
29 Dou J H. Preparation and corrosion resistance of degradable composite coating on magnesium alloy for orthopedics [D]. Ji’nan: Shandong University, 2018
29 窦金河. 医用镁合金表面可降解复合膜层的制备及其耐蚀性的研究 [D]. 济南: 山东大学, 2018
30 Song Y L, Liu Y H, Yu S R, et al. Plasma electrolytic oxidation coating on AZ91 magnesium alloy modified by neodymium and its corrosion resistance [J]. Appl. Surf. Sci., 2008, 254: 3014
31 Muhaffel F, Mert F, Cimenoglu H, et al. Characterisation and corrosion behaviour of plasma electrolytic oxidation coatings on high pressure die cast Mg-5Al-0.4Mn-xCe (x=0, 0.5, 1) alloys [J]. Surf. Coat. Technol., 2015, 269: 200
32 Yoo B, Shin K R, Hwang D Y, et al. Effect of surface roughness on leakage current and corrosion resistance of oxide layer on AZ91 Mg alloy prepared by plasma electrolytic oxidation [J]. Appl. Surf. Sci., 2010, 256: 6667
33 Wang Y, Lu D H, Wu G L, et al. Effect of laser surface remelting pretreatment with different energy density on MAO bioceramic coating [J]. Surf. Coat. Technol., 2020, 393: 125815
34 Wang L Q, Zhou J S, Liang J, et al. Microstructure and corrosion behavior of plasma electrolytic oxidation coated magnesium alloy pre-treated by laser surface melting [J]. Surf. Coat. Technol., 2012, 206: 3109
35 Gheytani M, Aliofkhazraei M, Bagheri H R, et al. Wettability and corrosion of alumina embedded nanocomposite MAO coating on nanocrystalline AZ31B magnesium alloy [J]. J. Alloy. Compd., 2015, 649: 666
36 Chen L L, Gu Y H, Liu L, et al. Effect of ultrasonic cold forging technology as the pretreatment on the corrosion resistance of MAO Ca/P coating on AZ31B Mg alloy [J]. J. Alloy. Compd., 2015, 635: 278
37 Wei Z, Ma B J, Li L, et al. Effect of ultrasonic rolling pretreatment on corrosion resistance of micro-arc oxidation coating of Mg-alloy [J]. J. Chin. Soc. Corros. Prot., 2021, 41: 117
37 魏征, 马保吉, 李龙等. 镁合金表面超声滚压预处理对微弧氧化膜耐蚀性能的影响 [J]. 中国腐蚀与防护学报, 2021, 41: 117
38 Hussein R O, Zhang P, Nie X, et al. The effect of current mode and discharge type on the corrosion resistance of plasma electrolytic oxidation (PEO) coated magnesium alloy AJ62 [J]. Surf. Coat. Technol., 2011, 206: 1990
39 Cui X J, Wang R, Wei J S, et al. Effect of electrical parameters on micromorphology and corrosion resistance of micro-arc oxidation coating on AZ31B Mg alloy [J]. J. Chin. Soc. Corros. Prot., 2014, 34: 495
39 崔学军, 王荣, 魏劲松等. 电参数对AZ31B镁合金微弧氧化膜微观形貌及耐蚀性的影响 [J]. 中国腐蚀与防护学报, 2014, 34: 495
40 Zou B, Lü G H, Zhang G L, et al. Effect of current frequency on properties of coating formed by microarc oxidation on AZ91D magnesium alloy [J]. Trans. Nonferrous Met. Soc., 2015, 25: 1500
41 Liu F, Yu J, Song Y W, et al. Effect of potassium fluoride on the in-situ sealing pores of plasma electrolytic oxidation film on AM50 Mg alloy [J]. Mater. Chem. Phys., 2015, 162: 452
42 Ryu H S, Mun S J, Lim T S, et al. Microstructure evolution during plasma electrolytic oxidation and its effects on the electrochemical properties of AZ91D Mg alloy [J]. J. Electrochem. Soc., 2011, 158: C266
43 Pak S N, Yao Z P, Ju K S, et al. Effect of organic additives on structure and corrosion resistance of MAO coating [J]. Vacuum, 2018, 151: 8
44 Zhang Y, Chen F, Zhang Y, et al. Influence of graphene oxide additive on the tribological and electrochemical corrosion properties of a PEO coating prepared on AZ31 magnesium alloy [J]. Tribol. Int., 2020, 146: 106135
45 Gu Y H, Bandopadhyay S, Chen C F, et al. Effect of oxidation time on the corrosion behavior of micro-arc oxidation produced AZ31 magnesium alloys in simulated body fluid [J]. J. Alloy.Compd., 2012, 543: 109
46 Tang J W, Shao Y W, Zhang T, et al. Effect of cyclic pressure on degradation Behavior of epoxy coating in simulated deep ocean environment [J]. J. Chin. Soc. Corros. Prot., 2011, 31: 275
46 唐俊文, 邵亚薇, 张涛等. 循环压力对环氧涂层在模拟深海环境中失效行为的影响 [J]. 中国腐蚀与防护学报, 2011, 31: 275
47 Wang Y, Huang Z Q, Yan Q, et al. Corrosion behaviors and effects of corrosion products of plasma electrolytic oxidation coated AZ31 magnesium alloy under the salt spray corrosion test [J]. Appl. Surf. Sci., 2016, 378: 435
48 Chen Z N, Ji H T, Geng X Q, et al. 3-D distribution characteristics of the micro-defects in the PEO coating on ZM6 mg-alloy during corrosion [J]. Corros. Sci., 2020, 174: 108821
49 Chen Y L. Corrosion Control and Strength Assessment of Naval Aircraft Structures [M]. Beijing: National Defense Industry Press, 2009
49 陈跃良. 海军飞机结构腐蚀控制及强度评估 [M]. 北京: 国防工业出版社, 2009
50 Fischerauer S F, Kraus T, Wu X, et al. In vivo degradation performance of micro-Arc-oxidized magnesium implants: A micro-CT study in rats [J]. Acta Biomater., 2013, 9: 5411
51 Xu H T, Hu T, Wang M L, et al. Degradability and biocompatibility of magnesium-MAO: The consistency and contradiction between in-vitro and in-vivo outcomes [J]. Arab. J. Chem., 2020, 13: 2795
52 Toorani M, Aliofkhazraei M, Mahdavian M, et al. Effective PEO/Silane pretreatment of epoxy coating applied on AZ31B Mg alloy for corrosion protection [J]. Corros. Sci., 2020, 169: 108608
53 Bordbar-Khiabani A, Yarmand B, Mozafari M. Functional PEO layers on magnesium alloys: Innovative polymer-free drug-eluting stents [J]. Surf. Innov., 2018, 6: 237
54 Zhang X, Aliasghari S, Němcová A, et al. X-ray computed tomographic investigation of the porosity and morphology of plasma electrolytic oxidation coatings [J]. ACS Appl. Mater. Interfaces, 2016, 8: 8801
55 Lu X P, Blawert C, Tolnai D, et al. 3D reconstruction of plasma electrolytic oxidation coatings on Mg alloy via synchrotron radiation tomography [J]. Corros. Sci., 2018, 139: 395
56 Zhao P X, Wu W, Dan Y. Application of spatial-resolution technology for in-situ monitoring of metal corrosion [J]. J. Chin. Soc. Corros. Prot., 2020, 40: 495
56 赵鹏雄, 武玮, 淡勇. 空间分辨技术在金属腐蚀原位监测中的应用 [J]. 中国腐蚀与防护学报, 2020, 40: 495
57 Mingo B, Guo Y, Němcová A, et al. Incorporation of halloysite nanotubes into forsterite surface layer during plasma electrolytic oxidation of AM50 Mg alloy [J]. Electrochim. Acta, 2019, 299: 772
58 Zhang S D, Wu J, Qi W B, et al. Effect of porosity defects on the long-term corrosion behaviour of Fe-based amorphous alloy coated mild steel [J]. Corros. Sci., 2016, 110: 57
59 Friedemann A E R, Thiel K, Ha linger U, et al. Investigations into the structure of PEO-layers for understanding of layer formation [J]. Appl. Surf. Sci., 2018, 443: 467
60 Karavai O V, Bastos A C, Zheludkevich M L, et al. Localized electrochemical study of corrosion inhibition in microdefects on coated AZ31 magnesium alloy [J]. Electrochim. Acta, 2010, 55: 5401
61 Pilbáth A, Szabó T, Telegdi J, et al. SECM study of steel corrosion under scratched microencapsulated epoxy resin [J]. Prog. Org. Coat., 2012, 75: 480
62 Huang V M, Wu S L, Orazem M E, et al. Local electrochemical impedance spectroscopy: A review and some recent developments [J]. Electrochim. Acta, 2011, 56: 8048
63 J ensson M, Thierry D, Lebozec N. The influence of microstructure on the corrosion behaviour of AZ91D studied by scanning Kelvin probe force microscopy and scanning Kelvin probe [J]. Corros. Sci., 2006, 48: 1193
64 Wang W, Zhang X, Wang J. Heterogeneous electrochemical characteristics of biofilm/metal interface and local electrochemical techniques used for this purpose [J]. Mater. Corros., 2009, 60: 957
65 Jiang M, Chai Y S, Zhou J, et al. Temperature field distribution of micro-arc oxidation process based on COMSOL [J]. Surf. Technol., 2017, 46(5): 17
65 姜曼, 柴永生, 周京等. 基于COMSOL的微弧氧化过程温度场分布研究 [J]. 表面技术, 2017, 46(5): 17
66 Ma X, Blawert C, H che D, et al. Investigation of electrode distance impact on PEO coating formation assisted by simulation [J]. Appl. Surf. Sci., 2016, 388: 304
67 Ma X, Blawert C, H che D, et al. Simulation assisted investigation of substrate geometry impact on PEO coating formation [J]. Surf. Coat. Technol., 2018, 350: 281
68 Peng F, Wang D, Tian Y, et al. Sealing the pores of PEO coating with Mg-Al layered double hydroxide: enhanced corrosion resistance, cytocompatibility and drug delivery ability [J]. Sci. Rep., 2017, 7: 8167
69 Liu P, Liu Q F, Huang D Q, et al. Research progress of pore sealing technology for micro-arc oxidation films [J]. Surf. Technol., 2019, 48(7): 61
69 刘朋, 刘群峰, 黄德群等. 微弧氧化膜封孔技术研究进展 [J]. 表面技术, 2019, 48(7): 61
70 Duan H P, Du K Q, Yan C W, et al. Electrochemical corrosion behavior of composite coatings of sealed MAO film on magnesium alloy AZ91D [J]. Electrochim. Acta, 2006, 51: 2898
71 Zeng D P, Liu Z Y, Bai S, et al. Influence of sealing treatment on the corrosion resistance of PEO coated Al-Zn-Mg-Cu alloy in various environments [J]. Coatings, 2019, 9: 867
72 Yang J J, Blawert C, Lamaka S V, et al. Corrosion protection properties of inhibitor containing hybrid PEO-epoxy coating on magnesium [J]. Corros. Sci., 2018, 140: 99
73 Li Z X, Yang W B, Yu Q L, et al. New method for the corrosion resistance of AZ31 Mg alloy with a porous micro-arc oxidation membrane as an ionic corrosion inhibitor container [J]. Langmuir, 2019, 35: 1134
74 Ivanou D K, Yasakau K A, Kallip S, et al. Active corrosion protection coating for a ZE41 magnesium alloy created by combining PEO and sol-gel techniques [J]. RSC Adv., 2016, 6: 12553
免责声明:本网站所转载的文字、图片与视频资料版权归原创作者所有,如果涉及侵权,请第一时间联系本网删除。
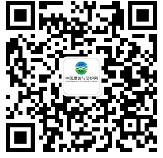
官方微信
《中国腐蚀与防护网电子期刊》征订启事
- 投稿联系:编辑部
- 电话:010-62316606-806
- 邮箱:fsfhzy666@163.com
- 中国腐蚀与防护网官方QQ群:140808414