第七章
腐蚀控制
Vol.7.5
选材、腐蚀试验及腐蚀控制
7.5.2
选材腐蚀试验设计
材料的腐蚀试验是检测金属或其他材料因与环境发生相互作用而引起的化学、电化学或物理(或机械)-化学损伤过程的材料试验。是掌握材料与环境所构成的腐蚀体系的特性、了解腐蚀机制,从而对腐蚀过程进行控制的重要手段。
01 试验目的
①在给定环境中的服役寿命;
②在特定环境中确定各种防蚀措施的适应性、最佳选择、质量控制途径和预测采取这些措施后构件的服役情况,评价材料的耐蚀性能,筛选评定各种备选材料的耐蚀性,包括腐蚀速率和局部腐蚀的可能性和速率;
③对新材料进行耐蚀性分析;
④确定环境的侵蚀性,研究环境中各组分、条件和腐蚀产物等对腐蚀速度、腐蚀形态的作用;
⑤研究腐蚀控制方法的有效性及选取最佳的控制参数;
⑥研究对腐蚀对环境或产品的污染作用;
⑦分析失效原因时作再现性试验;
⑧检验材料质量的例行实验,研究或验证制造工艺对材料耐蚀性的影响;
⑨验证产品的耐蚀性;
⑩研究腐蚀机理。
02 试验方法分类
材料的耐蚀性能是与环境条件、化学、物理、机械等因素密切相关的。因此,在腐蚀试验中必须注意试验体系与实际工作条件尽可能有良好的一致性。为比较材料的耐蚀性能,常需要制订标准试验方法来概括可能的工作条件。然而,由于实际腐蚀体系的复杂性,这种方法只能近似和相对地比较所得结果。按腐蚀试验与实际工作条件接近的程度或试验场合的不同,试验方法可分为实验室试验、现场挂片试验和实物试验3类。
①实验室试验。实验室试验是指在实验室内有目的地将专门制备的小型试样在人工配制的、受控的环境介质条件下进行的腐蚀试验。
优点是可孤立地研究某一因素的作用或几个因素的共同作用。为缩短试验周期,常在不改变实际腐蚀机制的前提下强化试验条件,进行加速腐蚀试验。可充分利用实验室仪器、控制设备,自由选择试样的大小及形状,可严格地控制有关的影响因素,试验时间较短,可精确和灵活性地进行试验,试验结果的重现性较好。所有,腐蚀试验一般应先在实验室进行,实验室试验有:
a.模拟试验。是一种不加速的长期试验,在实验室的小型模拟装置中,尽可能地精确地模拟自然界或工业生产中所遇到的介质及条件,虽然介质和环境条件的严格重现是困难的,但主要影响因素可充分考虑。这种试验周期长,费用大,但实验数据较可靠,重现性也高;
b.加速腐蚀试验。是一种强化的腐蚀试验方法,把对材料腐蚀有影响的因素如介质浓度、化学成分、温度、流速等加以改变,使之强化腐蚀作用,从而加速整个试验过程的进行。可在较短时间内确定材料发生某种腐蚀的倾向,或若干种材料在指定条件下的相对耐蚀顺序。
缺点是只能强化一个或少数几个控制因素。除特殊腐蚀试验外,一般不应引入实际条件下并不存在的因素,也不能因引入了加速因素而改变实际条件下原来的腐蚀机理和特征。
②现场挂片试验。指把专门制备的试样置于现场的实际环境中进行的腐蚀试验。试验方法和过程较简单,环境条件的真实性使它的试验结果比较可靠,结果更具有代表性。但现场试验中的环境因素无法控制,很难按需要来改变试验条件,结果的重现性较差,试验周期较长,且试验用的试样与实物状态之间存在较大的差异。
在实验室实验获得初步结果后,除理论研究和常规检验外,一般都需要进一步进行模型或现场试验。这是因为实验室试验通常有加速性质,小试件的表面状态与设备的大表面有较大的差别,试验环境不可能模拟生产环境,在生产中的介质环境可能有变化等;
③实物试验。指将试验材料制成实物部件、设备或小型试验性装置,在现场的实际应用下进行的腐蚀试验。解决了实验室试验及现场试验中难以全面模拟的问题,而且包括了结构件在加工过程中所受的影响,能够较全面正确地反映材料在使用条件下的耐蚀性。但费用较大,试验周期长,且不能对几种材料同时进行对比试验。因此,实物试验应在实验室试验和现场试验的基础上进行。
自然环境中的暴露试验周期都很长,如在大气或海洋中观察试件的失重和外观变化,试验周期可长达20~30a以上。实验数据的积累是一项重要的工作。
03 试样的准备
①试样材料。对所用试样的各种原始资料应尽可能地详细了解,其中包括材料的牌号、化学成分和力学性能等,对于金属还应包括试样的冶金和加工工艺特征、热处理及金相组织等。这些资料的了解,对于腐蚀结果的分析有重要的参考作用;
②试样的形状与尺寸。取决于试验的目的、试验的方法、材料的性质、试验的时间和试验的装置等。试样的外形要求简单,以便于精确测量表面积、清除腐蚀产物和进行加工。
为消除边界效应的影响,试样表面积对边缘面积之比应尽量大,试样表面积对试样重量之比也要尽量大些。
通常实验室所用的试样尺寸为:矩形 50mm×25mm×(2-3)mm,圆盘形Φ(30-40)mm×(2-3)mm,圆柱形Φ10mm×20mm,等;
③试样的表面处理。试样表面的粗糙度、均一性和洁净程度是影响腐蚀实验结果重现性和可比性的重要因素,因此在试验前应经过严格的表面处理。
通常从原材料上切取试板、经适当的机械加工和必要的研磨抛光制成试样,再经统一的清洗使之具有相近的表面状态;
④平行试样的数量。为提高试验结果的准确性,每次试验时须用一定数量的平行试样。平行试样越多,结果的准确性就越高。
通常一般试验的平行试样为3-12个,常用5个,最少3个。加载应力试验,试样为5-20个,常用10个,最少3个。在同一试验容器中只可进行1个或几个同一材质的平行试样的腐蚀试验。
04 腐蚀的暴露条件
①腐蚀介质
a. 直接取自生产现场;
b. 按现场介质成分人工配制,应当用蒸馏水和纯度为化学纯以上试剂精确地配制试验溶液,以严格控制试液的成分。
在试验过程中,还必须防止由于溶液蒸发及其它原因引起介质浓度、成分和体积的变化,以免影响介质的腐蚀性能和结果的可靠性。介质体积与试样面积比须符合标准的规定。
②试验温度。
腐蚀试验温度应尽量模拟实际腐蚀介质的温度。实验室控温方法有水浴、油浴或空气恒温箱等。控制的温度应是整个试样的表面温度,但为简便起见,往往以介质温度为控制对象。
③试验时间。
材料的全面腐蚀速率很少是恒定不变的,经常随时间而不断变化,因此试验的时间一般取决于材料的腐蚀速度。
局部腐蚀试验时间应按相关试验标准进行。全面腐蚀试验在实验室里一个周期的试验时间通常为24-168h,即1-7d。如果腐蚀速度是中等以下,则可由下式粗略地估计试验时间,该式仅适用于已知大概腐蚀速率的试验。
试验时间(h)=50/腐蚀速率(mm·a-1) (7-1)
④试样暴露的条件。
在实验室试验中,根据试验目的的不同,试样可全部(全浸)、部分(半浸)或间断(间浸)暴露于腐蚀介质中,以模拟实际应用中可能遇到的各种情况。
⑤试样安放与涂封。
a. 防止电偶效应。试样的安放应保证试样与试样之间、试样与容器之间、试样与支架之间电绝缘;保证试样有恒定的暴露面积,用绝缘材料将试样部分表面涂封遮蔽。在进行电化学测试时,必须在试样上引出导线,导线和试样的结点必须涂封,以防电偶腐蚀的干扰。涂封要求绝缘好、牢固、简便;
b. 防止缝隙腐蚀。试样与试样之间、试样与容器之间、试样与支架之间不产生缝隙,试样表面与介质充分接触。同时,要求试样装取方便、牢固可靠;支架本身耐蚀等;
c. 防止水线腐蚀(浓差腐蚀)。
05 腐蚀结果评定
①全面腐蚀速率。常用的腐蚀速率评定方法有失重法、线性极化法、电阻法和塔费尔极化曲线外推法等;
②孔蚀的评定。孔蚀试验的试样比失重试样大,一般约数十平方厘米。评定指标有:最大孔蚀深度、平均孔蚀深度、孔蚀密度和单位面积失重等;
③晶间腐蚀试验。一般腐蚀试验都可以用来检查晶间腐蚀。可用拉伸或弯曲试验评定晶间腐蚀引起的力学性能损失,或用金相显微镜观察晶间的腐蚀情况;
④应力腐蚀试验。应力腐蚀试验方法有很多种,试样也有多种类型,适用于各自特定目的,其加载应力、腐蚀暴露方法和时间、计算应力和评定结果的方式各不相同,其特点和局限性也不同,须根据试验目的和实际条件来选择加载方式、试样类型和试验方法。一般,按载荷加载方式来分有恒载荷、恒变形、慢应变速率3种。而具体试样的类型又可以分成以下几种:光滑试样,弯梁试样、C形环试样、U形试样和O形试样;缺口试样;预裂纹试样,增K型试样、恒K型试样、降K形试样。
a. 慢拉伸速率试验(SSRT)。是将拉伸试样放在特定介质中,通过慢拉伸速率拉伸试验机,以一个相当缓慢的应变速率对置于应力腐蚀环境中的试样施加应力,通过强化应变状态来加速腐蚀裂纹的发生和发展过程。SSRT方法提供了在传统应力腐蚀试验不能迅速激发应力腐蚀的环境里确定延性材料应力腐蚀敏感性的快速试验方法,它能使任何试样在较短时间内发生断裂,因此是一种相当苛刻的加速试验方法。SSRT的提出者认为:在发生应力腐蚀体系中,应力的作用是为了促进应变速度,真正控制应力腐蚀裂纹产生和扩展的参数是应变速率而不是应力本身。
不同的行业,不同的材料有不同的慢应变速率应力腐蚀试验标准,试验标准有ISO 7539.7[1]、GB/T 15970.7[2]、HB 7235[3]、HB 5260[4]等。慢应变速率法中应变速率的确定至关重要,如果应变速率过快,则试样来不及产生有效的应力腐蚀,就已经产生韧性断裂;如果应变速率过慢,在试样表面膜破裂后来不及产生有效的腐蚀,裸露的金属就再发生钝化,使应力腐蚀不发生,最后也将产生韧性断裂。不同的腐蚀体系采用的临界应变速率也不一样,表7-10。
表7-10 不同腐蚀体系SSRT临界应变速率
慢应变速率法应力腐蚀敏感性表征参量,通常以慢应变速率试验结果与在不发生应力腐蚀的惰性介质(如油或空气)中的试验结果进行比较,以两者在相同温度和应变速率下的试验结果的相对值表征应力腐蚀的敏感性。主要有以下几个评定指标:
i.断裂应力:在腐蚀介质中和惰性介质中的断裂应力比值愈小,应力腐蚀敏感性就愈大;
ii.断裂时间:从开始试验到载荷达到最大值时所需的时间t。应变速率相同时,腐蚀介质中和惰性介质中断裂时间比值愈小,则应力腐蚀敏感性愈大;
iii.吸收的能量:应力-应变曲线下的面积代表试样断裂前吸收的能量。惰性介质(空气)和腐蚀介质试验中吸收能量差别愈大,应力腐蚀敏感性也愈大;
iv.塑性损失:用腐蚀介质和惰性介质中的延伸率、断面收缩率的相对差值来度量应力腐蚀敏感性;
v.断口形貌:对大多数压力容器钢材,在惰性介质中断裂后将获得韧窝性断口,而在腐蚀介质中,拉断后往往获得脆性断口。其中脆性比例愈高,则应力腐蚀愈敏感。如介质中拉断后断面存在二次裂纹,也可以用二次裂纹的长度和数量来衡量应力腐蚀的敏感性。
在载荷-拉伸曲线上,将在惰性介质中的各特征参数与在腐蚀介质中的特征参数进行SSRT试验结果评定:
ISCC =(I惰-I腐)/ I惰 ×100% (7-2)
式中 ISCC-应力腐蚀敏感性指数;
I惰-在惰性介质中的试验参数;
I腐-在腐蚀介质中的试验参数。
评定应力腐蚀开裂敏感性指数ISCC,目前比较认可的参数有:ReL、Rm、A、Z、da/dt、内积功。ISCC衡量应力腐蚀开裂敏感性大小的一般评定:
当ISCC 大于35%,研究体系具有明显的应力腐蚀倾向;
当ISCC介于25%~35% 之间,研究体系有应力腐蚀倾向;
当ISCC 小于25%,研究体系没有明显的应力腐蚀倾向
b. 断裂力学方法。运用断裂力学理论,研究应力腐蚀开裂,不仅可以定量地测定材料在特定环境中的应力腐蚀开裂门槛应力强度因子KISCC,而且能够测定材料在特定环境介质中的裂纹扩展速率da/dt。KISCC标志着结构件中可以存在而又不引起应力腐蚀裂纹扩展的最大缺陷的尺寸,也就是规定了允许的最大临界尺寸,da/dt反映了材料在环境介质中抗开裂的能力,这两个重要参数可直接提供工程设计和材料研究使用,具有相当大的实际意义。
材料在应力腐蚀破坏过程中,其破坏寿命包括裂纹扩展前的孕育期和裂纹慢扩展期两部分组成。如果已经测得了裂纹扩展速率da/dt,那么就可以估算构件材料的安全使用期。为了测定应力腐蚀裂纹扩展速率,Brown等人于1965年首先使用WOL型试样采用了恒定位移法进行了研究。恒位移试样具有以下优点:
i.用螺钉自行加载,故不需要用试验机,可以大批量测试。特别是可以把试样放在实际使用的环境中做试验,从而可以获得现场条件下的试验数据;
ii.随着裂纹扩展,恒位移试样的KI下降,当降到KISCC时裂纹将停止扩展。因此用1个试样就可以测出止裂的KISCC,同时也可测出da/dt;
iii.可带载荷在显微镜下直接观察裂纹的形核和扩展过程;
iv.对于WOL试样,也可在线切割后不预制裂纹,但不能加载到出现裂纹,只要初始KI略大些或经过长的孕育期后就可从缺口处产生滞后裂纹。一旦出现裂纹后再降低Vo(即降低初始值),则裂纹在扩展一段长度后就会止裂,由此可得KISCC。
c.各种SCC试验方法对比。以加载方式区分的3种SCC物理试验方法的评定方式、优缺点特征列于表7-11中。因为各种试验方法的评定对象和优缺点各不相同,所以实际选用时要考虑到材料、介质、试验要求等多方而的因素,选用合适的试验方法。
表7-11 应力腐蚀试验方法的特点
06 腐蚀试验设计
试验设计在科学实验、工业生产和工程设计中能发挥重要的作用,例如:提高产量;减少质量的波动,提高产品质量;大大缩短新产品试验周期;降低成本;延长产品寿命等。
试验设计方法是一套完整的系统方法,如何安排实验,使实验次数尽量少,而又能达到好的试验效果,这是经常会碰到的问题。解决这个问题有一门专门的学问即“试验设计”。上世纪30年代,由于农业试验的需要,费歇(R.A.Fisher)在试验设计和统计分析方面做出了一系列先驱工作,从此,试验设计成为统计科学的一个分支。
60年代,华罗庚教授在我国倡导与普及的“优选法”,与我国的数理统计学者在工业部门中普及的“正交设计”法都是试验设计方法。这些方法经普及后,已为广大技术人员与科学工作者掌握,取得一系列成就,产生了巨大的社会效益和经济效益。“优选法”是单变量的最优调试法,即假定我们处理的实际问题中只有一个因素起作用,但这种情况几乎是没有的,所以在使用时,只能抓“主要矛盾”,即突出一个因素,而将其他因素固定,这样来安排实验。因此“优选法”还不是一个很精确的近似方法。
“正交设计”的基础是拉丁方理论与群论,可以用来安排多因素的试验,而且试验次数对各因素的各水平的所有组合数来说是大大地减少了,但对于某些工业试验与昂贵的科学实验来说,试验仍嫌太多,而无法安排。
1978年,七机部由于导弹设计的要求,提出了一个5因素的试验,希望每个因素的水平数要多于10,而试验总数又不超过50,显然优选法和正交设计都不能用,王元和方开泰提出了一个新的试验设计,即所谓“均匀设计”,将这一方法用于导弹设计,取得了成效。均匀设计属于近40年发展起来的“伪蒙特卡罗方法”的范筹,将经典的确定的单变量问题的计算方法推广后用于多变量问题的计算时,计算量往往跟变量个数有关。乌拉母(S.Ulam)与冯诺依曼(J.von Neumann)在40年代提出蒙特卡罗方法,即统计模拟方法,这个方法的大意是将一个分析问题化为一个有同样解答的概率问题,然后用统计模拟的方法来处理后面这个问题,这样使一些困难的分析问题反而得到了解决,例如多重定积分的近似计算。蒙特卡罗方法的关键是找一组随机数作为统计模拟之用,所以这一方法的精度在于随机数的均匀性与独立性。不论是均匀设计或配方均匀设计,其数据分析都要藉助于回归分析,要用到线性回归模型、二次回归模型、非线性模型,以及各种选择回归变量的方法(如前进法、后退法、逐步回归、最优回归子集等)。
影响腐蚀的因素众多,要通过试验来摸索,试验设计得好,则会事半功倍。均匀设计的思想也能用于配方试验,已在我国包括腐蚀研究的领域有较广泛的普及与使用[5],取得了一系列可喜的成绩。
但均匀设计只具有充分均匀性,而正交设计还具有齐整可比性。试验设计倾向对不同的方法取长补短,在不同阶段适当结合。均匀设计的分批是按试验结果直接逼近最优点,经计算机验证可知,均匀设计的分散性程度很强,突出性效果亦很好,因此特别在试验前期可以出一些好结果。但是对出好成果的均匀设计若改用正交设计,其平均效果可能也会很好。用均匀设计和正交设计从事开发工作,远比不采用设计好得多[6]。
①试验的因素和水平
a. 因素:在实验中,影响试验考核指该指标的量称为因素,因素是自变量(Xs),如试验中的材料、时间、温度、成分、浓度、流速、pH值等。通常将固定的因素在试验方案中并不称为因素,只有变化的因素才称为因素,固定因素称为因子;
b. 水平:是试验中各因素的不同取值,这些值称做该因素的水平。如因素A、B、C均有3个取值,D、E均有6个取值等。为了便于试验的安排,每个因素要根据以往的经验来选择一个试验范围,然后在试验范围内挑出几个有代表性的值来进行试验。
②因素和水平的选择
选择因素和水平是关系到一个试验能否成功的关键,使用试验设计应注意:
a. 因素选择。在一项试验中,应由有经验的研究人员和工人共同讨论决定从众多的有关因子中挑选出试验方案中的因素,在一次试验中,因素不宜选得太多(如超过10个),否则可能会造成主次不分。相反地,因素也不宜选得太少,如只选定1、2个因素,这样可能会遗漏重要的因素,或遗漏因素间的交互作用,使试验的结果达不到预期的目的。因素和水平的含意可以是广义的。例如5种材料用于试验,要比较不同材料的耐蚀性,这时“材料品种”可设定为1个因素,5种材料就是该因素下的5个水平 。
在试验设计时,试验因素(输入变量)有两种,一种是在试验时可以人为进行控制的,称可控因素;一种是人为无法控制的,称噪声(随机)因素;
b. 试验的范围控制。如果试验在试验室进行,试验范围大比较容易实现;如果试验直接在生产中进行,则试验范围不宜太大,以防产生过多次品,或产生危险。试验范围太小,不易获得比已有条件有显著改善的结果。历史上有些重大的发明和发现,是由于“事故”而获得的,也就是说试验的范围大大不同于有经验的范围;
c. 试验范围和每一因素的水平个数应匹配。试验设计的目的在于捕捉各试验因素对输出变量的最大影响,因此在选择试验因素的水平时,水平范围要足够宽,否则就可出现缩小甚至抵削变量影响,同时也看不出因素间交互作用对输出的影响。当然因素水平设置也不可过宽,否则同样可能缩小此因素的影响,或将其它因素的影响掩盖掉。过宽还可能超出允许操作范围,造成意外损失;
d. 水平的间隔和生产控制精度是密切相关的。如压力容器的工艺物料温度设定控制在100℃,控制精度只能作到±5℃,于是在生产过程中温度将会在100℃±5℃,即95-105℃波动。则试验温度设定的3个水平95℃、100℃、105℃之间间隔太小,应当加大,如90℃、100℃、110℃。
③因素的主效应和因素间的交互效应
在试验中用来衡量试验结果的量叫试验指标,在数理统计中,称试验指标为响应(response)。根据试验的目的,要预先确定一项或多项试验指标。
由于试验中总存在一些偶然因素的干扰,如室温变化、介质浓度波动、材料的不均匀性,这些偶然因素总称为随机误差。由于试验误差的存在,不可能产生理想的情况。实际上,当试验的水平和相应的结果为连续变量时,其数学模型也可以用回归方程来表达。有一点必须注意的是,模型中的主效应或模型中的线性回归效应都强烈地依赖于试验条件、试验范围。实际情况是多种多样的,例如X和Y之间可能有非线性回归关系,或其它相关关系。
④因素间交互作用的概念
首先,设有两个因素A和B它们各取2个水平A1、A2和B1、B2。这时共有4种不同的水平组合,其试验结果如图7-13。当B=B1时,A1变到A2使Y增加30-10=20;类似地,当B=B2时,A1变到A2使Y也增加40-20=20。这就是说A对Y的影响与B取什么水平无关,图7-13a。类似地,当B从B1变到B2时,Y增加20-10(或40-30=10),与A取的水平无关。这时,我们称A和B之间无交互作用。判断A和B之间有没有交互作用,选用图7-13b的作图方法更为直观。当图中的两条线平行时(或接近平行时),判断A和B之间没有交互作用,图7-13c、d给出了一个有交互作用的例子。
a. A和B之间无交互作用 b. A和B之间无交互作用
c. A和B之间有交互作用 d. A和B之间有交互作用
图7-13 因素间交互作用
交互作用在实际中是大量存在的,特别是在腐蚀试验中,许多因素间都有交互作用。当因素A、B 及其它们的试验指标Y都为连续变量时,可以建立Y和A、B之间的回归方程。若回归方程为式(7-3)时A对Y的影响由回归系数β完全决定,不受B取哪个水平的影响;同样,B对Y的影响由回归系数γ完全决定,不受A取哪个水平的影响;类似地,对Y的影响由回归系数α决定,不受取哪个水平的影响。这时A和B没有交互作用。
当A和B之间有交互作用时,回归模型不可能为线性的,其中一定有非线性的。最常见的模型之一为:
式中α、β、γ、δ为回归系数,ε为随机误差。这时若δ>0,称A和B之间有正交互作用;若δ<0,称A和B之间有负交互作用。
⑤全面试验和多次单因素试验
在一项试验中,当因素和水平确定后,如何设计该项试验主要有两种方法:
a. 全面试验。该方法将每一个因素的不同水平组合做同样数目的试验,例如将每个因素的不同水平组合均作一次试验。在一项试验中若有m个因素, 它们各有l1…lm个水平, 则全面试验至少需做l1×l2…×lm次试验。当因素的个数不多,每个因数的水平数也不多时,常用全面试验的方法,并且通过数据分析可以获得较为丰富的结果,结论也比较精确。当因数较多,水平数较大时,全面试验要求较多的试验。对绝大多数场合,做这么多次试验是不可能的。
b. 多次单因素试验。这个方法在工程和科学试验中常被人们所采用。当因素之间没交互作用时,这个结论是正确的;当因素之间有交互作用时,该结论一般不真。因此,多次单因素试验法有局限性。特别是,当因素的数目和水平数更多时,常常会得到错误的结论,不能达到预期的目的。
c. 正交试验法(正交设计)。所有的试验设计方法本质上就是在试验的范围内给出挑选代表点的方法。正交设计是根据正交性准则来挑选代表点,使得这些点能反映试验范围内各因素和试验指标的关系。统计学家将正交设计通过一系列表格来实现,这些表叫做正交表。例如表7-12就是一个正交表,并记为L9(34),这里“L”表示正交表“9”表示总共要作9次试验,“3”表示每个因素都有3个水平,“4”表示这个表有4列,最多可以安排4个因素。还有一批混合水平的表在实际中也十分有用,如 L8(4×24)、L12(23×3)、L16(44×23)等。
表7-12 正交表 L9(34)
在表7-13的正交试验设计中,可以看到有如下的特点:每个因素的水平都重复了3次试验、每两个因素的水平组成一个全面试验方案。这2个特点使试验点在试验范围内排列规律整齐,称为“整齐可比”。另一方面,如果将正交设计的9个试验点点成图(图7-14),我们发现9个试验点在试验范围内散布均匀,这个特点被称为“均匀分散”。正交设计的优点本质上来自“均匀分散,整齐可比”这两个特点。
图7-14 正交设计均匀分散性
d. 均匀设计。正交设计在挑选代表点时有两个特点:均匀分散,整齐可比。“均匀分散”使试验点有代表性;“整齐可比”便于试验数据的分析。为了保证“整齐可比”的特点,若在一项试验中有s 个因素,每个因素各有q 水平,用正交试验安排试验,则至少要作q2个试验,当q 较大时,q2将更大。对这一类试验,若要减少试验的数目,只有去掉整齐可比的要求。
均匀设计就是只考虑试验点在试验范围内均匀散布的一种试验设计方法,和正交设计相似,也是通过一套表来进行试验设计的,每一个均匀设计表有一个代号Un(qs)或U*n(qs),其中“U”表示均匀设计,“n” 表示要做n 次试验,“q”表示每个因素有q个水平,“s”表示该表有s列。的右上角加“*”和不加“*”代表两种不同类型的均匀设计表,如表7-13。通常加“*”的均匀设计表有更好的均匀性,应优先选用。
每个均匀设计表都附有一个使用表,它指示我们如何从设计表中选用适当的列,以及由这些列所组成的试验方案的均匀度。如表U*6(64)最多可以安排4个因素的试验。若用正交表安排3个6水平因素,至少要采用L36(63),该表最多能安排3个因素,可要做36次试验,而两个表的偏差一个为0.1875(U*6),另一个为0.1597(L36),相差并不十分大。由此例可见均匀设计的优点。表7-14是U*6(64)的使用表,它告诉我们,若有2个因素,应选用1,3两列来安排试验;若有3个因素,应选用1,2,3三列,…,最后1列D表示刻划均匀度的偏差(discrepancy),偏差值越小,表示均匀度越好。当试验数n给定时,通常Un表比U*n表能安排更多的因素。故当因素s较大,且超过U*n的使用范围时可使用Un表。
表7-13 U*7(74)
表7-14 U*6(64)的使用表
均匀设计有其独特的布(试验)点方式,其特点表现在:每个因素的每个水平做一次且仅做一次试验。任2个因素的试验点点在平面的格子点上,每行每列有且仅有一个试验点,如表U*6(66)的第一列和第三列点成图7-15a;这两个特点反映了试验安排的“均衡性”,即对各因素,每个因素的每个水平一视同仁;均匀设计表任两列组成的试验方案一般并不等价,例如用U*6(66)的1,3 和1,4列分别画图,得图7-15a、b。可见a的点散布比较均匀,而b的点散布并不均匀。均匀设计表的这一性质和正交表有很大的不同,因此,每个均匀设计表必须有一个附加的使用表。
图7-15 均匀设计的均衡性
当因素的水平数增加时,试验数按水平数的增加量在增加。如当水平数从9水平增加到10水平时,试验数n 也从9增加到10。而正交设计当水平增加时,试验数按水平数的平方的比例在增加。当水平数从9到10时,试验数将从81增加到100。由于这个特点,使均匀设计更便于使用。
均匀设计表的使用步骤和正交设计很相似,但也有一些不同之处。通常有如下步骤:
i.根据试验的目的,选择合适的因素和相应的水平;
ii.选择适合该试验的均匀设计表,然后根据该表的使用表从中选出列号,将因素分别安排到这些列号上,并将这些因素的水平按所在列的指示分别对号。
参考文献
[1] ISO 7539.7-2005.Corrosion of metals and alloys – Stress corrosion testing Part7: Method for slow strain rate testing
[2] GB/T 15970.7 -2017.金属和合金的腐蚀 应力腐蚀试验 第7部分:慢应变速率试验
[3] HB 7235-1995.慢应变速率应力腐蚀试验方法10
[4] HB 5260-1983.马氏体不锈钢拉伸应力腐蚀试验方法
[5] 卢志明,朱建新,高增梁。 16MnR钢在湿硫化氢环境中的应力腐蚀开裂敏感性研究[J].腐蚀科学与防护技术,2007,19(6):410-413
[6]夏之宁,堪其亭,穆小静,等。正交设计与均匀设计的初步比较[J].重庆人学学报(自然科学版),1999,22(5):112-117
免责声明:本网站所转载的文字、图片与视频资料版权归原创作者所有,如果涉及侵权,请第一时间联系本网删除。
相关文章
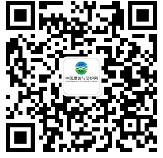
官方微信
《中国腐蚀与防护网电子期刊》征订启事
- 投稿联系:编辑部
- 电话:010-62316606-806
- 邮箱:fsfhzy666@163.com
- 中国腐蚀与防护网官方QQ群:140808414
点击排行
PPT新闻
“海洋金属”——钛合金在舰船的
点击数:7343
腐蚀与“海上丝绸之路”
点击数:5905