0 前言
铁基合金材料以优秀的强韧性、成型性和高性价比等性能被广泛应用于航空、航天、石油、化工、冶金等工业领域;由于工作环境严苛,要求铁基合金材料兼具各种优异性能,尤其是抗腐蚀性能。目前提高铁基合金的抗腐蚀等性能的方法是在合金表层沉积、喷涂、镀上或渗入各种合金元素(Cr、Al、Si、Ni、 Zn、RE) 以在表层形成保护层或牺牲层保护基体[1-3]。铁基合金加入足够多的Cr、Al、Si、Ti等合金元素,则会形成Cr2O3、Al2O3、SiO2、Spinel(尖晶石)等保护性氧化膜,从而提高抗腐蚀性能。已有学者探索了Fe-Cr及Fe-Al合金形成氧化膜的最低含量要求[4-5]。 Fe-Cr合金在常压下形成保护膜的最低理论含量为12%,实际中因为富铬碳化物的作用,实际要求高于17%[6]。 AHMED [7]发现在600℃, Fe-(10~12)Al合金可以形成具有保护性的外氧化膜。至于Fe-Al-Cr合金,为了平衡合金的机械性能与耐蚀性能,元素含量控制在A1 ∶ 8%~12%,Cr: 18%~27%。过多的合金元素会使合金的机械性能恶化,成本上升[4]。
预氧化处理工艺具有实施高效环保和保护层抗腐蚀能力强的特点,在工业界逐步得到重视。例如, 预氧化对提升FeCrAl合金在含KCl的O2 +H2O气氛中的抗腐蚀能力有极大的益处[8],预氧化可以显著改善Fe-21Cr-9Mn合金的抗腐蚀能力[9]。低氧压选择性氧化膜与基体间的黏附性强于在空气中形成的氧化膜,膜更平整、气密性更好[10-11]。 JANG等[5]的研究证实了Fe-5Al合金在800~900℃低氧分压下可以形成Al2O3 保护层,且Fe基体不发生氧化。 NAKAYAMA等[12]同样发现在H2/H2O控制的恒定低露点20℃下,Fe-5Al合金700~900℃ 形成含少量Fe的 γ-Al2O3 层,当温度高于920℃时形成含Fe的 α-Al2O3 层。对于FeCr合金而言,在低氧压10-22 MPa下,9%的Cr含量合金就足以形成保护膜[13]。 UNOCIC等[14] 研究了Fe-Al-Cr-Y合金在1 200~1 475℃ 的氧化行为,发现Al含量为5%~6%,Cr含量为10%~12%时,合金在125ppm氧压下可以形成保护层。最新研究结果显示FeAlCr合金在10-21.2~10-19.7 MPa下就拥有形成保护膜的能力[15]。由此可见,而在低氧压下,合金中少量的Al、 Cr、Si等活泼元素可以表面富集,形成均匀致密氧化膜;添加少量合金元素就可提高材料的抗腐蚀能力。因此,本研究通过分析各试验参数下的低氧压氧化现象,厘清Fe-3Al-6Cr合金在不同氧压下的氧化产物及氧化膜的耐腐蚀性能,为设计和开发耐腐蚀的Fe-Al-Cr合金提供参考。
1 试验准备
试验中使用的设计合金是Fe-3Al-6Cr(w/%)。通过真空电弧炉熔炼铸造合金锭,然后在真空中于1 000℃退火1周,以消除残余的机械应力并达到平衡。使用线切割机从合金锭上切下10mm×10mm× 1mm的样品,然后用碳化硅纸研磨,金刚石悬浮液抛光。抛光后的样品用丙酮和酒精超声清洗。最终将样品在流动的空气中吹干。在真空容器中加热金属及其氧化物粉末来获得平衡氧压[16-18],是目前普遍人工制造低氧压的方法。试验装置如图1所示。其制作过程参考Ranganathan的的试验方法。将Cr/Cr2O3 粉、Fe/FeO粉混合物按原子比分别为2 ∶ 1、1 ∶ 1配制、均匀研磨并压成块。制膜前将粉堆与合金试样分别放入干净的小坩埚中,然后放入石英管中,粉末放置于底端,石英管中部加热使之轻微凹陷,冷却后放置样品,随后用氩气洗气三次,待真空度为1.9×10-3 Pa,抽真空密封好。试验前将粉末端预热20min,待Cr/Cr2O3 粉、Fe/FeO粉混合物达到平衡时,装置垂直放入箱式炉中,进行热处理。 Cr/Cr2O3 粉、Fe/FeO粉混合物在950℃ 下相应的平衡氧压分别为10-23、10-16 atm.。样品在950℃,10-16、 10-23 和0.2atm.的3种氧压下对Fe-3Al-6Cr合金进行了预氧化试验,预氧化时间为10min、30min、 60min、300min、600min和1 200min。试验结束后,取出石英管空冷至室温后取出试样。使用扫描电镜(SEM,FE-SEM)、X射线衍射(XRD)、X射线光电子能谱(XPS)等手段对样品进行观察和分析。
图1 试验装置示意图
试验运用Factsage7.0中的Phase Diagramm模块,以FToxid和FSstel数据库计算得到的Fe-3Al-6Cr合金在600~1 000℃,10-30~10-10 atm.氧压下基体与氧化物的平衡相图。
试验采用中性盐雾试验测试Fe-Al-Cr合金进行选择性氧化前后的试样在盐雾条件下的耐腐蚀性能。盐雾箱内的NaCl溶液质量分数为5%,PH=6.5~7.2,箱内温度保持在35℃ ±1℃。初期每隔24h测试增重,后期每隔48h测试增重。
2 结果与讨论
2.1 选择性氧化的热力学分析
图2 为Fe-3Al-6Cr合金不同氧压和温度的计算氧化物相图,图2中红线以下区域稳定的氧化物是M2O3,代表Al2O3 和Cr2O3 混合,基体Fe不发生氧化。蓝线与红线围成的区域间出现了一个新的氧化相Spinel,代表FeM2O4(M ∶ Al+Cr,下同)。此区域内虽然Fe发生了氧化,但形成的FeM2O4 氧化层十分致密,粘附性好,可以抑制O的向内扩散,表现出优秀的耐腐蚀性能[19]。蓝线以下区域形成的氧化物M2O3、FeM2O4 致密,具有抵抗腐蚀的能力,是制备氧化膜的理想候选区。而蓝线以上形成的氧化物是FeO(Monoxide)、Fe3O4、Fe2O3 结构疏松,没有耐蚀性能。选取了950℃ 作为固定温度,研究了Fe-3Al-6Cr合金在10-23 atm.、 10-16 atm.与空气下即0.2atm.氧分压下氧化物随时间的变化以验证计算结果。
2.2 氧压对氧化行为的影响
Fe-3Al-6Cr合金在950℃ 不同氧压中氧化10min后的表面形貌如图3所示。图3a所用的是Cr/Cr2O3 粉末组,平衡氧压为10-23 atm.。试样表面表现为底部黑色组织上分布着大量白色蠕虫状组织,但是根据能谱分析,两者成分大致相同,底部黑色组织成分为O:22.7%,Al:14.3%,Cr:4.8%,Fe:5 8.3%。白色组织成分为O:20.7%,Al:10.6%,Cr: 10.2%,Fe:58.5%。根据能谱成分推断,结构都为(Al,Cr)2O3,唯一的区别是Cr含量的多少,由于Cr的扩散速度快于Al,所以上层的(Al,Cr)2O3 中含有较多的Cr含量。图4为Fe-3Al-6Cr合金在10-23 atm.、950℃ 氧化10min的表面XPS分析,Al2p3/2 峰值处于74.1eV,通过对照X射线光电子能谱数据库可以找出对应的氧化物是Al2O3。 Cr的XPS谱图与WANG等[20] 的试验数据相似,分为两个峰。 Cr 2p在576.1eV处出现了2p1/2 峰,在585.0eV处出现了2p3/2 峰,和已有公开的Cr2O3 数据相近。因此,EDS与XPS数据共同确认了表面氧化物为(Al, Cr)2O3。
图2 Fe-3Al-6Cr合金的计算氧化物相图
图3b所用的是Fe/FeO粉末组,平衡氧压为10-16 atm.。表面氧化物颗粒粗大且可以清晰的看到表面上的小孔。表面的能谱成分为O: 45.0%, Al: 0.3%,Cr: 0.7%,Fe: 54.0%,表面几乎没有Al、Cr元素,氧化物为FeO。图5a试样的XRD图谱,确认氧化物有FeO和Fe(Al,Cr) 2O4,由于在表面没有发现Fe(Al,Cr) 2O4,所以推断应该存在于内层。
图3 Fe-3Al-6Cr合金在不同氧压下950℃氧化10min的表面形貌
图4 Fe-3Al-6Cr合金在10-23 atm.、 950℃氧化10min的表面XPS图谱
图3c是Fe-3Al-6Cr合金在空气中即标准大气压1atm.,氧分压0.2atm.下,950℃氧化10min后的表面形貌。表层平坦,氧化膜完整覆盖基体表面, 根据图5b的XRD能谱,确认氧化物主体为Fe2O3, 含有少量(Al,Cr)2O3。
2.3 氧化时间对表面氧化产物的影响
2.3.1 Cr/Cr2O3 控制气氛
Fe-3Al-6Cr合金在950℃、Cr/Cr2O3 粉末组控制的10-23 atm.氧压下氧化不同时间后的表面形貌如图6所示。图6a与图6b都是由场发射扫描电镜拍摄,放大倍数都是15 000倍,图6c~6f是由普通扫描电镜拍摄,放大倍数都是2 000倍。从图6可以看出,随氧化时间的延长,白色颗粒由蠕虫状变为圆形再逐渐减少至消失。部分试样组织成分如图6所示,随氧化时间延长,表面氧化物由(Al,Cr)2O3 向A2O3 转变。在足够低的氧压下,不足以让所有Al、Cr元素发生氧化时,在氧化前期由于Cr的扩散速度快,先形成Cr2O3,但是进行到氧化后期时,Al元素会还原Cr2O3 形成Al2O3。从图6中可以看到在黑色(Al,Cr)2O3 膜(图6中以D-(Al,Cr)2O3 表示)上的同物种白色颗粒(Al,Cr)2O3(图6中以W-(Al,Cr)2O3 表示)中的Cr含量较高,随着氧化时间的延长,所有组织中的Cr含量都在逐渐降低而Al含量增加。
图5 Fe-3Al-6Cr合金在不同氧压下950℃ 氧化10min的XRD图谱
Fe-3Al-6Cr合金在950℃、Cr/Cr2O3 粉末组控制的10-23 atm.氧压下氧化10min和1 200min后的截面如图7所示。氧化膜极薄,难以看清氧化膜厚度。因此,对氧化10min后的样品进行了XPS深度剖析,元素含量随深度变化如图8所示,元素含量精确度远高于表1中的EDS数据。刻蚀时间为200s, 数据基本稳定,代表表层氧化膜厚度至少为50nm。氧化膜的主要组成为Al2O3,少量Cr2O3。 Cr2O3 没有在表层发生富集,仅基体中6%的Cr形成了稳定的Cr2O3。此外,在10-23 atm.氧压下,Fe不能发生氧化,以固溶方式存在于氧化膜中,含量为10%左右。因此,Factsage计算的氧化相图结果与试验研究结果完全符合。
图6 Fe-3Al-6Cr合金在950℃、10-23 atm.氧化不同时间后的表面形貌
图7 Fe-3Al-6Cr合金在950℃、10-23 atm.氧化不同时间后的截面
图8 Fe-3Al-6Cr合金在950℃、10-23 atm.氧化10min后的XPS深度剖析
2.3.2 Fe/FeO控制气氛
Fe-3Al-6Cr合金在950℃、Fe/FeO粉末组控制的10-16 atm.氧压下氧化不同时间后的表面形貌如图9所示。图9a由场发射扫描电镜拍摄,放大倍数为是15 000倍,图9b~9f是由普通扫描电镜拍摄, 放大倍数都是2 000倍。在10-16 atm.氧压下氧化10min的2 000倍图片在上图3b中已提及,表面的FeO形貌放大后如图9a所示,可以发现毛绒团块装的FeO是由无数细小碎片状的FeO组成的,且这些碎片状的FeO没有完全连成一片,堆叠处也显疏松。当氧化时间延长到30min时,FeO被部分还原,表面组织变为 α-Fe +FeO,具体成分如图9所示,局部出现了FeM2O4 从裂缝处生长出来。当氧化时间为300min时,表面的 α-Fe再次氧化为大片的毛绒FeO,下层氧化物为FeO+FeM2O4。当氧化时间延长至1 200min后,表面大片的FeO再次被还原,只余少量存在。覆盖了整个表面的灰色网格状组织与底下黑色组织都为 α-Fe+FeM2O4,其中上层组织中含Al:10.2%、Cr:11.7%,下层组织中Al: 7.8%、Cr: 10.4%。其上分布着许多白色细小FeM2O4 颗粒。
图9 Fe-3Al-6Cr合金在950℃、 10-16 atm.氧化不同时间后的表面形貌
图10 为图9中各试样的截面,可以发现明显的内氧化现象。图10a为Fe-3Al-6Cr合金氧化10min后的截面,出现了在表层没有发现的FeM2O4 相,与图5a的XRD图谱结果相符合。在截面中可以看到丝状的FeM2O4 相横向分布在距表面0~25 μm的深度范围,在距表层25 μm处有连成带状的趋势。而在氧化层与基体的交界处,发现了大量黑色点状相,其能谱结果如表1所示,O含量极少,富Al、Fe,查看Fe-Al二元相图,确认为FeAl相。 FeAl相的出现体现出基体中的Al元素向表层扩散偏聚而未与氧反应时会与Fe形成化合物。
图10 Fe-3Al-6Cr合金在950℃、10-16 atm.氧化不同时间后的截面
表1 图10中试样组织成分(a/%)
随氧化时间的延长,O原子向基体内部扩散的深度增大,氧化层与基体交界处的FeAl相与O接触反应形成了带状Al2O3 相。致密的Al2O3 层抑制了O原子的继续扩散,氧化层深度没有受氧化时间继续延长的影响,氧化物种类保持不变,为FeM2O4 与Al2O3。只有FeM2O4 相形态、成分随氧化时间延长发生了明显变化。在30~60min氧化时间内,与最内层Al2O3 层左侧接触的FeM2O4 层快速增厚,外层的丝状FeM2O4 相没有发生明显变化。当氧化时间延长到300min后,最内层的FeM2O4 相已生长至饱和,与氧化60min后的最内层相似,而开始外层的丝状FeM2O4 相生长增大。氧化时间为1 200min时,最内层Al2O3 层变得极薄, FeM2O4 分为两层,中间隔着 α-Fe层,此 α-Fe层没有探测到Al、Cr元素,可以证明是0~25 μm深度范围的Al、Cr元素不断向外层与内层形成FeM2O4 相,但基体中的活泼元素含量不足以形成连续的外氧化层。 Factsage计算的氧化相图显示Fe-3Al-6Cr合金在950℃、10-16 atm.氧化所得产物为FeO与FeM2O4。而在试验研究中,氧化初期(10min) 氧化物为FeO与FeM2O4,此外内层出现了FeAl化合物, 随氧化时间的延长, 氧化物稳定为FeO、 FeM2O4、Al2O3 。因此,试验结果与理论结果略有不同,理论结果计算出了表面氧化物种类,而内氧化物Al2O3 没有计算出。
2.3.3 空气气氛
Fe-3Al-6Cr合金在950℃、空气中氧化10~60min后的表面形貌相似,氧化10min的表面在上图3c中已有显示,氧化30min和60min的表面形貌如图11所示,不同之处是氧化30~60min后的试样表面混合氧化物Fe2O3 与(Al,Cr)2O3 的起伏程度轻微增加,且表面上出现了一些细小孔洞,这些孔洞意味着O原子能继续扩散进合金基体,这层氧化膜的耐蚀性是不够的。氧化300~1 200min后的试样表面形貌相同,以氧化300min的试样为例, 在氧化膜上出现了大颗毛绒球状的Fe2O3 。图11c右上角为矩形框内氧化膜的放大图,起伏程度明显增加。
图11 Fe-3Al-6Cr合金在950℃、 0.2atm.氧化不同时间后的表面形貌
图12 中显示了Fe-3Al-6Cr合金在空气中氧化30min和300min的试样截面。从图12a中难以看到氧化膜的厚度,图13显示了表层氧化膜的元素分布情况,当刻蚀时间为20~80s即刻蚀深度为6~24nm时,Fe2O3 在氧化膜中的占比较高,Fe2O3 与( Al, Cr) 2O3 的占比约为7 ∶ 3。刻蚀时间在100~200s范围时,Fe2O3 含量减少,( Al,Cr) 2O3 含量略有增长,比值为3 ∶2。当Fe-3Al-6Cr合金在空气中氧化超过300min后,大颗粒Fe2O3 会破坏Fe2O3 与( Al,Cr) 2O3 的混合氧化层,向基体内部继续扩展生长。
图12 Fe-3Al-6Cr合金在950℃、0.2atm.氧化不同时间后的截面
图13 Fe-3Al-6Cr合金在950℃、0.2atm.中氧化30min后的XPS深度剖析
2.4 氧化膜的耐蚀性能能力
图14 揭示了Fe-3Al-6Cr合金在950℃ 的Cr/Cr2O3 气氛下氧化10~600min的试样在盐雾测试中的耐腐蚀性能,由于氧化1 200min的试样氧化膜易剥落,所以没有参与测试。从图14中可以发现, 耐蚀性最强的为在Cr/Cr2O3 气氛下氧化30和60min的试样,其次是原始试样,为经过抛光而未进行氧化的Fe-3Al-6Cr合金片,此试样腐蚀480h后在边缘出现了了大量的铁锈,但增重并不明显。在Cr/Cr2O3 气氛下氧化10min制备的(Al,Cr)2O3 膜增重略高,说明此条件下制备的氧化膜并不完整, 耐蚀性较差。当试样在Cr/Cr2O3 气氛下氧化时间超过300min后氧化膜又会发生剥落现象,也不利于氧化膜的耐蚀性。
图14 Fe-3Al-6Cr合金在950℃、10-23 atm下氧化的试样在盐雾环境内的增重
图15 为Fe-3Al-6Cr合金在Fe/FeO和空气气氛下氧化30、60min后在盐雾测试中的增重曲线,从图15中可以看出在空气中氧化后30min、60min形成的Fe2O3 与(Al,Cr)2O3 混合氧化膜的耐蚀性能优于在Fe/FeO气氛下形成的 α-Fe+FeO+Fe(Al, Cr)2O4。但与图14比较,可以得出没有(Al,Cr)2O3 氧化膜的耐蚀性强。
图15 Fe-3Al-6Cr合金在950℃下10-16 atm.和0.2atm.氧压下氧化的试样在盐雾环境内的增重
盐雾测试中, Fe-3Al-6Cr合金在950℃、 Cr/Cr2O3 气氛中氧化30~60min后获得的(Al,Cr)2O3 氧化膜具有最强的耐蚀性。
3 结论
(1) Fe-3Al-6Cr合金在950℃、Cr/Cr2O3 控制的10-23 atm.氧压下制备的外氧化膜为(Al,Cr)2O3, 在空气中0.2atm.氧压下获得的是Fe2O3 与(Al, Cr)2O3 的混合氧化层,研究结果完全符合Factsage计算结果。
(2) 在Fe/FeO控制的10-16 atm.氧压下,氧化10min的外氧化物为FeO,合金内层存在内氧化物Fe(Al,Cr)2O4 与FeAl化合物。随氧化时间的延长,外层氧化物变为FeO+ Fe(Al,Cr)2O4,Fe( Al, Cr)2O4 的体积比逐渐增大, 内氧化物为Fe( Al, Cr)2O4 +Al2O3。 Factsage计算出了稳定后的表面氧化物种类,但没有计算出内氧化Al2O3 。
(3) Fe-3Al-6Cr合金在950℃、Cr/Cr2O3 气氛中氧化30~60min制备的(Al,Cr)2O3 氧化膜具有最好的耐蚀性。
参考文献
免责声明:本网站所转载的文字、图片与视频资料版权归原创作者所有,如果涉及侵权,请第一时间联系本网删除。
-
标签: 预氧化, Fe-3Al-6Cr, 氧化薄膜, 盐雾腐蚀
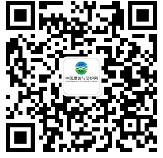
官方微信
《中国腐蚀与防护网电子期刊》征订启事
- 投稿联系:编辑部
- 电话:010-62316606-806
- 邮箱:fsfhzy666@163.com
- 中国腐蚀与防护网官方QQ群:140808414