油气井口装置包含大量连接站内设备设施的管道,其压力变化大、规格样式多、结构复杂,并担负着高温、高压、易燃、易爆和有毒介质的输送任务,在油气场站中扮演着重要角色。随着服役时间的增长,其管壁因受流体冲刷、电化学腐蚀、化学腐蚀等作用,会逐步产生管壁减薄、腐蚀、裂纹等缺陷,一旦发生泄漏失效,轻则影响生产进度并带来经济损失,重则将造成重大安全生产事故。
目前,主要通过人工检测方式对油气井口装置的管道腐蚀状况进行定期检测,此方式无法及时掌握检测间隔期间井口装置的实际腐蚀状况,并且当管道进行高危的压裂作业时,将无法采用人工方式进行检测。此外,腐蚀刮片是也是常用的管道腐蚀监测手段,但其实时性低且无法准确获得关键危险点的腐蚀情况。因此,亟需对相关管道的腐蚀在线检测开展技术研究,找到一种实时在线的井口装置易损部位腐蚀监测与智能预警方法。
压电超声测厚法因其稳定可靠、成本低,在管道腐蚀监测方面具有巨大潜力。因此四川大学机械工程学院和中国石油集团川庆钻探工程有限公司安全环保质量监督检测研究院的科研人员提出了使用一种可以进行液-固转变的耐候材料作为耦合剂的压电超声干耦合方法,同时利用温度传感器对管道表面温度进行在线监测,以消除不同温度下管道声速变化对腐蚀监测造成的影响。在此基础上,结合物联网技术、云平台技术等,开发了基于云平台的管道腐蚀在线监测系统,并通过现场应用验证了其实用性与推广价值。
基于云平台的管道腐蚀在线监测方案
针对管道腐蚀远程监测中的壁厚传感、多通道采集、无线传输、数据存储与分析等关键问题,结合井口装置腐蚀机理与监测实际需求,提出了基于干耦合压电传感的多通道腐蚀在线监测方法,以获取井口装置易腐蚀点多个部位的腐蚀数据,并通过信号处理系统与物联网通信系统接入云平台,进行数据存储与分析。
图1 油气钻采装备冲刷腐蚀在线监测系统框图
液-固转变耦合压电传感方法
由于流失和挥发问题,常规液体耦合剂不适用于管道腐蚀监测。另一方面,针对弧形管道,尤其是小曲率管道,探头与管壁之间的耦合更为困难,因此,需要研究一种易安装、不流失的干耦合方法。最佳的耦合剂是安装时为液态,可保证小曲率管道的耦合效果,安装完成后耦合剂变为固态,实现不流失、不挥发。同时,耦合剂还需保证在一定的高低温极端环境中声特性却不发生变化。针对上述需求,科研人员研发了一种可进行液-固转变的耐候材料,作为干耦合剂。
干耦合剂材料以聚二甲基硅氧烷为主要原料,辅以交联剂、填料、增塑剂、偶联剂、催化剂等混合而成,在室温下与空气中的水蒸气发生反应,达到固化的效果。该干耦合剂材料具有安装施工前为糊状半液态,施工后转化成固态的特点,可轻易地排除耦合间隙的空气,且无需较大的耦合压紧力,同时可耐户外自然老化。
干耦合材料合适的声特性阻抗是保证超声波能够有效进入管道的基础。为消除耦合层对测厚数值和精度的影响,回波-回波的超声测厚模式比较适合管道壁厚的检测。理想透射系数约为0.25,通过理论计算分析得到干耦合材料的声特性阻抗接近于压电晶片的声特性阻抗。因此,在研制干耦合材料时,可以以压电晶片声特性阻抗为参考。
图2 声波在压电晶片-耦合剂-管道3层介质中的传播模型
另外,当d远小于波长的时候,d越小声强损失越小。经试验对比发现,研发的耐候干耦合剂与传统耦合剂甘油的耦合效果相当。
在数字式超声测厚仪超声波接收电路增益固定为16.5dB的条件下,使用干耦合剂的超声回波脉冲幅值稍低于采用传统耦合剂甘油的超声回波脉冲幅值,如图3所示,信噪比良好。
图3 使用不同耦合剂的超声测厚仪波形显示
传感网络布局与传感器安装方法
探头安装状态是决定声波是否能够有效进入管道的关键。传感器安装的3个关键点如下:
(1) 布点选取。只有获得最易腐蚀的布点位置,才能够全面获得管道的健康状态。针对此问题,一般通过有限元仿真法获得在不同流体速度、颗粒含量、颗粒直径、管道结构等条件下的管道腐蚀速率与关键位置,同时结合实际管道腐蚀检测的工程经验,获得整个装置的最佳布置点。
(2) 传感器定位。只有精确的传感器定位,才能使超声波传播路径适应小管道、90°弯管外侧、三通等结构。
(3) 传感器固定。管道腐蚀监测系统需要长期工作,而井口装置在流体作用下会产生震动,压裂井口装置震动更为严重,因此需要对传感器进行固定,避免传感器松动导致耦合不良。
冲刷腐蚀一般在弯管外侧、变径、三通等位置较为严重,如图4所示,因此腐蚀监测方法侧重于对上述位置进行监测。
图4 管道冲刷腐蚀严重位置
在传感器定位方面,提出了一种基于磁吸附定位并结合钢扎带固定的传感器安装方法,如图5所示。
图5 干耦合超声监测探头安装现场
在设计过程中,需要实现传感器的小型化与轻量化,以满足狭窄空间的安装需求。另外,该方式不需要进行焊接即可固定,保证了油气站场的安全。
基于云平台的数据处理与显示方法
系统采用B/S(浏览器/服务器)架构方式监测数据,利用运营商所搭设的4G网络传输至云端,经过数据处理与分析后存储在云平台的数据库中。客户可通过网页浏览监测数据并进行互操作。具体来说,就是在云服务器中部署后台软件,对波形脉冲数据进行特征识别并计算厚度,最后将计算得到的厚度转发至客户端网页,供用户随时随地查看壁厚数据。后台软件兼顾壁厚寿命预测功能,可结合历史壁厚数据估算腐蚀速率,并预测管道的剩余寿命,为安全生产作业做出合理的指导;同时,每个通道设定报警阈值,当低于某个安全预设数值时,系统会自动报警并通知用户及时前往现场查验;用户还可根据需要通过客户端网页远程修改现场超声设备的唤醒周期、增益、激励脉宽等参数,以应对壁厚减薄对波形的影响。
现场测试
综合上述关键技术,开发了一种基于云平台的管道腐蚀监测系统,具体指标包括:通道数(不大于80个);采集频率(最高1次/h);工作温度(-20~100℃);壁厚动态监测精度(0.1mm);壁厚显示分辨率(0.01mm);软件功能(实时壁厚、腐蚀速率、预警功能、剩余寿命预测等);通信方式(4G网络);供电方式(电池);探头安装方式(磁吸附、钢扎带等多种形式);适应范围(不同管径、壁厚与形状的井口装置)。
图6 干耦合超声监测系统工作现场
如图6所示,将设计的干耦合管道腐蚀监测系统安装在某平台进行试验。将超声激励与采集系统、控制系统、通信模块与电源等放入防爆配电箱内,并连接工装探头与同轴电缆线,通过防爆挠性管引入防爆配电箱内。被测管道外径分别为76,134,146mm。根据现场工人的维护经验,将探头布置在采气树出气口阀门法兰连接处,采集频率为每天1次,在数据非采集期间设备将处于待机状态,以提高电池寿命。
图7 管道腐蚀监测结果
如图7所示,截取的是其中3个布点处近3个月的数据,其中布点1厚度由最初的28.39mm减薄到27.32mm,布点2厚度由30.63mm减薄到29.96mm,布点3厚度由37.88mm减薄到37.36mm。经过现场手持测厚仪验证和数据校验,系统监测结果在误差范围之内。目前管道腐蚀监测系统工作稳定,传感器各项指标均满足要求,干耦合剂性能稳定。
值得注意的是,高低温环境对腐蚀检测精度有一定的影响,需要通过测温或者采用标定板的方式进行消除。探头安装过程极为重要,当管道表面存在涂层或表面纹路时,需先进行清理,再布置探头,否则会影响信号强度与信噪比。
结论
1 使用液-固转变耦合剂可保证长期稳定、清洁的耦合效果,使压电传感器在耦合条件苛刻的环境下依然能够可靠地工作,为长期在线监测提供了思路。
2 基于物联网与云平台的B/S监测系统架构,可为用户提供一种便捷、可靠、灵活的监测数据管理与分析应用方案。
3 由于液-固转变耦合剂性能的限制,系统的服役温度应为100℃以下,后续研究人员将针对更高温度的监测需求,开展高温压电传感的研究工作。
免责声明:本网站所转载的文字、图片与视频资料版权归原创作者所有,如果涉及侵权,请第一时间联系本网删除。
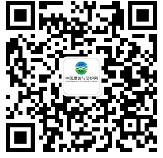
官方微信
《中国腐蚀与防护网电子期刊》征订启事
- 投稿联系:编辑部
- 电话:010-62316606-806
- 邮箱:fsfhzy666@163.com
- 中国腐蚀与防护网官方QQ群:140808414