摘要: 将原位微区电化学与传统宏观电化学技术相结合,应用电化学扫描显微镜(SECM)技术和电化学阻抗谱技术并结合微观形貌分析,研究了碳钢涂层缺陷处在不同交流电流强度下的腐蚀行为。结果表明:SECM拓扑形貌直观反映了碳钢涂层缺陷处局部腐蚀过程中电化学活性点的变化。交流电流使涂层缺陷处腐蚀活性点的数量明显增多,且使表面腐蚀产物积累对腐蚀产生的抑制作用明显减弱;浸泡初期涂层缺陷处的腐蚀为电子转移控制过程,浸泡10 h后转为扩散控制过程;随着交流电流强度的增大和浸泡时间的延长涂层的剥离程度提高,点蚀坑的深度和宽度随之增大。
关键词: 材料失效与保护 ; 原位 ; 碳钢 ; 腐蚀 ; 交流电流
中国内陆高原地区的昼夜温差大、风沙多和强紫外线使钢结构的涂层失效,严重威胁电网的安全。同时,在电网的小电阻、易放电部位(如涂层破损、剥落的缺陷处)产生的电流腐蚀加速了涂层剥离,使局部腐蚀愈加严重[1,2,3]。
扫描电化学显微镜(SECM)是一种基于电化学原理的原位高空间分辨率扫描探针显微技术,能实时观测研究系统的现场和三维空间,具有拓扑形貌和电化学活性表征功能等优势。SECM是研究腐蚀和涂层的有效技术手段[4,5]。张明明等[6]采用SECM技术结合电导率和伏安循环曲线研究了304L不锈钢在NaCl溶液中的点蚀行为,发现点蚀是不锈钢表面的不稳定电活性点形成的。周和荣等[7]用SECM研究了纯铝在NaCl溶液中的腐蚀行为,发现铝的表面腐局部区域先溶解,部分区域后溶解,不同区域腐蚀程度不同,且试样表面的氧化电流峰分布呈条带状。王新印[8]用SECM技术研究了纯镁的腐蚀行为,发现纯镁的腐蚀析氢速率随着Na2SO4浓度的增大而减慢,因为SO42-与H+结合使H+的活性降低。Y. González-García等[9,10]用SECM反馈收集模式研究了自我修复防腐涂层,发现在涂层破坏后释放甲硅烷酯并覆盖破损区使涂层愈合,防止基体继续腐蚀并提供了有效保护。
本文将SECM微区电化学和传统电化学手段相结合研究局部腐蚀的各自优势,以及在交流电流干扰条件下碳钢涂层缺陷处的腐蚀行为。
1 实验方法
将实验用碳钢线切割成尺寸为10 mm×10 mm×3 mm的试样。用60#水砂纸将试样表面打磨后在其背面焊接导线,然后将背面和侧面用环氧树脂封装,暴露出的面积为1 cm2。再将试样依次用200#~800#水砂纸打磨,用无水乙醇或丙酮清洗后放入干燥器中干燥24 h。将环氧树脂E51和聚醚胺D230按3:1的质量比配制防腐涂层试剂,将其均匀地涂刷在试样表面,在室温固化24 h后再在80℃恒温干燥3 h。涂层的厚度为120 μm。
在试样上制作面积为5 mm×0.5 mm的缺陷以模拟服役涂层在工况环境中因碰撞等原因产生的缺陷,用以研究缺陷处涂层的剥离过程。实验用溶液为质量分数为3.5%的NaCl溶液。
用KH-8700型三维视频显微镜观察试样的表面形貌和腐蚀形貌。观察缺陷处腐蚀形貌应先去除剥离涂层,再彻底去除腐蚀产物,进而观测缺陷处和剥离区域涂层下的金属腐蚀。除锈剂采用含乌洛托品缓蚀剂成分的盐酸溶液,在去除腐蚀产物的同时尽量保护裸露金属,不会破坏金属试样的形貌。
将制作出的试样表面用丙酮和无水乙醇擦拭并分组,放入装有NaCl溶液的电解槽中。用信号发生器分别给试样通入电流密度为50、100、300 A/m2、频率为50 Hz的交流电流,分别在0、5、10、24 h用SECM(CHI 920D)反馈模式对缺陷中部进行面扫描。氧化还原介质为KI。为了避免交流电流影响SECM信号、干扰试验结果,在浸泡过程中对金属涂层试样施加交流电到达目标浸泡时间立刻断开并开始SECM扫描。SECM扫描位置为线缺陷的中间位置,扫描时线缺陷处在扫描区域的中间。根据缺陷处涂层的剥离面积扫描范围(纵向长度和横向长度)最小为1000 μm×1000 μm,最大为3000 μm×1400 μm,扫描速度为10 μm/s,探针电位设置为0 V。实验装置的示意图,如图1所示。
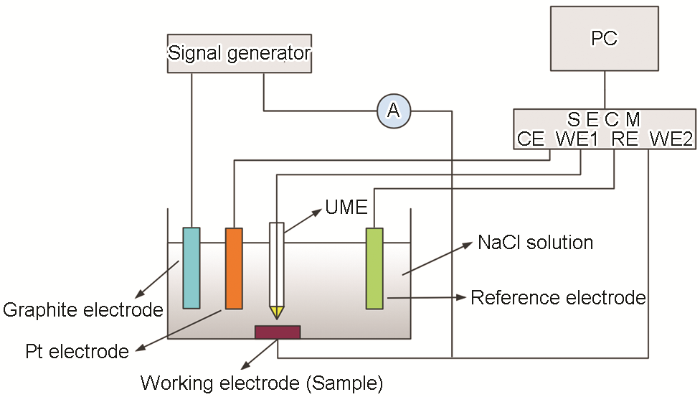
图1 SECM面扫描装置示意图
以传统的三电极体系为基础,进行电化学阻抗谱测试。涂层试样为工作电极,参比电极为有效工作面积为1 cm2的饱和甘汞电极,辅助电极为面积为4 cm2的铂电极。试样分别在0、5、10、24 h浸泡完之后,将电解池的参比电极、工作电极、辅助电极与仪器连接。测试前,先测试开路电位(OCP)15 min,稳定后测试电化学阻抗谱,测试频率范围为105~10-2 Hz,正弦交流电的波幅值为20 mA。
2 实验结果和讨论
2.1 SECM拓扑形貌
采用SECM的电流反馈模式以原位研究碳钢涂层缺陷处腐蚀过程中微区活性点的产生和变化以及拓扑形貌等信息,探讨不同浸泡时间、不同交流电流干扰强度对碳钢涂层缺陷处电化学活性点的影响,结合电化学阻抗谱技术和微观形貌分析,研究局部腐蚀特征及其机理。
SECM探针电流i的大小反映基底电极表面电化学活性[11,12,13]。探针电流i越大,电极表面电化学活性越大,腐蚀速率越大。图2~图5分别给出了涂层缺陷试样有无交流电流下不同浸泡时间SECM面扫描电流拓扑形貌图,反映了探针电流i的空间分布,颜色越靠近黑色(上端),电流越正且电流越大,为阳极电流,反之电流值越负,为阴极电流。较大的阳极电流对应的区域代表阳极区,阴极电流对应的区域代表阴极区。表1列出了涂层缺陷处不同交流电流强度下不同浸泡时间的最大探针电流峰值。探针电流为
图2 在无交流电流情况下不同浸泡时间试样的SECM图像
图3 电流强度为50 A/m2、不同浸泡时间试样的SECM像
图4 电流强度为100 A/m2不同浸泡时间试样的SECM像
图5 电流强度为300 A/m2不同浸泡时间试样的SECM像
表1 不同交流电流强度和浸泡时间涂层缺陷处的最大阳极电流峰值
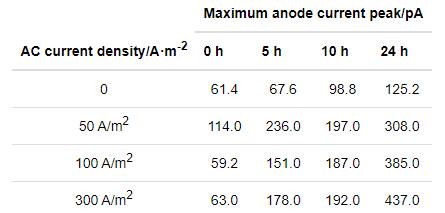
其中F为法拉第常数;C0为KI的浓度;D0为KI的扩散系数;a为探针的半径;n为电极反应的电子数。
没有交流电流干扰(图2)和在50 A/m2(图3)、100 A/m2(图4)、300 A/m2(图5)交流电流干扰下涂层的缺陷处均呈现明显的局部腐蚀特征,即随着浸泡时间的延长涂层缺陷处活性点的数量和分布在不断变化,最大阳极电流峰值不断增大(表1)。对比结果表明,有交流电流时涂层缺陷处腐蚀活性点的数量明显多于无交流电流时,最大阳极电流峰值约为无交流电流时的2.5~3.5倍,可见腐蚀明显加快,腐蚀加重。这一方面与基体微观不均匀性使微区活性点分布不均匀有关,另一方面与交流对电场的影响有关。研究表明[14,15]:施加交流一方面为体系补充了电极反应消耗的电量,从而加速了体系的腐蚀,而且交流干扰越大补充的电量越多;另一方面,施加的交流干扰越大正负电荷层积累的电子越多,加强了电极与溶液之间的界面电场,加速了体系的腐蚀。
同时,随着浸泡时间的延长涂层缺陷处活性点的数量在10 h时明显增多,表现为更多的电流尖峰;而浸泡24 h时活性点的数量开始减少,可能与表面腐蚀产物积累产生了一定阻碍作用有关,但是腐蚀活性点仍然较多。
图6给出了涂层缺陷试样在不同交流电流强度下浸泡不同时间SECM探针电流。可以看出:(1)在未施加交流电流时(0 h)涂层缺陷处的探针电流的数量级为10-11,随着浸泡时间的延长涂层缺陷处的探针电流不断增大,说明腐蚀电化学活性不断增大,局部腐蚀程度逐渐增大;(2)通电浸泡5 h探针电流稍有增大;浸泡10 h探针电流明显增大,比未施加交流电流时增大了近1个数量级,达到10-10数量级;浸泡24 h探针电流更明显增大;(3)在通电浸泡时间相同的条件下,交流电流强度越大则涂层缺陷处探针电流越大,腐蚀速率越大。施加的交流电流强度增大时涂层缺陷处发生的电化学反应加剧,电极反应的电子数n增大,探针电流i随之增大。
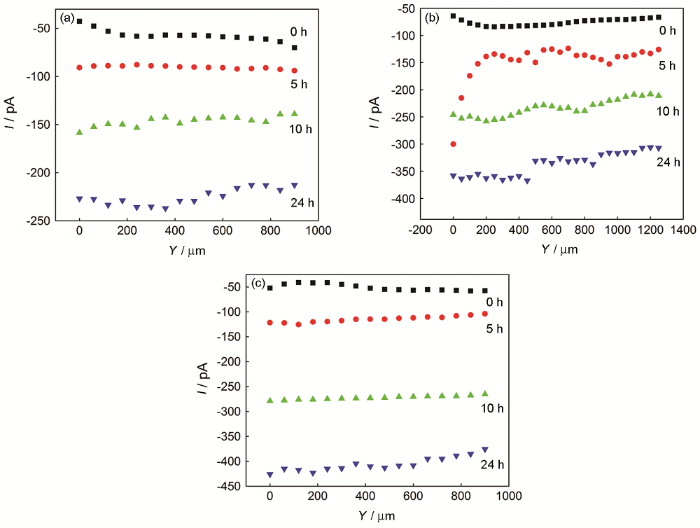
图6 不同交流电流强度和浸泡时间涂层缺陷处的探针扫描电流
2.2 电化学阻抗谱
图7给出了涂层缺陷试样分别在三种交流电流强度下不同浸泡时间后的电化学阻抗Nyquest图和Bode图。可以看出,在三种交流电流强度浸泡时间不同的条件下,涂层缺陷试样的Nyquest图和Bode图特征相近,均呈现两个常数的阻抗特征。其中的高频区域代表涂层的特性,而低频区域则反映了涂层/金属基材上的腐蚀反应。在交流电强度相同的条件下,随着浸泡时间的延长阻抗弧半径都是先变小再变大,浸泡10 h达到极小值。用图8中的等效电路拟合阻抗谱,拟合结果列于表2。其中Rs为溶液电阻,Rf、Cf分别为涂层电阻和涂层电容,Qd、Rp分别为金属/涂层界面双电层电容和界面电荷转移电阻,Zw为Warburg阻抗。Qd、Rp反映了涂层覆盖下金属基体的腐蚀速率[16,17]。电荷转移电阻Rp对应腐蚀反应速率电荷转移电阻越大,电极耐腐蚀性越好。图9给出了涂层缺陷处在三种交流电流强度浸泡时间不同的条件下Rp的变化。可以看出,在交流电流强度相同的条件下随着浸泡时间的延长Rp先减小后增大,浸泡10 h时骤降至极小值。
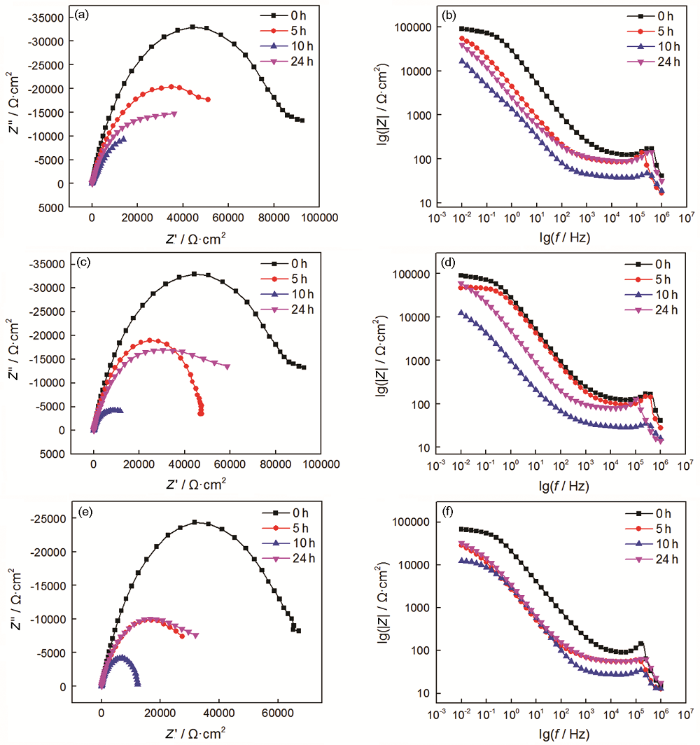
图7 不同交流电流强度和浸泡时间涂层缺陷处的Nyquest图和Bode图
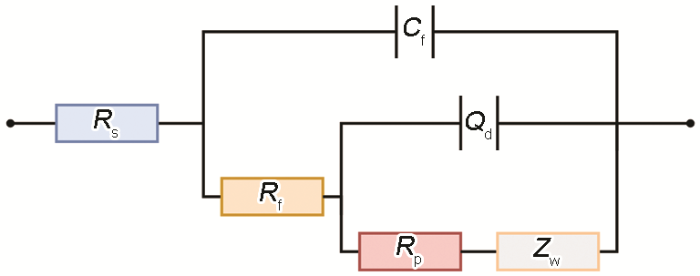
图8 涂层缺陷试样的电化学阻抗谱等效电路图
表2 各等效电路元件拟合结果

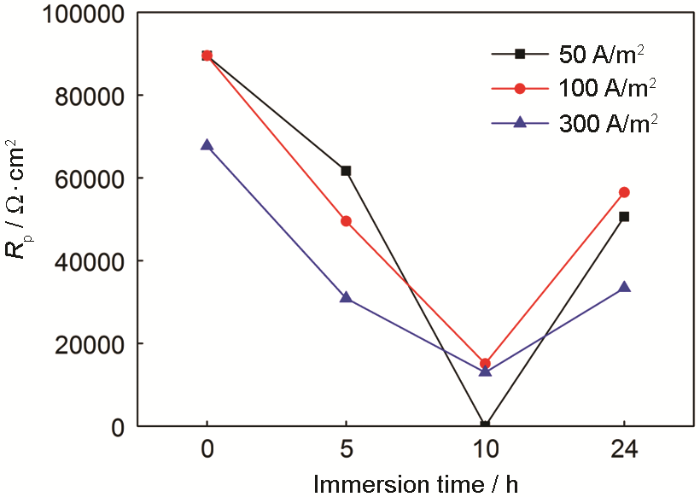
图9 不同交流电流强度和浸泡时间涂层缺陷处的Rp变化
涂层缺陷处金属腐蚀与缝隙腐蚀的机理类似,为氧浓差电池机理[18,19]。在浸泡初期腐蚀介质溶液和去极化剂O2通过涂层缺陷处直接扩散到金属基体表面,在活性点发生腐蚀并逐渐发展成点蚀,此过程为电子转移控制。浸泡至10 h时低频区的阻抗半径明显减小,Rp骤降至极小值,表明涂层性能发生了改变,发生了涂层剥离[16,21]。浸泡时间延长到10~24 h,腐蚀介质溶液和去极化剂O2需要通过腐蚀产物层才能进一步向内扩散。腐蚀产物增多增大了电子转移的阻力,浸泡10 h时电荷转移电阻Rp出现极小值,电子转移阻力达到最大,转为电解质溶液和去极化剂O2扩散控制[20]。腐蚀产物增多并在剥离处和缺陷处形成腐蚀产物层使剥离区域扩大,剥离程度加重,浸泡24 h涂层剥离的程度达到最大。
结合SECM结果可知,从浸泡初期到10 h涂层缺陷处表面活性点的数量开始从极大值减小,说明电子转移阻力开始增大。这个结果,与电荷转移电阻Rp反映出的浸泡10 h后电子转移阻力增大一致。
2.3 点蚀的形貌
表3列出了交流电流强度和浸泡时间不同条件下腐蚀坑的深度。可以看出,点蚀坑腐蚀的形貌与SECM的结果吻合。在未施加交流电的条件下涂层缺陷处的腐蚀量较小;浸泡5 h后,在三种交流电流强度下试样缺陷处金属基底的腐蚀坑深度相差不大。随着浸泡时间的延长,从10 h开始三种不同交流电流强度下试样缺陷处的腐蚀速率差异加大,且电流强度越大腐蚀越严重,涂层出现剥离。浸泡时间为24 h时300 A/m2电流强度下腐蚀坑的深度为238.4 μm,明显大于50 A/m2和100 A/m2时的腐蚀坑深度143.2 μm和154.1 μm。300 A/m2电流强度下腐蚀坑的宽度也明显大于50 A/m2和100 A/m2,因为涂层缺陷面积较小时缺陷处腐蚀产物不断扩散到剥离区,使阴、阳极区分离,阴极区碱性的OH-不断积累,降低了涂层与基体的结合力,涂层剥离程度不断增大[21]。
表3 不同交流电流强度和浸泡时间涂层缺陷处的腐蚀坑深度
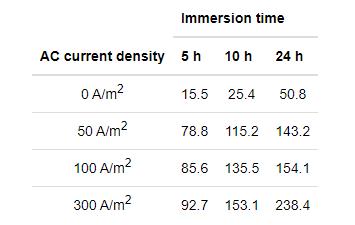
3 结论
(1) 有无交流电流,涂层缺陷处呈现不同的局部腐蚀特性。有交流电流时涂层缺陷处腐蚀活性点的数量明显高于无交流电流时,且表面腐蚀产物积累对腐蚀产生的抑制作用明显弱于无交流电流时。
(2) 随着交流电流强度的增大和浸泡时间的延长,涂层缺陷处的最大阳极探针峰值电流不断增大,涂层的剥离程度不断提高,点蚀坑的深度和宽度随之增大。
(3) 有交流电流时浸泡初期涂层缺陷处的腐蚀为电子转移控制过程,浸泡10 h时电荷转移电阻Rp出现极小值,转变为电解质溶液和去极化剂O2扩散控制。
参考文献
[1]Dong S J, Wang N. Research on high temperature urea cyclic corrosion resistance of stainless steel for SCR post processor [J]. Automob. Technol. Mater., 2017, (5): 41
[1](董善举, 王楠. SCR后处理器用不锈钢耐尿素高温循环腐蚀性能的研究 [J]. 汽车工艺与材料, 2017, (5): 41)
[2]Xu Z H, Zhang G L, Li M C, et al. Corrosion behavior of stainless steels in simulated automotive SCR environment [A]. Proceedings of the 10th China Iron & Steel Annual Meeting and the 6th Baosteel Academic Annual Meeting III [C]. Shanghai: China Metal Society, 2015: 975
[2](徐泽瀚, 张国利, 李谋成等. 不锈钢在汽车SCR模拟环境中的腐蚀行为研究 [A]. 第十届中国钢铁年会暨第六届宝钢学术年会论文集[C]. 上海: 中国金属学会, 2015)
[3]Shang C J. Research progress of ferritic stainless steel for automobile exhaust system [N]. World Metals, 2018-08-28(B08))
[3](尚成嘉. 汽车排气系统用铁素体不锈钢的研究进展 [N]. 世界金属导报, 2018-08-28(B08))
[4]Li M X, Shang C J. Corrosion study of stainless steels for commerial Vehicle SCR system [J]. Shanghai Coatings, 2018, 56(2): 5
[4](李明轩, 尚成嘉. 商用车SCR系统用不锈钢的腐蚀性研究 [J]. 上海涂料, 2018, 56(2): 5)
[5]Nocker J, Nyborg L, Norell M. Corrosion of stainless steels in simulated diesel exhaust environment with urea [J]. Mater. Corros., 2011, 63: 388
[6]Miraval C, Saedlou S, Evrard R, et al. Influence of Selective Catalytic Reduction (SCR) system on stainless steel durability [J]. Meta. And Mater., 2013, 66: 153
[7]Wang S D, Han P H, Ma R Y, et al. Effect of urea on condensates corrosion of stainless steels in simulated automotive exhaust environments [J]. Chin J. Soc. Corros. Prot., 2013, 33: 41
[7](王士栋, 韩沛洪, 马荣耀等. 尿素对模拟汽车废气环境中不锈钢冷凝液腐蚀行为的影响 [J]. 中国腐蚀与防护学报, 2013, 33: 41)
[8]Zhang Y F, Shores D A. Cracking and spoiling of oxide scale from 304 stainless steel at high temperatures [J]. J. Electrochem. Soc., 1994, 141: 1255
[9]Teng Y F. High temperature fatigue behavior of 429 and 429 Mo ferritic stainless steels [D]. Shenyang: Shenyang University of Technology, 2016
[9](滕云峰. 429与429Mo两种铁素体不锈钢的高温疲劳行为 [D]. 沈阳: 沈阳工业大学, 2016)
[10]Yun D W, Seo H S, Jun J H, et al. Molybdenum effect on oxidation resistance and electric conduction of ferritic stainless steel for SOFC interconnect [J]. Int. J. Hydrogen Energ., 2012, 37: 10328
[11]Jiang Y, Kim S, Lee J. Effect of different Mo contents on tensile and corrosion behaviors of CD4MCU cast duplex stainless steels [J]. Metall. Mater. Trans., 2005, 36A: 1229
[12]Li M X, Zhang W, Wang X L, et al. Effect of Nb on the performance of 409 stainless steel for automotive exhaust systems [J]. Steel. Res. Int., 2018, 89: 1700558
[13]Fujita N, Ohmura K, Kikuchi M, et al. Effect of Nb on high-temperature properties for ferritic stainless steel [J]. Scr. Mater., 1996, 35: 705
[14]Shu J. Investigation on corrosion resistance properties and formabilities of ferritic stainless steel used as aumotive exhaust system [D]. Shanghai: Shanghai Jiao Tong University, 2013
[14](舒俊. 汽车排气系统用铁素体不锈钢耐蚀性能和成形性能的研究 [D]. 上海: 上海交通大学, 2013)
[15]Li Z. Research on intergranular corrosion resistance of low chromium ferritic stainless steel [D]. Shanghai: Fudan University, 2013
[15](李钊. 低铬铁素体不锈钢耐晶间腐蚀性能研究 [D]. 上海: 复旦大学, 2013)
[16]Zhang H, Zhang G L, Liu X, et al. Condensate corrosion behavior of stainless steels for automotive mufflers [J]. Chin J. Soc. Corros. Prot., 2016, 36: 20
[16](张辉, 张国利, 刘星等.消声器用不锈钢的冷凝液腐蚀行为研究 [J]. 中国腐蚀与防护学报, 2016, 36: 20)
[17]Zhang C Q, Lv G M, Ouyang M H, et al. Research progress of nitride precipitation and its effects on corrosion resistance of high-nitrogen austenitic stainless steel [J]. Hot Work. Technol., 2018, 47(2): 33
[17](张昌青, 吕广明, 欧阳明辉等. 高氮奥氏体不锈钢氮化物析出及其对耐蚀性影响的研究进展 [J]. 热加工工艺, 2018, 47(2): 33)
[18]Guo Y Y. Study on the technology of plasma nitriding and plasma nitrocarburising of austenitic stainless steel in the low lem perature [D]. Shenyang: Northeastern University, 2008
[18](郭元元. 奥氏体不锈钢低温离子渗氮及碳氮共渗工艺研究 [D]. 沈阳: 东北大学, 2008)
[19]Nockert J, Norell M. Corrosion at the urea injection in SCR-system during component test [J]. Mater. Corros., 2013, 64: 34
[20]Saedlou S, Santacreu P, Leseux J. Suitable stainless steel selection for exhaust line containing a selective catalytic reduction (SCR) system [J]. SAE Int., 2011-01-1323
[21]Xiao J M. The Metallization of Stainless Steel. 2nd ed. [M]. Beijing: Metallurgical Industry Press, 2006
[21](肖纪美. 不锈钢的金属学问题. 第2版 [M]. 北京: 冶金工业出版社, 2006)
[22]Wan Z. Study on intergranular corrosion of ferrite stainless steel [J]. Corros. Prot. Petrochem. Ind., 2015, 32(4): 62
[22](万章. 铁素体不锈钢晶间腐蚀问题的探讨 [J]. 石油化工腐蚀与防护, 2015, 32(4): 62)
[23]Zhang H W. Research on Corrosion Resistance of Stainless Steel for Automotive Exhaust System [D]. Beijing: University of Science and Technology Beijing, 2013
[23](张宏伟. 汽车排气系统用不锈钢耐腐蚀性能研究 [D]. 北京: 北京科技大学, 2013)
[24]Chen C, Shang C J, Song X, et al. Condensate corrosion behavior of new style ferritic stainless steels used in automotive exhaust system [J]. Iron Steel, 2009, 44(10): 78
[24](陈超, 尚成嘉, 宋欣等. 新型汽车排气系统用铁素体不锈钢的冷凝液腐蚀 [J]. 钢铁, 2009, 44(10): 78)
[25]Salgado M F D, Rodrigues S C S, Santos D M, et al. Cyclic oxidation resistance of ferritic stainless steels used in mufflers of automobiles [J]. Eng. Fail. Anal, 2017, 79: 89
免责声明:本网站所转载的文字、图片与视频资料版权归原创作者所有,如果涉及侵权,请第一时间联系本网删除。
相关文章
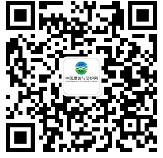
官方微信
《中国腐蚀与防护网电子期刊》征订启事
- 投稿联系:编辑部
- 电话:010-62316606-806
- 邮箱:fsfhzy666@163.com
- 中国腐蚀与防护网官方QQ群:140808414
点击排行
PPT新闻
“海洋金属”——钛合金在舰船的
点击数:7204
腐蚀与“海上丝绸之路”
点击数:5800