摘要
针对无铬达克罗防腐性能较差的问题,向涂液中添加不同含量石墨烯制备复合涂层以期提升涂层的耐蚀性能。实验采用硝酸铵快速腐蚀实验、浸泡实验、中性盐雾实验测试了涂层的耐蚀性能,利用SEM、EDS、XRD、Raman等方法观察分析了涂层腐蚀前后的组织形貌以及成分变化,明确了石墨烯在无铬达克罗涂层中的形貌与状态,并结合电化学实验,测试了4种涂层在模拟海水 (3.5% (质量分数) NaCl溶液) 中的Tafel极化曲线以及电化学阻抗谱,对其结果进行比较且应用相应的等效电路分析了其提高防腐性能的机理。结果表明:在腐蚀过程中Zn最先被消耗,Al与其他物质发生化学反应生成难溶于水的致密腐蚀产物;石墨烯以片状的结构嵌在锌铝粉之间,与片状锌铝粉相互交叠、保持平行,增加了涂层的致密性;加入少量石墨烯能够使无铬达克罗涂层的自腐蚀电位升高,腐蚀电流密度降低;涂层Nyquist低频半径和Bode幅值在同一时间段内的最大值均为0.12%石墨烯增强涂层,耐盐雾能力最佳。石墨烯加强了无铬达克罗涂层机械的壁垒保护作用,延缓了电解质溶液渗入的进程。
关键词: 无铬达克罗 ; 石墨烯 ; 耐蚀性 ; 电化学
Abstract
Composite coatings based on Cr-free Dacromet coating with addition of different amount of graphene were prepared aiming to increase the corrosion resistance of Cr-free Dacromet coating. The corrosion performance of the coatings was assessed via ammonium nitrate rapid corrosion test, immersion test and salt spray test. The state of graphene in composite coatings was characterized by means of SEM, EDS, XRD and Raman spectroscope. While the electrochemical behavior of coatings in artificial seawater (3.5% (mass fraction) NaCl solution) was comparatively examined via open-circuit potential measurement and Tafel polarization curve and electrochemical impedance spectroscopy, and the corrosion mechanism was analyzed with the corresponding equivalent circuits. The results show that: (1) Zn is first consumed in the corrosion process, and Al reacts with other substances to form dense corrosion products, which are insoluble in water; (2) graphene as sheet-like structure is embedded between Zn- and Al-powder, which is overlapping and paralleling with Zn flake and Al powder, thereby, increases the compactness of coatings; (3) a small amount of graphene can increase the corrosion potential and decrease the corrosion current density of Cr-free Dacromet coating, and accordingly; (4) the capacitive arc radius and impedance of the composite coatings reached the maximum when the graphene content was 0.12%, and the salt spray resistance of the coatings was the best. In conclusion, the graphene can strengthen the barrier effect of Cr-free Dacromet coatings and delay the inward migration process of the corrosive species from the electrolyte.
Keywords: Cu-free dacromet ; graphene ; corrosion resistance ; electrochemistry
本文引用格式
蔡家斌, 肖齐洪, 杨绿。 石墨烯对无铬达克罗涂层耐蚀性能影响[J]. 腐蚀科学与防护技术, 2019, 31(6): 565-575 doi:10.11903/1002.6495.2019.127
CAI Jiabin, XIAO Qihong, YANG Lv. Effect of Graphene on Corrosion Resistance of Chromium-free Dacromet Coatings[J]. Corrosion Science and Protection Technology, 2019, 31(6): 565-575 doi:10.11903/1002.6495.2019.127
达克罗技术是一种具有高防腐特性的金属表面涂层技术。达克罗涂层具有比一般传统电镀锌、热浸锌更为突出的优点,如高耐腐蚀性、无氢脆性、工艺简单等,但是达克罗中含有致癌的Cr6+,严重危害到人体健康[1]。为了解决这一问题,国内外科学工作者对达克罗涂层进行去铬处理。与传统达克罗涂层相比,无铬达克罗涂层中使用的是钝化剂,并且没有铬酐,这避免了Cr6+的危害,但在耐蚀性能上略逊于传统达克罗涂层。在此基础上,文献[2,3,4]分别研究了氧化钇、氧化锌、二氧化钛等纳米颗粒对无铬达克罗涂层耐蚀性能的影响,研究结果表明添加一些纳米颗粒可改善无铬达克罗的耐腐蚀性能。石墨烯作为一种特殊的二维纳米片,具有强度高、热稳定性好、阻隔性能优良和气液渗透性低等诸多优点[5],近年来,科研工作者们已尝试将其作为增强相加入到传统防护涂层中配置成复合涂层以提升涂层的某种性能。Liu等[6]将改性的石墨烯加入环氧树脂中,与纯环氧树脂相比,石墨烯的加入使其摩擦学性能和防腐性能有了显著的改善;Chang等[7]采用纳米铸造技术制备了环氧树脂/石墨烯复合材料 (EGCs) 作为疏水涂层 (HEGC),结果表明样品表面水滴的接触角从82 (环氧表面) 增加到127 (复合涂层),提高了涂层的疏水性。Ramezanzadeh等[8]合成了一种氨基化的氧化石墨烯 (FGO),并在低碳钢基体上采用FGO/环氧复合材料,通过盐雾试验和电化学阻抗谱 (EIS) 对其阻隔和腐蚀防护性能进行了表征,结果表明,在环氧涂层中加入0.1% (质量分数) FGO纳米片,能够提高涂层的阻隔性能,显著提高了涂层的耐腐蚀性。Christopher等[9]、Mo等[10]、Li等[11]通过加入功能化的石墨烯有效地提高了聚氨酯复合涂层的摩擦学性能和耐腐蚀性能;张松[12]研究了氧化石墨烯 (Hummers 法)、石墨烯纳米片、石墨烯干粉等石墨烯材料的加入对水性环氧富锌涂料性能的影响,结果显示防腐效果均有明显提升。
本文通过将不同含量石墨烯纳米粒子加入无铬达克罗涂层中制备石墨烯增强无铬达克罗涂层 (以下简称石墨烯增强涂层),以期提升无铬达克罗涂层的耐蚀性能,并确定最佳的石墨烯添加量。利用SEM、EDS、Raman、XRD等仪器以及电化学阻抗技术,研究了复合涂层的电化学腐蚀行为并解释其防护机理。
1 实验方法
试样基体为40Cr钢 (山东众鑫金属材料有限公司提供),其化学成分 (质量分数) 为:C 0.37~0.44,Si 0.17~0.37,Mn 0.50~0.80,Cr 0.80~1.10,Ni≤0.30,P≤0.03,S≤0.03,Cu≤0.30,Mo≤010,Fe余量。规格为10 mm×10 mm×4 mm。
为了除去金属表面的油膜和铁锈,确保基体表面光滑平整,提升涂液与基体之间的附着力,必须对基体试样进行前处理。实验先将工件浸入工业除锈剂中30 min,待初步除锈后,用流动的自来水清洗;再分别用100目、320目、800目、2000目和5000目的氧化铝砂纸打磨除锈后,对工件进行抛光处理,并用去离子水冲洗;将抛光后的工件浸入石油醚中,用超声波细胞粉碎机去除表面油污以及细小杂质,设置超声波细胞粉碎机功率为60%,工作15 s暂停5 s,持续30 min经去离子水冲刷和污水乙醇清洗,最后将样品用冷空气干燥,保存在无水乙醇溶液中备用。
实验前期采用正交试验法进行了大量的试验,确定涂液的初始配方以及石墨烯最佳添加量范围,在本工作中,实验将在其他成分含量不变的情况下,缩小石墨烯添加量的范围,并以一定的浓度梯度差配置涂液。
拟配置涂液50 g,配置过程分为3组。将KH560硅烷偶联剂 (AR)、乙二醇 (AR) 和去离子水在磁力搅拌器上常温下搅拌5 h,使硅烷充分水解,获得清澈透明的液体,记为A组;将Tween-20 (AR)、乙二醇、钼酸钠 (AR)、硼酸 (AR) 和去离子水在磁力搅拌器上常温下搅拌至缓蚀剂完全溶解,再加入片状锌粉铝粉 (工业级) 继续搅拌,直至粉浆完全分散均匀,记为B组;将石墨烯粉、Tween-20、去离子水和少量羟乙基纤维素醚混合搅拌均匀后,再先后用离心机和超声波细胞粉碎机进行去除杂质和超声分散,得到一定质量分数的石墨烯水性分散溶液,记为C组分。将上述A、B、C组份混合并搅拌,待充分混合均匀后 (约1 h),再依次将增稠剂和消泡剂加入混合溶液中,搅拌5 h。石墨烯改性无铬达克罗涂料的成分如表1所示,拟添加4种不同含量 (质量分数) 的石墨烯,分别为0%(0 g)、0.12%(0.06 g)、0.24%(0.12 g)、0.36%(0.18 g)。采用刷涂法将无铬达克罗涂料涂于经预处理的40Cr钢试样表面上,首先经90 ℃烘烤10 min,然后再在280 ℃下烧结25 min。经历两次刷涂和固化过程。

采用扫描电镜 (SEM,S-3400N) 观察涂层表面和截面形貌,并结合能谱仪 (EDS,Apollo) 观察涂层中元素分布及含量;采用激光显微共焦拉曼光谱仪 (LadRAM HR Evoluion) 检测涂层中的石墨烯;采用X射线衍射仪 (XRD,X′PertPowder) 检测涂层腐蚀前后组织成分变化。
电化学测试在25 ℃的3.5% (质量分数) NaCl 溶液中进行,测试运用DH7001电化学工作站,采用由铂电极、饱和甘汞电极和自制工作电极组成的三电极体系,工作电极面积为10 mm×10 mm,非工作面用环氧树脂密封。开路电位下进行实验,电位扫描范围为电极开路电位-0.25~+0.25 V,扫描速率为5 mV/s。电化学阻抗试验测量频率范围为105~10-2 Hz,扫描方向由高频至低频,扰动信号为幅值6 mV的正弦交流电位。每次测试均采用2个平行试样。
中性盐雾测试 (NSS),使用5% (质量分数) NaCl溶液 (pH=7),实验温度为35 ℃。按照GB/T 10125—2012标准,评估无铬达克罗涂层的耐蚀性能。
2 结果与讨论
2.1 涂层形貌及相成分
图1为不同石墨烯添加量无铬达克罗涂层SEM形貌。从图1中可以看出,各涂层表面较为平整,片状锌粉、铝粉片径大约从5~25 ?m不等,分布均匀致密,无明显孔洞和裂缝,在整个防腐过程中提供初步的阻挡作用。图中部分片状金属粉末会呈现亮白色的边缘,经EDS检测此处多为铝以及铝的氧化物,这是因为铝的吉布斯自由能ΔG比锌低,更容易被氧化,从而产生不导电的氧化物,故在扫描电镜下呈亮白色[13]。从图中还可以看出,加入石墨烯粒子前后涂层的表面没有明显变化,说明添加石墨烯粒子不会影响膜层的形貌特征。图2为0%石墨烯增强涂层与0.12%石墨烯增强涂层的截面图以及EDS谱。由图可知,涂层与基体结合较好,厚度大约为30~40 ?m之间。从图2b中能清晰的看到片状铝粉几乎与基体平行,层层相叠。结合EDS分析结果可知,0.12%石墨烯增强涂层中C的净强度远高于0%石墨烯增强涂层,说明在0.12%石墨烯增强涂层中该位置有明显的C,且极有可能为石墨烯。
为了更好地观察石墨烯的形貌以及在涂层中的存在状态,用5%的稀盐酸滴在不同石墨烯增强涂层上,使涂层表面的锌粉、铝粉迅速反应,尽量暴露出石墨烯以便观测。以0.12%石墨烯增强涂层为例,图3为0.12%石墨烯增强涂层滴入5%HCl后的表征结果,其中,图3b~d结果表明,在去除表层的锌粉、铝粉后,石墨烯 (对应Raman频移1350和1580 cm-1[14]) 呈平铺层叠特征,再结合图3a可以清晰地观察到石墨烯平铺镶嵌在锌铝粉之间,一起交错相叠,增加了涂层的致密性,从而有效减缓腐蚀介质向金属基体的浸入,起到物理屏蔽的作用。

2.2 涂层耐腐蚀实验分析

图5为涂层在3.5%NaCl溶液中浸泡了1030 h后的外观样貌图,从图中可以观察到,0%和0.36%石墨烯增强涂层均有明显的气泡出现,0%石墨烯增强涂层表面开始出现微微泛黄,0.36%石墨烯增强涂层出现明显腐蚀。0.24%石墨烯增强涂层表面较为平整,无明显气泡,但是试样边缘有点蚀现象出现。0.12%石墨烯增强涂层表面光滑平整,无气泡,无明显铁锈。在这4种涂层中,0.12%石墨烯增强涂层耐盐水性能最佳。

由图6对比可见,0%石墨烯增强涂层试样表面有严重腐蚀迹象,腐蚀向涂层内部扩展,可初步推测涂层与基体粘接性较弱;而0.12%石墨烯增强涂层试样整个表面完整,出现轻微的点蚀现象;0.24%和0.36%石墨烯增强涂层试样有明显腐蚀痕迹。

2.3 涂层形貌变化以及成分对比分析
观察图7并对比图1可知,经硝酸铵和盐雾腐蚀后的涂层表面较腐蚀之前相比更为平整,钝化效果明显;横向对比来看,图7a和b中0%石墨烯增强涂层表面相对粗糙,有明显层次感,0.12%石墨烯增强涂层表面则相对更加光滑、致密;图7c和d经800 h盐雾腐蚀之后0%石墨烯增强涂层中出现了大量孔洞,而0.12%石墨烯增强涂层中并无明显孔洞现象。图7表明添加少量石墨烯能有效防止腐蚀介质的垂直方向的渗透,减少孔洞现象的出现。
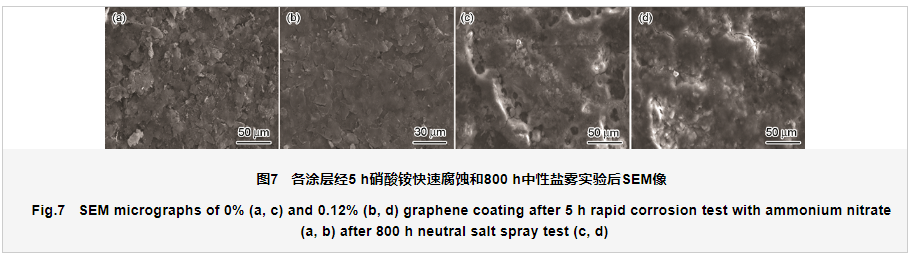
图8为0.12%石墨烯改性无铬达克罗涂层腐蚀前后XRD图谱,从图8a中可以看出,腐蚀前涂层的主要元素为Zn、Al、C (包含几种同素异形体) 和一些铝和硅的氧化物。图8b为涂层经过1030 h浸泡实验后XRD图谱,与图8a相比,富锌相的强度显著下降,43°峰强度由4500降至约100以下,36°和54°左右的峰消失不见,说明在腐蚀过程中Zn粉被大量的消耗,Zn粉被消耗是因为Zn比Fe活泼,其自腐蚀电位比Fe低,在腐蚀过程中充当阳极被优先腐蚀。同时,富铝相的强度也有明显下降,并且伴随Al的氧化物 (Al2O3、AlOOH和AlOCl) 出现。Al2O3在水中不稳定,通常会和水继续反应先后生成胶状的AlOOH和Al(OH)3膜,AlO-通常会与水和CO2反应生成更稳定的Al(OH)3,Al(OH)3与溶液中存在氯离子发生反应,生成碱式氯化铝Al5Cl3(OH)124H2O[15],这些难溶于水的产物晶粒细小,它的形成能够阻止腐蚀介质的继续侵入,有效地降低腐蚀速率。
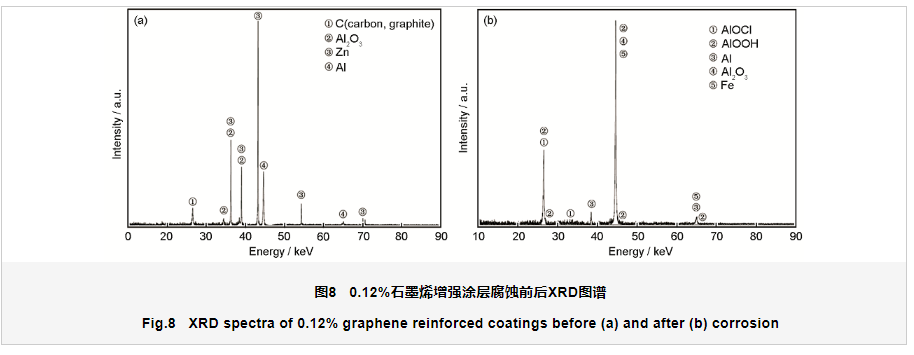
2.4 涂层耐蚀性能分析
2.4.1 涂层Tafel极化曲线分析
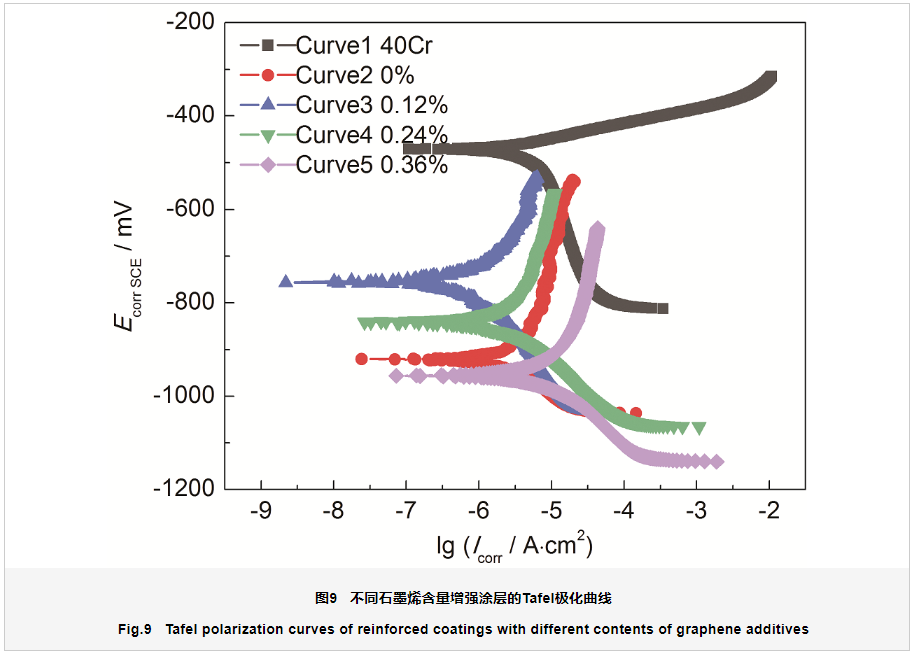
对比涂覆涂层试样的Tafel曲线 (曲线2、3、4、5) 可知,0.12%石墨烯增强涂层 (曲线3) 的自腐蚀电位最高,为-756 mV,比0%石墨烯增强涂层的-920 mV (曲线2) 向正向平移了164 mV;0.36%石墨烯增强涂层 (曲线5) 的自腐蚀电位最低,为-956 mV,比0%石墨烯增强涂层向负向平移了36 mV;0.24%石墨烯增强涂层 (曲线4) 的自腐蚀电位为-841 mV。自腐蚀电位能在一定程度上反映腐蚀倾向,自腐蚀电位越高,腐蚀倾向越低,自腐蚀电位由高到低依次为0.12%、0.24%、0%、0.36%石墨烯增强涂层。自腐蚀电流密度反映涂层的腐蚀速率,自腐蚀电流密度越低,发生腐蚀反应的速率越慢,防腐时间越长。图 10中,涂层试样自腐蚀电流密度由低到高依次为0.12%、0%、0.24%、0.36%石墨烯增强涂层,说明涂层中添加少量石墨烯纳米片可以使腐蚀电流密度降低,从而能有效提高涂层的防腐性能。

少量石墨烯纳米片的加入,使涂层自腐蚀电位正移和腐蚀电流密度降低的原因在于:石墨烯是十分稳定的片状结构,它的存在能够起到物理屏蔽作用,延缓腐蚀介质的渗透进程。而随着石墨烯含量的增加,自腐蚀电位反而降低且自腐蚀电流密度升高。这是因为石墨烯本身是导电性能十分优异的材料,随着石墨烯含量的增加,在涂层之间可能会出现石墨烯与石墨烯直接相连的情况,从而使得涂层的导电性增加,腐蚀电流密度升高。
图9中另一个明显的特征,加入石墨烯纳米片并没有使涂层的极化曲线的形状发生较大的变化。这表明在无铬达克罗涂层中添加石墨烯纳米片对其电极反应过程无影响。
2.4.2 涂层电化学阻抗谱分析
电化学阻抗谱法是采用小振幅的正弦波电位作为扰动信号对涂层体系进行测量的一种电化学方法,该方法能够在很宽的频率范围对涂层体系进行测量,因此它能获得更多的动力学信息[16]。如:在Nyquist图中,通过观察时间常数的个数以及各个频率段数值的大小来推测电极过程的状态变量,通常中低频区对应涂层的腐蚀反应,所包含的腐蚀变化较为复杂,而高频区可能与涂层的物理电阻有关[17,18]。在电化学阻抗谱Bode图中,相频图相角曲线的减小表示涂层电容值的增加和涂层电阻值的减小[19],而幅频图则直接反映涂层电阻情况。
图10为石墨烯增强涂层试样浸泡在3.5%NaCl 溶液中不同时间下的EIS图。由图10可以观察到,不同石墨烯含量达克罗涂层的电化学阻抗在浸泡期间内差异较大,低频区域更为明显,这是因为低频半圆给出了达克罗层中金属粉末的相关腐蚀反应的信息。根据EIS谱图中时间常数的变化以及低频区的圆弧半径小-大-小的演变趋势,将整个浸泡过程大致分为浸泡前期、浸泡中期和浸泡后期。
在浸泡初期,4种涂层的Nyquist曲线大致相同,但又有所区别。4种涂层在浸泡了1 d之后,出现略微平坦的半圆形。可以看出,阻抗谱仅具有一个时间常数,表明整个涂层等同于屏蔽层,将腐蚀介质和基体完全隔离。0.12%石墨烯增强涂层具有最大的电阻半径,说明此膜层很致密,此时腐蚀介质难以到达基体表面,但随着石墨烯含量的增加,其容抗弧半径反而减小。说明添加更多的石墨烯反而会降低涂层的耐蚀性能。从图11的相频图可以看到,由于电解质溶液的渗透,所有涂层低频区域的相角均随着时间的延长而逐渐减小。从图11的幅频图可以看出,所有涂层的|Z|值均有所增长,其中0.12%石墨烯增强涂层的|Z|值最大。浸泡初期阻抗谱所对应的物理模型则可由图12a中的等效电路给出。
随着浸泡时间的延长,从第5 d左右开始,各涂层开始陆续出现高频阻抗弧,此时进入浸泡中期。虽然高频区阻抗弧并不明显,但是出现了第二个时间常数,说明腐蚀介质已经接触到基底金属,并且在基体与涂层之间形成了腐蚀微电池,其阻抗反映涂层中的锌铝粉及其腐蚀产物。浸泡中期Nyquist谱低频容抗弧幅值变化不稳定,有升有降,频繁发生波动,但幅值总体呈上升趋势,0.12%石墨烯增强涂层低频容抗弧幅值同比依然最大。从图11的相频图中观察到,低频区域相角逐渐缓慢地向低频移动,这意味着暴露于腐蚀环境的基体面积正在慢慢增加。从图11的幅频图中可知,0.12%石墨烯增强涂层的阻抗值在同时段内依然最高,其防腐性能同比最好。同时还发现,曲线在中低频区域斜线越来越陡,斜率在-0.5至-0.3之间且向-0.5靠近,这是由于涂层中产生腐蚀产物和石墨烯的阻挡效应所导致的,电解质溶液顺着锌、铝粉之间的间隙向内渗透,曲折前行,腐蚀介质粒子并不完全沿着浓度梯度的方向传导。浸泡中期阻抗谱的等效电路如图12b所示。
浸泡后期跟浸泡中期相似,但是各涂层进入浸泡后期的时间有所差别。0%,0.12%,0.24%,0.36%石墨烯增强涂层分别在第49 d,88 d,76 d,19 d进入浸泡后期,说明石墨烯能一定程度上延缓腐蚀进程。该阶段阻抗谱同样有两个时间常数,不同的是低频区容抗幅值数值急剧减小。出现这种阻抗谱是因为最初存在于有机涂层中的浓度梯度随着宏观孔的形成而消失,并且暴露于腐蚀环境的基板面积逐渐增加。这种阻抗谱的阻抗复平面图及其等效电路图示于图12b。
2.4.3 拟合结果
根据图10中阻抗谱特征,将其测得的阻抗数据用Zsimp进行分析,并采用图12所示的等效电路进行拟合。拟合结果如图13所示。

图12a为涂层浸泡前期所对应的等效电路,Rs是参比电极与工作电极间的溶液电阻,Cc为涂层电容,Rc为涂层电阻。图12b为涂层浸泡中后期所对应的等效电路,Rp0为微孔电阻,Cc为涂层电容,用CPE1表示,CPE1-Rp0对应高频时间常数。Cp-Rp对应金属粉的腐蚀反应,为涂层中的腐蚀反应电阻,用来表征电化学反应的难易程度[4];在实际情况下,由于“弥散效应”的存在,大部分情况下阻抗谱上的半圆圆心都在x轴之下,或者是半圆呈扁平状。因此,通常采用常相位角元件CPE (用Q表示) 来代替纯电容C来拟合,优化拟合过程[20]。
由图13a可知,在浸泡前期48 h内,4种涂层的Cc的数值都急剧增加,且在随后的几天保持稳定。电容值增大是因为电解质溶液的渗入,由于电解质溶液具有较大的介电常数,其浸入到涂层中的孔隙当中后会显著增加涂层的电容。横向对比来看,0.12%石墨烯增强涂层具有最小的Cc值,与0%石墨烯增强涂层相比,浸泡48 h后比0%石墨烯增强涂层小210 ?F。较小的电容值代表较少的电解质溶液,说明添加少量石墨烯能够阻止电解质溶液的渗入。Rc为涂层电阻,通常反映涂层的孔隙率和实效程度。一般来说,Rc值和涂层中的缝隙、孔穴、空泡数量挂钩,电解质很溶液顺着这些孔隙穿过涂层,到达基体界面。0.12%石墨烯增强涂层的Rc值最大,说明添加少量石墨烯能使涂层间的微孔数量更少,水和其他腐蚀介质更难到达基体表面。
图13b~d表示涂层中后期电路参数的演变。极化电阻Rp反映涂层的腐蚀速率,Rp值越大说明涂层的腐蚀速率越慢。4种涂层Rp的数值逐渐增大,一直到浸泡中期的后半段才开始逐渐减小,这与图10的Nyquist图保持一致。浸泡中期Rp值增长较为迅速,是由于锌、铝粉的钝化作用,以及在浸泡过程中金属粉和电解质溶液发生的腐蚀反应。其产生的腐蚀产物会堵塞涂层孔隙,从而增大涂层电阻。横向对比来看,0.12%石墨烯增强涂层的Rp值在几乎各个时间段都为最大值。同时,与0%石墨烯增强涂层相比,0.12%石墨烯增强涂层在浸泡中期持续了更长的时间,这是因为石墨烯的存在增加了涂层的致密性,填补了涂层之间的缝隙,增大了涂层电阻,延缓了电解质溶液渗入的进程。同时,从图13b还可以发现,与0%石墨烯增强涂层相比,0.36%石墨烯增强涂层的Rp值反而更低。这一结果与浸泡过程中Cc的快速增加所表明的显著吸水率相一致 (图13c),0.12%石墨烯增强涂层的Cc值最小,0.24%和0%石墨烯增强涂层的Cc值依次增大,都没有明显的波动,表明其吸水性有限且稳定。而0.36%石墨烯增强涂层的Cc值急速增加,比其它3种涂层高了1个数量级。这是因为过多的石墨烯纳米片可能会发生团聚,堆叠在涂层间会割裂涂层的连续性,使涂层之间产生更多的孔洞,减少涂层致密性,更容易使腐蚀介质渗入。
综上所述,添加少量石墨烯能使无铬达克罗在前中后期获得更为优异的耐腐蚀性能。
3 结论
(1) 添加石墨烯增强了无铬达克罗涂层的致密性。石墨烯在无铬达克罗涂层中以片层状的结构形式存在,嵌在锌粉与铝粉层与层的缝隙之间,与片状锌铝粉保持平行,一起交错相叠排布。在腐蚀过程中Zn最先被消耗,Al与其他物质发生化学反应生成难溶于水的致密腐蚀产物,能够减缓腐蚀介质的进一步侵蚀。
(2) 添加适量石墨烯有助于提高无铬达克罗涂层的耐蚀性。随着石墨烯的增加,涂层的自腐蚀电位先升高后降低,自腐蚀电流密度先减小后增大,与0%石墨烯增强涂层相比,0.12%石墨烯增强涂层的自腐蚀电位高出164 mV,自腐蚀电流密度降低了一个数量级。在3.5%NaCl溶液浸泡下的各时间段内,0.12%石墨烯增强涂层始终有最大的低频容抗弧和阻抗值,在第19 d达到最大值25932 Ω·cm2。
(3) 0.12%石墨烯增强涂层耐蚀效果最好。在无铬达克罗中添加少量石墨烯能有效提升涂层的耐腐蚀性的原因在于,片状的石墨烯嵌在涂层之间增加了涂层的致密性,增大了涂层电阻,减少了孔洞的出现,起到了阻挡作用,延缓了电解质溶液在垂直方向渗入的进程。
参考文献
[1]
Xu G Q, Meng Z.
Study on non-chromate dacromet technology for magnesium alloy
[J]. Surf. Technol., 2006, 35(3): 51
[本文引用: 1]
(徐关庆, 孟中。
镁合金无铬达克罗工艺研究
[J]. 表面技术, 2006, 35(3): 51)
[本文引用: 1]
[2]
Qiao J F, Zhang M M, Zhang X L, et al.
Effect of yttrium oxide nanoparticles on corrosion resistance of chromium-free dacromet coating
[J]. Heat Treat. Met., 2016, 41(7): 178
URL [本文引用: 1]
(乔静飞, 张明明, 张小麟等。
氧化钇纳米颗粒对无铬达克罗涂层耐蚀性能的影响
[J]. 金属热处理, 2016, 41(7): 178)
URL [本文引用: 1]
[3]
Tong F.
Study on chromium-free zinc-aluminum coatings enhanced by nano materials
[D]. Nanjing: Nanjing University of Aeronautics and Astronautics, 2014
[本文引用: 1]
(仝飞。
微纳米材料增强无铬锌铝涂层研究
[D]. 南京: 南京航空航天大学, 2014)
[本文引用: 1]
[4]
Jiang Q, Gao X, Ji T A, et al.
Preparation and properties of water-based Chromium-free Zn-Al alloy coatings enhanced by nanoparticles
[J]. China Surf. Eng., 2018, 31(1): 123
[本文引用: 2]
(蒋穹, 高欣, 季铁安等。
纳米微粒增强水性无铬锌铝合金涂层的制备及其性能
[J]. 中国表面工程, 2018, 31(1): 123)
[本文引用: 2]
[5]
Fu H L, Zhao J P, Fang L, et al.
Application of graphene in corrosion protection of metals and its prospect
[J]. Surf. Technol., 2017, 46(3): 202
[本文引用: 1]
(付红丽, 赵继鹏, 方露等。
石墨烯在金属防护中的应用与展望
[J]. 表面技术, 2017, 46(3): 202)
[本文引用: 1]
[6]
Liu D, Zhao W J, Liu S, et al.
Comparative tribological and corrosion resistance properties of epoxy composite coatings reinforced with functionalized fullerene C60 and graphene
[J]. Surf. Coat. Technol., 2016, 286: 354
URL [本文引用: 1]
[7]
Chang K C, Hsu M H, Lu H I, et al.
Corrigendum to “Room-temperature cured hydrophobic epoxy/graphene composites as corrosion inhibitor for cold-rolled steel” [Carbon 66 (2014) 144-153]
[J]. Carbon, 2015, 82: 611
URL [本文引用: 1]
[8]
Ramezanzadeh B, Niroumandrad S, Ahmadi A, et al.
Enhancement of barrier and corrosion protection performance of an epoxy coating through wet transfer of amino functionalized graphene oxide
[J]. Corros. Sci., 2016, 103: 283
URL PMID:18717276 [本文引用: 1]
[9]
Christopher G, Kulandainathan M A, Harichandran G.
Comparative study of effect of corrosion on mild steel with waterborne polyurethane dispersion containing graphene oxide versus carbon black nanocomposites
[J]. Prog. Org. Coat., 2015, 89: 199
[本文引用: 1]
[10]
Mo M T, Zhao W J, Chen Z F, et al.
Excellent tribological and anti-corrosion performance of polyurethane composite coatings reinforced with functionalized graphene and graphene oxide nanosheets
[J]. RSC Adv., 2015, 5: 56486
URL [本文引用: 1]
[11]
Li Y Y, Yang Z Z, Qiu H X, et al.
Self-aligned graphene as anticorrosive barrier in waterborne polyurethane composite coatings
[J]. J. Mater. Chem., 2014, 2A: 14139
[本文引用: 1]
[12]
Zhang S.
Preparation and properties studying of graphene/water-borne epoxy Zinc-rich coating
[D]. Harbin: Harbin University of Technology, 2017
[本文引用: 1]
(张松。
石墨烯/水性环氧富锌涂料的制备及性能研究
[D]. 哈尔滨: 哈尔滨工业大学, 2017)
[本文引用: 1]
[13]
Ji L Y, Yao Z J.
Preliminary research on the technique of non-chromate dacromet coating
[J]. Electroplat. Pollut. Control., 2011, 31(3): 22
[本文引用: 1]
(季利亚, 姚正军。
无铬达克罗涂层的工艺研究
[J]. 电镀与环保, 2011, 31(3): 22)
[本文引用: 1]
[14]
Wu J X, Xu H, Zhang J.
Raman spectroscopy of graphene
[J]. Acta Chim. Sin., 2014, 72: 301
URL [本文引用: 1]
(吴娟霞, 徐华, 张锦。
拉曼光谱在石墨烯结构表征中的应用
[J]. 化学学报, 2014, 72: 301)
URL [本文引用: 1]
[15]
Jiang Q.
Research on preparation and corrosion mechanism of Zn-Al-based alloy coatings based on dacromet coating
[D]. Nanjing: Nanjing University of Aeronautics and Astronautics, 2014
[本文引用: 1]
(蒋穹。
基于达克罗技术的Zn-Al基合金涂层的制备及耐蚀机制研究
[D]. 南京: 南京航空航天大学, 2014)
[本文引用: 1]
[16]
Cao C N, Zhang J Q.
An Introduction to Electrochemical Impedance Spectroscopy
[M]. Beijing: Science Press, 2002: 155
[本文引用: 1]
(曹楚南, 张鉴清。
电化学阻抗谱导论
[M]. 北京: 科学出版社, 2002: 155)
[本文引用: 1]
[17]
Hu H L.
Development of chrome-free Zinc-Aluminum paints and the failure mechanism
[D]. Harbin: Harbin Institute of Technology, 2008
[本文引用: 1]
(胡会利。
无铬锌铝烧结涂料的研制及耐蚀机理
[D]. 哈尔滨: 哈尔滨工业大学, 2008)
[本文引用: 1]
[18]
Geng J F.
Research on the performance and preparation of chromium-free zinc aluminum alloy coating with new acrylic resin as binder
[D]. Nanjing: Nanjing University of Aeronautics and Astronautics, 2016
[本文引用: 1]
(耿建飞。
新增丙烯酸树脂粘结剂的无铬锌铝合金涂层的制备及性能研究
[D]. 南京: 南京航空航天大学, 2016)
[本文引用: 1]
[19]
Liu J G, Gong G P, Yan C W.
EIS study of corrosion behaviour of organic coating/Dacromet composite systems
[J]. Electrochim. Acta, 2005, 50: 3320
URL [本文引用: 1]
[20]
Hu H L, Li N.
Electrochemical Measurement
[M]. Beijing: National Defense Industry Press, 2007
[本文引用: 1]
(胡会利, 李宁。
电化学测量
[M]. 北京: 国防工业出版社, 2007)
[本文引用: 1]
免责声明:本网站所转载的文字、图片与视频资料版权归原创作者所有,如果涉及侵权,请第一时间联系本网删除。
相关文章
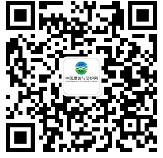
官方微信
《中国腐蚀与防护网电子期刊》征订启事
- 投稿联系:编辑部
- 电话:010-62316606-806
- 邮箱:fsfhzy666@163.com
- 中国腐蚀与防护网官方QQ群:140808414
点击排行
PPT新闻
“海洋金属”——钛合金在舰船的
点击数:7214
腐蚀与“海上丝绸之路”
点击数:5804