为改善轴承钢锻造后的不均匀组织,获得良好的机加工性能,并为淬火做好组织准备,以便淬火、回火后获得最佳的组织及性能,轴承钢都要进行球化退火处理。一般采用连续球化退火或等温球化退火,由于连续球化退火存在碳化物不均匀、能耗高等缺点,而逐渐被淘汰,等温球化退火大大缩短了工艺时间,能够灵活控制各个温度点,从而获得稳定均匀的球化组织。
本文主要介绍保护气氛辊底炉的结构特性,及其在轴承钢等温球化退火工艺中的控制应用,由于设备具备抽真空系统,有效隔离了进出料过程中空气造成的工件氧化,同时炉内通入保护气氛,并采用氧探头控制碳势,有效解决了工件脱碳问题。
1.球化退火的目的及要求
(1)降低硬度,一般要求GCr15:179~207HBW;GCr15SiMn:179~217HBW。
(2)获得细小均匀的粒状珠光体组织,退火组织的碳化物呈球状,按碳化物分布及形态,组织级别一般分为1级欠热、2~4级合格、5级碳化物不均匀和6级过热。
(3)脱碳层不大于单边最小加工留量的2/3。
2.保护气氛辊底炉结构、性能及工作原理
(1)设备由三工位上料台、前真空锁气室、加热保温区、中间门、等温球化区、降温区、后真空锁气室、三工位卸料台组成,设备全貌见图1。
图1 设备全貌
装、卸料台是料筐的进、出转运平台。
前、后锁气室通过抽真空,隔离进出料时的空气进入,避免对炉内气氛的影响。
加热区完成工件由原始片状珠光体组织转变为奥氏体组织,并将碳化物大部分熔解进入奥氏体中,为球化转变做好准备。
中间门将加热区与等温区隔离开,防止互相干扰。
等温区完成工件由奥氏体缓慢转变为球状珠光体组织,等温区进料端设计了风冷套降温系统,将工件温度迅速降低到低于珠光体开始转变温度,大大缩短了工艺时间。
降温区将结束组织转变的工件迅速降温至<180℃,防止工件出炉产生微量氧化,降温通过布置在炉壁两侧的水冷套和变频循环风扇完成。
(2)生产线各区配备温度及碳势控制仪表,所有机械动作采用PLC自动控制,过程参数、料盘信息及生产过程由上位机监控记录完成,永远保存备查,全部生产过程只需配备一名操作者。
辊底炉传动系统采用变频控制,能够实现不同产品的工艺周期可调。
工况面板显示全部动作过程及料盘位置,操作者管理设备一目了然,见图2。
图2 工况面板图
(3)此设备是全套进口技术,原设计不带中间门,加热区与球化区是相通的,由于两个区的控制温度差异,加热、冷却互相干扰,显得有些不足。
在长期应用过程中,国内进行了设计完善,增加中间门和炉底传动系统。设备改进后缩短了炉子的整体长度,从而降低了设备制造和维护成本,并降低了单位产品能耗。目前两种炉型在国内都有多个用户使用,我们对某单位同种产品的能耗进行过详细测量对比,无中间门的炉型单位产品能耗为0.330kWh/kg,增加中间门后能耗降低到0.274kWh/kg,按照每天产量18t,每年生产320天计算,每年节约电量18*1000*320*(0.330-0.274)=322560度,降耗效益相当可观。
附表是某用户采用增加中间门结构辊底炉在连续生产时的能耗统计数据。
总用电量:(电度表结束值—初始值)*电度表倍率 (75.4-70.4)*300=1500kW·h
每公斤产品能耗:总用电量/产品总重量=1500/5472=0.274kW·h /kg
设备生产能力:单盘装料1250kg/盘(毛重),产量750~800kg/h(净重),进料周期 60~80min可调,根据产品种类调整选择合适的进料周期,料盘按照物流方向运转,见图3。
图3 设备各区整体布局
3.等温球化退火工艺
首先将工件加热至高于Ac1温度并保温(一般设定780~810℃),完成奥氏体转变。
在随后的冷却过程中,如冷却速度足够缓慢或快冷至低于Ar1温度(一般设定700~730℃)进行等温,在等温过程中完成奥氏体向珠光体的转变,即溶入的碳化物将以粒状在未溶碳化物上或者新位置上析出,同时奥氏体转变为铁素体,基体上分布着粒状碳化物。粒状珠光体为球化退火的正常组织。典型等温球化退火工艺见图4。
图4 轴承钢等温球化退火工艺曲线
4.保护气氛及碳势自动控制
保护气氛采用氮气加丙烷,为了保持一定的炉压,要通入适量的氮气和丙烷常量,炉体上装有氧探头,在线测量炉内气氛,并通过碳控仪表控制辅助丙烷电磁阀,精确控制炉内碳势,产品全部生产过程在保护气氛中进行,做到既不脱碳也不增碳。按照轴承钢的生产实践,碳控仪表设定值在950~1050mv比较合适。
产品经过等温球化退火后,外观呈银灰色,不允许有氧化皮,脱碳层能够控制在<0.03mm,表面不允许有碳黑,禁止表面增碳。产品外观颜色见图5。
图5 保护气氛退火产品外观
5.影响产品组织、硬度及外观颜色的主要因素
(1)加热区影响因素
加热温度提高后,球化组织会变粗,甚至产生过热组织。反之球化组织就细小。
加热时间要保证能够完成适当的碳化物溶解,时间太短导致球化组织太细小,甚至残留未转变的锻造组织,特别是芯部转变滞后,更容易出现问题;反之时间过长造成球长大,甚至出现过热组织,通过调整进料周期可以改变加热时间。
(2)等温区影响因素
等温区设定的珠光体开始转变温度设定值高会形成较大球化组织,反之会形成较小的球化组织。
等温过程完成球化转变过程,等温球化的时间要保证足够长,否则球化不充分。
等温区出炉温度,即珠光体转变结束温度高,则硬度偏低;反之硬度偏高。
总之,通过调整加热区加热温度、等温球化区开始转变温度、等温区球化结束转变温度三个关键点,并通过改变工艺进料周期来影响冷却速度,从而获得相应的组织及硬度,即改变球状珠光体的大小和形态。
图6是保护气氛辊底炉在某用户现场调试时,轴承钢产品金相检测结果,评判为3级,球化组织和形态非常均匀。
图6 放大500X的球化退火组织
(3)外观颜色
产品出炉后,有时工件会呈现五颜六色的外观颜色,外观颜色对产品内在质量无影响,这往往是工件出炉温度高造成,增加降温区冷却水流速、控制好水温以及合理分配炉内气氛流向,一般能够得到很好解决,图7、图8是典型的外观颜色氧化色。
图7 套圈外观颜色氧化色
图8 钢球外观颜色氧化色
6.结语
保护气氛辊底炉很好解决了工件等温球化退火过程中的氧化脱碳问题,球化效果好,用户一致反映设备具有机械性能可靠、维护成本低、自动化程度高、产品质量稳定及单位产品能耗低等优点,被国内外众多轴承厂商采用。
国产化改进增加中间门,降低了设备成本和能耗,可以更精准的控制各区的温度,避免相互干扰,提高了产品质量稳定性。
脱碳层可以控制在<0.03mm,减少了机加工留量,降低了产品制造成本,尤其适合精锻毛坯产品的生产。
免责声明:本网站所转载的文字、图片与视频资料版权归原创作者所有,如果涉及侵权,请第一时间联系本网删除。
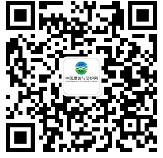
官方微信
《中国腐蚀与防护网电子期刊》征订启事
- 投稿联系:编辑部
- 电话:010-62316606-806
- 邮箱:fsfhzy666@163.com
- 中国腐蚀与防护网官方QQ群:140808414