有机涂层因能良好阻隔外界环境对钢结构材料的腐蚀而被广泛应用于海洋环境中[1],而水线区域是腐蚀最为严重和涂料最容易失效的区域,干湿交替是涂层失效的主要原因[2]。例如海上钻井平台所用的重防腐涂料,在海平面区域的涂层往往会经历周期性浸没在海水环境和暴露在大气环境中,故而通常遭受比单一浸没区域或大气区域更严重的损坏。有许多学者研究了干湿交替环境中涂层的失效机制,如Park等[3]使用电化学阻抗谱 (EIS) 监测环氧和聚氨酯双层涂层的吸水率,并讨论了在含Cl-环境中有机涂层暴露在干湿循环交替环境下的腐蚀机理。Coniglio等[4]通过重力液体吸附实验研究了100%固体环氧树脂涂层中水的吸附,并提出吸附-脱附循环交替可以增加水的移动速度。Zhao等[5]利用自制网格特性图 (SOM) 辅助EIS,研究了在干湿循环交替下碳钢表面有机涂层的失效过程。Lendvay-Gy?rik等[6]研究了苯乙烯-丙烯酸酯和醇酸-丙烯酸酯涂料等水性涂料的失效过程,认为干湿交替环境降低了其防腐性能,并指出膜吸水和脱水的循环过程促进了涂层孔隙增大。Allahar等[7]研究了在稀释NaCl溶液中周期浸润循环条件下环氧涂层的降解行为。Zhang等[8]利用EIS手段研究了浸泡条件下和不同干-湿比循环条件下铁红醇酸底漆的劣化过程,并指出与浸泡相比,4-4 h干湿循环大大加快了整个劣化过程,12-12 h的干湿循环使整个劣化过程减速。
环氧防腐涂料由于优良的防腐性能而被广泛用作海洋工程结构的底漆。我国渤海、黄海等海域潮汐类型为半日潮型。本文模拟了半日潮型的干湿交替循环频率,采用EIS对比研究了环氧防腐涂层在干湿交替和全浸两种环境下的失效过程,并借助扫描电镜 (SEM) 和Fourier红外光谱 (FT-IR) 等分析讨论了涂层的失效机理。
1 实验方法
1.1 实验材料及样品制备
实验中所用的金属基体材料为海洋平台用钢,其化学成分 (质量分数,%) 为:C 2.76,Mo 0.58,Si 0.24,Ni 2.61,Cr 0.79,Fe 92.48。钢片的尺寸为50 mm×50 mm×2 mm。参照国标GB/T 13288-1991《涂装前钢材表面粗糙度等级的评定》中关于涂装前钢材的表面粗糙度等级相关规定,将试样进行喷砂处理,再经丙酮超声除油,无水乙醇除水,吹干,置于干燥器中备用。
本实验所用的涂料是由哈尔滨工程大学研制的HGL-2环氧防腐底漆,使用前按A和B组分质量比3∶1混合搅匀。除去涂料中气泡,静置1 h后,均匀涂覆到备用钢片上,25 ?C固化24 h后,60 ℃固化48 h。采用PosiTector6000型测厚仪测定涂层厚度。选取固化后涂层厚度为 (100±5) μm的试样作为实验试样,进行EIS测试。
1.2 实验条件
在全浸泡和干湿交替两种环境下对涂层的防护性能进行了实验和评价分析。
1.2.1 全浸实验环境
模拟海水溶液浸泡,每周更换溶液。本实验所采用的模拟海水溶液配方参照国标GB/T 7790-2008,溶液配方及含量为:NaCl 23 g/L,MgCl2·10H2O 9.8 g/L,Na2SO4·10H2O 8.9 g/L,CaCl2 1.2 g/L。
1.2.2 干湿交替 (周期浸没) 实验环境
将试样浸泡于模拟海水溶液中6 h后,在空气中停留6 h (干燥阶段),一个测试循环周期 (C) 为12 h,以此循环往复。实验在自行设计的可调节干湿交替频率的干湿交替实验装置上进行,实验装置简图如图1所示。
图1 干湿交替实验装置
1.3 性能测试
采用PGSTAT302型电化学工作站进行EIS测试。测试过程中选用三电极体系:试样为工作电极,Pt片为辅助电极,饱和甘汞电极为参比电极 (SCE)。阻抗测试频率范围为105~10-2 Hz,扰动信号为20 mV,试样测试面积约为4.5 cm2,测试溶液为人工海水溶液。为了防止外界电磁信号的干扰,EIS测试在Faraday屏蔽笼里进行。测试得到的EIS数据均采用ZSimpWin软件进行拟合。
利用PosiTest附着力测量仪,采用拉开法对各体系涂层的干态附着力和浸泡或干湿交替循环不同时间的湿态附着力进行测试。湿态附着力测试是:将带涂层的试样在人工海水溶液中浸泡一段时间后,或是经过干湿交替循环一段时间后进行测试。每个体系有6组平行试样,计算附着力的平均值。
干湿交替循环过程中,采用质量法对涂层的吸水率进行测试。参考国标GB 1738-1979《绝缘漆漆膜吸水率测定法》。测试前要先对基体称重再进行涂装,待涂料完全固化在基体上再称量重量,由此计算涂膜重量,并记录涂膜的厚度。然后将其浸泡在模拟海水溶液中,浸泡一段时间后取出,用滤纸吸干表面水分后称重,求得吸水质量。在之后的每次循环里每隔一定的时间重复称重。涂膜的吸水率W计算公式如下:
W=mt-m0m0×100%
式中,m0是浸泡前干膜的质量,mt为浸泡t小时后涂膜的质量。每个体系均测量4个平行样,分别计算出该体系下不同涂层试样的吸水率,并取平均值。
利用JSM-6480型SEM对涂层下的金属基体进行微观形貌观察,并采用X射线能谱仪 (EDAX,JSM-6480A型) 对腐蚀产物进行成分分析;通过Spectrum 100型FT-IR对涂层浸泡/干湿交替前后官能团的变化进行分析。
2 结果与讨论
2.1 电化学阻抗谱
电化学阻抗谱能够提供丰富的界面信息[9,10,11]。如图2所示为涂层在全浸泡条件下浸泡2520 h期间电化学阻抗谱的变化情况。在浸泡前期 (图2a),水逐渐渗透进入涂层,涂层低频阻抗模值从3×1010 Ω·cm2下降至1×1010 Ω·cm2,容抗弧半径明显降低,相位角在较宽的频率范围内接近-90?,仍呈现出纯电容性特性,此阶段为涂层渗水阶段,阻抗谱呈现一个时间常数特征。在浸泡288 h后 (图2b),涂层低频阻抗模值下降至1×109 Ω·cm2,Bode图低频区出现平台,呈现双电容特征,双容抗弧表明水已经渗入金属表面,涂层/金属界面开始发生反应,为浸泡中期阶段。在浸泡288~1896 h期间,涂层低频阻抗模值从1×109 Ω·cm2缓慢下降至约1×107 Ω·cm2,下降了2个数量级。进入浸泡后期2016~2520 h (图2c),Nyquist图出现了高频段的一半圆弧加低频段与实轴呈现约45?的Warburg阻抗扩散尾,Bode图低频阻抗再次快速下降至107 Ω·cm2以下,最后低于1×106 Ω·cm2,涂层屏蔽性能丧失,失去了防护作用。低频扩散尾的出现可能是因为随着基体金属腐蚀反应的不断进行,越来越多的腐蚀产物在金属表面沉积覆盖,使得界面腐蚀反应受传质扩散过程控制[12]。
图2 涂层在不同浸泡时期下的阻抗图
图3所示为涂层在干湿交替条件下经194个循环期间的电化学阻抗变化情况。在干湿交替循环前期 (图3a),涂层阻抗谱的Nyquist图为高阻抗的单容抗弧。经过40个循环 (480 h),随着时间延长,容抗弧半径逐渐减小,涂层低频阻抗模值从1×1011 Ω·cm2下降至2×1010 Ω·cm2,相应的Bode图相位角在较宽测试频率范围内接近-90?,表现为典型的涂层渗水阶段的阻抗谱响应特征。从第66个循环开始,Nyquist图低频段出现波动,从单容抗弧快速变换为双容抗弧,表现为两个时间常数特征,但是低频段的半圆弧表现并不明显。在66~144个干湿交替循环期间,Bode图低频阻抗模值快速下降到1×107 Ω·cm2。第二个时间常数的出现说明此时腐蚀性介质已经渗透到涂层/基底界面,界面区基底金属开始发生反应。进入浸泡后期 (图3c),在156~210个干湿交替循环 (约2500 h) 期间,Nyquist图低频段呈现圆弧特征,低频段与实轴没有呈现45?的Warburg阻抗扩散尾,也没有明显的扩散特征,其原因可能是此干湿循环阶段涂层/金属界面上的界面反应不受离子传质过程控制,阻抗谱仍然呈现出两个时间常数。
图3 涂层在不同干湿交替循环时期下的阻抗图
2.2 涂层的低频阻抗模值的演化
低频阻抗模值可以反映涂层的防护性能[13]。图4为涂层在模拟海水中全浸泡和干湿交替循环过程中低频阻抗模值|Z|0.01 Hz随浸泡时间的变化曲线。可见,在干湿循环前期的40个循环期间,低频阻抗模值略有下降,之后缓慢下降。在144个循环之前,涂层低频阻抗模值都高于同一时期全浸泡涂层约1个数量级,具有良好的防护作用;在后期144~210个循环期间,涂层的低频阻抗模值快速下降,低于同一时期浸泡条件下的低频阻抗模值。对于全浸泡涂层而言,在浸泡初始的约100 h,低频阻抗模值急剧下降,但仍然保持较高的值,仍具有较高的防护性能,之后略有上升。之后,低频阻抗模值保持缓慢下降的趋势。随着浸泡时间的延长,水分子、氧气及腐蚀性离子如Cl-等穿过涂层渗入到基体表面,基体开始发生腐蚀反应。涂层在经2520 h浸泡后,低频阻抗模值下降至106 Ω·cm2以下,失去防护性能。
图4 涂层在全浸泡及干湿交替循环后的低频阻抗模值|Z|0.01 Hz变化谱
2.3 涂层宏观形貌
经过2050 h浸泡及干湿交替210个循环后,环氧防腐涂层试样表面宏观形貌如图5所示。在全浸泡2050 h后,涂层表面发生了鼓泡现象,鼓泡数目较少。干湿交替210个循环后,涂层表面发生了大量的鼓泡现象,鼓泡数目较多,鼓泡现象较为严重。干湿交替环境对涂层的破坏能力更大。
图5 全浸泡2050 h及干湿交替210个循环后试样的宏观表面形貌
2.4 附着力变化
涂层附着力是衡量涂料性能的重要指标之一[14]。附着力越高,说明涂层与金属基体结合强度越大,防护性能越好[15]。图6是在干湿交替及全浸泡条件下涂层的干态及湿态附着力测试结果。
图6 全浸泡和干湿交替暴露条件下涂层的附着力随时间的变化
可以看出,随着腐蚀时间的延长,两种涂层的附着力均呈现下降趋势。在实验之前,涂层的干态附着力达到19 MPa以上,具有很高的附着力。在腐蚀1000 h后,两种条件下涂层湿态附着力无明显差别,涂层附着力在12~14 MPa之间,仍然具有较高的附着力。但在腐蚀1800 h之后,干湿交替条件下涂层的湿态附着力明显低于同一时期全浸泡条件下涂层的湿态附着力值。浸泡2500 h之后,全浸泡条件下涂层的湿态附着力为7.62 MPa,而干湿交替条件下涂层湿态附着力仅为4.85 MPa。干湿交替条件下涂层的湿态附着力低于全浸泡条件下涂层的附着力。
图7给出了环氧防腐涂层经不同时间 (0,300和2500 h) 全浸实验,并经附着力测试的拉拔实验后的表面形貌照片。从涂层浸泡前的拉拔实验表面照片中可见,拉拔后没有可见的金属基体裸露出来,说明此时断裂面是从涂层内部发生的,被拔掉的只有涂层,说明涂层与金属之间的附着力高于19.45 MPa。浸泡300 h后,从金属基体上拔掉的涂层破损面积很小;而浸泡2500 h后,大块涂层被拔掉。
图7 经不同时间全浸实验后涂层样品进行结合力测试的拉拔实验后的表面形貌照片
图8给出了环氧防腐涂料在不同海水周期浸没循环阶段 (0,300和2500 h) 的附着力拉拔实验后的表面形貌照片。从涂层浸泡前的拉拔实验表面照片可见,和全浸泡条件类似,拉拔后没有可见的金属基体裸露出来,对应附着力为18.83 MPa。干湿循环300 h后,拉拔实验后仍然没有金属基体裸露出来,此时涂层湿态附着力仍然高达16 MPa。浸泡2500 h后,干湿循环涂层剥离面积大于全浸泡条件下涂层剥离面积,此时涂层的附着力只有4.85 MPa。
图8 干湿交替条件下不同阶段涂层/金属体系拉拔实验后表面形貌照片
2.5 讨论
2.5.1 FT-IR
为了探索涂层失效的原因,利用FT-IR测试方法分析涂层在干湿交替环境及全浸泡条件下防护性能发生变化的内部原因[16,17]。图9为HGL-2环氧防腐底漆在干湿交替及全浸泡条件下涂层失效后的红外分析谱。可见,在3369 cm-1处为环氧树脂的羟基伸缩振动峰,2924和2871 cm-1处为C—H振动峰,1732和1607 cm-1处为苯环骨架振动峰,1296 cm-1处为羧基官能团C—OH弯曲振动形成的吸收峰,1243 cm-1处为芳基醚的伸缩振动峰,1084 cm-1处为烷基醚的伸缩振动峰,828 cm-1处为芳香环中的C—H弯曲振动峰,797 cm-1处为环氧基团的吸收峰,557 cm-1处可能为Fe—O键的振动峰。可以看出,相对于原始涂层试样的红外谱图来说,经过干湿交替循环及全浸泡实验后,红外谱图上各个基团的吸收峰位置仍然存在,说明环氧防腐涂层在干湿交替或全浸泡环境下涂层内部分子链降解程度很小,基本上没有发生明显的变化,在一定程度上表明两种条件下涂层的失效不是由涂层内部分子链以及相关键的断裂所致。
图9 干湿交替及全浸泡条件下涂层失效后的FT-IR谱
2.5.2 阻抗拟合
根据图2和3阻抗谱变化图可知,涂层在浸泡开始时都表现为一个时间常数,选用图10a中的等效电路进行拟合;当涂层出现两个时间常数后,选用图10b的等效电路进行拟合;浸泡后期当出现Warburg扩散尾阻抗,则采用图10c的等效电路进行拟合[18]。其中,Rs代表溶液电阻,Qc和Rc分别代表涂层电容和涂层电阻,Qdl和Rt分别为金属腐蚀反应的双电层电容和金属腐蚀反应的电荷转移电阻,Zw代表Warburg扩散电阻。
图10 不同时期的等效电路图
图11为全浸泡及干湿交替条件下Rc随时间的变化曲线。Rc反映了涂层阻挡侵蚀性离子穿过涂层的能力[10],是表征涂层防护性能的重要参数。可以看出,全浸泡条件下的涂层电阻在250 h之内从1010 Ω·cm2急剧下降到106 Ω·cm2以下,下降了4个数量级,之后稳定在105~106 Ω·cm2之间波动。对于干湿交替而言,在前40个干湿交替循环期间 (480 h),Rc下降缓慢;之后,Rc急剧下降,说明在此期间,水的渗入正在加剧,涂层防护作用正在降低;120个循环之后,涂层电阻达到稳定,与浸泡条件下的电阻值一致,稳定在105~106 Ω·cm2之间波动。在实验前期及中期,干湿交替条件下Rc值要高于同一时期全浸泡条件下的,这是由于干湿交替条件下,涂层并非总是处于海水中,涂层吸水率较全浸阶段小;但进入后期,干湿交替条件下Rc值与全浸泡条件下一致,说明干湿交替环境中环氧防腐涂层前期的屏蔽较好,涂层后期失效快于全浸泡环境下的失效速率。这是由于干湿交替环境下,当在干燥阶段,涂层会经历失水的过程,表面干燥较快,涂层收缩;当再次进入浸润阶段时,涂层重新吸水,经历过不断的干湿循环后,涂层不断膨胀、收缩,缺陷增多,失效加快。
图11 全浸泡及干湿交替条件下涂层电阻随时间的变化曲线
2.5.3 孔隙率
利用拟合的电化学阻抗数据,可以计算得到干湿交替及全浸环境下涂层孔隙率的变化趋势,如图12。
图12 干湿交替及全浸环境下涂层孔隙率的变化曲线
涂层的孔隙率计算公式如下:
P=RptRp
(1)
其中,P为涂层的孔隙率,Rpt为理论电阻 (假设涂层孔隙率具有无限大),Rpt=dAK,d为被测试涂层的厚度 (d=1×10-4 m),A为涂层的测试面积 (A=4.5×10-4 m2),K为人工海水溶液在25 ℃下的电导率 (测试值为40.4 S×m-1),Rp为被测涂层阻抗数据拟合后得到的涂层孔隙电阻。涂层的吸水量对Rpt也有重要影响,与孔隙率既有联系、又有区别。
从干湿交替及全浸环境下涂层孔隙率的变化曲线 (图12) 可知,在涂层失效过程的初始阶段,即涂层渗水阶段,干湿交替条件下涂层的孔隙率远低于全浸泡条件下涂层的孔隙率,涂层孔隙率越低,吸水量越低,涂层的渗水能力越差,涂层的屏蔽性能越好,涂层阻抗值越高。之后,干湿交替条件下的涂层孔隙率上升,在1500 h时与浸泡条件下涂层孔隙率曲线相交,之后干湿交替条件下的涂层孔隙率高于全浸条件下的涂层孔隙率,说明浸泡1500 h后期干湿交替环境中的涂层防腐性能已低于全浸环境下的,这一趋势与低频阻抗模值所得结果一致。
2.5.4 涂层微观形貌及失效机理
全浸泡及干湿交替条件下涂层失效后的微观形貌如图13所示。可以看出,全浸泡2050 h后涂层鼓泡且鼓泡处开裂 (见图13a)。在全浸泡条件下,涂层不断渗水,到达涂层/基体界面。随着氧及腐蚀性离子如Cl-等的渗入,在界面发生Fe的腐蚀反应,腐蚀产物的堆积使得涂层剥离鼓泡。干湿交替失效后,涂层表面有明显的孔洞,同时涂层发生劣化,在涂层劣化周围可见许多明显的孔隙,说明干湿交替使涂层发生体积的吸水溶胀和失水收缩,导致涂层发生劣化,涂层孔隙率增大,涂层的失效就是从这些孔隙较多的地方开始发生,如图13b所示。
图13 浸泡2050 h及干湿交替210个循环后试样的微观形貌
为了探索干湿交替条件下涂层的失效形式及失效机理,对干湿交替后涂层的截面进行了观察。图14为浸泡2050 h及干湿交替210个循环后涂层的截面微观形貌图。可见,未浸泡的涂层截面凹凸不平,没有裂纹,涂层完好;浸泡2050 h后涂层内部出现了开裂,裂纹长度约为4 μm;干湿交替210个循环后涂层内部同样出现了开裂,裂纹数量明显多于全浸泡条件下的涂层,最大裂纹长度约为18 μm,开裂程度远大于全浸泡涂层的开裂程度,说明干湿交替较全浸泡对涂层的破坏能力高。
图14 未浸泡、全浸泡及干湿交替后涂层截面的微观形貌
在全浸泡条件下,有机涂层的失效是由于水溶液 (电解质溶液) 沿着涂层孔隙或者微缺陷不断渗入涂层内部,此过程为涂层吸水阶段。当溶液到达涂层/金属界面后,溶液中的氧、Cl-等腐蚀性离子随之扩散到界面,并在界面发生反应,此为界面反应发生阶段。后进入金属基体腐蚀发生与发展阶段,扩散到界面的O2被迅速消耗,不断产生的腐蚀产物沉淀,破坏了涂层与金属的结合力,使得涂层阻抗下降,孔隙率增大,甚至涂层鼓泡剥离。涂层干湿交替环境下,当在干燥阶段,涂层会经历失水的过程,表面干燥较快,涂层收缩;当再次进入浸润阶段时,涂层重新吸水;经历过不断的干湿循环后,涂层不断膨胀、收缩,缺陷增多变大,因此在实验后期,干湿交替环境下涂层的失效速度要高于全浸环境下的。
为了探索干湿循环过程中涂层吸水率的变化情况,测试了不同循环次数下单个干湿循环期间涂层的吸水率变化。图15为单个干湿交替循环期间,涂层吸水率的变化曲线。
图15 不同干湿交替循环次数下涂层吸水率的变化曲线
可知,随着干湿循环次数的增加,浸泡阶段涂层吸水速度加快且涂层的吸水率不断升高,干燥阶段涂层不断失水。对比浸泡阶段与干燥阶段,可知涂层的吸水与失水是两个不对称的过程,涂层的失水速度大于涂层的吸水速度。
Lendvay-Gy?rik等[6]曾提出干湿交替环境下涂层吸水及脱水过程具有不对称性特点,认为涂层表面吸水后会导致涂层内部先发生溶胀现象,这种现象的产生会暂时阻挡本体溶液中的水继续向涂层内部扩散;进入干燥阶段后,涂层表面直接失水,所以涂层的失水速度快于吸水速度。张亮等[19]在研究氟碳涂层在干湿交替环境下的失效实验中提出,由于干湿交替过程中涂层吸水与脱水过程的反复交替,使得涂层体积经历增大和缩小的交替过程,促进了微孔隙的增大并最终导致涂层与基体附着力降低。当涂层试样处在浸泡阶段,由于涂层孔隙变大,使得电解质溶液不断渗入膜层下,导致涂层产生不规则起泡。
本文结合环氧防腐涂层在干湿交替条件下的实验结果,提出了干湿交替条件下涂层的失效形式及失效机理的改进模型 (图16)。有机涂层在浸泡阶段表面不断吸水发生体积溶胀,水、C1-等腐蚀介质会通过涂层微孔或缺陷不断渗入涂层内部,直至到达涂层/金属界面。进入干燥阶段,涂层失水较快,体积发生收缩。经历多次干湿循环过程,涂层反复溶胀和收缩,使得涂层中的微孔增大、增多,涂层吸水速度增加,水、氧等具有腐蚀性的离子更容易进入涂层。到达涂层/金属界面后的水、氧等腐蚀离子与金属发生电化学反应,生成Fe的相关腐蚀产物[20,21],破坏了涂层与金属的结合力,导致涂层的鼓泡剥离[22]。
图16 环氧防腐涂层干湿交替失效机理模型
在不断的干湿交替过程中,涂层的交替膨胀和收缩过程使得涂层内部受到“交变载荷”的作用,最终涂层内部及表面开裂,彻底失去防护作用。如图13b中,涂层孔隙处出现了明显的裂纹,并且多条微小裂纹分布在整个孔隙区域。再如图14c中,涂层内部出现较长的开裂,说明干湿交替导致涂层的破坏。
3 结论
(1) 经干湿交替暴露实验,环氧防腐涂层内部分子链及官能团性质未发生显著变化,涂层失效原因不是由涂层内部分子链断裂所致。
(2) 在全浸泡及干湿交替的前期及中期,涂层附着力相差不大;而在后期,干湿交替条件下的涂层附着力均低于全浸泡条件下的。在全浸泡及干湿交替的前期及中期,干湿交替下的涂层阻抗值比全浸泡下的高;而在后期,干湿交替条件下的涂层阻抗值低于全浸泡下的,涂层表面鼓泡现象也更严重。说明相对于全浸泡环境而言,干湿交替环境暴露后期,涂层的失效速度更快。
(3) 环氧防腐涂层在干湿交替环境下的失效原因,是由于涂层经历吸水溶胀和失水收缩的交替过程,使得涂层内部受到“交变载荷”的作用,导致涂层内部孔隙增大、增多,涂层表面开裂,腐蚀介质更容易进入涂层/金属界面,最终导致涂层完全失效。
免责声明:本网站所转载的文字、图片与视频资料版权归原创作者所有,如果涉及侵权,请第一时间联系本网删除。
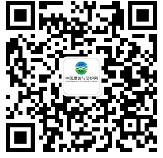
官方微信
《中国腐蚀与防护网电子期刊》征订启事
- 投稿联系:编辑部
- 电话:010-62316606-806
- 邮箱:fsfhzy666@163.com
- 中国腐蚀与防护网官方QQ群:140808414