钛合金是上世纪50年代发展起来的一种重要的结构材料,它具有高强度、低密度、耐热性高、耐蚀性好等优点,已经广泛应用于航空航天、医疗、海洋化工等领域[1]。其中,TC4钛合金由于具有较好的综合力学性能、低密度、良好的耐蚀性和低成本等特点[2],已经成为应用最广泛的钛合金之一。随着现代石油工业的快速发展,对钻井条件的要求更加苛刻,用于常规钻井的材料,例如碳钢[3,4]、不锈钢[5,6]、铝合金[7,8]等,已经无法满足现代钻井的需求[9],钛合金由于自身的一系列优点,是近年发展的一个新方向,其中以TC4钛合金为钻杆本体的材料也已经被RTI及Grant Prideco等公司所开发[10]。然而在超深井复杂环境中,其作业环境含有CO2、H2S、Cl-等介质,井底温度可达200 ℃以上,开发耐蚀性更好的石油工业用钛合金具有很高的需求和价值。其中,通过合金化提高钛合金耐腐蚀性是研究方向之一。金属元素Ru属于铂族金属的一种,微量的Ru (0.1%,质量分数) 添加至钛合金中可起到阴极改性的作用[11],加速阴极反应使钛合金耐蚀性提高,并且相比于另一常用的铂族金属Pd,它的成本更为低廉,仅为Pd的1/4。因此,美国RMI公司也开发出以TC4合金为基体,添加0.1%Ru的钛合金用于石油工业中,取得了很好的效果。至今,有关铂族金属Ru对TC4钛合金在石油工业中作用的研究和应用较多[11,12,13],但多数研究集中在对耐蚀性的评价上,有关Ru提高钛合金耐蚀性的直接实验证据还较缺乏,其作用机理有待深入研究。所以,本实验旨在对TC4和TC4-Ru的腐蚀行为进行对比研究,探讨Ru对TC4合金耐蚀性的影响,通过X射线光电子能谱仪 (XPS) 及深度刻蚀揭示Ru对腐蚀产物的影响及提高TC4合金耐腐蚀性方面的作用机理。
1 实验方法
1.1 实验材料
所用材料为Ti-6Al-4V-0.1Ru和Ti-6Al-4V合金,化学成分见表1。采用真空熔炼方法制备,合金所用原料为一级海绵钛、高纯铝 (99.999%,质量分数)、铝钒中间合金、TiO2和钌粉 (99.99%)。真空熔炼的步骤包括:配料→压制电极→熔炼→去头尾及扒皮,再进行均匀化→开坯锻造及轧制→去应力退火,得到3 mm厚的板材。
表1 TC4和TC4-Ru合金的化学成分 (mass fraction / %)
1.2 电化学实验
电化学实验在Multi Autolab M204电化学工作站上完成。将合金样品制备成10 mm×10 mm×3 mm的试样,每种成分取3个平行样。样品的一面连接导线并用环氧树脂封装,保留10 mm×10 mm的工作面,并用砂纸打磨至1200#后超声清洗,吹干。采用三电极体系,Pt电极为辅助电极,饱和甘汞电极为参比电极,工作电极为合金试样。实验溶液为10% (质量分数) HCl,温度37 ℃。将工作电极浸入实验溶液中,稳定后得到开路电位。极化曲线的扫描范围是相对于开路电位-500~2500 mV,扫描速率1 mV/s。
1.3 腐蚀失重实验和腐蚀形貌
腐蚀失重样品尺寸为20 mm×10 mm×3 mm,每种成分取3个平行样。用砂纸将样品表面打磨至1200#后超声清洗。实验溶液为15% (质量分数) HCl,温度37 °C,时长为10 d,每2 d取出试样进行称重记录,并更换新的溶液。腐蚀速率v根据ASTM G1计算得出,
v=(8.76×104×W)/(A×t×D)
(1)
其中,W为试样质量变化 (g),A为试样表面积 (cm2),t为腐蚀时间 (h),D为试样密度 (g/cm3)。为了评价两种合金的耐蚀性,在相同条件下腐蚀3 h后,采用扫描电镜 (SEM, Sirion-200) 对腐蚀形貌进行表征。
1.4 氧化膜表征
腐蚀失重后的样品在常温下干燥,使用ESCALAB 250Xi型XPS进行能谱检测,X射线源采用单色化Al Kα X射线源,并采用Ar+进行深度刻蚀,速率为0.38 nm/s。XPS分析时,采用样品表面污染碳的C 1s结合能 (284.68 eV) 进行电荷校正,数据处理和峰的解析使用Avantage 5.52软件。使用SEM自带的能谱仪 (EDS) 进行EDS分析。
2 结果与讨论
2.1 开路电位及动电位极化曲线
图1为TC4和TC4-Ru合金在10%HCl溶液中的开路电位。可知,约在3500 s后,两种试样在溶液中得到稳定的开路电位,并且TC4和TC4-Ru合金在整个过程中表现出相似的变化趋势,它们的开路电位稳定后分别是-0.597和-0.556 V。TC4-Ru合金的开路电位比TC4的更正,说明在该环境下TC4-Ru合金发生腐蚀的倾向更小,耐蚀性更好。此外,两种合金的开路电位大约在2000 s时都有一个大幅度下降的变化,该现象是由于钛合金在空气中形成的钝化膜在酸溶液中发生了部分溶解[14,15],导致基体暴露于溶液中使电位下降。对于TC4-Ru合金,表面钝化膜溶解的时间滞后于TC4合金,并且整体过程相对缓慢,可以说明TC4-Ru合金的钝化膜更稳定。
图1 TC4和TC4-Ru合金在10%HCl溶液中的开路电位
图2为TC4和TC4-Ru合金在10%HCl溶液中的动电位极化曲线,表2为相应的拟合结果。由图2可知,TC4和TC4-Ru合金在阳极区都存在一个活化-钝化的转换过程[16],并且它们的钝化电流密度以及钝化区的范围也基本相同。这是由于添加微量Ru在极化过程中不改变合金的阳极极化行为[11],所以两种合金的极化曲线在阳极区具有相似性。由表2可知,TC4和TC4-Ru合金的腐蚀电位分别为-0.585 和-0.529 V,TC4-Ru合金的更正;TC4和TC4-Ru合金的腐蚀电流密度分别为6.193×10-5和2.750×10-5 A/cm2,TC4-Ru合金的更小,大概是TC4的1/2,表明TC4-Ru合金具有更好的耐蚀性。上述电化学测试结果表明,添加微量Ru对TC4合金在盐酸溶液中起到了有效的阴极改性作用,促进了阴极反应的进行,使TC4-Ru合金的腐蚀电位升高,腐蚀电流密度降低,进而增强了合金的耐蚀性。
图2 TC4和TC4-Ru合金在10%HCl溶液中的极化曲线
表2 TC4和TC4-Ru合金在10%HCl溶液中的阳极极化参数
2.2 腐蚀速率及腐蚀形貌
图3为TC4和TC4-Ru合金在37 ℃下15%HCl溶液中每48 h的腐蚀速率。可以看出,在整个反应周期内,TC4-Ru合金的腐蚀速率始终低于TC4合金的;当腐蚀速率最终稳定时,分别为0.94和1.48 mm/a,说明在酸性条件下添加Ru对TC4合金的耐蚀性有很大的提高。在腐蚀过程中,两种合金的初始反应速率较快,第3个周期后有了较大幅度的下降,这是由于反应过程中腐蚀产物的堆积不断阻碍金属与酸溶液的反应,降低了腐蚀速率。
图3 TC4和TC4-Ru合金在37 ℃下15%HCl溶液中的腐蚀速率
图4为试样在37 ℃下15%HCl溶液中腐蚀3 h后的表面形貌。可以看出,两种合金都发生了一定程度的腐蚀。相比TC4-Ru合金,TC4合金的腐蚀坑数量更多且每一个腐蚀坑都较深;而TC4-Ru合金虽然发生了部分腐蚀,但大多数腐蚀坑较浅。表明在相同条件下,添加Ru延缓了表面的腐蚀过程,这种不均匀的腐蚀现象是由于TC4合金中α和β相的电位差导致,它们之间的电偶作用[17]使腐蚀反应的发生不能同时进行。Hack等[18]的研究表明,合金相中的成分是电偶作用的首要因素。钛合金中α相富集Al,β相富集V;β相中由于富集V,使其表面的钝化膜耐蚀性较好。所以,在腐蚀反应过程中,α相比β相优先被腐蚀[19],形成大小不一的腐蚀坑。
图4 TC4和TC4-Ru合金在37 ℃下15%HCl溶液中腐蚀3 h后的表面形貌
2.3 腐蚀产物分析和Ru的作用机理
图5和表3为TC4-Ru合金腐蚀10 d后的表面形貌及EDS分析。可以看出经过长时间的腐蚀,合金表面破坏较为严重,形成深浅不一的腐蚀坑。通过EDS分析,Ru在合金表面的含量约为2%,相比0.1%的添加量有了很大增长,表明腐蚀反应过程中Ru在表面发生富集,增加含量能够起到更有效的改性作用,提高合金的耐蚀性。
图5 TC4-Ru合金在HCl溶液中腐蚀10 d后的表面形貌
表3 图5中标注点的EDS分析结果 (mass fraction / %)
图6为合金腐蚀后钝化膜表面的XPS分析结果。图6a和b为两种合金的Ti 2p谱,可以看出对于TC4和TC4-Ru合金,腐蚀后表面钝化膜主要成分为TiO2,并有少量的Ti2O3,TiO以及一部分Ti。通过两种合金表面Ti 2p谱的对比可见,添加Ru没有对Ti的腐蚀产物造成影响。从它们的Al 2p和V 2p图谱可以看出,表面产物同样为Al2O3和V2O5,并伴随一部分金属Al和金属V。图6g为TC4-Ru合金表面的Ru 3d谱,说明Ru在反应后还是以金属元素的形式存在,起到阴极改性作用,不参与合金其他元素的反应过程,这与Schtuz[11]提出的作用机理相符。
图6 TC4和TC4-Ru合金在37 ℃下15%HCl溶液中腐蚀10 d后表面的XPS谱
为了研究Ru提高钛合金耐蚀性的作用方式,对合金钝化膜的主要组成元素Ti进行XPS深度刻蚀。图7为TC4和TC4-Ru合金腐蚀后并经不同时间刻蚀后钝化膜中Ti的XPS分析结果。可以看出,两种合金在刻蚀时间为0 s时也就是腐蚀表面,Ti 2p的曲线为双峰结构,表面Ti主要以TiO2的形式存在,这也是钛合金钝化膜的主要组成相[20];并且约在454 eV处有一个小峰,对应的是金属Ti。从图7a中可以看出,对TC4合金表面刻蚀时间为70 s时,TiO2大量减少,虽然它还是钝化膜的主要组成相,但含量相比表面处的已经明显减少;Ti3+和Ti2+的氧化物含量增多,这也表明钛合金钝化膜是分层存在的。当刻蚀时间增大到140 s时,Ti主要以金属的形式存在并且TiO2的峰已经消失,表明此时已刻蚀至合金的基体。时间继续增大到210 s时,Ti 2p的图谱基本保持不变,其主要成分同样为金属Ti,这说明在140~210 s之间的组分为合金的基体,并且钝化膜在140 s之前已经被击穿。从图7b可以看出,对TC4-Ru合金表面刻蚀时间为70 s时,虽然Ti3+和Ti2+的氧化物含量增多,但TiO2依然是主要组成相。刻蚀时间为140 s时,金属Ti的峰虽然明显增强,但TiO2依然为主。刻蚀时间为210 s的Ti 2p图谱与140 s时的保持一致,说明140~210 s之间钝化膜依然存在且主要组成为TiO2,并含有较多的金属Ti。通过XPS分析表明,TC4合金的钝化膜在刻蚀70 s后已经消失,而TC4-Ru合金的钝化膜在刻蚀210 s后依然存在。根据溅射的速度 (0.38 nm/s),可以估算TC4合金的钝化膜厚度约为39.9 nm,而TC4-Ru合金的钝化膜厚度大于79.8 nm,约为TC4的一倍以上,因此在腐蚀过程中起到更好的阻挡腐蚀性离子扩散作用。
图7 TC4和TC4-Ru合金在37 ℃下15%HCl溶液中腐蚀10 d后Ti 2p峰随刻蚀深度的变化
3 结论
(1) 添加Ru到TC4钛合金中,可起到阴极改性的作用,增大阴极反应速度,使TC4合金的开路电位和腐蚀电位升高,腐蚀电流密度降低,显著提高了TC4合金的抗腐蚀性能。
(2) 在盐酸溶液中,合金的腐蚀速率先下降后趋于稳定。通过相同条件下腐蚀速率比较,添加Ru显著降低了TC4合金的腐蚀速率,提高了耐蚀性。
(3) 腐蚀反应中,添加Ru不改变合金的腐蚀产物。在盐酸溶液中TC4合金的主要腐蚀产物为TiO2,Al2O3和V2O5,并在表面伴随有少量金属元素。添加Ru使钝化膜的主要成分TiO2在反应过程中在表面聚集并累积;相比于TC4合金,TC4-Ru合金表面钝化膜厚度增大一倍。Ru通过使钝化膜增厚的方式阻碍腐蚀反应的进行,提高TC4合金的耐蚀性。
免责声明:本网站所转载的文字、图片与视频资料版权归原创作者所有,如果涉及侵权,请第一时间联系本网删除。
-
标签: Ti-6Al-4V钛合金, Ru, 电化学, XPS, 耐蚀性机理
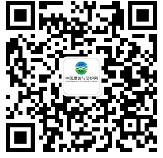
官方微信
《中国腐蚀与防护网电子期刊》征订启事
- 投稿联系:编辑部
- 电话:010-62316606-806
- 邮箱:fsfhzy666@163.com
- 中国腐蚀与防护网官方QQ群:140808414