45钢具有较高的强度和较好的切削加工性,在机械制造领域广泛应用[1]。电沉积制备复合材料,是利用电化学原理将纳米颗粒与金属离子在阴极工件表面实现共沉积,并制得性能优越的复合材料的工艺过程。研究发现,采用电沉积的方法在零件表面制备镀层能提高基体材料的耐腐蚀性能,延长其使用寿命。Ni-P合金具有高硬度、高耐磨性及高耐腐蚀性,使其成为广泛应用的镀层材料。张欣颖等[2]采用期望函数法对喷射电沉积Ni-P合金镀层的不同工艺参数进行了优化;王巍等[3]在糠醛装置的换热器管束内外壁上验证了Ni-P镀层具有较好的耐腐蚀效果。李法顺[4]通过研究Ni-P-BN(h) 化学复合镀层的制备工艺,发现其具有较好的力学性能和耐摩擦性能。曲彦平等[5]研究发现添加Al2O3粒子可以提高Ni-P复合镀层的耐磨性和显微硬度;郝亚丽等[6]研究了表面活化剂的种类和用量对Ni-P-Al2O3复合镀层的耐腐蚀性能的影响。侯勇[7]在汽车用镁合金上分别进行常规化学镀和超声波辅助化学镀,制备了两种Ni-P-Al2O3镀层,发现其耐腐蚀性均有提升且超声波辅助化学镀层具有更好的耐腐蚀性能。
喷射电沉积技术是电沉积技术的延伸,其可提高电沉积过程的沉积速度,细化沉积层组织[8],优化复合镀层的力学性能和耐腐蚀性能。喷射电压和喷射间隙是喷射电沉积加工过程中的重要参数。因此,本实验采用喷射电沉积在45钢基体表面制备Ni-P-BN(h)-Al2O3复合镀层,研究喷射电压和喷射间隙对复合镀层的耐腐蚀性能影响。
1 实验方法
喷射电沉积装置如图1所示。喷射电沉积的过程中,由计算机控制的三轴数控机床驱动安装在机床上的喷嘴,在水平方向上做往复运动,将工作电源正极与喷嘴上的镍棒相连,工作电源负极与待镀工件相连,接通电源,由水泵将镀液吸入喷嘴,并高速喷向待镀工件,多余镀液由回液管输送回镀液槽,实现镀液的循环利用。

图1 喷射电沉积装置
试件尺寸为7 mm×8 mm×30 mm的45钢,其表面经过打磨、电净除油、强活化和弱活化等预处理加工,用去离子水清洗后吹干待用。
利用喷射电沉积的方法制备Ni-P-BN(h)-Al2O3复合镀层,镀液的成分为:200 g/L NiSO4·6H2O (六水合硫酸镍)、30 g/L NiCl2·6H2O (六水合氯化镍)、20 g/L H3PO3 (亚磷酸)、30 g/L H3BO3 (硼酸)、60 g/L C6H8O7 (柠檬酸)、0.01 g/L CH4N2S (硫脲)、0.08 g/L C12H25SO4Na (十二烷基硫酸钠)、8 g/L 50 nm BN(h) 颗粒、1 g/L 30 nm Al2O3颗粒。镀液的温度为70 ℃,加工时工件与阳极喷嘴的相对运动速度为1.35 cm/s,加工的时间为20 min,实验的喷射间隙为1.6、1.8和2.0 mm,喷射电压为22,25和28 V。
采用Quanta FEI 250扫描电镜 (SEM) 对复合镀层腐蚀前的表面形貌进行观察。电化学测试采用三电极体系,试件为工作电极,工作面积为1 cm2,铂片为辅助电极,饱和甘汞电极 (SCE) 为参比电极,其余部分使用EVA热熔胶密封[9]。极化曲线测试和电化学阻抗实验均在室温下由CS350电化学工作站完成。测试中腐蚀介质为50 g/L的NaCl溶液,极化曲线扫描速率为1.5 mV/s,采用极化曲线外延法得到自腐蚀电位和自腐蚀电流密度等参数。在开路电位下采用电化学阻抗谱,其测试频率为105~10-2 Hz,扫描方向由高频到低频,并使用Zview软件对测得的阻抗谱拟合分析。
2 结果与讨论
2.1 复合镀层的表面形貌
图2a~c为不同喷射电压下Ni-P-BN(h)-Al2O3复合镀层的表面形貌。在喷射电压22~28 V的范围内,随着电压的增大,Ni-P-BN(h)-Al2O3复合镀层表面的平整程度先提升后降低,胞状结构尺寸一致性先增强后减弱。在电压为25 V时,复合镀层的表面最为平整,胞状结构尺寸一致性最好。这是因为,随着电压的增大,晶核的形成速率与长大的速率均增大,但是电压低于25 V时,晶核的长大速率低于形成晶核的速率[10],镀层表面胞状结构的尺寸一致性增强。而随着电压超过25 V时,由于晶粒的长大速度过快,致使复合镀层的表面胞状结构尺寸一致性降低。
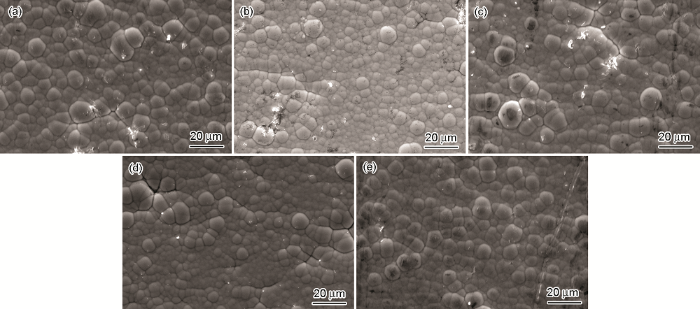
图2 不同喷射电压复合镀层的表面形貌和不同喷射间隙复合镀层的表面形貌
图2b、d和e为不同喷射间隙下Ni-P-BN(h)-Al2O3复合镀层的表面形貌。通过对比可知,在喷射间隙1.6~2.0 mm的范围内,随着间隙的增大,Ni-P-BN(h)-Al2O3复合镀层的胞状结构的尺寸稍有增大,但是表面平整程度提升。在间隙为2.0 mm时,复合镀层的表面最为平整。这是因为,当间隙较小时,复合镀层的表面由于胞状结构较小,在胞状结构的晶界连接处的表面积增大[11],晶界连接处的微小裂纹增多,镀层易受腐蚀。并且随着间隙的增大,镀液对待镀工件喷射的冲击力减弱,待镀离子在喷射电沉积的过程中更加稳定。
2.2 不同喷射电压下复合镀层的Tafel极化曲线
利用电化学工作站测复合镀层的极化曲线,并使用工作站自带的corrtest软件,采用Tafel极化曲线外延法可以得到极化曲线对应的自腐蚀电位、自腐蚀电流密度和腐蚀速率,拟合结果如表1所示。一般来说,自腐蚀电流密度反映复合镀层的腐蚀速度[12],其数值越小,自腐蚀电位发生正移,则复合镀层的耐腐蚀性能越好[13]。
表1 Ni-P-BN(h)-Al2O3镀层极化曲线分析结果

不同喷射电压下Ni-P-BN(h)-Al2O3镀层的极化曲线如图3所示,图中复合镀层的Tafel曲线均在阳极区发生了钝化现象。由图3和表1可知,在喷射电压22~28 V的范围内,当电压增大时,自腐蚀电流密度和腐蚀速率先减小后增大,并且在电压为25 V时达到最小值,分别为8.9251×10-6 A/cm2和0.1082 mm/a。这是因为,随着电压的增大,复合镀层表面的平整程度先提升后降低,并且25 V时的复合镀层表面最为平整,出现的细微孔隙较少,NaCl溶液中腐蚀性较强的Cl-难以渗入复合镀层表面,并且虽然复合镀层在25 V时的自腐蚀电位发生负移,但是此时复合镀层的钝化现象较为明显,表面产生了较好的钝化膜,使镀层的腐蚀减弱,自腐蚀电流密度和腐蚀速率下降,复合镀层的耐腐蚀性能最好。
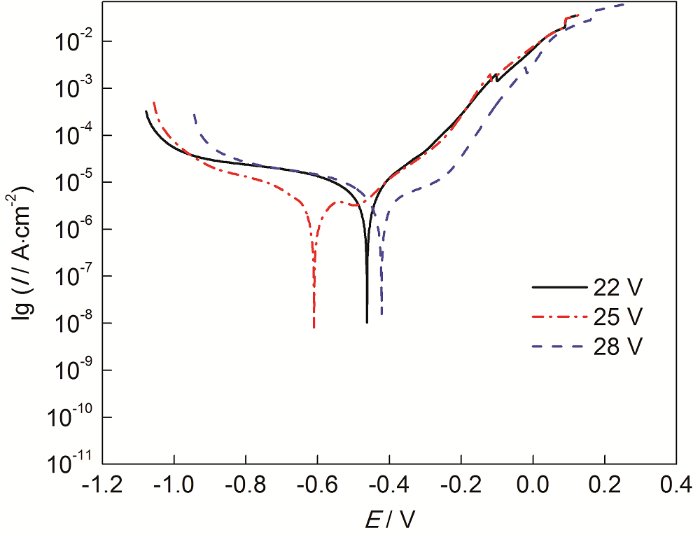
图3 喷射间隙为1.6 mm时不同喷射电压条件下复合镀层的Tafel曲线
不同喷射间隙下Ni-P-BN(h)-Al2O3镀层的极化曲线如图4所示。由图4和表1可知,在喷射间隙1.6~2.0 mm的范围内,随着间隙的增大,复合镀层的Tafel曲线整体下移,自腐蚀电位发生正移,自腐蚀电流密度和腐蚀速率逐渐减小,并在间隙为2.0 mm最小,分别为2.5664×10-6 A/cm2和0.0311 mm/a,此时复合镀层的耐腐蚀性能最好。这是因为,喷射间隙较小时,两极间电流密度较大,此时镀液的阴极极化作用增强,镀层表面金属离子缺乏,过多的电子与氢结合,产生疏松等表面缺陷,使腐蚀性较强的Cl-容易渗入复合镀层的表面。并且随着间隙的增大,加工区域的镀液喷射压力逐渐减小,冲击力对枝晶形成的影响减弱[14]。因此,随着间隙的增大,复合镀层的自腐蚀电流密度和腐蚀速率减小,耐腐蚀性能增强。
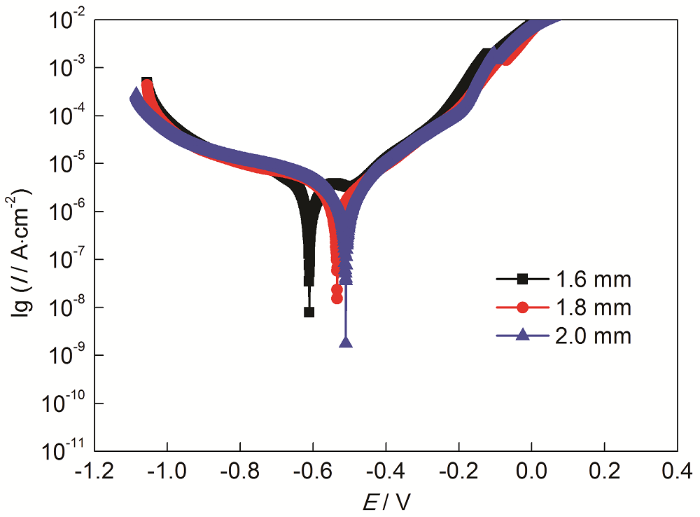
图4 喷射电压为25 V时不同喷射间隙条件下复合镀层的Tafel曲线
2.3 复合镀层的电化学阻抗谱分析
Ni-P-BN(h)-Al2O3复合镀层试样在50 g/L的NaCl溶液中,不同的喷射电压和喷射间隙测得的电化学阻抗谱分别如图5和6所示。由图可知,Ni-P-BN(h)-Al2O3复合镀层的Nyquist曲线均呈现出半圆形的形状,表现为单一的容抗弧。几种图谱相似是因为这几个镀层的基质均为Ni-P合金镀层,它们与腐蚀介质NaCl接触时发生的基本反应是一致的[15,16]。

图5 喷射间隙为1.6 mm时不同喷射电压的Nyquist曲线
从图5可以看出,在喷射电压22~28 V的范围内,随着电压的增大,容抗弧的半径先增大后减小,并在电压为25 V时,容抗弧的半径达到最大值,这说明随着电压的增大,复合镀层的耐腐蚀性能先提升后降低,在电压为25 V时耐腐蚀性能最好。从图6可以看出,在喷射间隙1.6~2.0 mm的范围内,随着间隙的增大,容抗弧的半径增大,并且在间隙为2.0 mm时,容抗弧的半径达到最大值,这说明随着间隙的增大,复合镀层的耐腐蚀性能提升,在间隙为2.0 mm时耐腐蚀性能最好。
图6 喷射电压为25 V时不同喷射间隙的Nyquist曲线
图7是复合镀层在不同工艺参数的相位角图,由图可知,Bode图均表现为一个时间常数,腐蚀介质只与复合镀层表面发生反应,电极过程主要受电荷转移作用。图8为经过Zview软件分析拟合得到的电化学阻抗谱的等效电路图,其所得参数如表2所示。其中,Rs为NaCl溶液电阻,Rp为电荷转移电阻,其大小由复合镀层的电导率和溶解过程中的极化电阻共同作用。CPE为常相位角元件,它与复合镀层的双电层电容有关,当CPE-P等于1时,可以等效为纯电容;CPE-P等于0时,等效为纯电阻[17],在这里,CPE是介于纯电阻和纯电容的元件。由表2可知,在喷射电压22~28 V的范围内,随着电压的增大,电荷转移电阻RP先增大后减小,并在25 V时达到最大值。在喷射间隙1.6~2.0 mm的范围内,随着间隙的增大,电荷转移电阻RP增大,在喷射间隙为2.0 mm时,电荷转移电阻最大。由于电荷转移电阻RP反映复合镀层的耐腐蚀性能,它的值越大,则复合镀层耐腐蚀性能越好[18],因此,在喷射电压为25 V时,复合镀层的耐腐蚀性能最好。在喷射间隙为2.0 mm时,复合镀层的耐腐蚀性能最好。电化学阻抗谱和等效电路图的分析结果与极化曲线的分析结果一致。

图7 Ni-P-BN(h)-Al2O3复合镀层在不同参数的相位角图

图8 电化学阻抗谱拟合用等效电路图
表2 电化学阻抗谱各元件等效电路拟合值

3 结论
(1) 通过扫描电镜检测了复合镀层的表面形貌,结果表明:喷射电压和喷射间隙的变化对复合镀层的表面形貌产生了影响。在喷射电压22~28 V的范围内,随着电压的增大,复合镀层的表面平整程度先提升后降低,胞状结构尺寸一致性先增强后减小。在电压为25 V时,复合镀层的表面最为平整,胞状结构尺寸一致性最好。在喷射间隙1.6~2.0 mm的范围内,随着间隙的增大,镀层的胞状结构的尺寸稍有增大,但是表面平整程度提升。在间隙为2.0 mm时,复合镀层的表面最为平整。
(2) 在喷射电压22~28 V的范围内,随着电压的增大,复合镀层均发生阳极强化,自腐蚀电流密度和腐蚀速率先减小后增大,复合镀层的耐腐蚀性能先提升后降低,在电压为25 V时,复合镀层的耐腐蚀性能最好。在喷射间隙1.6~2.0 mm的范围内,随着间隙的增大,复合镀层自腐蚀电位正移,自腐蚀电流密度和腐蚀速率减小,复合镀层的耐腐蚀性能逐渐提升,并在间隙为2.0 mm时复合镀层的耐腐蚀性能最好。
(3) 在喷射电压22~28 V的范围内,随着电压的增大,复合镀层的阻抗谱曲线半径大小和电荷转移电阻先增大后减小,复合镀层的耐腐蚀性能先提升后降低,并在电压为25 V时,曲线半径最大,电荷转移电阻最大,此时复合镀层的耐腐蚀性能最好。在喷射间隙1.6~2.0 mm的范围内,随着间隙的增大,复合镀层的阻抗谱曲线半径增大,电荷转移电阻增大,复合镀层的耐腐蚀性能逐渐提升,并在间隙为2.0 mm时最大,此时复合镀层的耐腐蚀性能最好。
免责声明:本网站所转载的文字、图片与视频资料版权归原创作者所有,如果涉及侵权,请第一时间联系本网删除。
-
标签: 喷射电沉积, Ni-P-BN(h)-Al2O3复合镀层, 耐腐蚀性
相关文章
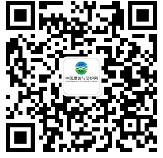
官方微信
《中国腐蚀与防护网电子期刊》征订启事
- 投稿联系:编辑部
- 电话:010-62316606-806
- 邮箱:fsfhzy666@163.com
- 中国腐蚀与防护网官方QQ群:140808414
点击排行
PPT新闻
“海洋金属”——钛合金在舰船的
点击数:7130
腐蚀与“海上丝绸之路”
点击数:5741