导读:摩擦滚动增材制造(FRAM)是一种新兴的固态增材制造技术,适用于使用基于融合的增材制造方法容易产生凝固缺陷的高强度铝合金。然而,FRAM中间层之间良好粘合的机制仍不清楚。本研究发现。首先,材料塑性流动和宏观迁移行为在夹层沿纵向和横向同时发生,形成宏观机械互锁的非平面界面。刀头上的凸螺纹增加了横向的材料流动,有利于相邻层的材料混合。其次,严重的塑性变形导致界面两侧的晶粒显著细化。?AA2319和AA6061侧边的平均晶粒度降低率分别为98.3%和95.9%。直接接触,没有明显的氧化物,冶金界面结合完全。这些发现有助于阐明FRAM的基本物理过程,并为工艺参数优化提供指导
高强铝合金具有密度低、比强度和比模量高、断裂韧性好、疲劳强度高、耐腐蚀性好等特点,适用于航空航天和国防工业。然而,传统的以熔合为基础的增材制造(AM)方法,涉及到材料-熔化-凝固,通过形成粗晶、裂纹和气孔,极大地恶化了这些合金的力学性能。因此,近年来发展了基于摩擦的固态增材制造方法,如搅拌摩擦增材制造(FSAM)、搅拌摩擦沉积增材制造(AFSD)和摩擦堆焊(FS)等,它们在高强度铝合金中具有显著的发展潜力和前景。这些方法起源于摩擦搅拌焊接(FSW),通过摩擦产生热量,并通过严重的塑性变形实现层间粘接。然而,FSAM-nor-FS方法都不能实现连续的材料添加,以及AFSD昂贵的要求和定制设备;使得后一种方法不适合使用。最近,作者团队[开发了一种新型的低成本固态方法,称为摩擦滚动增材制造(FRAM)。该方法通过快速旋转的工具头产生热量,同时实现连续加料。由于固态加工的固有特性,材料在FSAM过程中不熔化,避免了制造中的凝固缺陷,即所谓的“不可焊”高强度铝合金。
在大多数固态制造工艺中,相邻层之间的结合质量:取决于这些层的塑性变形和材料流动行为,以及界面处的冶金结合。在严重的塑性变形过程(如FSW)中,材料的流动行为是由刀具/工件界面处的热-机械相互作用造成的。在我们之前的研究中,我们对fram 生产的6061铝合金的显微组织和抗拉强度做了初步的评估。结果表明,成功地获得了无缺陷、晶粒细化的全致密组织。与搅拌搅拌区材料受到周围冷金属的限制不同,FRAM 中的流动环境要复杂得多,因为进料是不断地送到搅拌区。在FRAM 中如此复杂的热-力学条件下,材料在相邻层界面处的流动和界面结合行为可能与FSw有明显的不同,然而,由于每一层都是用相同的材料(6061铝合金)沉积的,相邻层之间的界面无法被区分,fram产生的部分的相邻层发生的基本物理机制,特别是为什么可以实现层间结合的原因仍然不清楚,这对于掌握固态FRAM方法的本质至关重要。
在本文中,北京工业大学Haibin Liu教授团队首次揭示了FRAM过程中的材料流动行为和层间键合机制。我们采用2319铝合金焊丝作为示踪材料,AA6061作为基底,因为混合铝合金可以很容易地区分彼此。利用三维x射线计算机断层扫描(CT)研究了夹层的三维形貌,从宏观上揭示了夹层材料混合和材料流动行为的基本原理。随后,利用电子背散射衍射(EBSD)和透射电镜(TEM)研究界面附近的微观结构,以阐明微观层面的层间键合行为。最后,通过力学性能测试进一步验证了杂化材料的结合质量,本文获得的研究结果将有助于了解FRAM 的基本物理过程,并为今后的工艺参数优化和刀头设计提供指导。本研究以“Revealing the bonding mechanisms between deposit and substrate of the friction rolling additive manufactured hybrid aluminum alloys”为题发表在Additive Manufacturing上
论文链接:
https://www.sciencedirect.com/science/article/abs/pii/S2214860422003384
1.在FRAM过程中,使用高速旋转的刀头对界面处的材料进行挤压剪切。材料塑性流动和宏观迁移行为同时发生,在aa -2319和AA-6061合金之间形成机械互锁非平面界面。
2.材料在界面处的流动和混合行为与刀头螺纹形状密切相关。 螺纹突出显著促进了塑性材料的横向流动,有利于层间材料的混合和不均匀界面的形成
3.在工具头的剪切作用下,塑化材料首先形成细长的晶粒,然后在其内部断裂形成等轴细晶粒。严重的塑性变形导致界面两侧晶粒显著细化。AA -2319和AA -6061侧边的平均粒度降低率分别为-=98.3%和95.9%。
图1所示。(a) FRAM过程示意图;(b) fram生产的铝筒;(c)沉积标本;(d) CT和EBSD观察职位;(e)刀头结构。
图2(a)衬底和(b)SEM图像
图3所示。(a)AA 2319丝沉积在AA 6061基板上的CT结果;(b)沉积材料放大的3D形貌。
图4所示。样本截面(Y-Z平面):(a)所选位置;(b)-(e)四个与所选位置对应的截面图。
图5所示。样品纵剖面(X-Z平面):(a)所选位置;(b)-(e)与所选位置对应的四种典型纵剖面视图。
图6所示。(a)沉积试样不同宽度的AA 2319面积百分比曲线;(b-e )和所选位置对应的纵剖面图像
图7所示。(a沉积试样不同高度的AA 2319面积百分比曲线;(b-f)和所选位置对应的横截面图像。
图8所示。:(a)AA 2319进给线反极图(IPFs);(b) AA 6061基板;(c) 沉积后在界面附近沉积的AA 2319材料;(d)沉积后界面附近的AA 6061材料;(e)沉积后AA2319的粒度分布直方图;和(f) 沉积后A6061的粒度分布直方图。
图9所示。(a沉积试样在截面上的界面微观结构(即;,沿Y-Z平面):(b-c)两个典型位置界面的光学显微图(蚀刻后),如图9(a)所示;(d-e)与图9(b-c)对应的IPF图像
图10所示。沉积试样在纵向(沿X-Z平面)方向的界面微观结构(a)三个典型位置界面的光学显微图(蚀刻后); (b-d)各自的IPF图像;(eg)
图11所示。取向差分布(a)AA6061衬底,(b)FRAM 工艺后的 AA6061(c)界面处的AA606
图12界面处的SEM图像(a)和各元素的元素分布(b-f)。
图13FIB实验位置(a);FIB制备的TEM标本(b);界面TEM图像(c-d);EDS线扫过界面(e);和EDS区域扫描周围的接口(f)。
图14 (a)单轴拉伸试验的工程应力-应变曲线,(b-c)形貌的断口形貌,(d)断口表面的Cu分布。
图15所示。FRAM 的层间粘接机制:(a)相邻层在宏观层面形成的机械互锁非平面界面:(b)界面处的动态再结晶,在微观层面形成完整的冶金结合。
实验证明,不含氧化物的直接接触界面是可行的获得AA-6061和aa -2319之间的合金,形成坚固的冶金结合。
免责声明:本网站所转载的文字、图片与视频资料版权归原创作者所有,如果涉及侵权,请第一时间联系本网删除。
相关文章
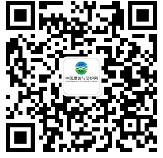
官方微信
《腐蚀与防护网电子期刊》征订启事
- 投稿联系:编辑部
- 电话:010-62316606-806
- 邮箱:fsfhzy666@163.com
- 腐蚀与防护网官方QQ群:140808414
点击排行
PPT新闻
“海洋金属”——钛合金在舰船的
点击数:8148
腐蚀与“海上丝绸之路”
点击数:6486