先进航空发动机朝着高推质比、高可靠性、长寿命和经济可承受性的方向发展,苛刻且相互矛盾的指标要求航空发动机关重件构型复杂、轻质高效。传统的“减材”制造技术面临生产周期长、成品率低、制造成本高等挑战,成为制约先进航空发动机研发的瓶颈。变革性的“近净成形”增材制造技术,因具有一体化成形、无需模具、制造成本低等优点,最早被美国联合技术研究中心(UTRC)尝试用于涡轮叶盘一体化制造,随后通用电气(GE)、罗尔斯-罗伊斯(RR)等航空发动机企业也开始应用增材制造技术加工或修复零部件。例如,GE公司在GE9X、Leap 系列航空发动机中已成功应用增材制造技术成形了燃油喷嘴、传感器外壳、热交换器、涡轮叶片等10 余种结构。Safran、MTU等发动机公司增材制造了燃油喷嘴、燃烧室机匣等结构,提升了生产效率。中国航发湖南动力机械研究所采用增材制造技术加工了微型涡喷发动机,将近百个零件集成制造为10个,包括增材制造成形的压气机/涡轮的整体叶盘结构,并成功通过某型涡喷发动机试车。
图1 拓扑优化后增材制造航空发动机泄压门铰链
增材制造技术给航空发动机复杂结构的加工提供了新的途径,但在能量源“逐点扫描熔化-逐线扫描搭接-逐层凝固堆积”的过程中,粉末/丝材局部熔化形成熔池,熔池内残留未完全恢复的“匙孔”,导致增材制造结构内部存在广布缺陷;且受限于加工可达性,复杂结构(如涡轮叶片)内部空腔等关键部位残留粉末等表面缺陷。另外,增材制造结构不同部位处的晶体形貌、内部/表面缺陷等具有显著差异,导致结构强度、疲劳寿命与结构特征密切相关且表现出大的分散性。为此,美国联邦航空管理局(FAA) 、欧洲航空安全局(EASA)分别于2018 年、2021 年发布的《粉末床熔融增材制造成形涡轮发动机零件及修复指南》建议稿、《增材制造认证备忘录》等适航认证文件中指出,需发展适用于航空发动机增材制造结构的强度及寿命评价方法。
图2 基于点阵结构的空心风扇叶片设计
目前航空发动机增材制造结构在无损检测技术与初始缺陷表征、强度预测方法、寿命评估方法及创新结构一体化设计方面的研究进展,得到主要结论如下:
1)涡流、超声等技术可以检测增材制造简单结构近表面及内部缺陷,借助这些方法,实现增材制造结构初始缺陷形貌的量化表征,进而建立缺陷空间取向与增材制造方向的关联规律。
2)基于CT 检测的原位试验方法,揭示了单轴拉伸、循环拉伸等典型载荷下缺陷演化机理,发展了用于预测拉伸极限、延伸率等性能的塑性损伤模型,实现了增材制造发动机离心叶轮破裂转速的准确预测。
3) 发展了以初始缺陷等效参量为输入的增材制造材料级寿命模型,实现了增材制造标准试样、缺口试样的高循环疲劳、低循环疲劳寿命预测。
4)考虑增材制造工艺约束、强度、多物理场服役环境等因素,发展了航空发动机增材制造结构一体化设计方法,并开展了齿轮箱壳体、离心叶轮、整体叶盘等创新构型的设计与试验验证。
为了进一步推动航空发动机增材制造结构的实际应用,仍需开展以下几个方面的研究:
1) 在试验数据方面,国内外学者针对增材制造材料的拉伸、高循环及低循环疲劳等开展了试验研究,但仍处于零散、样本量少的状态。需针对航空发动机选用的材料开展系统且深入的试验研究,扩大数据样本,表征材料力学特性及分散性。同时,涡轮叶盘等热端结构长期工作在复杂、严苛的载荷环境中,现有研究仍无法满足增材制造热端结构设计的需求,仍需针对复杂失效模式开展蠕变、蠕变-疲劳等试验研究。
2) 航空发动机空心气冷涡轮叶片、双辐板涡轮盘等结构具有复杂内腔与几何不连续特征。采用增材制造工艺成形后,结构局部呈现大应力梯度-缺陷-表面粗糙度多因素耦合特征。如何实现复杂结构的缺陷-表面粗糙度表征,阐明多因素耦合下的失效机理,并建立相应的强度、寿命评估方法仍是当前应用的难点。
免责声明:本网站所转载的文字、图片与视频资料版权归原创作者所有,如果涉及侵权,请第一时间联系本网删除。
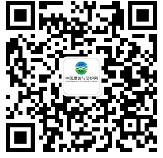
官方微信
《腐蚀与防护网电子期刊》征订启事
- 投稿联系:编辑部
- 电话:010-62316606
- 邮箱:fsfhzy666@163.com
- 腐蚀与防护网官方QQ群:140808414