开发深海资源,维护主权权益,提高我国海洋技术支撑和保障能力,必须要发展重大技术装备。而海洋工程材料则将在其中发挥关键性作用。本文将从研究进展,发展方向、应用分析等多角度深度为大家解读海洋防腐材料。
1 发展背景
海洋约占地球表面积的 70%,世界贸易中,90% 以上的货运靠海洋运输,海洋资源与航海船舶业已经成为世界经济发展中不可或缺的重要支柱。然而,随着海面风浪等对金属构件产生的往复冲击;海水、海洋生物及其代谢产物等对金属材料的腐蚀,海洋环境已成为极为苛刻的腐蚀环境。无论海水里还是海面上的潜艇、船舶等,都需要采用高强、耐腐蚀材料制造,并涂刷防腐涂层进行保护。因此,寻找最合适的海洋防腐材料已引起人们的广泛关注[1] 。
目前,我国正处于集约低碳经济转型期的关键阶段,也是走向海洋战略实施的关键时期,远洋运输、深海新能源开发、沿海港口、船舶等行业的迅速发展,对海洋防腐材料有了更高的要求,研发绿色无害化、长寿命、经济化的海洋防腐材料是客观必要的。
此外,海洋石油工业的发展促进了海洋防腐材料在海洋平台上的应用。近海海岸工程,如码头、海上桥梁等,同样需要高性能防腐涂料进行防护。海底管线也需要重防腐涂料进行防护。海洋重防腐涂料针对海洋的苛刻腐蚀环境设计。使用于海洋平台、海工混凝土工程、海底输油管道等,海洋的特殊环境要求海洋防腐涂料具有高的耐腐蚀性、耐划伤性和耐侯性。
海洋环境涉及气象、流体、物理、化学以及生物等多领域复杂因素。传统金属材料逐渐不能满足先进海洋设备和机械的使用条件。高速船体材料、高耐腐蚀海洋建筑材料以及深海探测材料都面临更新换代的局面。改进传统海洋材料,针对海洋环境设计高性能、耐腐蚀、环保、绿色的新材料以及对新材料的可应用性进行深度的探索己经迫在眉睫。
2 海洋腐蚀现状
腐蚀是导致各种基础设施和工业设备破坏和报废的主要原因。我国每年由于腐蚀造成的损失约为 GDP 的 5%,远高于美国的 3.4%和日本的不足 3%。国际公认,腐蚀损失超过所有自然灾害损失的总和。在海洋环境中服役的基础设施和重要工业设施的腐蚀问题严重,特别是船舶与海洋平台的腐蚀问题更加突出,腐蚀已经成为影响船舶、近海工程、远洋设施服役安全、寿命、可靠性的最重要因素,引起世界各国政府海洋工业界的高度重视。因此,大力发展海洋工程防腐材料和技术,对于保障海洋工程和船舶的服役安全与可靠性,降低重大灾害性事故的发生,延长海洋构筑物的使用寿命具有重大意义。
海水作为腐蚀性电解质的最显著特点,是它含有很多自由离子,即含盐量很高。另外,海水中含有复杂的无机物和有机物。除了氯化物以外,海水还含有经常处于饱和状态的碳酸盐以及多量的镁、钙离子,它们可以在金属表面生成保护性的覆盖层。此外,海水中有些微量组分也会影响腐蚀,其中有些有机、无机分子能和金属形成络合物,这些络合物直接影响着金属的溶解和腐蚀产物的生成和沉积。不仅如此,由于海水中有多种动物、植物和微生物生长,各种生物特别是栖居在金属表面的附着生物对腐蚀有很大的影响。我国沿海常见的附着生物有:藤壶、牡蛎、苔藓虫、石灰虫、水螅、红螺等。与腐蚀有关的微生物是细菌类,主要是硫酸盐还原菌[1] 。
海水腐蚀的特点
(1)海水中的氯离子等卤素离子能阻碍和破坏金属的钝化,海水腐蚀的阳极过程较易进行。
(2)海水腐蚀的阴极去极化剂是氧,阴极过程是腐蚀反应的控制性环节。一切有利于供氧的条件,如海浪、飞溅、增加流速,都会促进氧的阴极去极化反应,加速金属的腐蚀。
(3)海水腐蚀的电阻性阻滞很小,异种金属的接触能造成显著的腐蚀效应。
影响腐蚀的海水环境因素
(1)温度的影响
从动力学方面考虑,海水温度升高,会加速阴极和阳极过程的反应速度。但海水温度变化会使其他环境因素随之变化。海水温度升高,氧的扩散速度加快,这将促进腐蚀过程进行。另一方面,海水温度升高,海水中氧的溶解度降低,同时促进保护性钙质水垢生成,这又会减缓金属在海水中的腐蚀。
(2)溶解氧的影响
溶解氧对铁腐蚀的影响较多。氧是在金属电化学腐蚀过程中阴极反应的去极化剂。对碳钢、低合金钢等在海水中不发生钝化的金属,海水中含氧量增加,会加速阴极去极化过程,使金属腐蚀速度增加;对那些依靠表面钝化膜提高耐蚀性的金属,如铝和不锈钢等,含氧量增加有利于钝化膜的形成和修补,使钝化膜的稳定性提高,点蚀和缝隙腐蚀的倾向性减小。
(3)盐度的影响
水中含盐量直接影响到水的电导率和含氧量,因此必然对腐蚀产生影响。随着水中含盐量增加,水的电导率增加而含氧量降低,所以在某一含盐量时将存在一个腐蚀速度的最大值。海水的含盐量刚好为腐蚀速度最大时所对应的含盐量。
(4)pH 的影响
一般说来,海水的 pH 值升高,有利于抑制海水对钢的腐蚀。在施加阴极保护时,阴极表面处海水 pH 值升高,很容易形成碳酸钙水垢这种沉积层,这对阴极保护是有利的。
(5)氧化还原电位的影响
氧化还原电位可以反映海水的氧化还原性能。在海水介质中,由于各种氧化还原体的浓度都很小,不可能某一对起决定作用。
(6)其它影响
海水的流速以及波浪都会对腐蚀产生影响。从静止到有一定的流速,开始时,随流速加,氧扩散加速,阴极过程受氧的扩散控制,腐蚀速度增大。当海水中含有悬浮的固体颗粒时,高的海水流速还会造成腐蚀磨损;在水轮机叶片、螺旋桨旋推进器等装置中,由于水轮机叶片、螺旋桨旋推进器的高速运动,会形成流体空泡,这些空泡崩破,产生高压冲击波,造成空泡腐蚀。海生物对腐蚀也有重要的影响。海洋环境中存在着多种动物、植物和微生物,与海水腐蚀关系较大的是附着生物。
海洋腐蚀的区域分类
要想提高传统材料的耐腐蚀性能、开发新型环境友好防腐、防污涂层以及设计针对海洋环境使用的海洋用新型材料,归根结底是要先了解材料在海洋中的腐蚀形式、腐蚀机理,只有在根本上切断材料腐蚀的途径,才能真正达到防腐耐用的目的。综合海洋各类极端环境主要包括:海洋大气区,浪花飞溅区,潮差区,全浸区和海泥区五个区域[3-5]。
(1) 海洋大气区
海洋大气环境与内陆有着明显的不同,在海洋大气区影响腐蚀的重要因素是存在金属表面上的含盐粒子量。同时海洋大气的湿度大,它们积存在钢铁表面形成导电良好的电介质,他们是电化学腐蚀的有利条件,使得海洋平台钢结构的腐蚀速度加快。
(2)海洋浪花飞溅层
最初提出的海洋飞溅带这一概念是泛指在海水平均高潮位 (M.H.W.L) 以上部分,腐蚀最严重的部位 ( 峰值 ) 取决于海洋气象条件,并没有明确的范围。金属在飞溅带受到的严重腐蚀有其特殊性、诸如没有海生物附着、供氧充分、浪花的冲击和润湿以及日光照射形成干湿交替的环境等外在因素。海盐粒子在飞溅带上积聚的量要比海洋大气中高 3-5 倍,甚至十几倍,而且在峰值附近含盐粒子量更高。飞溅带的金属表面被海雾、水滴润湿的电量值远大于大气带,而且有较高的干湿交替频率。因此,在飞溅带海水膜润湿时间长、干湿交替频率高、海盐粒子的大量积聚以及飞溅的海水粒子之冲击乃是造成激烈腐蚀的主要外因。
在飞溅带上含盐粒子量在各个月份均远大于大气带,且飞溅带峰值附近的含盐粒子量也远大于飞溅带其它位置。通过比较处在飞溅带金属表面和处在大气带钢样表面的水膜湿润时间及干湿交替频率,可以发现飞溅带处材料表面的润湿时间更长,电流也更大。
(3)海浪潮差区
在海浪冲击层中应用的材料使用环境十分恶劣,海洋工程结构除经受海水腐蚀外还要承受海浪、风暴等力学因素的作用。因此在这一腐蚀环境下材料和构件的腐蚀疲劳是影响其结构安全的重要因素之一。金属材料在海浪冲击层受到环境腐蚀和循环载荷的同时作用所引起的损伤,往往比他们单独作用所引起的损伤相加要严重得多,例如在海水环境中进行疲劳实验的碳钢试件的寿命,比先浸泡在海水中一定时间再进行疲劳试验的试样寿命短得多。可见腐蚀加速了疲劳损伤,疲劳损伤又进一步促进了腐蚀进程。
(4)海水全浸层
在岸边的浅海海水通常为氧所饱和。污染、沉积物、海生物污损和海水流速等都可能起重要的作用。在这一个区域中,其腐蚀速率可能比海洋大气中更为迅速,尤其是保护涂层在此区腐蚀最为严重。高浓度氯离子的存在是各种金属在海洋环境中遭受着严重腐蚀的主要原因。由于氯离子较多,使得 Fe 等各种金属难以钝化,即使像不锈钢这种高合金成分的材料也会由于钝化膜的稳定性变差,极易发生点蚀。另外波浪的作用使得水深 200 m 之内海水中的含氧量达到饱和,海水中高的氧含量和中性pH 值,使得金属在海水中的腐蚀主要由氧还原所产生的阴极反应所控制。
金属材料在海水全浸层中多发生均匀腐蚀,这与在金属表面上所产生的任意形态的全面腐蚀不同,均匀腐蚀一般属于微观电池腐蚀。其腐蚀形式按其腐蚀速度受控制的情况分为受阴极反应控制和受紧密附着的钝化膜控制两大类。因此在这一区域中,金属的腐蚀行为与金属所处的腐蚀状态环境条件变化及其自身钝化性有关。
深海及海泥区
海底沉积物的物理性质、化学性质和生物性质随海域和海水深度不同而异,因此海底泥土区环境状况很复杂。在这一区域中,氧含量变小,甚至出现无氧区,为硫酸盐还原菌等厌氧菌的存活和大量繁殖提供十分有利的条件。因此腐蚀的主要形式是微生物附着腐蚀引起的材料表面点蚀和海底沉积物引起的间隙腐蚀。
3 我国海洋防腐材料的发展现状
海洋工程构筑物大致分为 :海岸工程(钢结构、钢筋混凝土)、近海工程(海洋平台、钻井、采油、储运 )、深海工程 ( 海洋平台、钻井、采油、储运 )、海水淡化、舰船 ( 船体、压载舱、水线以上 ),简称为船舶与海洋工程结构。船舶与海洋工程结构的主要失效形式包括 : 均匀腐蚀、点蚀、应力腐蚀、腐蚀疲劳、腐蚀 / 磨损、海生物 ( 宏生物 )污损、微生物腐蚀、H 2 S与CO 2 腐蚀等等。
控制船舶和海洋工程结构失效的主要措施包括 : 涂料 ( 涂层 )、耐腐蚀材料、表面处理与改性、电化学保护 ( 牺牲阳极、外加电流阴极保护 )、缓蚀剂、结构健康监测与检测、安全评价与可靠性分析及寿命评估。
从腐蚀控制的主要类型表来看,涂料 ( 涂层 ) 是最主要的控制方法、耐腐蚀材料次之,表面处理与改性是常用的腐蚀控制方法,电化学保护 ( 牺牲阳极与外加电流 ) 是海洋结构腐蚀控制的常用手段,缓蚀剂在介质相对固定的内部结构上经常使用,结构健康监测与检测技术是判定腐蚀防护效果、掌握腐蚀动态以及提供进一步腐蚀控制措施决策和安全评价的重要依据,腐蚀安全评价与寿命评估是保障海洋工程结构安全可靠和最初设计时的重要环节。
海洋工程中使用的材料体系众多,包括钢铁材料、钢筋混凝土结构、有色金属材料 ( 铝合金、钛合金、铜合金、镁合金等)、复合材料等。从使用量上看,钢铁、钢筋混凝土用量最大。就腐蚀防护技术而言,前述的多种防护技术在不同材料上都可应用,然而,不同材料防护技术相互之间存在差异。复合材料的轻量化特点,在海洋工程中的使用有望进一步加大,其防护技术还有待深入探讨。
目前,我国没有海洋钢筋混凝土平台,海工用钢筋混凝土主要用于海岸工程、海外大桥。海工钢筋混凝土的长效防护是国际上非常重要的课题。如何保障我国众多的跨海大桥长期寿命至关重要。高性能、长寿命的海工钢筋混凝土对我国南海及岛礁工程的建设具有重要价值。钢筋混凝土破坏的主要原因是海洋中的氯离子渗透、接触到钢筋,导致钢筋发生腐蚀。为了有效控制氯离子的渗透,除了提高混凝土本身抵抗氯离子渗透的性能外,在混凝土表面施加防护涂料是常用办法,国外已经广泛使用,我国近年来已开始重视。
我国在防腐材料方面的研究发展现状:
1) 我国海洋涂料市场几乎完全被国外垄断,特别是远洋船只涂料、海洋平台涂料、防污涂料等完全采用国外涂料。就技术水平而言,国内的部分涂料技术已达到可应用的水平,但缺少实际工程应用机会,这不仅影响国内相关关键技术的发展,同时也影响我国建造的海洋平台在国外的应用。此外,传统防腐涂料含有重金属和一些难降解的有机物,其无论在生产或使用过程中,均会危害环境。
(2) 在船舶与海洋平台的电化学保护方法中,我国常规牺牲阳极占世界份额的绝对优势,但高档稳定化牺牲阳极仍然进口,而且我国目前没有生产大电流阴极保护系统这类装备的能力。
(3) 我国严重缺乏海洋工程与船舶的材料表面改性等特殊防护技术,特别是关键重要部件的防护技术,从设备、材料到技术,主要依赖进口,受到国外工业发达国家的制约。目前,我国部分国产化技术缺乏系统的基础研究和高端开发,只限于较低端的应用,特别是表面处理装备几乎大多是从国外进口。我国应该推动在陆地和航空行业中取得成功的表面处理技术在海洋工程中的应用。
鉴于此,需要我们的海洋材料研究人员结合国家最新政策,加大研究和实用力度,争取打好海洋工程开发的“战役”。
3.1防腐涂料(涂层)
涂料是船舶和海洋结构腐蚀控制的首要手段。海洋涂料分为海洋防腐涂料和海洋防污涂料两大类。按防腐对象材质和腐蚀机理的不同,海洋防腐涂料又可分为海洋钢结构防腐涂料和非钢结构防腐涂料。海洋钢结构防腐涂料主要包括船舶涂料、集装箱涂料、海上桥梁涂料和码头钢铁设施、输油管线、海上平台等大型设施的防腐涂料 ; 非钢结构海洋防腐涂料则主要包括海洋混凝土构造物防腐涂料和其他防腐涂料[7] 。
防腐涂料的类型主要包括有机硅树脂涂料、环氧类涂料、聚氨酯类防腐涂料等,环氧类防腐涂料是目前应用范围最广的海洋工程结构防腐涂料。实际应用中,涂料可以分为面漆、中间漆、底漆。面漆包括乙烯树脂、丙烯酸树脂、聚氨酯等;中间漆包括环氧玻璃鳞片、环氧云铁等;底漆包括热喷涂铝漆、富锌底漆(无机类的硅酸依稀、有机类的环氧富锌)等。
(1)有机硅树脂涂料
有机硅树脂涂料是以有机硅树脂或者改性有机硅树脂为主要成膜物质的一种元素有机涂料,主要分为纯有机硅树脂涂料和改性有机硅树脂涂料,耐热耐寒性强,绝缘性、附着力、柔韧性、防霉性等性能优异。改性有机硅树脂应用更广泛,包括机械混合型和缩聚型,可以通过添加不同填料或颜料来改性有机硅树脂,增强其耐热性、绝缘性和耐候性等。
虽然有机硅树脂涂料具有优异的耐高低温性和耐候性、耐化学品、耐磨性等突出优点,但是它的强度低,与基底的粘附力低等缺点也限制了其应用范围。以后的工作主要是采取不同方法改性,如无机 - 有机混接技术,使其兼具有机物与无机物的最佳特性;通过探明有机硅树脂涂料成膜机理,对各种聚合物如丙烯酸树脂、环氧树脂等进行改性,获得性能更为优异的有机硅改性涂料;制备交联型有机硅树脂涂料从而增强其致密性,提高耐水、耐溶剂和耐热等性能;使有机硅树脂涂料向低污染、健康环保的方向发展也是以后的研发重点。
(2)环氧类防腐涂料
环氧类防腐涂料以环氧树脂为主体,与颜料、催干剂、助剂等调制而成。环氧树脂涂料性能优异:高附着力、高强度、耐化学品和耐磨性是目前海洋重防腐领域应用最早、范围最广的重防腐涂料种类之一。
环氧类防腐涂料种类繁多,主要分为双酚 A 环氧树脂和酚醛环氧树脂两大类。双酚 A 环氧树脂(如图)分子结构中含羟基、醚键和环氧基团,与基底粘附力强;苯环使树脂具有较强的机械强度和耐磨性;涂膜后耐酸碱性、耐腐蚀性和耐化学品性能优异;常温固化、施工方便,固化收缩率低,无挥发性物质产生,绿色环保。
环氧双酚A的结构式
酚醛环氧树脂,因含较多的环氧基团,耐腐蚀性能和粘附力更强;固化交联度更大,致密性更强,同时具有酚醛树脂的耐高温和耐腐蚀性能。但环氧基团的增多使脆性增大,影响了其应用范围。以双酚 A 代替苯酚合成双酚 A 酚醛环氧树脂(如图),游离酚含量低,分子量分布窄,双酚 A 的引入使树脂力学性能更强,收缩率更低,环氧基团的增多使粘附力极强,柔韧性、热稳定性、绝缘性、耐水耐腐蚀性等性能更优异。
双酚A酚醛环氧树脂
通过填料等手段改性环氧树脂,可以拓展其应用范围。Ghaffari 等以双官能团硅烷作改性剂,通过红外光谱和热重分析等分析方法,对环氧复合材料中悬浮纳米填料和涂层性能进行研究,研究表明改性剂使悬浮纳米填料的分散效果更好,加入质量分数 0.5% 的改性悬浮纳米填料后,涂层在浸泡期内效果明显。Paula 等对水性环氧树脂的微观结构展开分析,结果表明涂层表面的平均针孔大小与氯化物的渗透性有很好的相关性。刘江涛等分析了水性改性胺环氧固化剂与液体环氧树脂配比,填料、助剂的选择等问题,结果表明环氧基团胺氢当量比为 1 ∶ 1,颜料、非离子与阳离子润湿剂配合使用时,制成的漆膜力学性能和耐化学性能优异。Mukesh 等以腰果酚代替双酚 A 合成新型环氧树脂并进行红外光谱和核磁共振谱的表征,结果表明:新型环氧树脂腰果酚只需原来环氧树脂中双酚 A 使用量的 40% ~ 60% 就能达到相同的性能。
但目前这些改性方法只能改善树脂某一特性,在面对复杂的海洋腐蚀环境时,应用优势并不明显。根据不同的使用领域,通过与各种树脂和填料等混合,再结合物理和化学改性的方法研制水性化或高固体化环氧类防腐涂料是其发展方向,比如我们以双酚 AF 代替双酚 A合成酚醛树脂,再对其进行环氧化,得到的含氟环氧树脂,不但对基底具有优异的吸附性能,而且极大的提高了环氧树脂的防腐性能,在海洋防腐领域优势突出。涂料性能的优劣依赖于树脂的特性,还包括改性剂的研发,涂装工艺的优化等也是以后环氧类防腐涂料的科研方向。
(3)聚氨酯防腐涂料
聚氨酯涂料是常见的一类涂料,和环氧涂料有相似的性能,分为双组份和单组份聚氨酯涂料。聚氨酯中除存在氨基甲酸酯键外,还有许多—OH、—NCO和不饱和双键等,涂层耐酸碱、耐油、耐腐蚀、耐高低温和耐磨等性能优异。聚氨酯涂料属于高固低 VOC 涂料,环境污染物排放量很低;聚氨酯涂料与基底附着力强,物理机械性能优异,装饰性能也很强,可在重防腐领域中作为面漆使用。
目前,国内外对水性聚氨酯防腐涂料改性方法有很多,主要包括:环氧树脂改性、有机硅共聚改性、纳米改性、复合改性。改性后水性聚氨酯防腐涂料的性能得到了很大的改善,但仍存在耐水性不强,对施工条件要求苛刻,产品价格较高等问题。
研发新的水性聚氨酯防腐涂料改性方法是水性聚氨酯防腐涂料科研的主要方向,如使用乳化剂或者在主链上引入羧基、羟基等亲水基团制备水性聚氨酯涂料,研究的重点是如何提高其耐水性和缩短固化时间等方向;另外,双组份聚氨酯涂料的研发很不成熟,这也是以后的一个研究热点。总之,开发高性能的水性、高固体含量聚氨酯涂料,通过与环氧树脂、氟碳树脂等不同类型涂料联用的技术是今后的研发方向。
3.1.1海洋防腐涂料的发展
未来海洋重防腐涂料的发展方向是 : 环保、节能、省资源、高性能和功能化。例如 : ①低表面处理防锈涂料不但可以减轻表面处理的压力,避免预处理对环境造成的污染,并可节约大量维修费用 ; ②无铅无铬化是无公害高性能防锈颜料和填料的发展方向 ; ③水性无机富锌涂料作为零 VOC 的环保型水性防腐涂料被广泛应用 ; ④无溶剂涂料是研究的热点,主要有无溶剂环氧涂料、无溶剂聚脲和聚氨酯涂料 ; ⑤纳米粒子的引入可以改善涂料流变性,提高涂层附着力、涂膜硬度、光洁度和抗老化性能,是重要的发展方向之一 ; ⑥超耐候性面漆———氟碳树脂及含氟聚氨酣等改性材料是面漆基料的极佳选择,除用于船壳漆外,还可用于接触强腐蚀介质的内舱涂料等。换句话说,高固体化、无溶剂化 ( 包括粉末涂料化 ) 或弱溶剂化、水性化、无重金属化、高性能化、多功能化、低表面处理化、省资源化以及智能化等是涂料发展的国际趋势。
(1)环保涂料
无公害高性能防锈颜填料随着环境保护呼声的日益高涨,健康环保的海洋涂料的开发应用必将成为船舶涂料发展的趋势,防腐颜料的无铅无铬化是防腐蚀涂料的发展方向。为此专家们研究开发出抑制钢铁腐蚀的新型防锈颜料,如磷酸锌、磷酸钙、钼酸锌、钼酸钙以及含锌化合物等;新型的锌 - 硅酸盐改性的三聚磷酸铝颜料等也是替代重金属颜料的有效品种。金属锰和其化合物在防腐涂料中作为防腐蚀作用的抑制性颜料使用无论是单独效能还是综合效能,与传统的钼酸盐和铬酸盐抑制性颜料几乎具有相同的效果;铁氧体作为防腐蚀活性颜料也具有极佳的防腐效能。美国Gerace 公司用离子交换型防锈颜料代替含重金属的防锈颜料,配制的涂料已用于北海油田平台的防腐;发达国家已经禁止使用红丹防锈漆,所生产涂料中的颜料也都采用无毒的铝粉、锌粉、铁红等。
纳米微粒,如纳米级 TiO 2 、ZnO、CaCO 3 及 SiO 2 ,用于防腐涂料具有极好的协同作用。纳米颗粒与涂层形成较强的氢键结合,增强了涂层的致密性及抗离子渗透性。此外,纳米微粒还可以改善涂料的流变性,提高涂层的附着力、硬度、光洁度和耐老化性,是重要的发展方向之一。
(2)水性涂料
水性涂料中最重要的防腐涂料就是水性无机富锌涂料,它是以无机物为主要成膜物、高含量的锌粉为防锈颜料、水为分散介质的高固体分厚膜涂料,是海洋环境防腐蚀领域中防锈性能最优异的一类涂料,并且很有推广价值。水性无机富锌涂料作为一种零 VOC 的环保型防腐涂料,已被各行各业所接受,具有广阔的发展和应用前景。近年国外还出现了无机磷酸盐水性富锌涂料,对底材处理要求相对较低,性能优异。如德国GalvatechLed公司开发的Zinga富锌涂料,含锌 95%,已使用多年,防腐性能极好。近年国内水性高模数硅酸钾、硅酸锂富锌涂料已在工程上应用,性能也在不断改进完善中。除了水性无机富锌涂料外,厚浆醇酸、水性环氧、丙烯酸改性醇酸或环氧、水性聚氨酯等水性涂料已达到了产业化和实际应用的阶段,在内舱和油水舱中底面配套使用时可极大地改善施工环境。但是,因为船舶所处的环境比较恶劣,水性涂料的防腐蚀性能还达不到要求,使得水性涂料在船舶上的应用较少。
(3)低处理表面防锈涂料
船舶及海洋设施有许多狭小或不能搬动的部件,维修时往往难以进行彻底的表面处理,通常处理后仍带有不同程度的锈蚀物,并经常处于高度潮湿及带油(油舱维修时)的状态,需要一种可以在这种低处理表面上直接进行涂装的高性能涂料。这种涂料不但减轻了表面处理的压力,避免了预处理对环境造成的污染,并且节约了很多维修费用,目前国内外各公司均试图开发出能适应低处理表面的通用底漆。
(4)无溶剂聚脲、聚氨酯涂料
20世纪90年代以来,无溶剂聚脲、聚氨酯喷涂工艺得到了迅速发展。它一次喷涂厚度可达到 2cm,几分钟即可固化成膜,不受施工环境的影响,特别适合于要求快速施工的厚涂平台甲板和弹性地板涂装。但是当务之急是开发与之配套的原材料和施工工艺。为此,近年来国外为适应环保要求而研制开发了一种新型无溶剂、无污染的防腐及装饰材料:无溶剂聚脲弹性体及其涂装技术。该弹性体具有强度高,柔韧性、耐磨性、抗湿滑性、抗热冲击性、抗冻性及装饰性好等特点,同时也具有耐酸、碱、油、盐及盐雾等多种化学介质的腐蚀和防水等性能,这类涂料已在化工设备及港口设施中得到了广泛应用。国内的海洋化工研究院也开发了相应的体系,其研究水平处于国内领先地位。
3.2防污涂料
船舶和海洋工程结构建设在海洋管线、钢桩、平台等部分,一定会面临着海洋污损生物的侵害与腐蚀,此生物污损而导致的后果特别严重,是广泛存在的腐蚀类型。因为海洋微生物可以依附在工程设备的表面上,既影响设备外观,也对船舶的正常行驶造成影响,出现提高燃油成本等问题。防污涂料可以比较全面的保护船舶和海洋工程结构,降低和避免海洋生物对其的污损和附着。在实际使用过程中,防污涂料对海洋生物而言是一种有毒制剂,此防污剂能够有效的将海洋工程结构表面上的海洋生物清理掉。防污涂料包括无机类和有机类两种。其中有机类包括有机锡化合物、有机氧化合物等;无机类包括氯化锌、氧化亚铜、氧化汞等[1] 。
图1 海洋生物污损形成过程(网络版彩图)
海洋防污涂料的使用由来已久,可追溯到公元前 2000 多年。最早的时候,为了保护船底,人类开始将薄铅板包覆在船壳上,后来人们开始懂得将硫磺、砷等与油混合后涂覆在船底,再逐渐发展到采用焦油、蜡和铅覆盖船体。到了公元前 3 世纪,罗马人和希腊人用铜钉来保护铅覆盖物。13 ~ 15 世纪,沥青被广泛用于船舶的保护,甚至有时与油、松香或动物脂混合使用。随着时代发展,铜板开始被用作防污材料,防污效果也有了很大的提高。由此人们意识到铜离子对海生物具有很强的杀灭作用,从而开创了以铜离子为毒料制备船底防污涂料的时代。
18 世纪中期以来,从聚合物介质中释放毒物这一想法出发,人们开发了不同品种的防污涂料,并且受到了广泛欢迎。1906 年,美国海军造船厂就在该原理的基础上,选用焦油为基料,选用红色氧化汞为毒料,配制成防污涂料,结果表明:这种防污涂料的平均防污期限可达9 个月。1926 年,松香被美国海军成功地用于船舶防污涂料中,并且选用铜和汞的氧化物作为毒料,从而使船舶防污涂料的防污期限从 9 个月增加到 18 个月。
20 世纪 50 年代中期,人们开始将有机锡作为毒料用于船舶防污涂料中。三丁基锡(TBT)具有广谱高毒性,60年代初人们开发出含有 TBT 毒料的船舶防污涂料,并很快进入市场,当时这种广谱杀虫剂还是以游离的形式存在于涂料中,直到 70 年代,人们才开发出一种长效的有机锡自抛光船舶防污涂料(TBT-SPC),很快就成为防污涂料的主流产品。TBT 防污剂在海水中有一定的溶解度,会对海生物和海洋环境造成破坏,从而影响海生物的生长繁殖,甚至有可能引起畸形,而且能在生物体富集,通过食物链进入人体,对人类的生命安全造成危害。因此国际社会逐渐意识到有机锡对海洋生态,甚至是人类的潜在威胁,各个沿海国家也纷纷通过立法来限制有机锡的使用[2-4] 。
1999 年 11 月,在伦敦举行的第 21届国际海事组织会议通过一项决议,规定把使用 TBT 的最终期限定为 2003 年1 月 1 日, 从 2008 年 1 月 1 日 开 始,完全禁止在防污涂料中使用 TBT,即 2008 年后,涂有有机锡防污涂料的船舶不再允许在海上航行。自此,海洋防污技术进入了全新的时代,主要的防污涂料公司,如英国国际涂料公司、丹麦 HEMPEL 公司、挪威 JOTUN 公司、荷兰 SIGMA 公司、美国AMERON 公司等,从 2003 年 1 月开始不再生产含有 TBT 的防污涂料。因此对新型环境友好型无毒防污涂料的研发刻不容缓。
目前的防污除污方法主要有物理防污法、化学防污法和生物防污法等,因本身具有的局限性,远远不能满足日益增长的海洋开发工作对高效经济环保的防除手段的需要。新型环境友好型无毒防污涂料见表。
(1)无锡自抛光防污涂料[4-5]
目前应用最广泛的低毒防污涂料主要为以丙烯酸硅、铜和锌作为树脂基料的无锡自抛光防污涂料,其基料设计主要借鉴了有机锡树脂的结构设计 : 在丙烯酸树脂主链接枝含硅、铜或锌侧链基团,形成类似于有机锡侧链基团的结构,使含硅、铜或锌侧链基团在海水环境中也可与海水中的钠离子发生离子交换反应而逐渐水解,并溶解至水体中,如图。由于这类新型树脂不含有机锡,具有良好的环保性,因此无锡自抛光防污涂料也逐渐成为低毒防污技术的研究热点,截至 1996 年,关于无锡自抛光防污涂料的注册专利已达数百项。
但是,丙烯酸铜、硅或锌无锡自抛光防污涂料的实际使用效果并未达到有机锡防污涂料的使用效果,主要原因是侧链的水解性能受水解过程中树脂玻璃化转变温度变化、吸水性及树脂膨胀变化等因素影响,同时涂料体系中含有松香,导致其光稳定性更高。另外,侧链基团无任何防污作用,需要依靠添加杀生剂来抑制污损生物的附着,如氧化亚铜。
尽管丙烯酸铜、硅或锌无锡自抛光防污涂料通过与海水发生作用实现杀生剂的有效控释,可满足长效自抛光防污需求,但是由于其高抛光速率及树脂骨架需海水冲刷的特性,其涂料表面容易形成释出层,往往释出层厚度会随着抛光时间的延长而增厚,造成释出层孔隙路径增长,后期会影响杀生剂的有效渗出,如图。因此该类型防污涂料通常最长应用寿命为 3 年,部分可达 5 年,但是无法达到有机锡防污涂料的高效防污效果。
随着生物降解材料的发展,人们开始利用生物降解材料的生物降解特性,将其应用于无锡自抛光防污涂料体系。主要采用含醚键或酯键的聚酯聚合物作为树脂基料,利用醚键或酯键在碱性海水中缓慢水解来使聚酯聚合物发生降解,通过其降解作用进行杀生剂控释,同时避免树脂主链残留过多形成释出层,影响杀生剂渗出。
(2)仿生防污涂料[3-6]
表面结构仿生
结构仿生防污的仿生对象主要是大型的海洋动物如鲨鱼、海豚、鲸等或者贝类。其研究重点是利用分子技术,设计制备特定的高分子材料,模拟大型动物的表皮结构和几何形貌,形成一系列的人工表面。这种模拟通常是微纳米级的,而且是多结构的,任何单一的人工结构都不能防止多种海洋生物的附着污染。
其中最经典的是借鉴了鲨鱼皮的结构特征。鲨鱼皮是由微小的矩形鳞片组成,鳞片为盾鳞,排列紧凑有序,呈齿状,齿尖趋向同一方向,前后相临的鳞片在边缘部位有重叠现象。这些微小鳞片及其有序排列,使鲨鱼表面比较光滑;同时鲨鱼表皮分泌黏液,形成亲水低表面能表面,但其表皮并不是光滑的,其矩形鳞片上附有刺状突起和刚毛,按照特殊的排列方式形成 V 形微沟槽,同时使海洋生物难以附着。
化学仿生防污涂料
从海绵、珊瑚、红藻、褐藻中已提取甾类化合物、杂环化合物、生物碱等化合物,证明具有防污作用,将这些物质添加到自抛光防污涂料体系,通过自抛光作用,使表面不断更新,宛如不断分泌补充驱避物质的海洋生物表面,达到防污目的。
近年在化学仿生防污方面的最新成果是生物酶的研究,如藻类生物所含的钒卤代过氧化物酶。在酶的催化作用下,海水中的过氧化氢与溴化物离子产生少量的次溴酸,分解附着生物的蛋白质,干扰污损生物的代谢,抑制附着生物的变形和生长,从而达到防污的目的。
仿生防污涂料的研究不仅开展了海洋生物的模仿,同时也逐渐开始关注人类自身。目前应用于人工脏器制造的高分子材料,需与血液接触,因此需要具有优良的抗凝血性能。由于生物的污损与血管内血栓的形成有很大的相似性,都是从蛋白质或生理物质的附着开始的。基于这一点,开发出了具有微相分离结构的防污涂料。但是该类涂料面临的最大问题是如何在复杂的施工现场环境下形成相分离结构,而且如何将微相分离结构控制在一定的尺寸范围内,这些都是值得关注的。
(3)低表面能防污[5]
无毒低表面能防污涂料 (FRC) 不含任何杀虫剂,环境友好性能得到广泛认可,其研究已经取得很大的进展,并获得了商业应用。低表面能防污涂料主要以有机硅、有机氟污损释放型防污涂料为主,此类防污涂料通过涂层低表面能的特性使污损生物不易附着或附着不牢,容易被水流冲刷掉,从而达到防污的目的。从理论上讲,完全不依靠防污剂的渗出来防污。
低表面能防污涂料的代表是阿克苏诺贝尔旗下国际油漆公司的旗舰产品 Intersleek 系列,利用其专利氟树脂技术,现已开发出三代产品。最新的一代产品是 Intersleek1100 SR,可以用于温带水域,甚至是速度较慢的航行环境中。其次是 PPG 公司 2014 年 7 月推出的最新 产 品 Sigmaglide1290,100% 采 用 分子水平的硅氧烷树脂,该涂料所形成的涂层表层硅氧烷密度高,以至于海洋生物感知不到是可以附着的表面,无法进行附着。该涂料采用动态的表面再生技术,利用水作催化剂,使涂层不断恢复到初始的表面能状态,因此克服了低表面能防污涂料随着时间推移受紫外线、太阳光及污染物的作用而劣化失效的缺点。该涂料实现了低表面能涂料的技术突破。Hydrex 公司的 Ecospeed 防污产品是一种玻璃鳞片加强的无毒非硅氧烷体系,基于乙烯酯树脂,涂装后形成酒窝状的坚硬涂层表面,且使船壳的粗糙度降至 20μm 以下。
(4)纳米防污涂料[4-6]
由于纳米材料具有表面效应、小尺寸效应、量子尺寸效应、宏观量子隧道效应等诸多优良的特性,将纳米材料引入环境友好型抗海洋生物污损涂料可以使涂料得到更加优异的物理化学性能。此外,通过加入纳米粒子制备出具有微米 - 纳米阶层结构的无毒疏水海洋防污涂料,使涂层表面含有大量的微米纳米乳突、微纳米孔道和凹槽的微观粗糙疏水结构,形成理想的疏水表面,借此提升涂料的抗污性能。
Ag 具有优异的广谱抗菌特性,环境友好,安全、无毒副作用,而纳米Ag 由于其表面效应,抗菌能力是微米级 Ag 的 200 倍以上,且纳米颗粒的尺寸越小,其抗菌活性越高。因此,纳米Ag 材料广泛用于抗菌及抗生物污损;纳米 SiO 2 的加入可使原来涂料的涂膜硬度、抗磨耗、抗划伤及抗污性能多种性能均得到显著提高;纳米 TiO 2 不仅可以改善涂料的成膜性能,而且纳米 TiO 2 在光照射下能产生强烈的氧化能力,将有机污染物降解;纳米级的 Cu 2 O 结合高效杀生剂制成纳米防污涂料,包裹在基料中的Cu 2 O不会随海水的冲刷而流失,但是可以缓慢地释放出来,达到了长效防污的效果。纳米 Cu 2 O 可改善与防污涂料中其他组分的相容性,使防污涂料稳定有效地释放防污剂,并可减少防污涂料中防污剂的用量;随着性能优异的纳米海洋无毒防污涂料的陆续出现,在现有单一添加纳米材料实验的基础上,将几种不同的纳米材料同时添加到防污涂料中进行复配,对于防污性能有一定增强的空间。
(5)导电防污涂料[6]
导电防污涂料的作用原理是通过在漆膜表面产生微弱的电流,使海水电解产生次氯酸离子,以达到防污目的。导电防污涂料主要有两种作用方式:一是在船体表面涂覆一层导电高聚物,船体为阴极,导电涂膜为阳极,通入微电流电解海水,在涂层表面形成次氯酸离子层,从而起到防污效果;二是不通微电流,将电导率较大的掺杂导电高聚物为有效物质的涂料直接涂覆在船体上。
导电涂料一般分为本征型导电涂料和掺杂型导电涂料。本征型导电涂料有聚苯胺、聚吡咯、聚噻吩和聚喹啉等。掺杂导电涂料是以高聚物为基础加入石墨、金属氧化物和纳米管等导电物质而具有导电性的涂料。导电涂膜防污技术是一种环保型的防污技术,对环境无污染,但是由于其受环境等因素的影响比较大,未能在船体大面积推广使用。
海洋防污涂料的发展趋势是开发环境友好型防污涂料。目前众多环保型防污涂料中,无锡自抛光防污涂料是唯一获得大规模商业化应用的一种涂料产品,其面临的最大问题依然是低效性及有毒性。防污涂料的发展方向应该是低毒环保、广谱高效,未来防污涂料的研究方向是将仿生技术和纳米技术相结合的污损释放型防污涂料。
传统溶剂型防污涂料不仅含有较多有机溶剂,而且添加的防污剂大多是对环境有不利影响的有机物质,违背了防污涂料环保、低毒的发展方向,因此以天然提取物作为防污剂的环境友好型防污涂料是未来防污涂料的发展方向。
在仿生技术方面,各国研究者在模仿海生物的表面机体结构、模仿海生物表面渗出物质,以及低表面能仿生方面取得了巨大进步,其中低表面能仿生技术已经获得初步的应用;
在纳米技术方面,我国起步较晚,研究较少,可以商业化的产品甚至研究成果更是少之又少,与世界先进水平还有很大的差距,但在实验室阶段已取得一定进展。将纳米材料与低表面能涂料结合,不但能获得较好的性能,而且符合环境友好型标准。我国也不断有研究人员在低表面能防污涂料中应用到纳米技术,并取得了实质性进展。将仿生技术和纳米技术相结合的低表面能防污涂料将成为 21 世纪防污涂料的主流。
3.3耐腐蚀材料 [5-8]
海洋中使用的耐腐蚀材料包括 : 耐海水腐蚀钢、耐腐蚀钢筋、双相不锈钢、钛合金、铜合金、复合材料、高分子材料、高性能混凝土等。金属和钢筋混凝土的使用量最大。
耐腐蚀金属材料是通过调整金属材料中的化学元素成分、微观结构、腐蚀产物膜的性质,实现降低电化学腐蚀的反应速度,从而可以显著改善金属材料的耐腐蚀性。
美国从 1936 年开始研制耐海水腐蚀钢,到1951年研制成功了“Mariner”钢。法国研制出 Cr - Al 系的耐海水腐蚀钢APS 系列。日本的几大钢厂也已研制出不同的系列,如新日铁 Mariloy 系列钢、JFE 海洋系列钢、三菱制钢 NEP-TEN50与 60、神户制钢所 TAICO R M50A.B.C。德国研发出 HSB55C 钢 (Ni - Cu - Mo系 )。我国从 1965 年起开始研制耐海水腐蚀钢,主要有 Cu 系、P-V 系、P-Nb-R e 系和 Cr-Al 系等类型,如 08PV、08PV R e、10CrPV 等,但与国外比较,我国的耐海水腐蚀钢还有待进一步研发。近年来日本已经在船舶上使用免涂装的耐腐蚀钢,已有 20 多条船采用了耐腐蚀钢,日本在极力推荐使之成为国际标准用钢。此外,运动部件还需要考虑耐腐蚀性与耐磨损性能的相互协调,同时具有耐腐蚀磨损的能力。
3.4表面处理技术 [6, 8]
表面改性或称为表面处理,是采用化学物理的方法改变材料或工件表面的化学成分或组织结构以提高部件的耐腐蚀性。化学热处理 ( 渗氮、渗碳、渗金属等)、激光重熔复合、离子注入、喷丸、纳米化、轧制复合金属等是比较常用的表面处理方法。前 3 种是改变表层的材料成分,中间两种是改变表面材料的组织结构,后者则是在材料表面复合一层更加耐腐蚀的材料。
虽然对于大面积的海上构筑物可以采用重防腐涂料等防护技术,但对于许多形状复杂的关键部件,如管件、阀门、带腔体、钢结构螺栓、接头等复杂结构的零部件,在其内部刷涂层比较困难,传统的防腐涂料无法进行有效保护并很难达到使用要求。因此一方面通过提高材料等级来防腐,例如 : 使用黄铜、哈氏合金、蒙乃尔合金、钛等金属材料来制作复杂的零部件。另一方面,亟需发展先进的低成本表面处理等防腐技术。例如 : 随着超深、高温、高压、高硫、高氯和高二氧化碳油气田尤其是海上油气田的相继投产,传统单一的材料及其防腐技术已不能满足油气田深度开发的需要,双金属复合管的应用正在迅速扩大,即采用更耐腐蚀的材料作为管道的内层金属实现抗腐蚀。
对于复杂结构部件,常采用化学镀镍进行表面处理。近年来银 / 钯贵金属纳米膜化学镀是一种新的方法,它与基体形成化学电偶,银 / 钯将诱使基体金属阳极钝化或在钝化膜被破坏时在钯提供的阳极电流作用下将有更好的自修复能力,从而起到较好的防护作用。以先进热喷涂技术、先进薄膜技术、先进激光表面处理技术、冷喷涂为代表的现代表面处理技术,是提高海洋工程装备关键部件性能的重要技术手段。
超音速火焰喷涂 (HVOF) 是 20 世纪80 年代出现的一种热喷涂方法,它克服了以前的热喷涂涂层孔隙多、结合强度不高的弱点。HVOF 制备耐磨涂层替代电镀硬铬层是其最典型的应用之一,已应用在球阀、舰船的各类传动轴、起落架、泵类等部件中。近年来,低温超音速火焰喷涂 (LT - HVOF) 以其焰流温度低、热量消耗少、沉积效率高而成为HVOF 的发展趋势。应用 LT - HOVF 可获得致密度更高、结合强度更好的金属陶瓷涂层、金属涂层。如 : 在钢表面制备致密的钛涂层,提高钢的耐海水腐蚀性能;在舰船螺旋桨表面制备NiTi涂层,提高螺旋桨的抗空蚀性能。
等离子喷涂是以高温等离子体为热源,将涂层材料融化制备涂层的热喷涂方法。由于等离子喷涂具有火焰温度高的特点,非常适合制备陶瓷涂层,如Al 2 O 3 、Cr 2 O 3 涂层,从而提高基体材料的耐磨、绝缘、耐蚀等性能。但是,等离子喷涂制备的涂层存在孔隙率高、结合强度低的不足。近年来发展的超音速等离子喷涂技术克服了这些不足,成为制备高性能陶瓷涂层的极具潜力的新方法。
气相沉积薄膜技术主要包括物理气相沉积和化学气相沉积。利用气相沉积薄膜技术可在材料表面制备各种功能薄膜。如起耐磨、耐冲刷作用的 TiN、TiC薄膜,兼具耐磨与润滑功能的金刚石膜,耐海水腐蚀的铝膜等。
激光表面处理是用激光的高辐射亮度、高方向性、高单色性特点作用于金属材料特别是钢铁材料表面,可显著提高材料的硬度、强度、耐磨性、耐蚀性等一系列性能,从而延长产品的使用寿命并降低成本,如利用激光熔敷技术对扶正器进行表面强化来提高其表面耐磨、耐蚀性能。激光技术的另一个重要应用则是对废旧关键部件进行再制造,即以明显低于制造新品的成本,获得质量和性能不低于新品的再制造产品,如对船用大型曲轴和扶正器的再制造等。
冷喷涂是俄罗斯发明的一种技术,由于喷涂温度低,在海洋工程结构的腐蚀防护中具有潜在的应用价值。
总之,现代表面工程技术是提高海洋工程装备关键部件表面的耐磨、耐腐蚀、抗冲刷等性能,满足海洋工程材料在苛刻工况下的使役要求,延长关键部件使用寿命与可靠性、稳定性的有效方法,也是提升我国海洋工程装备整体水平的重要途径。
3.5电化学保护[ 8-9]
金属 - 电解质溶解腐蚀体系受到阴极极化时,电位负移,金属阳极氧化反应过电位减小,反应速度减小,因而金属腐蚀速度减小,称为阴极保护效应。电化学 ( 阴极 ) 保护法分两种 : 外加电流阴极保护和牺牲阳极阴极保护。
牺牲阳极阴极保护是将电位更负的金属与被保护金属连接,并处于同一电解质中,使该金属上的电子转移到被保护金属上去,使整个被保护金属处于一个较负的相同的电位下。该方式简便易行,不需要外加电源,很少产生腐蚀干扰,广泛应用于保护小型 ( 电流一般小于 1A) 金属结构。对于牺牲阳极的使用有很多失败的教训,失败的主要原因是阳极表面生成一层不导电的硬壳,限制了阳极的电流输出。
外加电流阴极保护是通过外加直流电源以及辅助阳极,迫使电流从介质中流向被保护金属,使被保护金属结构电位低于周围环境。该方式主要用于保护大型金属结构。
近些年来,深海环境下材料及构件阴极保护的研究受到了格外的重视。阴极保护可以采用牺牲阳极方式,也可以采用外加电流方式。从可靠性和管理维护等方面来看,以牺牲阳极型的阴极保护居多。
20 世纪 60 年代开始,我国开发了一系列的常规牺牲阳极材料,目前无论船舶还是海洋工程结构的常规阴极保护都大多采用了国产阳极,几乎完全实现了国产化,并且已大量出口。近年来我国也开发了深海牺牲阳极(深海环境)、低电位牺牲阳极 ( 高强钢等氢脆敏感材料)和高活化牺牲阳极(干湿交替环境)材料,但这类关键部位的牺牲阳极材料还是主要国外进口。
3.6缓蚀剂
缓蚀剂是“一种以适当的浓度和形式存在于环境 ( 介质 ) 中时,可以防止或减缓腐蚀的化学物质或几种化学物质的混合物。”一般来说,缓蚀剂是指那些用在金属表面起防护作用的物质,加入微量或少量这类化学物质可使金属材料在该介质中的腐蚀速度明显降低直至为零。同时还能保持金属材料原来的物理、力学性能不变。合理使用缓蚀剂是防止金属及其合金在环境介质中发生腐蚀的有效方法。缓蚀剂技术由于具有良好的效果和较高的经济效益,已成为防腐蚀技术中应用最广泛的方法之一。尤其在石油产品的生产加工、化学清洗、大气环境、工业用水、机器、仪表制造及石油化工生产过程中,缓蚀技术已成为主要的防腐蚀手段之一。
缓蚀剂可分为无机缓蚀剂、有机缓蚀剂、聚合物类缓蚀剂。
①无机缓蚀剂:无机缓蚀剂主要包括铬酸盐、亚硝酸盐、硅酸盐、钼酸盐、钨酸盐、聚磷酸盐、锌盐等。
②有机缓蚀剂:有机缓蚀剂主要包括膦酸 ( 盐 )、膦羧酸、琉基苯并噻唑、苯并三唑、磺化木质素等一些含氮氧化合物的杂环化合物。
③聚合物类缓蚀剂:聚合物类缓蚀剂主要包括聚乙烯类,POCA,聚天冬氨酸等一些低聚物的高分子化学物。
参考文献:
[1] 王路明,海洋材料「M]. 北京 : 化学工业出版社,2008.
[2] 刘建国,中国科学院海洋研究所,博士论文,2010.
[3] 刘涛,中国海洋大学,博士论文,2009.
[4] 张洪荣,原培胜。船舶防污技术[J]。舰船科学技术,2006,28(1):10-14[5] 辜志俊,苏方腾,张志刚,等。防海生物污损材科的研究[J]。腐蚀与防护,1999,20(4):166.
[6] 何庆光,任润桃,叶章基。船舶防污涂料用树脂基料的发展及作用[J]。涂料工业,2009,39(6):51-55.
[7] 陆刚,余红伟,晏欣,魏徵等 . 船舶防污涂料的研究现状及展望 [J]. 弹性体,2016,26(4):74-77.
[8] 韩 恩 厚, 陈 建 敏, 宿 彦 京, 刘 敏 . 海 洋 工 程 结 构与船舶的腐蚀防护———现状与趋势 [J]. 中国材料进展 ,2014,33(2):65-76.
[9] 许君男,海洋工程结构与船舶防腐蚀技术措施研究 [J].现代商贸工业 ,2015,9:221-222.
免责声明:本网站所转载的文字、图片与视频资料版权归原创作者所有,如果涉及侵权,请第一时间联系本网删除。
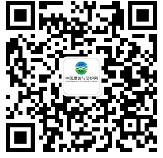
官方微信
《中国腐蚀与防护网电子期刊》征订启事
- 投稿联系:编辑部
- 电话:010-62316606-806
- 邮箱:fsfhzy666@163.com
- 中国腐蚀与防护网官方QQ群:140808414