一文解析钢的渗碳 将金属或者合金工件放置在活性介质中加热或者保温条件,让一种或几种元素渗入其表层改变其化学成分、组织和性能,称为金属的化学热处理。这种化学热处理实际上是通过介质高温裂解物在金属材料表面进行分解、吸附、固溶、化合反应,使元素进入金属表面形成一种或多种合金元素的渗层,能够提高工件“表硬内韧”的性能要求。 今天我们主要解析渗碳,顺便跟渗氮做一对对比,方便大家区别这两种化学热处理工艺。
化学热处理技术在现代工业中被广泛应用,能够提高金属工件得表面强度、硬度、耐磨性等力学性能、抗咬合性能、抗疲劳性能以及特殊的耐蚀性、抗高温氧化性能等物理化学性能,同时工件自身还应保持原有的良好的塑韧型等基本性能,从而提高机器零件在各种复杂工况下的耐用度。
化学热处理的主要特征:
固体扩散渗入改变工件表面层的化学成分,又改变其组织,渗层与基体之间有扩散层,获得单一材料难以获得的性能或进一步提高工件的使用性能。绝大多数化学热处理后对工件的变形小、精度高、尺寸稳定性好的特点。该过程是一个复杂的物理化学过程,工艺处理周期较长,对设备的要求也比较高。
化学热处理的驱动力是浓度梯度。
化学热处理形成渗层的结构遵守相图,其结构是连续的,属于冶金结合。
化学热处理的分类方法多样,包括按照元素种类、渗入先后顺序及渗入时金属状态进行分类:
定义:
将钢件置于具有足够碳势的介质中加热到奥氏体状态并保温,使其表层形成一个富碳层的热处理工艺。
碳势:
纯铁在一定温度下于加热炉气中加热时达到既不增碳也不脱碳并与炉气保持平衡时的表面含碳量。
目的:
渗碳介质在工件表面产生的活性碳原子,经过表面吸收和扩散将碳渗入低碳钢或低碳合金钢工件表层,使其达到共析或略高于共析成分时的含碳量,以便将工件淬火和低温回火后,提高工件表面的硬度、耐磨性和疲劳强度,同时保持心部具有一定强度和良好的塑性与韧性。
应用范围:
在机器制造业中,有许多重要零件,如汽车变速箱齿轮、活塞销、摩擦片等。可以渗碳的钢一般是碳的质量分数为0.12%-0.25%的低碳钢或低碳合金钢如20、20Cr、20CrMnTi、20CrMnMo、18Cr2Ni4W等。
根据渗碳剂的不同,渗碳方法可分为固体渗碳、液体渗碳和气体渗碳。
(1)固体渗碳---粒状或膏状渗碳剂中渗碳。
将工件置于填满木炭(90%左右)和催渗剂(BaCO3、CaCO3或 Na2CO3等)(10%左右)的固体渗碳箱内进行的,如图1所示。固体渗碳在渗碳法中历史最老,不适于连续处理大量工件,作业环境不良,已有衰退倾向,不过炉及其他设备也较简单,多种少量的处理也较方便,不至完全绝迹。
图1 固体渗碳箱
1-渗碳剂 2-工件 3-箱体4~6mm
铁板 4-泥封 5-试棒ϕ10mm
6-盖:铁板厚6~8mm
缺点:渗速慢,劳动条件差
(2)液体渗碳---盐浴渗碳
液体渗碳就是在液体介质中进行的渗碳工艺。
可分为两类:一类是加有氰化物的盐浴,另一类是不加氰化物的盐浴。因氰化物有剧毒现已基本不用。不加氰化物的盐浴由NaCl或KCl、Na2CO3、和(NH2)2CO或木粉组成,如图2所示。
图2 井式气体渗碳炉
1-风扇电动机 2-废气火焰 3-炉盖 4-砂封 5-电阻丝 6-耐热罐 7-工件 8-炉体
优点:液体渗碳技术渗层性能优良,工艺简单,采用无毒低氰渗剂容易操作,且对人体危害小,可以广泛的得到推广与应用
(3)气体渗碳---有机含碳气氛
气体渗碳是指零件在气体渗碳剂中进行渗碳的工艺。气体渗碳法的生产率高,渗碳过程容易控制,渗碳层质量好,且易实现机械化与自动化,应用最广。
优点: 质量好, 效率高;
缺点: 渗层成分与深度不易控制
原理
1)渗碳介质的分解
由介质中分解出活性碳原子。渗碳气氛在高温下分解出活性碳原子[C],即:
注:在供应的原料气组分稳定的情况下,只要控制气氛中的微量组分CO2、H2O、CH4或O2中的任何一个含量,便可控制上述反应达到某一平衡点,从而实现控制气氛碳势的目的。通常,生产中用露点仪控制H2O含量;用红外线仪控制CO2含量;用氧探头法控制O2含量。
2)碳原子的吸收 工件表面吸收活性碳原子,也就是活性碳原子由钢的表面进入铁的晶格而形成固溶体,或形成特殊化合物。
3)碳原子的扩散 被工件吸收的碳原子,在一定温度下,由表面向内部扩散,形成一定厚度的渗层。
工艺参数选择
1)气氛碳势
一般渗碳件的表面含碳量可在0.6%-1.1%间变化。确定最佳表面碳含量的出发点首先是获得最高的表面硬度;其次是使渗层具有最高的耐磨性和抗磨损疲劳性能。研究表明,渗碳层的表面碳的质量分数最好在0.8%-1.0%范围内最佳表层碳含量确定后就可根据表面碳含量与碳势的关系,确定碳势。
2)渗碳温度
渗碳温度首先影响着分解反应平衡,粗略地说,如果气氛中的CO2含量不变,则温度每降低10℃将使气氛碳势增加约0.08%;其次,温度也影响碳的扩散速度,如果气氛碳势不变,温度每提高100 ℃可使渗碳层深度增加1倍;第三,温度还影响着钢中的组织转变,温度过高会使钢的晶粒粗大。生产上广泛使用的温度是900-930 ℃。对于薄层渗碳温度可降到880-900 ℃,这主要是为了控制渗碳层深度;而对于深层渗碳(大于5mm),温度可提高到980-1000 ℃,这主要是为了缩短渗碳时间。
3)渗碳时间
渗碳时间主要影响渗层深度,同时也在一定程度上影响浓度梯度。
d—渗层深度(mm);t—渗碳时间(h);T—渗碳温度(K)
渗碳工艺参数的综合选择 图3 气体渗碳典型工艺曲线 ①升温阶段 工件达到渗碳温度前的一段时间,用较低的碳势; ②高速渗碳阶段 正常温度或更高温度下,用高于所需表面碳含量的碳势,时间较长; ③扩散阶段 工件降到或维持在正常渗碳温度下碳势降到所需表面碳含量,时间较短; ④预冷阶段 使温度降低到淬火温度,便于直接淬火。 低碳钢渗碳后,表层含碳量可达过共析成分,由表往里碳浓度逐渐降低,直至渗碳钢的原始成分。 渗碳件缓冷后,表层组织为珠光体加二次渗碳体;心部为铁素体加少量珠光体组织;两者之间为过渡层,越靠近表层铁素体越少 。一般规定,从表面到过渡层一半处的厚度为渗碳层的厚度。 图4 低碳钢渗碳缓冷后的显微组织 表1 典型零件渗碳层厚度确定方法 1.淬火 淬火是为了获得马氏体组织,以得到高硬度。通常有三种方法,即预冷直接淬火、一次加热淬火和二次加热淬火。渗碳零件淬火温度的选择要兼顾高碳的渗层和低碳的心部两方面的要求。原则上,过共析层的淬火温度低于Accm,而亚共析层的淬火温度高于Ac3。如果Accm> Ac3,很容易选择一个淬火温度来同时满足这两者的要求;果Accm≤Ac3,则很难同时兼顾。在这种情况下,要根据对零件的主要技术要求、钢件的心部能否淬透、渗碳后零件的表面含碳量和所采用的淬火方法等综合考虑加以决定。 图5 渗碳后的热处理示意图 渗碳件常用的淬火方法: ①预冷直接淬火 对于碳钢,预冷温度应在Ar1~Ar3之间。对于多数合金钢,通常预冷温度在820~850℃之间。 ②一次加热淬火 一般合金渗碳钢,常采用稍高于Ac3的温度(820~860℃)加热淬火。 ③二次加热淬火 第一次淬火的加热温度应高于心部的Ac3温度,第二次淬火主要是为细化表层组织,温度选择稍高于表层的Ac1。 常用方法是渗碳缓冷后,重新加热到Ac1+30-50℃淬火+低温回火。 此时组织为: 表层:M回+颗粒状碳化物+A’(少量) 心部:M回+F(淬透时) 2.回火 渗碳件淬火后尚需进行低温回火,回火温度通常为150~190℃。 3.冷处理 作用是减少或消除残余奥氏体,从而适当提高渗层硬度。由于冷处理生产成本高,又增加了工序,目前生产中除特殊渗碳零件外,一般很少采用。
1)外观
工件表面无氧化、锈蚀、剥落、碰伤、裂纹等。
2)硬度
在淬火、回火后检验,表面硬度、心部硬度及非渗碳区硬度应符合技术要求。对渗碳齿轮,JB/T7516-1994规定表面硬度以分度圆处齿面为准[1],心部硬度的检测部位为齿根圆与轮齿中心线相交处[2]。检率按规定执行。硬度不合格时,应加倍抽检,仍不合格则视情况进行返修或判报废。
3)渗碳层深度
常用渗碳层深度检测法有以下四种:
①宏观断口分析
将随炉渗碳的试样直接淬火,然后打断,观察其断口。在断口上渗碳层呈白色瓷状断口,未渗碳部分为灰色纤维状断口,根据两种断口交界至表面的距离就可以量出渗碳层深度,从而可以确定出炉时间。
②金相测量法
渗碳缓冷后的试样经磨制、腐蚀后,在显微镜下测定。碳钢的渗碳层深度是从表面垂直量至1/2过渡区[3],其渗碳层包括过共析层+共析层+1/2过渡区, 并要求过共析与共析区之和应占总层深的75%以上;合金钢渗层深度是从表面垂直量至出现心部原始组织为止,包括过共析层+共析层+过渡区全部,并要求过共析与共析区之和应占总层深的50%以上。
③硬度测量法
根据GB/T9450-2005进行测量。
④剥层化学分析法
此法精确可靠,但取样和分析较麻烦,生产中很少采用。
4)金相组织检验
一般在淬火、回火后,按有关行业标准进行检验。检验项目包括碳化物(大小、数量和分布等),马氏体针的大小及残余奥氏体数量多少,心部游离铁素体的大小和数量等。
5)裂纹
可靠性要求高的齿轮在热处理和磨齿后,100%检验,一般齿轮进行抽检。检验方法有磁粉探伤、超声波探伤、金相法等。
6)畸变
按图样技术要求进行检验。
[1] 也可用齿顶硬度代替;对斜齿轮、圆锥齿轮,还可用齿端面硬度代替,但均应考虑与齿面硬度的差异。对无法用硬度计检验的齿轮,可用标准锉刀检验,或用随炉试样检测。
[2] 心部硬度也可用随炉试样检测。其他零件心部硬度在距表面三倍渗碳层深度以外处进行检测。
[3]所谓过渡区,是指由共析区内侧至心部外侧组织之间的区域。
(一)常见缺陷
1)表面硬度偏低
2)渗层深度不够或不均匀
3)金相组织不合格
4)渗碳层内出现氧化
5)零件变形超差
6)心部硬度过高
(二)产生原因
1.表面硬度偏低
可能是表面脱碳,或出现非马氏体组织,或是表层马氏体回火抗力低等
2.渗层深度不足或不均匀
深度不足:渗碳时间过短;
深度不均匀:炉气循环不良或温度不均匀,往往与炉子设计和零件装炉情况不良有关。
3.金相组织不合格
不采用过高的气氛碳势;采用细晶粒钢;采用一次加热淬火;采用冷处理;适当提高淬火温度
4.渗碳层内氧化
渗碳气氛中含有O2,H2O,CO2等氧化性组分,而钢中又含有与氧原子亲和力比铁强的合金元素。
5.变形超差
6.心部硬度过高
(1)硬度
获得高硬度是渗碳的重要目的之一。渗碳并淬火后零件的表面层硬度可达58~62HRC。而硬度沿渗碳层的变化规律,大体上和碳浓度梯度的变化相一致,这是因为马氏体的硬度主要取决于马氏体的含碳量。
(2)耐磨性
渗碳是提高耐磨性的重要手段之一,渗碳后钢的耐磨性比普通淬火、回火的中碳钢耐磨性高得多。
一般硬度升高,耐磨性亦随之增加,但硬度并非是影响耐磨性的唯一因素。理论与实践证明,细小或隐晶马氏体和均匀分布的粒状碳化物组织的表面层具有高的切断抗力,也具有高的耐磨性。从提高耐磨性角度来看,碳量高一些好,但过高会引起起强度、塑性下降。通常渗碳件表面碳浓度以不超过1.05%为宜。
(3)强度
ⅰ渗碳层强度 图6为渗碳层强度与合碳量的关系。
从图可以看出,表层含碳且不应超过1.1%C,而在0.8-1.05%C最为合适。渗碳层组织对强度有着决定性的影响,当出现网状碳化物或粗大马氏体针和残余奥氏体过多时,均会显著降低渗碳层的强度。
ⅱ 心部强度 随着心部强度的增加,渗碳后整个工件强度亦增加。影响心部强度的主要因素是钢的淬透性。淬透性愈好,愈易在心部得到低碳马氏体。其次,心部含碳量愈高,强度也愈高。
图6 渗碳层强度与含碳量的关系
(4)塑性
图7为渗碳层的塑性(用压痕直径表示)与含碳量的关系。常用厚度为3毫米的薄片样品作渗碳试验,用它来了解渗碳层的塑性与表面层含碳量的关系。这是因为压痕增大,表示渗碳层的塑性亦增加。实验发现,含碳量增加会使渗碳层的塑性下降,当含碳量超过1.1%时,塑性将显著下降。
图7 渗碳层的塑性与含碳量的关系
(5)冲击韧性和断裂韧性
钢经渗碳后冲击韧性和断裂韧性都会降低,而且表面碳含量越高、渗层越深,这两种性能降低得也越多。
(6)疲劳强度
同高频感应加热淬火一样,渗碳也可显著提高钢的疲劳强度,这是因为在淬火时,高碳的渗层发生马氏体转变比心部晚,而且其马氏体的比容比心部大得多,使表层存在较大的残余压应力。这种残余压应力可以抵消相当一部分由于外加负载在表层引起的拉应力,从而提高疲劳强度。自然,渗层的高强度也有助于疲劳强度的提高。而工件表面压应力的大小则受渗碳层的深度及碳浓度高低的影响。当渗碳层浓度以及组织完全相同的条件下,增加渗碳层深度会提高疲劳强度。但是,在通常的情况下,增加渗层厚度将会增加表面碳浓度并使组织恶化。所以,增加渗层深度并不一定使疲劳强度增加。
总结:
渗碳可以大大改善钢的力学性能,特别是使疲劳强度和耐磨性有明显提高,因此渗碳是化学热处理中最重要最常用的一种有效强化方法。随着科学技术的发展,渗碳工艺也在不断发展。例如,为了缩短渗碳时间,提高渗碳温度的办法已得到应用,其温度可达980~1080℃。由于真空炉的推广,也大大促进了真空渗碳工艺的发展。离子氮化成功地用于生产也带动了离子渗碳的研究。为了节约能源和石油消耗,直接在工作炉内滴注有机液体以获得渗碳气氛,或以氮基气为载体气的气体渗碳法目前也有了长足的进展。采用微机对渗碳过程进行全自动控制是一个重要的发展方向。
滲氮层硬度和耐磨性高于滲碳层,硬度可达69~72HRC,且在600~650℃高温下仍能保持较高硬度;
滲氮层具有很高的抗疲劳性和耐蚀性;
滲氮后不需再进行热处理,可避免热处理带来的变形和其他缺陷; 滲氮温度较低。
渗氮只适用于中碳合金钢,需要较长的工艺时间才能达到要求的滲氮层。
免责声明:本网站所转载的文字、图片与视频资料版权归原创作者所有,如果涉及侵权,请第一时间联系本网删除。
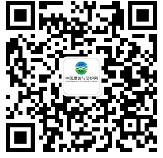
官方微信
《腐蚀与防护网电子期刊》征订启事
- 投稿联系:编辑部
- 电话:010-62316606
- 邮箱:fsfhzy666@163.com
- 腐蚀与防护网官方QQ群:140808414