硫化氢的分子量为 34. 08, 密度为 1. 539mg/m3。而且是一种无色、 有臭鸡蛋味的、 易燃、 易爆、 有毒和腐蚀性的酸性气体。
H2S 在水中的溶解度很大, 水溶液具有弱酸性, 如在 1 大气压下, 30℃水溶液中 H2S 饱和浓度大约是 300mg/L, 溶液的 pH 值约是 4。
1) 酸性气体系统:气体总压≥0. 4MPa, 并且 H2S 分压≥ 0. 0003MPa;
2) 酸性多相系统:当处理的原油中有两相或三相介质(油、 水、 气) 时, 条件可放宽为:气相总压≥1. 8MPa 且 H2S 分压≥0. 0003MPa;当气相压力≤1. 8MPa 且 H2S 分压≥0. 07MPa;或气相 H2S 含量超过 15%。
(2) 国内湿硫化氢环境的定义
“在同时存在水和硫化氢的环境中, 当硫化氢分压大于或等于 0. 00035 MPa 时, 或在同时存在水和硫化氢的液化石油气中, 当液相的硫化氢含量大于或等于 10×10-6 时, 则称为湿硫化氢环境” 。
(3) 硫化氢的电离
在湿硫化氢环境中, 硫化氢会发生电离, 使水具有酸性, 硫化氢在水中的离解反应式为:
H2S = H+ + HS- (1)
HS- = H+ + S2- (2)
2. 硫化氢电化学腐蚀过程
阳极:Fe - 2e → Fe2+
阴极:2H+ + 2e → Had + Had → 2H → H2↑↓[H] → 钢中扩散
其中:Had - 钢表面吸附的氢原子[H] - 钢中的扩散氢
阳极反应产物:Fe2+ + S2- → FeS ↓
注:钢材受到硫化氢腐蚀以后阳极的最终产物就是硫化亚铁, 该产物通常是一种有缺陷的结构, 它与钢铁表面的粘结力差, 易脱落, 易氧化, 且电位较正, 因而作为阴极与钢铁基体构成一个活性的微电池, 对钢基体继续进行腐蚀。
4.硫化氢腐蚀的影响因素
1.材料因素
在油气田开发过程中钻柱可能发生的腐蚀类型中,以硫化氢腐蚀时材料因素的影响作用最为显著,材料因素中影响钢材抗硫化氢应力腐蚀性能的主要有材料的显微组织、强度、硬度以及合金元素等等。
1)显微组织
对应力腐蚀开裂敏感性按下述顺序升高:
铁素体中球状碳化物组织→完全淬火和回火组织→正火和回火组织→正火后组织→淬火后未回火的马氏体组织。
注:马氏体对硫化氢应力腐蚀开裂和氢致开裂非常敏感,但在其含量较少时,敏感性相对较小,随着含量的增多,敏感性增大。
2) 强度和硬度
随屈服强度的升高,临界应力和屈服强度的比值下降,即应力腐蚀敏感性增加。
材料硬度的提高,对硫化物应力腐蚀的敏感性提高。材料的断裂大多出现在硬度大于HRC22(相当于HB200)的情况下,因此,通常HRC22可作为判断钻柱材料是否适合于含硫油气井钻探的标准。
油气开采及加工工业对不昂贵的、可焊性好的钢材的需要,基本上决定了研究的工作方向就是优先研制抗硫化物腐蚀开裂的低合金高强度钢。
3)合金元素及热处理
有害元素:Ni、Mn、S、P; 有利元素:Cr、Ti
碳(C):增加钢中碳的含量,会提高钢在硫化物中的应力腐蚀破裂的敏感性。
镍(Ni):提高低合金钢的镍含量,会降低它在含硫化氢溶液中对应力腐蚀开裂的抵抗力。原因是镍含量的增加,可能形成马氏体相。所以镍在钢中的含量,即使其硬度HRC<22时, 也不应该超过1%。
铬(Cr):一般认为在含硫化氢溶液中使用的钢,含铬0.5%~13%是完全可行的,因为它们在热处理后可得到稳定的组织。
钼(Mo):钼含量≤3%时,对钢在硫化氢介质中的承载能力的影响不大。
钛(Ti):钛对低合金钢应力腐蚀开裂敏感性的影响也类似于钼。试验证明,在硫化氢介质中,含碳量低的钢(0.04%)加入钛(0.09%Ti),对其稳定性有一定的改善作用。
锰(Mn):锰元素是一种易偏析的元素,研究锰在硫化物腐蚀开裂过程的作用十分重要。当偏析区Mn、C含量一旦达到一定比例时,在钢材生产和设备焊接过程中,产生出马氏体/贝氏体高强度、低韧性的显微组织,表现出很高的硬度,对设备抗SSCC是不利的。
硫(S):硫对钢的应力腐蚀开裂稳定性是有害的。随着硫含量的增加,钢的稳定性急剧恶化,主要原因是硫化物夹杂是氢的积聚点,使金属形成有缺陷的组织。同时硫也是吸附氢的促进剂。因此,非金属夹杂物尤其是硫化物含量的降低、分散化以及球化均可以提高钢(特别是高强度钢)在引起金属增氢介质中的稳定性。
磷(P):除了形成可引起钢红脆(热脆)和塑性降低的易熔共晶夹杂物外,还对氢原子重新组合过程起抑制作用,使金属增氢效果增加,从而也就会降低钢在酸性的、含硫化氢介质中的稳定性。
4) 冷加工
经冷轧制、冷锻、冷弯或其他制造工艺以及机械咬伤等产生的冷变形,不仅使冷变形区的硬度增大,而且还产生一个很大的残余应力,有时可高达钢材的屈服强度,从而导致对SSCC敏感。一般说来钢材随着冷加工量的增加,硬度增大,SSCC的敏感性增强。
2. 环境因素的影响
1) 硫化氢浓度
从对钢材阳极过程产物的形成来看,硫化氢浓度越高,钢材的失重速度也越快。
高强度钢即使在溶液中硫化氢浓度很低(体积分数为1×10-3mL/L)的情况下仍能引起破坏,硫化氢体积分数为5×10-2~6×10-1 mL/L时,能在很短的时间内引起高强度钢的硫化物应力腐蚀破坏,但这时硫化氢的浓度对高强度钢的破坏时间已经没有明显的影响了。硫化物应力腐蚀的下限浓度值与使用材料的强度(硬度)有关。
2)pH值对硫化物应力腐蚀的影响:
随pH的增加,钢材发生硫化物应力腐蚀的敏感性下降。pH≤6时,硫化物应力腐蚀很严重;6<pH≤9时,硫化物应力腐蚀敏感性开始显著下降,但达到断裂所需的时间仍然很短;pH>9时,就很少发生硫化物应力腐蚀破坏。
3)温度
在一定温度范围内,温度升高,硫化物应力腐蚀破裂倾向减小。在22℃左右,硫化物应力腐蚀敏感性最大。温度大于22℃后,温度升高硫化物应力腐蚀敏感性明显降低。
4)流速
流体在某特定的流速下,碳钢和低合金钢在含H2S流体中的腐蚀速率,通常是随着时间的增长而逐渐下降,平衡后的腐蚀速率均很低。
如果流体流速较高或处于湍流状态时,由于钢铁表面上的硫化铁腐蚀产物膜受到流体的冲刷而被破坏或粘附不牢固,钢铁将一直以初始的高速腐蚀,从而使设备、管线、构件很快受到腐蚀破坏。因此,要控制流速的上限,以把冲刷腐蚀降到最小。通常规定阀门的气体流速低于15m/s。相反,如果气体流速太低,可造成管线、设备低部集液,而发生因水线腐蚀、垢下腐蚀等导致的局部腐蚀破坏。因此,通常规定气体的流速应大于3m/s。
5)氯离子
在酸性油气田水中,带负电荷的氯离子,基于电价平衡,它总是争先吸附到钢铁的表面,因此,氯离子的存在往往会阻碍保护性的硫化铁膜在钢铁表面的形成。但氯离子可以通过钢铁表面硫化铁膜的细孔和缺陷渗入其膜内,使膜发生显微开裂,于是形成孔蚀核。由于氯离子的不断移入,在闭塞电池的作用下,加速了孔蚀破坏。在酸性天然气气井中与矿化水接触的油套管腐蚀严重,穿孔速率快,与氯离子的作用有着十分密切的关系。
5. 硫化氢引起氢损伤的腐蚀类型
抗H2S腐蚀钢材的基本要求:
1)成分设计合理:材料的抗H2S应力断裂性能主要与材料的晶界强度有关,因此常常加入Cr、Mo、Nb、Ti、Cu等合金元素细化原始奥氏体晶粒度。超细晶粒原始奥氏体经淬火后,形成超细晶粒铁素体和分布良好的超细碳化物组织,是开发抗硫化物应力腐蚀的高强度钢最有效的途径。
2)采用有害元素(包括氢, 氧, 氮等)含量很低纯净钢;
3)良好的淬透性和均匀细小的回火组织,硬度波动尽可能小;
4)回火稳定性好,回火温度高(>600℃);
5)良好的韧性;
6)消除残余拉应力。
免责声明:本网站所转载的文字、图片与视频资料版权归原创作者所有,如果涉及侵权,请第一时间联系本网删除。
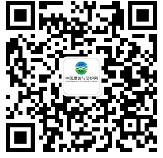
官方微信
《腐蚀与防护网电子期刊》征订启事
- 投稿联系:编辑部
- 电话:010-62316606
- 邮箱:fsfhzy666@163.com
- 腐蚀与防护网官方QQ群:140808414