非金属材料的腐蚀
在环境介质的作用下,非金属材料性能发生蜕化,甚至完全丧失使用功能的现象,称为非金属材料的腐蚀。
非金属材料与金属材料有着不同的组成和结构,因此,腐蚀原理也有着本质的区别。非金属材料(除石墨材料)的导电性很差或完全不导电,或电化学稳定强,即使将其置于电解质溶液中,也不会发生电化学腐蚀。非金属材料的腐蚀主要由物理作用和化学作用引起。
01
有机非金属(高分子)材料
有机非金属(高分子)材料腐蚀主要是物理的或化学的作用,主要腐蚀机理有:
① 物理腐蚀
高分子材料的物理腐蚀是其在介质中的溶解,整个溶解过程为溶胀和溶解两个阶段。溶胀和溶解过程与高分子材料的结构(晶态或非晶态)、分子排列(是线性还是网状)有密切关系。介质向材料内部渗透扩散,材料中的某些成分,如增塑剂、稳定剂等添加剂或相对低分子质量组分也会向介质迁移。腐蚀介质通过材料表面渗入内部,就会使质量增加,材料中的可溶成分及腐蚀产物逆向扩散进入介质中使质量减少。当材料的溶出量小于介质渗入量是腐蚀试验表现为正的质量变化率,即质量增加。相反,当材料中的逆向扩散出来的质量超过介质渗入量时,表现为负的质量变化率,即质量损失。
在有机非金属高分子材料耐蚀性能评定中经常测定的浸渍质量增加率,实质是介质向材料内部渗透扩散与材料组成物、腐蚀产物逆向溶出的总的表现。若仅用质量增加率做标准来评定腐蚀程度的话,可能得出错误结论,因为当吸收介质增加的质量与溶出而减少的质量均很大,但差值却很小时,材料虽然已完全损坏,但总质量增加率却不大。渗透是指由浓度差引起的扩散过程,无论材料成分的溶出或是介质的渗入均与渗透扩散性有关,只是溶出是在腐蚀性介质渗入有机非金属材料内部并与其发生作用后造成的。
物理腐蚀的影响因素有:
a.相似形相溶,溶剂和高分子材料的化学结构越相似,如极性相近等,溶解的可能性越大;
b.非晶态材料结构松散,容易溶解;晶态材料结构紧密,分子间作用力强,不容易溶解;相对线性非晶态材料来说,分子质量增大,温度降低,溶解减缓。
② 化学腐蚀
化学腐蚀是指发生不可逆化学反应所导致的腐蚀,它往往是氧化、水解、取代和交联等反应的综合结果。作用机理是因高分子材料的大分子中一些具有一定活性的极性基团,这些极性基团与特定的介质发生化学反应,导致了材料性能的改变,从而造成材料的老化或者裂解破坏。
有机高分子材料的化学腐蚀可分为两类,一类是高分子材料在酸、碱、盐等介质中的水解反应,另一类是在空气中由于氧、臭氧等作用而发生的氧化反应,此外还有侧基的取代反应和交联反应均属化学腐蚀。
a.水解反应。高分子链中的O、N、Si等原子,它们与C之间构成极性键,如醚键、酯键、酰胺键等,水能与这些键发生作用,如:聚酯的水解反应,聚酯的碳氧键和聚酰胺的碳氧键水解后,生成相应的缩聚单体,而且碱能使酯发生皂化反应形成盐。因此,不饱和聚酯不太耐酸、更不耐碱,聚酰胺在酸的作用下因形成铵盐而被迅速破坏,但是它宜用做耐油或烃类溶剂的防腐材料;
b.氧化反应。大气中的氧、臭氧、污染物(NO2、SO2等)在一定的环境条件下使高聚物发生化学反应而破坏。如,高分子材料(天然橡胶和聚烯烃高聚物等),在辐射或紫外线等外界因素作用下,能发生高分子氧化反应;一些氧化剂如浓HNO3和H2SO4等,也会使高聚物分子发生氧化。一般认为,氧化过程分两步进行,第一步是氢过氧化物的形成(初级反应),第二步是氢过氧化物的分解产生多种分解产物(次级反应)。其原因是在高聚物大分子链上存在有键能较低的与叔碳原子相连的或与双键α位碳原子相连的C-H键;
c.降解。高聚物的降解过程就是相对分子量下降的过程,分为表面腐蚀(体积变小)、本体腐蚀(几何形状保持不变)。特征为:形态的变化,最初材料表面粗糙,慢慢地变成了多孔结构;腐蚀过程中齐聚物和单体的产生。
降解的途径分为光照、热、机械、化学降解,热降解对非生物降解高分子材料起主要作用。所有生物降解高分子材料都含有可水解的键。光降解实质是光氧化降解,取决于分子链所吸收波长的能量和化学键的强度,紫外光能量一般高于引起高分子链上化学键断裂所需要的能量。
降解的影响因素有,共聚物成分,其化学键活性对降解影响较大,酐和原酸酯键的水解反应速率最快,其次是酯和酰胺键;pH值通过催化作用影响反应速率;由于水解作用是水和不稳定功能基团间的双分子反应,因此亲水性的高聚物降解速率大;
d.取代基的反应。饱和的碳基化合物化学稳定性较高,但在加热及光照下,除被氧化外,还能被氯化。氯化是放热反应,随着含氯量的增加生成物的大分子间的作用力增强,结晶性改善,在溶剂中的溶解能力会大大提高;
e.交联反应。有些高聚物受日光或环境作用,相邻间会发生交联反应而使材料硬化变脆。例如聚乙烯薄膜在长期太阳光照下硬化;软聚氯乙烯在使用过程中变硬发脆;硬聚氯乙烯(特别是加有ZnO填料时)长期在阳光下暴晒性能变脆等。将聚苯硫醚320~360℃空气中进行热处理后,可以使具有脆性的线性结晶结构发生氧化交联,成为低结晶度网状结构而提高其力学性能及韧性。
③ 应力腐蚀开裂
a.环境应力开裂。在应力与某些介质(如表面活性剂)共同作用下,不少高分子材料会出现银纹,进一步长成裂纹,直至发生脆性断裂,其断裂应力比在惰性环境中低的多,这种现象称为环境应力开裂。按应力腐蚀开裂机理与种类可分为环境应力腐蚀开裂、溶剂开裂和氧化应力开裂。
有些聚合物,尤其是玻璃态透明聚合物如聚苯乙烯、有机玻璃、聚碳酸酯等,在存储及使用过程中,由于应力和环境因素的影响,表面往往会出现一些微裂纹。有这些裂纹的平面能强烈反射可见光,形成银色的闪光,故称为银纹,相应的开裂现象称为银纹化现象。
环境应力开裂的类型的介质可分为表面活性物质、溶剂型物质、强氧化性介质。有机高分子材料与醇类和非离子型表面活性剂等表面活性介质相接触时,不会产生很大的溶胀,而是通过局部表面渗入产生塑性增加的作用,使其在较低的应力作用下产生较多银纹,而使得应力集中又加剧了银纹的生长。因此,银纹的产生、生长、扩大直至汇合发生脆性断裂是典型的环境应力腐蚀开裂过程。
环境应力包括外加负载材料在加工、使用时残留于材料中的内应力。
环境应力开裂的主要理论有:表面能(ΔS)降低理论、附着功(W)理论、自由能变化值(ΔG)理论等,其中自由能变化值理论是最具有说服力的机理。在有机高分子材料表面层的某些部位,因局部的增塑作用及应力作用而产生裂纹,被公认是环境应力开裂的诱因;
b.溶剂开裂。有机高分子材料与溶解度参数相近的溶剂介质相接触时(参数太接近,溶剂化能力太强情况下,环境应力开裂也不典型),溶剂分子进入大分子之间就有了增塑作用,使得大分子链段易于相对滑移,材料强度下降,在较低的内应力作用下可发生应力开裂,称之为溶剂开裂。这种开裂之前产生的裂纹不多;
c.氧化应力开裂。当有机高分子材料与强氧化剂性介质如浓H2SO4、浓HNO3等接触时,会在材料表面发生氧化反应,使大分子链发生裂解,在应力作用下会在少数薄弱环节处产生银纹,银纹中的空隙又进一步加快了介质的渗入,最后在其银纹尖端应力集中比较大的地方,使大分子断链,形成开裂。这类开裂发生只是形成少数微裂纹,然后迅速发展而造成开裂,称为氧化应力开裂;
d.应力腐蚀开裂的影响因素。高分子材料的性质是最主要的影响环境应力开裂的因素。不同的高聚物具有不同的耐环境应力开裂的能力,即使是同一高聚物,也会因其相对分子质量、结晶度、内应力的差别而有很大的不同。相对分子量小、分布窄的材料因分子间解缠溶解而使开裂所需时间短;结晶度高容易产生应力集中,且在晶区和非晶区的过渡交界处容易受到介质作用,因此易于应力开裂。
聚乙烯的溶剂开裂比较严重,常影响到它在化工介质中的实际应用性能,所以在无应力时的浸渍数据不一定能反映真实的情况,用于含表面活性介质时更要注意。
聚合物的结晶度高,易产生应力集中。同时,晶区与非晶区的交界处同样易受到试剂的作用,所以有着能更快出现裂缝的趋势。此外结晶的大小与分布也影响应力腐蚀开裂。
材料中的缺陷、杂质、粘结不良的界面、表面刻痕及微裂等应力集中体,同样也会促进环境应力开裂。
加工不良引起的内应力,或者材料由于热处理条件不同产生的内应力,对环境应力开裂均有很大的影响。
相对分子质量的影响更大。相对分子质量小而相对分子质量分布窄的材料,发生开裂所需时间不长。因为相对分子质量越大,在介质作用下的解缠就越不容易。
环境和介质的影响包括介质的类型和介质的极性。
环境介质的性质,主要决定于材料与介质间的相对表面性质或溶度参数差值。
介质的类型。介质有助于裂纹的产生,这种现象有人用表面能降低的理论来解释。由断裂强度理论可知,裂纹尖端的应力大于裂纹扩展的临界应力时,裂纹才能扩展。介质中的表面活性物质与高分子材料接触时,其表面能会下降,因此产生新的表面所需的能量或临界应力可以减小。当临界应力小于外加应力或材料内部残余的内应力时,裂纹扩展,引起开裂。
介质的极性,介质对环境应力开裂的影响,还可以用它与材料间的相对表面性质或溶解度参数的差值来衡量。若介质与材料的溶解度参数很接近,即浸润性好,则易溶胀,不是典型的环境应力开裂剂。如果介质与材料的溶解度参数之差Δδ太大,材料就不会被介质所浸润,介质的影响也就变小。
应力的影响。应力包括拉伸应力和交变应力。材料必须受拉伸应力的作用是其银纹产生及发展的必要条件,其发展方向与拉伸方向相互垂直。重要条件是材料的应变应该超过其临界应变值εc。临界应变值是热塑性高聚物在特定介质中长期静拉伸或动拉伸应变作用下形变的极限值。同时εc的大小反映了高聚物在特定的应力条件下发生环境应力开裂的难易程度,也表征了各种聚合物允许使用的形变极限。由实验数据可知,聚碳酸酯和聚砜比聚丙烯酸酯更容易产生环境应力开裂,见表2-6。同时,同一种材料在空气中比在介质中的εc高,这是由于化学介质对材料有侵蚀增塑作用,促进了环境应力腐蚀开裂。
大量试验表明,将没有预先浸渍过的硬聚氯乙烯,在介质浸渍状态下测定长期强度,介质的影响很大。若以在空气中的长期强度为标准,则在介质中测得的都要比它小,而且介质腐蚀性越大,强度下降越多。应注意的是介质腐蚀能力的影响,不如材料的方向性(即大分子取向)影响大。另外硬聚氯乙烯在浓H2SO4与应力作用下试件出现银纹,随着时间的增加微细裂纹增多。由于H2SO4侵入裂纹及分子之间使之炭化,材料逐渐呈现黑色;裂纹进一步增多与扩大,就使材料出现脆性或接近脆性的断裂。
此外,在负荷作用下或处于应变状态下的高分子材料,其大分子链及链段将沿外力作用方向移动。若为拉伸应力,分了间距增大,这时介质分子易于侵入,质量变化比无负荷的静态浸渍时大。而压应力与拉应力的效果相反。
交变应力。橡胶、塑料具有因低频交变应力使寿命变短的倾向,而介质的存在使疲劳寿命下降得更严重。在实际应用中,应考虑交变应力对在介质中的高分子材料耐腐蚀性能的影响。实验证明,在水与某些表面活性剂中,高的应力振幅对疲劳破坏与蠕变破坏的影响没有多大差别,但在低的应力振幅下,则疲劳破坏强度比静态蠕变强度低得多。在腐蚀性较强的介质中,材料疲劳强度下降得多。水对玻璃钢的疲劳强度影响很大,硝酸、碱与非离子型表面活性剂对聚氯乙烯的影响,明显地比水大。
④ 大气老化
大气老化主要发生在有机高分子材料上,虽然无机材料也存在风化的大气老化问题,但是由于风化速度太慢,所以大气老化主要是针对高分子材料而言。高分子材料在大气环境中发生老化,通常以2种形式表现出来,一种是物理老化,另一种是化学老化。
a.物理老化。玻璃态高聚物多数处于平衡状态,其凝聚态结构是不稳定的。这种不稳定结构在玻璃化转变温度以下在存放过程中会逐渐趋向稳定的平衡状态,从而引起高聚物材料的物理力学性能随存放或使用时间而变化,这种现象被称为物理老化或“存放效应”。物理老化是玻璃态高聚物通过小区域链段的微布朗运动使其凝聚态结构从非平衡态向平衡态过渡的弛豫过程,因此与存放的温度有关。
物理老化使高聚物材料自由体积减小,堆砌密度增加,反映在宏观物理力学性能上是弹性模量和抗张强度增加,断裂伸长及冲击韧性下降,材料由延性转变为脆性,从而导致材料在低应力水平下的失效破坏;
b.化学老化。化学老化通常是高分子材料在大气环境中,受阳光的紫外线、热辐射、空气中温度、湿度、水分、氧等因素作用,性能随时间的延续而劣化的腐蚀现象。
影响老化的因素有紫外线、温度、湿气、活性气体及其他化学物质、辐射等。
02
无机非金属材料的腐蚀原理
无机非金属材料是指除有机高分子材料和金属材料以外的固体材料,其中多数为硅酸盐材料。所谓硅酸盐材料即指硅和氧组成的天然岩石、铸石、陶瓷、搪瓷、玻璃、水泥等。
① 无机非金属材料的物理腐蚀。无机硅酸盐材料其物理腐蚀主要表现在硅酸盐水泥材料中。硅酸盐水泥硬化以后,在通常使用条件下,一般可以有较好的耐久性。影响耐久性的因素很多,但抗渗性、抗冻性以及对环境介质的抗蚀性,是衡量硅酸盐水泥耐久性的3个主要方面。硅酸盐水泥材料的腐蚀有两种分类方法,其一是按腐蚀形态分类,可分为溶出型腐蚀和膨胀型腐蚀(或称结晶型腐蚀)。
a.溶出型腐蚀。溶出型腐蚀主要是由于硬化水泥石中的Ca(OH)2被溶解和洗出造成的。硅酸盐水泥属于典型的水硬性胶凝材料,本身具备一定的抗水能力。硬水含有Ca(HCO3)2 或Mg(HCO3)2,能把硬化水泥石中的Ca(OH)2变为CaCO3沉淀下来,形成的碳酸盐薄膜使硬化水泥石密实,所以普通的降水、河水、湖水或地下水等硬水对水泥石不构成严重问题。而软水不但能溶解Ca(OH)2,而且还能溶解硬化水泥石表面已形成的碳酸盐薄膜,因此能对硬化水泥石构成严重腐蚀。当混凝土中的CaO损失达33%时,混凝土就会被破坏。溶出型腐蚀的速度主要受水的冲洗条件、硬化水泥表面水体的更换条件,水体的压力、水体中含影响Ca(OH)2溶解度的物质数量等因素的影响;
b.膨胀型腐蚀。膨胀型腐蚀有2种类型,一种反应性产物膨胀,是渗入到硬化水泥石孔隙内部后的某些盐类溶液如果再经干燥后,盐溶液发生过饱和,并且在孔隙中结晶长大,产生一定的膨胀应力,导致材料的破坏;另一种情形是盐类结晶膨胀,即渗入到硬化水泥石孔隙内部发生化学反应生成膨胀性产物,使硬化水泥石孔隙内产生内应力,开始时仅只产生内应力,并无明显破坏迹象,但随着反应的继续进行,膨胀产物增多,体积膨胀,内应力增强,逐渐会使硬化水泥石开裂、剥落,直至严重破坏。
② 无机非金属材料的化学腐蚀。硅酸盐材料成分中以酸性氧化物SiO2为主,耐酸不耐碱,当SiO2(尤其是无定型SiO2)与碱液接触时发生如下反应受到腐蚀:
SiO2 + 2NaOH = Na2SiO3 + H2O
所生成的硅酸钠易溶于水及碱液中。
SiO2含量较高的耐酸材料,除HF和高温H3PO4外,能耐所有无机酸的腐蚀。温度高于300℃的H3PO4,任何浓度HF都会对SiO2发生作用:
SiO2 + 4HF = SiF4 + 2H2O
SiF4 + 2HF = H2SiF6
H3PO4 = HPO3 + H2O
2HPO3 = P2O5 + H2O
SiO2 + P2O5 = SiP2O7
一般来说,材料中的SiO2含量越高耐酸性越强,SiO2质量分数低于55%的天然及人造硅酸盐材料是不耐酸的,但也有例外,例如铸石中只含有质量分数为55%左右的SiO2,而其耐酸性却很好,红砖中的SiO2含量很高,质量分数达60%~80%,却没有耐酸性。由此可见,硅酸盐材料的耐酸性,不仅决定于化学组成,而且还决定于其矿物组成。含有大量的碱性氧化物(CaO、MgO)的材料属于耐碱材料。它们与耐酸材料相反,完全不能抵抗酸类的无机酸腐蚀,而在一般的碱液(浓的烧碱液除外)中都是耐蚀的。
玻璃的腐蚀主要有大气对玻璃的侵蚀和风化,大气侵蚀的实质是H2O(气)、CO2、SO2等作用的总和,水汽比水溶液具有更大的侵蚀性。因为它与玻璃主要发生离子交换的释碱反应,其产物不断的沉积在原来部位,使pH增大。风化是玻璃和大气长期作用,在表面出现雾状的薄膜或点片状白斑、细线状模糊物、彩虹等过程,风化过程分为溶解和水解浸析两种形式,大气中酸性气体、不通风的高温高湿环境,加速风化。在水、甲醇、甲酰胺等介质和静态拉应力下,玻璃会产生应力腐蚀。
陶瓷材料的玻璃相的腐蚀与玻璃类似,主相(晶体相)有其自身的特点。水介质中的腐蚀,晶体相的能量状态较玻璃相低,化学稳定性和耐腐蚀性通常也较玻璃相好。气体中最普遍的腐蚀是氧化,水蒸气可以加快陶瓷材料的氧化进程,会造成比液体更为严重的腐蚀。熔融玻璃、熔融盐、熔融金属等均可造成晶体陶瓷材料的腐蚀溶解。
③ 影响无机非金属材料腐蚀因素。常见的无机非金属材料基本上是硅酸盐材料,主要由硅、氧原子组成,常以硅酸盐和硅酸石(SiO2)存在。其耐蚀性能主要与氧化物的类型与含量、材料孔隙与结构、材料结构和腐蚀介质有关。
a.氧化物的类型与含量。无机非金属材料的主要成分SiO2为酸性氧化物,耐酸(HF、高温浓H3PO4除外),但不耐碱。在硅酸盐材料中SiO2含量越高,耐酸性能越强。另一种情况是当SiO2质量分数低于55%时,硅酸盐材料的耐酸性能却仍然很好,这是因为硅酸盐材料的耐酸性不仅与化学组成有关,而且与矿物组成及孔隙率有关。在高温下,铸石中的SiO2与Al2O3、Fe2O3生成耐蚀性很强的普通灰石矿物。另外,硅酸盐的熔融制品如玻璃、铸石等孔隙率很低,材料内部因介质难于渗入,不会发生化学溶解腐蚀,仅发生表面腐蚀,耐蚀性也较好。在硅酸盐材料中,碱性氧化物如CaO、MgO等,含量高时,耐酸性差,而耐碱性则会增强。碱性金属氧化物中,以K2O对化学稳定性影响最大,其次为Na2O和Li2O。硅酸盐水泥与浓碱、HF、热H3PO4易发生化学溶解腐蚀。与pH <7的酸溶液及镁溶液接触时易发生水解型腐蚀,即水泥中OH-与酸中的H+结合为水,Ca2+与溶液中的Mg2+相互交换,生成可溶性或无胶结性产物使水泥分解。另外,酸溶液还与水泥中的铝酸钙水化物和硅酸盐水化物反应,导致水泥腐蚀;
b.材料孔隙与结构。硅酸盐材料除玻璃、铸石等熔融制品外,或多或少总具有一定的孔隙率,孔隙会降低材料的耐蚀性,因为孔隙的存在会使材料受腐蚀介质作用的面积增大,使腐蚀不仅发生在表面上,也发生在材料内部,侵蚀作用也就显得强烈。当化学反应生成物出现结晶时还会造成物理性的破坏,例如制碱车间的水泥地面,当间歇地受到苛性钠溶液的浸润时,由于渗透到孔隙中的苛性钠吸收CO2后变成含水碳酸盐结晶,体积增大,在水泥内部膨胀,使材料产生内应力而破坏。如果在材料表面及孔隙中腐蚀生成的化合物为不溶性的,则在某些场合它们能保护材料不再受到破坏,水玻璃耐酸胶泥的酸化处理就是一例。当孔隙是互不相通而封闭时,受腐蚀性介质的影响要比开口的孔隙小。因为当孔隙为开口时,腐蚀性液体容易渗入材料内部。
c.材料结构。硅酸盐材料的耐蚀性还与其结构有关,晶体结构的化学稳定性较无定型结构高。例如结晶的SiO2虽属耐酸材料,但也有一定的耐碱性,而无定型的SiO2易溶解于碱溶液中。具有晶体结构的熔铸辉绿岩也是如此,它比同一组的无定型化合物具有更高的化学稳定性;
d.腐蚀介质。硅酸盐材料的腐蚀速率与酸的性质无关(除HF和高温H3PO4外),而与酸的浓度有关,酸的电离度越大,对材料的破坏作用也越大,酸的温度升高,离解度增大,其破坏作用也就增强。此外酸的粘度会影响他们通过孔隙向材料内部扩散的速度。例如HCl比同一浓度的H2SO4粘度小,同一时间渗入材料的深度就大,其腐蚀作用也就较H2SO4快,同样同一种酸的浓度不同,其粘度也不同,因而它对材料的腐蚀速率也不同。
03
复合材料的腐蚀
复合材料连续相称为基体,分散相(如纤维、颗粒状填料等)称为增强材料。
① 非金属基复合材料的腐蚀主要有:
a.腐蚀介质对树脂基体的影响,包括物理侵蚀和化学反应;
b.对增强纤维的影响,通过气泡、微裂纹、沿界面的渗入,纤维/树脂脱粘;
c.对复合材料界面的影响,介质聚集,溶胀产生拉应力,从界面析出可溶性物质,产生渗透压和化学反应。
② 金属基复合材料的腐蚀
它的耐蚀性一般比金属基体差,原因为:
a.合金元素在增强物/基体界面处偏析;
b.围绕增强物产生残余应力;
c.在增强物周围基体中位错密度高;
d.增强物/基体界面处产生空洞;
e.由于制备过程中基体金属与增强材料发生反应而导致活性界面层;
f.界面层的电偶效应
铝基复合材料,碳/铝复合材料易发生电偶腐蚀,这是由于碳纤维具有导电性,其在电解质中的电位也较高;碳化硅/铝复合材料的耐蚀性与基体相比,降低不多。
铜基复合材料,在海水中的耐蚀性与相应的基体差不多,腐蚀产物膜的成分是Cu2(OH)3Cl。
在增强相表面上施加涂层,化学保护膜(铬酸转化膜)、硫酸阳极保护膜、有机涂层、激光表面处理(熔覆一层合金)、热喷涂、包铝和添加缓蚀剂等,除了可以改善界面间的润湿性、减少界面反应,释放热应力外,还可以减少电偶腐蚀。
g.热处理,退火消除残余应力等。
免责声明:本网站所转载的文字、图片与视频资料版权归原创作者所有,如果涉及侵权,请第一时间联系本网删除。
相关文章
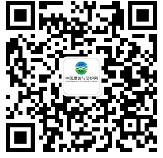
官方微信
《中国腐蚀与防护网电子期刊》征订启事
- 投稿联系:编辑部
- 电话:010-62316606-806
- 邮箱:fsfhzy666@163.com
- 中国腐蚀与防护网官方QQ群:140808414
点击排行
PPT新闻
“海洋金属”——钛合金在舰船的
点击数:7130
腐蚀与“海上丝绸之路”
点击数:5741