永磁材料是一种不需要消耗电能就可以持续提供磁能的物体,它具有能量转换的功能,是重要的功能材料。汝铁硼NdFeB永磁体以其极高的“磁能积”轰动于世,由于其优异的磁性而被称为“磁王”,是目前世界上最强的永磁体。
什么是磁性材料?
磁性材料是一种生活中非常重要的功能性材料,可分为一般永磁材料和稀土永磁材料。它的应用十分广泛,无论是国防军工、能源产业、信息通讯、汽车工业还是电机工程领域,都能见到它的身影。其中,稀土永磁材料由于其高性能,发展得十分迅猛,电子器件朝着小型化发展的趋势,在一定程度上也推动了它的发展。
磁性材料发展简史
1、钴钢:1930年,人类最早制造的磁石材料,磁性虽然比天然磁石强了许多,但仍旧是低性能永磁材料。
2、Alnico铸造永磁:后来人们利用Al、Ni、Co和Fe按比例配制成更强的永磁材料,Br可达12000~13000高斯,(BH)m可达5~10MGOe,Hc为500~600Oe。
3、恒磁铁氧体:20世纪50年代利用氧化铁粉研制成功金属陶瓷永磁材料,一般Br为3000~4000Gs,(BH)m为3.0~5.0 MGOe,Hc为1500~3000Oe。由于是氧化铁粉,所以成本较低,价格便宜。
4、稀土钴永磁(第一代):在20世纪70年代前后研制成功稀土钴永磁,Br可达0.9~11.0KGs,(BH)m为18~20MGOe,Hcj可达30K以上。是第一代稀土永磁。主要是SmCo5,SmPrCo5等牌号。
5、稀土钴永磁(第二代):到20世纪70年代末又研制成功Sm2(Co,Cu,Fe,Zr)17型稀土钴永磁,(BH)m可达30MGOe,常称第二代稀土永磁。
6、钕铁硼永磁(第三代):到20世纪80年代末又研制成功迄今为止世界上最强的磁体,钕铁硼(Nd-Fe-B)永磁材料,Br为12000~15000Gs,(BH)m可达40~50MGOe,Hc12.0~30KOe,称为第三代稀土永磁。
谁是“磁王”?
第三代稀土永磁材料钕铁硼是当代磁铁中性能最强的永磁铁,由于其优异的磁性能而被称为“磁王”。
它的BHmax值是铁氧体磁铁的5~12倍,是铝镍钴磁铁的3~10倍;它的矫顽力相当于铁氧体磁铁的5~10倍,铝镍钴磁铁的5~15倍;其潜在的磁性能极高,能吸起相当于自身重量640倍的重物。
“磁王”钕铁硼
钕铁硼是一种由稀土金属钕、金属元素铁、非金属元素硼以及少量添加元素镨、镝、 铌、 铝、镓、铜等元素组成的稀土永磁化合物,简单来讲是一种磁铁,又称磁钢。钕铁硼永磁体磁性能优良,质轻价廉,应用范围广泛,是迄今为止性价比最高的磁体材料。
钕铁硼拥有极高的磁性能其最大磁能积,其本身的机械加工性能亦相当之好,而且其质地坚硬,性能稳定,有很好的性价比,故其应用极其广泛。
但因为其化学活性很强,所以必须对其表面凃层处理(如镀Zn、Ni、电泳、钝化等)。
其温度性能不佳,在高温下使用磁损失较大,最高工作温度较低。一般为80℃左右,在经过特殊处理的磁铁,其最高工作温度才可达200℃。
一、NdFeB的相组成
材料的基本组成影响材料的性能,烧结钕铁硼永磁体主要采用粉末冶金法进行生产,它至少同时存在以下4种不同的相:
① 基体相(主相):Nd2Fe14B相。它是在1200℃左右通过包晶反应形成的,是合金中唯一的磁性相。NdFeB磁体的优异的磁性能主要归功于Nd2Fe14B相的高饱和磁化强度(μMs=1.6T)和各向异性场(7.3T)。
② 富Nd相:其熔点为650~700℃,是合金中最后凝固的,以薄层状和块状存在,分布在晶界的交隅处或Nd2Fe14B的晶界上。它虽然是非磁性相,但由于其低熔点特性,在烧结时弥散分布于主相周围,不但起到使烧结体致密化的作用,还使晶粒长大受到抑制,促进矫顽力提高,因此是必不可少的。
③ 富B相Nd1+εFe4B4:当合金中硼含量超过Nd2Fe14B的正常成分时才形成,它对磁性能没有贡献,一般数量极小,对磁性能影响不大。
④ α-Fe∶其熔点为1520℃,是合金中熔点最高的相,最先从液态合金中析出,a-Fe是软磁相,它的存在导致了主相的减少和富钕相的增加,破坏了主相和富钕相的最佳配比,损害了主相晶粒的磁取向,同时还使烧结过程中局部区域的晶粒粗化,不仅使磁性能恶化,也使电镀层组织变坏,影响防护作用。因此,从制造工艺上采取措施尽量减少或清除α-Fe相的产生,如片铸工艺和快淬工艺等。
二、钕铁硼的分类
由于制造方法和使用要求不同,NdFeB永磁可分为三大类:
(1)粘结型NdFeB(Bonded NdFeB):NdFeB粘结磁体是用激冷的方法获得微晶粉末,每个粉末内含有多个Nd-Fe-B微晶晶粒,再用聚合物或其它粘结剂将粉末混粘结合后压制,挤压或压延而成塑料状永磁体,因而通常的NdFeB粘结磁体是非致密的各向同性磁体。
通常的NdFeB粘结磁体的磁性能远低于NdFeB烧结磁体,但NdFeB粘结磁体有着许多NdFeB烧结磁体不可替代的优点:加工精度高、成材率高、精密度高、磁性能极佳、耐腐蚀性好、温度稳定性好;另外,Nd-Fe-B粘结磁体还便于任意方向充磁,能方便制作多极乃至无数极的整体磁体。
(2)烧结型NdFeB(Sintered NdFeB):烧结型NdFeB永磁体是通过粉末冶金法而制成的,主要工序为:合金化(熔炼)→粗破碎→细碎→研磨成3~5.0?m细粉→磁场取向压制→真空烧结回火→检验→加工→成品。
烧结型NdFeB永磁体矫顽力值很高,机械性能相当好,可以切割加工不同的形状和钻孔,但容易导致锈蚀,所以根据不同要求必须对表面进行不同的镀层处理。且非常坚硬和脆、有高抗退磁性、不适用于高工作温度。
(3)注塑钕铁硼(Zhusu NdFeB):有极高之精确度、容易制成各向异性形状复杂的薄壁环或薄磁体。
三、腐蚀机理
NdFeB永磁体的易腐蚀性一方面是由于Nd是化学活性最高的元素之一(它的标准电势E0(Nd?+/Nd)=-2.431V;另一方面,该合金是一种多相结构,各相间电化学位相差较大,易引起电化学腐蚀。
此外,NdFeB烧结过程中,磁体内部及表面容易出现微孔、结构疏松、表面粗糙等缺陷,而NdFeB永磁材料在应用中的工作环境常为高温、高湿,这些缺陷在高温、高湿环境下为NdFeB腐蚀提供了便利条件。同时,NdFeB制造过程中易含有O、H、Cl等杂质元素及其化合物,对腐蚀性影响最大的是O和Cl元素,磁体与O产生氧化腐蚀,而Cl及其化合物将加速磁体的氧化过程。
NdFeB易腐蚀的原因主要归结为:工作环境、材料结构、制作工艺。研究表明,NdFeB磁体的腐蚀主要发生在以下3种环境中∶暖湿环境、电化学环境、长时间高温环境(>250℃)。
01 高温环境
在干燥环境中,当温度低于150℃时,NdFeB磁体氧化速度很慢。但在较高温度下,富Nd区会发生如下反应∶4Nd+3O2=2Nd2O3。随后,Nd2Fe14B相会分解生成Fe和Nd2C3。进一步氧化,还将出现Fe2O3等产物。
02 暖湿环境
在暖湿条件下,NdFeB磁体表层的富敏晶界相首先与环境中的水蒸气按下式发生腐蚀反应:3H2O+Nd=Nd(OH)3+3H。反应生成的H渗人晶界中,与富Nd相发生进一步的反应:Nd+3H→NdH3,造成晶界腐蚀。NdH3的生成将会使晶界体积增大,造成晶界应力,导致晶界破坏,严重时会使晶界断裂造成磁体粉化。
环境湿度对磁体耐蚀性的影响要远比温度的影响大得多,这是因为磁体在干燥的氧化环境下,形成的腐蚀产物薄膜较致密,在一定程度上将磁体与环境分隔开,阻止了磁体的进一步氧化,而在潮湿的环境下生成的氢氧化物和含氢化合物不致密,不能阻止H2O对其的进一步作用。特别是当环境湿度过大时,如果磁体表面有液态水存在时,将会发生电化学腐蚀。
03 电化学环境
电化学环境中,NdFeB磁体中各相的电化学电势不同。富钕相和富硼相相对于Nd2Fe14B来说成为阳极,将会优先发生腐蚀,形成局部腐蚀的微电池。这种微电池具有大阴极小阳极的特点,少量的富钕相和富硼相作为阳极承担了很大的腐蚀电流密度,而它们是分布于Nd2Fe14B相的晶界上的,这样就会加速其晶界腐蚀。当磁体表面有金属镀层(如电镀Zn、Ni等)时,一但镀层出现孔洞、裂纹等缺陷,在磁体与金属镀层间也会形成腐蚀电池作用。
一般情况下,磁体作为阳极而优先腐蚀,金属镀层作为阴极,这就是为什么具有镀层的磁体往往出现暴皮现象的原因。另外,在对磁体进行表面处理的工艺过程中要接触各种镀液(如电镀、化学镀等),而烧结NdFeB磁体具有一定的孔洞,这样在这些工艺过程中,酸液或镀液就会进入孔洞,在以后的使用过程中也会造成电化学腐蚀。
四、防护技术
钕铁硼磁体的防护技术简单地分为化学防护技术和物理防护技术两大类。
化学防护技术主要包括制备金属镀层的电镀、化学镀,制备陶瓷镀层的转化膜以及有机涂层的喷涂、电泳等。生产中以电镀工艺在钕铁硼磁体工件表面制备金属防护镀层最为常用。
电镀是将磁体工件作为阴极,利用外电流,将电镀溶液中的金属阳离子在磁体表面还原,形成金属镀层的过程。烧结钕铁硼磁体电镀防护主要以提高磁体耐腐蚀性能为主,同时兼有提高表面力学性能、装饰等作用。
电镀的优点包括:工艺相对简单,成膜速度快,易于大批量生产。大部分用于钢铁、有色金属工件防护的电镀金属层的镀种均可用于钕铁硼磁体。用于钕铁硼磁体防护的主要镀种有Zn、Ni、Cu、Cr、Sn、Au、Ag等。由于钕铁硼磁体具有多孔结构和化学性质活泼,单层镀层常不能满足较高的耐蚀要求,一般说来采用多层复合镀可为磁体表面提供更为有效的防护。目前广泛采用的有电镀锌、电镀Ni-Cu-Ni、电镀Ni-Cu-Ni+Ag、电镀Ni-Cu-Ni+Au、电镀Ni-Cu-Ni+电泳环氧等。
锌没有磁性,作为防护镀层对磁体磁性能影响小。与镍、铜相比,镀锌价格相对低廉。锌的硬度较低,镀层内应力较小,不适用于防护易磨损的钕铁硼磁体工件。有文献报导锌镀层用于钕铁硼磁体防护形成原电池时可以通过牺牲阳极来保护基体。锌镀层的标准电极电位是-0.762V,在研究了钕铁硼磁体各成分相的电极电位后基本可以认定锌镀层并不能提供完全的阳极防护。实际使用效果上来看,锌镀层对钕铁硼磁体的牺牲防护的效果并不明显。锌镀层如果不经过处理,在空气中会变暗,因此镀锌后还需要进行钝化处理。
镍镀层的标准电极电位为-0.25V,较钕铁硼磁体正,为阴极性镀层,一旦外界电解质渗入镀层内部,反而会造成基材加速腐蚀,导致镀层和基体的结合力变差,出现镀层分层、起泡等缺陷,应用中对镍镀层致密度的要求非常高。钕铁硼磁体表面电镀镍,通常采用多层体系如Ni-Cu-Ni来降低镀层的孔隙率,提高镀层抗耐蚀性能。相对而言,电镀Ni-Cu-Ni成本比电镀锌高,但因耐高温、抗氧化、耐蚀、装饰性能、力学性能较优而受到用户青睐。
可直接用于钕铁硼磁体防护的单质金属电镀层还有铜、锡、金、银等,同时还有相当多的合金镀技术也可以用于钕铁硼磁体防护,如镍磷合金、镍硼合金、锌铁合金、锌镍合金等等。对于钕铁硼磁体来说,Zn-Ni合金镀层是阴极型镀层,在研究了不同组成的Zn-Ni合金镀层的稳定电位后表明,含Ni量为13%左右时,Zn-Ni 镀层为γ相的单相金属间化合物,它具有很高的热力学稳定性和耐蚀性。
经过多年生产和使用证明,钕铁硼磁体电镀防护镀层的缺点也相当明显:镀层孔隙率大,镀层不致密,有形状依耐性,工件边角处会因电镀过程中电力线集中镀层增厚,需要对磁体边角做倒角处理,对深孔样品无法施镀;电镀工艺对磁体基体有损伤作用,在一些较严酷的场合,电镀镀层长时间使用后,会出现镀层开裂、剥离、易脱落等问题,防护性能下降;随我国环保意识的日益提高,用于电镀三废处理的成本在磁体总成本中的比例急剧增长。
化学镀镍技术是指在不加外加电流的情况下,镀液中的金属盐和还原剂发生氧化还原反应,在工件表面的催化作用下,金属离子还原沉积的过程。与电镀相比,化学镀工艺设备简单,不需要电源及辅助电极,镀层厚度均匀,特别适合形状复杂的工件、深孔件、管件内壁等表面施镀,镀层的致密度和硬度较高。化学镀也存在一些缺点,镀层厚度上不去,可镀的品种不多,工艺要求相对较高,镀液维护比较复杂。化学镀镀种主要有镀镍、镀铜以及镀银等。目前化镀学镍磷合金在钕铁硼磁体防护工艺中有一定的采用,且多作为电镀镀层的追加防护使用。由于化学镀镍过程中有大量的氢气析出,对钕铁硼磁体基体造成较大损伤,同时使得镀膜具有较高的应力,使用过程中镀层易出现开裂、起皮等现象。
采用转化膜如磷化、钝化等技术在钢铁中很常见。在钕铁硼磁体表面采用传统的磷化也可以在表面形成一层致密的防护层。钕铁硼磁体磷化后可增加运输过程的防护,同时提高粘胶的结合力。
有机涂层的种类很多,大多可采用喷涂、刷涂以及电泳等方法进行涂覆加工。有机涂层成膜致密,对盐雾、水蒸气等有较好的阻隔作用。有机涂层可以与钕铁硼磁体电镀技术复合使用,达到进一步提高磁体防护性能的要求。
钕铁硼永磁体的应用
钕铁硼磁体可广泛应用于电动机、发动机、音圈马达、磁共振成像仪、通讯、控制仪表、音响设备等方面。
目前,稀土永磁电机是钕铁硼磁体最大的应用领域,约占磁体总应用量的70%,其种类繁多,形状、性能各异。
计算机硬盘配套的音圈电机占40%~50%,所以目前计算机产业是永磁电机的最大用户。
汽车工业是钕铁硼永磁应用增长最快的领域之一。在每辆汽车中,一般可以有几十个部位如引擎、制动器、传感器、仪表、音箱等会用到40~100颗NdFeB系及SmFeN系烧结磁体。
据悉,一辆全自动高级轿车约需消耗稀土永磁材料0.5kg~3.5kg;新能源汽车上钕铁硼材料的应用量更多,每辆混合动力车要比传统汽车多消耗约5kg钕铁硼,纯电动车采用稀土永磁电机替代传统发电机,多使用5~10kg钕铁硼。随着汽车工业的发展和电子技术要求的不断提高,其对钕铁硼永磁材料的需求量将越来越大。
免责声明:本网站所转载的文字、图片与视频资料版权归原创作者所有,如果涉及侵权,请第一时间联系本网删除。
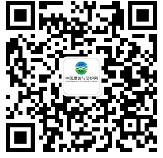
官方微信
《中国腐蚀与防护网电子期刊》征订启事
- 投稿联系:编辑部
- 电话:010-62316606-806
- 邮箱:fsfhzy666@163.com
- 中国腐蚀与防护网官方QQ群:140808414