0 引言
舰载机发动机热端部件, 由于受海洋环境的影响, 长期处于空气湿度大、 盐碱重的恶劣环境中服役, 除了受到冲蚀、 磨损外还要经受腐蚀考验。舰载机服役寿命的 90% 为停放状态, 有研究表明:连续长时间停放的腐蚀比经常使用和维护的严重, 因此发动机高温涂层耐常温海洋大气腐蚀的能力是不可忽略的。当发动机工作时, 热腐蚀成为典型故障之一, 不仅降低了发动机的使用效能, 而且增加了维修的工作量和费用。热腐蚀是在高温环境下氧及其他腐蚀性气体与材料表面的沉积盐共同作用而发生加速腐蚀的现象, 其危害性要远大于热氧化;而且, 随着“深蓝战略”实施的不断深入, 超过 1000℃以上服役的高温涂层抗热腐蚀性能研究, 将是今后一个时期研究的重点。
1 海洋大气特点
海洋大气环境极其复杂, 随着地球经纬度和海岸地理条件的差异, 温度、 湿度、 辐照度、 氯离子浓度、 盐度、 污染物等主要环境因子及其耦合作用对材料腐蚀行为的影响差异很大。海洋大气中腐蚀颗粒主要为 SO2、 HNO3、N2O5 与 NaCl反 应 生 成 的 Na+、 [Cl-]、[SO42-]、 [NO3-]、 [HN4+]等离子颗粒 。我国典型海洋大气表现为高温、高湿和高盐雾的特点。我国近海受大陆污染影响,离子、 SO2 含量都远高于国外;远海如西沙则离子含量高 。西太平沿岸 [NO3-] 浓度大于 [SO42-]浓度, 而我国 PM2.5、 PM10 离子颗粒浓度远高于其他西太平洋其它国家。欧美国家近、 远海主要是 [Cl-], SO2 含量很少, 近乎为零;东南亚[Cl-]、 SO2 相当。
海洋环境下服役舰载机发动机热端零部件容易受高湿、 盐雾以及微生物等形式的化学腐蚀,以及高温氧化、 冲蚀等叠加效应而形成的复杂热腐蚀,寿命大幅度缩短,维护费用和大修成本剧增,因此抗海洋大气热腐蚀的高温涂层技术需求紧迫。
2 热端涂层分类介绍
航空发动机不同部件由于工作环境的差别需要不同的涂层, 按功能可以分为:热障涂层、 高温抗氧化涂层、 耐磨/耐腐/抗冲蚀涂层、 封严涂层、抗微动磨损涂层、 阻燃涂层、 环境障涂层、 憎水涂层、 隐身涂层等。其中发动机热端主要有热障涂层、 耐磨/抗冲蚀涂层。
2.1热障涂层
热障涂层 (TBCs) 起源于 20 世纪 40 年代末50 年代初, 主要是用来提高镍基高温合金的高温性能的 。世界航空推进计划的三大隔热防护技术中, 单晶 ( 每年 1~2℃的速度增长 ) 和冷却气膜技术 ( 不断降低热效率、 增加加工难度 ) 的发展潜力已非常有限, 但应用厚度约 100~ 400μm 的热障涂层后, 基体温度可以降低 100~200℃, 这相当于高温合金过去三十年的发展总和 。因此,热障涂层被认为是目前提高发动机服役温度最切实可行的办法。目前在有气膜、 热障涂层的情况下, 单晶叶片的使用温度可以超过 1500℃, 未来需要承受 1800℃以上的温度, 依赖于开发新的叶片、 热障涂层材料(见图 1)。
图1 飞机发动机叶片耐温发展趋势
目 前 常 用 的 TBCs 材 料 有:7-8YSZ、 莫 来石、 Al2O3、YSZ+CeO2 、 La2Zr2O7、 硅酸盐, 其中Y2O3 部分稳定的 ZrO2(YSZ, Y2O3 含量一般为7%~8%, 质量分数)是应用最广泛的 TBCs 材料。近年来国内外在多元氧化物掺杂氧化锆、 A2B2O7型烧绿石或萤石化合物、 磁铅石型六铝酸盐化合物、 石榴石型化合物、 钙钛矿结构化合物和其他新型氧化物陶瓷等先进超高温热障涂层陶瓷材料方面进行了大量研究。2007 年哈佛大学 Clarke教授课题组和加州大学圣巴巴拉分校的 Lavi 教授等发现 ZrO2-YO 1.5-TaO2.5 的使用温度可以达到1500℃, 而热导率较 YSZ 下降 100%, 具有新型涂层发展潜质 。近几年, 新型稀土钽酸盐高温铁弹相变陶瓷材料进入人们的视野, 预期最高使用温度可以达到 1600℃ 。尽管稀土钽酸盐具有低热导率和膨胀率, 但是作为涂层材料需要优异的断裂韧性, 因此如何调控其铁弹性增韧将是未来一段时间探索的热点。
2.2耐磨涂层
高温耐磨涂层主要应用于发动机燃烧室喷嘴外罩及轴承座等零部件。目前常采用等离子喷涂技术制备 Cr3C2-NiCr、 WC-Ni、 WC-Co、 Cr2O3 涂层 。研究表明, 水会恶化涂层性能, 涂层材料断裂韧性越高, 孔隙率和微裂纹长度越小, 涂层的耐磨性越好 。有研究表明采用多层涂层可提高抗磨损性能。
2.3抗冲蚀涂层
飞机在低空飞行、 起飞和降落过程中, 空气中的盐粒、 火山灰、 雪和沙粒等, 燃油杂质以及发动机部件掉落的残骸等, 在高速气流作用下不可避免地被吸入涡轮发动机内 。风洞实验表明,直径大于 30μm 的砂粒能对叶片造成明显的冲蚀磨损, 大颗粒甚至能使叶片变形, 影响发动机性能或导致其失效 。上世纪八十年末到九十年代初, 抗冲蚀涂层技术才真正应用于航空器抗砂粒环境。目前应用最广泛的是合金化 TiAlN、ZrAlN 等涂层、 电弧镀等技术制备的 ZrN/TiN 多层纳米涂层以及复合的 Al/AlN、Ti/TiN、 Cr/CrN涂层等(如图 2 所示)。广泛应用于镍基高温合金、钛合金部件的抗冲蚀性能提升。总体来说,我国能在航空发动机上得到应用的抗冲蚀涂层很少, 还不能满足设计的技术要求。
抗冲蚀涂层脆性大, 增加了合金表面裂纹萌生的倾向, 从而降低合金的疲劳性能, 是亟待解决的技术难题。另外, 耐冲蚀涂层在干燥性空气中对压气机叶片具有很好的抗冲蚀防护作用, 但在海洋环境却可能受到严重的潮湿或盐雾腐蚀破坏, 使叶片寿命缩短, 给发动机带来安全隐患。目前这些工作还处在基础和应用研究阶段。
图 2 TiN/Zr/ZrN 多层涂层
3 海洋大气腐蚀研究现状
3.1海洋大气常温腐蚀
航空发动机在停放时将受到废气和尾气中的硫化物、 氮氧化物与海洋盐雾组合成的 pH 值为2.4~4.0 的酸性潮湿层腐蚀, 再形成酸性液膜,加速了涂层的失效 。海洋大气常温腐蚀一般采用乙酸盐雾试验以及电化学腐蚀实验。研究表明 TBCs 经过 400 小时的乙酸盐雾试验后, 表面变得粗糙不平, 产生了较大的裂纹 。通过改变TBCs 涂层化学结构, 比如掺杂YSZ/ (Ni,Al) 涂层较基体和纯 YSZ 涂层有更低的自腐蚀电流密度, 表现出优异的耐腐蚀能力。像 WC-CoCr 耐磨涂层在 NaCl 溶液和 HCl 溶液中, 耐腐蚀性明显优于镀铬涂层, 但在 NaOH 溶液中, 镀铬涂层发生剧烈钝化形成保护膜, WC-CoCr 涂层的耐腐蚀性弱于镀铬涂层。又比如 Ni-C 封严涂层在NaCl 溶液中主要发生电偶腐蚀, 溶液中的氧浓度是影响涂层腐蚀的重要因素, 腐蚀速率随氧浓度的提升而加快。
3.2海洋大气热腐蚀
相比较海洋大气常温腐蚀, 海洋大气热腐蚀要复杂得多。燃气热腐蚀试验 (gas hot-corrosiontest) 在指定的温度、 燃油流量、 油气比及海盐含量的条件下所形成的燃气中, 对试样进行冷热交变循环试验。叶片表面温度、 燃气中的盐含量以及燃油中的硫与钒是导致热腐蚀的重要因素。目前, 热腐蚀实验主要是采用有涂盐法和浸盐法两种。常用的熔盐有:NaCl/Na2SO4/K2SO4/V2O5等单一或两两组合。热腐蚀温度主要集中在 800-1000℃。热腐蚀时间以 2~10h 居多。从目前查阅的文献来看, 实验特点可以分为以下三种:
(a) 不带基体的纯熔盐热腐蚀
常用于新型陶瓷涂层材料的热腐蚀产物分析、热腐蚀动力学研究。采用涂盐法或者浸盐法, 将试样静置在高温炉内。比如多元氧化物掺杂的氧化锆/氧化铝/磷酸涂层材料与熔盐反应, 会生成掺杂金属的氧化物或者盐类而使得涂层失效。
(b) 带基体的纯熔盐热腐蚀
基体不一定是单晶或定向组织。采用涂盐法或者浸盐法, 将试样静置在高温炉内。此类研究最多, 也是应用最成熟的 YSZ 及其复合涂层。研究表明采用电子束物理气相沉积 (EB-PVD) 工艺制备 YSZ 涂层的热腐蚀寿命可以达到等离子喷涂 (APS) 工艺制备的两倍, 但是制备成本高、热导率高 。YSZ 的抗热腐蚀效应主要来自致密的 Al2O3, 其中 Cr、 Ta、 Y 能稳定 Al2O3 的生成提高涂层的抗热腐蚀性。而外来的 Na、 V 和 S都会引起 Y 元素生成 YVO4, 使得 YSZ 涂层退化。海洋环境下, 氯化物则是 YSZ 涂层热腐蚀的主要因素, 会造成涂层顶部以及涂层/粘结层之间产生大量的无保护性氧化物。近几年, 人们尝试着通过制备复合涂层来提高抗热腐蚀性能,在实验室获得比较好的效果, 比如 LaPO4/YSZ/NiCoCrAlY,Sm2Sr Al2O7(SSA)/NiCrAlY 复合涂层 MgO 和 NiO 起到提高抗热腐蚀的能力的作用。还有改进涂层制备技术, 如采用大电流脉冲电子束 (HCPEB) 工艺可以改善抗热腐蚀性能 。
(c) 模拟海洋大气热腐蚀
包括高温熔盐电化学测试,高温燃气热腐蚀,先涂盐, 再高温燃气烧蚀。这类对模拟装置要求高, 国内主要参照中华人民共和国航空工业标准HB7740-2004 进行 , 采取燃气 + 高温炉的方式保证高温, 试样保持静置。绝大多数文献都是以考核不同涂层工艺、 不同种类盐、 不同温度、 时间等对涂层材料热腐蚀产物的影响为主, 而结合力学失效分析的研究相对较少。发动机实际工作时, 涂层是处于动态的高温、 冲蚀、 腐蚀、 离心力环境, 因此实现模拟实际工况考察涂层的热腐蚀显得尤为重要, 遗憾的是, 国内外大部分实验室还无法模拟发动机实际工况, 在这一块发表的数据非常少, 因此模拟设备的标准化建设值得进一步探索和研究。
4 海洋大气环境涂层腐蚀失效机制
4.1海洋大气环境涂层常温腐蚀失效机制
发动机各种高温涂层一般具有多孔、 多相、多层的特性, 因而在海洋大气环境下的失效机理可主要分为闭塞电池腐蚀和电偶腐蚀。
闭塞电池腐蚀
闭塞电池腐蚀存在特有的微缝的金属构件中缝内外组成的电池。由于高温涂层往往具有连续的多孔结构, 在腐蚀性环境中, 腐蚀介质能够通过孔隙向涂层内部渗透, 在缝隙、 蚀孔内部存在“闭塞电池” 。在闭塞区域内发生贫氧、 酸化、[Cl-] 富集等变化, 在闭塞区内外电化学条件的差异产生自催化加速腐蚀效应。
电偶腐蚀
由于腐蚀电位不同, 异种金属彼此接触或通过其他导体连通, 处于同一介质中, 造成异种金属接触部位的局部腐蚀, 就是电偶腐蚀, 亦称接触腐蚀。高温涂层一般由几部分构成, 由于不同层的材料不同、 结构不同、开路电位不同, 因此在不同层之间、同层的不同材料之间形成电位差,满足电偶腐蚀产生的热力学因素;加之具有多孔,在不同层之间由于孔隙存在可以形成导通的回路,在高电位区域与低电位区域之间形成畅通的电子通道和离子通道, 满足电偶腐蚀产生的动力学因素;当热力学和动力学条件同时满足时, 即可发生电偶腐蚀 。
4.2海洋大气环境涂层热腐蚀失效机制
发动机在海洋环境中服役, 必然受到高温、高湿、 高盐度以及大量腐蚀颗粒的考验。因此,其热腐蚀失效是高温腐蚀、 热应力、 高温冲蚀的共同结果。
从单一因素考虑, 包括氧化相变机制、热应力作用机制 和外来物冲蚀 三种失效机制。在热腐蚀过程中, 氧化相变来自熔盐与涂层的腐蚀产物、 涂层自身高温相变以及涂层多结构之间的化学作用;热应力作用则更为复杂, 因温度梯度引起的热应力、 相变导致的热应力、 热不匹配引发的形变热应力、 氧化膜生长引起的应力等在界面处的聚集, 使得界面区域是破坏发生最多的区域。周益春等人 研究了涂层在热错配应力作用下的开裂机理, 建立了一种具有真实 TGO形貌的 TBCs 裂纹扩展有限元方法。通过对界面裂纹扩展的分析, 发现 TC/TGO 界面存在两种失效机理:(1) 由于没有微水平裂纹, 界面裂纹的发展导致 TC 层发生开裂;(2) 当存在微水平裂纹时,TC 层的开裂是水平裂纹和界面裂纹发展相互作用的结果。
海洋大气环境中的盐颗粒对涂层的冲蚀作用不可忽略。这种高温、 高速冲蚀会在涂层粘结层内部造成裂纹源, 从而引起涂层的失效。周益春团队构建了 APS TBCs 冲蚀模型:
其中 α 是冲击角度, Ke 每颗粒子吸收动能的比率, v 粒子速度, δ 层厚, ρc 陶瓷层密度, Γ 陶瓷层断裂韧性。
图 3 热障涂层冲蚀速率模拟
事实上, 航空发动机的高温涂层在海洋大气环境中服役剥落的本质是受到温度场、 应力场、化学场等“热力化” 耦合作用的结果。三者关系如下:
(1) 温度场:界面氧化、 冲蚀、 CMAS 都在高温下进行, 与温度场有直接的关系;
(2) 应力场:TBCs 各层热膨胀系数的不匹配、服役过程中的机械载荷决定了界面氧化、 冲蚀、CMAS 均在有应力场的作用下发生;
(3) 化学场:氧、 CMAS 和 TBCs 体系的各种元素反应生成新的化合物, 如 TGO, 硅酸锆, 尖晶石, 而它们取决于体系的化学势、 浓度等化学场的参量;
(4) 化学场、 温度场、 应力场的相互促进:化学反应时新的化学产物形成时会影响体系的温度场, 同时约束体系以及新材料加剧的热失配将改变体系的应力场;温度场极大的影响化学反应,如元素扩散、渗透深度、反应速度以及热失配应力;应力场则极大的影响氧或化学反应元素的扩散。
(5) 裂纹也是热力化耦合多场作用下的扩展过程:当有微缺陷存在时, 氧的扩散、 化学反应、应力场会在缺陷处产生明显的聚集、 集中 , 然后进一步促进裂纹的扩展。
Loeffel 和 Anand针对热障涂层的氧化 - 粘塑性变形问题建立了传热、 弹性 - 粘弹性变形、氧气扩散和氧化反应之间的耦合, 但该理论仅考虑氧化膨胀应变而不涉及扩散介质引起的体积变化, 同时采用幂函数形式的演化率方程来抽象地描述反应速率也是有欠缺的。
湘潭大学周益春课题组对 CMAS 渗透与腐蚀的热力化耦合理论进入了深入研究, 推导了不带基体 TBCs 高温腐蚀过程广义本构关系:熵与温度, 应力与弹性应变, 化学势与浓度三个广义本构关系:
其中, s 代表 CMAS 腐蚀涂层过程单位体积材料系统的熵;εe 代表高温腐蚀过程热量流动导致涂层的热应变, 考虑到腐蚀条件为恒温,则此应变等于零;Hemholtz 自由能 Ψ;温度 θ;CMAS 浓度 c;弹性应变 εe。从目前人们对 TBCs 破坏机制的研究来看,热力化耦合的本质机制依然存在一系列的科学问题需要解决:包括模型的建立和实验表征等。
5 涂层性能常用的测试分析方法
研究表明热端涂层失效的原因是受到温度场、应力场、 化学场耦合的结果, 因此选择时间、 空间分辨率高的分析技术来研究热端涂层服役过程中的温度场、 应力场、 化学场显得极为关键。目前常用的测试分析方法如下。
5.1温度场测量
随着航空航天事业的发展, 航空发动机正向着高效率、 高性能、 高推重比(发动机推力与发动机或飞机重量的比值) 发展, 为满足更高的要求, 需提高燃烧室的温度, 使燃料充分燃烧, 涡轮前进口温度也相应提高, 由于受到涡轮叶片材料的限制,热端部件的温度不能超过其承受范围,否则涡轮叶片将会融化变形,造成毁灭性的事故。现在服役的第四代发动机前进口温度已经接近2000K, 未来第五代发动机甚至可达到 2250K,在如此高的温度下, 发动机热端部件的温度测量已变得极为困难。
目前航空发动机涡轮叶片温度测量技术分为接触式和非接触式两类。接触式测量有壁温热电偶、 薄膜热电偶 、 液晶测温和示温漆等。
壁温热电偶测温是基于温差电效应, 两种不同材料连接成闭合回路, 当两种金属连接点存在温差时会产生相应的热电势, 以此判定材料此时的温度, 但是需要在测量目标上面开槽埋入热电偶,如此会对材料的强度造成影响。为避免这个缺点,随着沉积技术的日趋成熟, 可以将热电偶沉积在具有绝缘层的材料表面, 这就是薄膜热电偶。液晶测温和示温漆只能显示被测材料所经历的温度范围, 精确度不足, 不能实时显示温度, 且当涡轮叶片高速旋转时还会发生脱落, 造成温度测量的不准确, 因而科研工作者探索了非接触式测温方法。非接触式测温主要有红外辐射温度计、热辐射高温计, 这两种测温方法都是基于普朗克辐射定律, 通过搜集被测材料表面所发出的热辐射量而确定温度, 这种测温方法提供了既不干扰表面也不影响周围介质的测温方法, 对于高速旋转的涡轮叶片温度的实时检测是非常合适的。除此之外, 还有荧光温度计、 超声波等方法, 但是由于荧光材料、 测量精度等问题尚未在涡轮叶片上实现温度测量。
5.2应力场测量
目前, 测量应力的方法主要分为两大类。
(1) 机械法, 如钻孔法、 取条法等。机械法测量残余应力一般将具有残余应力的部分从构件中分离或切割出来, 使应力释放。然后测量其应变的变化求出残余应力, 是一种间接测量手段。机械法会对工件造成一定的损伤和破坏, 但由于其具有理论完善、 技术成熟、 测量精度较高等优点,目前在现场测试中应用广泛。
(2) 物理检测法, 如 X 射线衍射法、 中子衍射法、 超声波法、 纳米压痕法、 溅射深度剖析法、光激发荧光谱技术、 显微拉曼光谱技术、 声发射法等。这些方法均属于无损检测, 对工件不会造成破坏, 但成本较高, 其中 X 射线衍射法发展最为成熟。周益春团队开展了十多年的声发射无损检测技术研究, 已经掌握了该方法的集成、 检测与信号分析, 实现了服役环境模拟下失效过程的实时检测。
5.3化学场测量
目前化学元素、 相成分、 相结构方面的测定主要有:X 射线衍射相分析、 电化学原位拉曼光谱法、 交流阻抗谱 、 原位红外反射吸收光谱法(IRRAS)等。宫声凯等人发现交流阻抗谱中低频段阻抗值的变化可以有效地反映热障涂层热氧化层内横向裂纹的萌生及扩展 。周益春等人从实验和理论上解释了热障涂层复阻抗谱测量时电场发散的本质, 表征了氧化层厚度、 陶瓷层孔隙与氧化环境的演化关系。
但总的来说, 高温服役环境下损伤的实时检测,尤其是损伤的定量评价还不成熟。更重要的是,在现有的试验模拟装置中, 除了静态装置中有少量图像、 重量、 温度等参数的检测手段外, 很少有成熟的无损检测技术, 动态装置中的检测方法尤为匮乏, 是这一研究领域的巨大挑战。
6 结论
航空发动机高温涂层在海洋大气环境下服役,除了常温-高温热循环冲击外, 还要受到高湿、 高盐分的大气腐蚀, 因此其失效是一个非常复杂的热、 力、 化耦合的过程。
海洋大气具有复杂的腐蚀性,且具有动态性、地域性等特点。同一地点的海洋大气成分、 温度、湿度时刻发生着变化, 不同经纬度的海洋大气也存在差异, 因此在研究航空发动机高温涂层耐海洋大气腐蚀时, 需要考虑不同盐分、 浓度、 温度、湿度的情况;甚至需要仿真动态气氛环境下高温涂层的耐腐蚀性能。航空发动机高温涂层种类多, 每一种都具有其特定的性能, 但在海洋环境中却可能受到严重的潮湿或盐雾腐蚀破坏, 使叶片寿命缩短, 给发动机带来安全隐患。目前这些工作还处在基础和应用研究阶段。航空发动机实际服役情况是常温-高温热循环状态, 且 90% 以上时间处于常温状态。常温腐蚀机制为闭塞电池腐蚀和电偶腐蚀, 常采用盐雾腐蚀实验和电化学腐蚀实验进行考核。高温热腐蚀失效是高温腐蚀、 热应力、 高温冲蚀的共同结果,本质是受到温度场、 应力场、 化学场等“热力化”耦合作用的结果。
测试分析的方法由事后静态分析法向原位动态分析法发展,由接触破坏法向无损检测法发展。新的测试分析方法为更好地研究海洋大气环境涂层的腐蚀失效机制提供更加精确的数据。但也要看到:针对航空发动机高温涂层耐海洋大气腐蚀的研究, 依然存在很多问题, 可以预期的是:
(1) 理论方面, 需要综合考虑常温腐蚀与高温腐蚀交替进行过程中的氧化、 腐蚀、 蠕变、 塑性变形、 温度梯度及基底曲率等因素的影响, 分析不同结构涂层热循环、 腐蚀、 氧化、 冲蚀等作用下应力场与应力强度因子的演变规律。
(2) 结合非线性连续介质力学与相场理论, 建立涂层高温氧化、CMAS 腐蚀的力化本构模型,揭示出其热力化耦合的失效机制。
(3) 实验方面, 探索了原子尺度下涂层界面氧化、 涂层 CMAS 的高温原位透射电镜观察方法,结合第一性原理揭示了热障涂层原子尺度下氧化、腐蚀的机理。基于所发展的各种热力与服役环境模拟方法, 结合实时检测技术, 系统研究了热力载荷、 高温氧化、 冲蚀、 CMAS 腐蚀等载荷下的失效模式与失效准则。
本文发表在《热喷涂技术》第11卷第四期(总第42期)2019年12月:P1-P9。
免责声明:本网站所转载的文字、图片与视频资料版权归原创作者所有,如果涉及侵权,请第一时间联系本网删除。
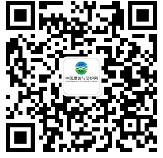
官方微信
《中国腐蚀与防护网电子期刊》征订启事
- 投稿联系:编辑部
- 电话:010-62316606-806
- 邮箱:fsfhzy666@163.com
- 中国腐蚀与防护网官方QQ群:140808414