高耐性抗静电涂料的研究
2016-02-04 16:13:42
作者:本网整理来源:
摘要:以酚醛环氧为树脂体系,添加一定量的导电云母粉,脂环胺作为环氧固化剂制备了高耐性抗静电涂料,探讨了导电云母粉的用量对导静电性能的影响;不同类型的环氧树脂和不同固化剂对涂层耐溶剂后导静电性能的影响;不同涂层耐盐雾性能以及中性盐雾对涂层导静电性能的影响。其中脂环胺固化酚醛环氧体系的导静电性能最稳定。
引言
抗静电涂料主要应用在石油储罐内壁涂装,我国石油储罐的设计寿命一般长达50a,基于储罐如此长的使用寿命以及高造价和贮存物质的重要性及特殊性,对石油贮罐进行防护极为必要。各类储罐(原油储罐、中间产品罐和成品油罐)在使用过程中,均存在静电和腐蚀这两个共同的问题,涂装涂料可以廉价、快捷地解决这两个问题[1]。
涂料的成膜物质一般为高聚物,其与流动的油品和各种液体烃类摩擦会产生静电,静电放电可能会点燃油品等易燃易爆的原料,引起火灾,甚至导致油罐爆炸。各类品质的石油对涂层的腐蚀破坏很严重,尤其是储罐的顶部,由于充斥了大量的空气、油蒸汽、水蒸气、H2S等很容易破坏保护涂层的混合气体,对钢质储罐造成严重腐蚀,可能引起泄漏和穿孔而酿成事故。国家标准GB/T13348—2009《液体石油产品静电安全规程》中规定:油罐内壁应使用抗静电涂料,涂层的表面电阻率应为108~1011Ω[2]。由于抗静电涂料大多应用于贮存和运输原油、石油中间产品和成品油的储罐内壁,这就要求该涂层应具备很好的耐溶剂性能,同时长时间溶剂浸泡过程中涂层的导静电性能应能满足国家规定要求。本研究探讨了不同环氧树脂和固化剂构成的涂层在耐溶剂浸泡后导静电性能的变化,用酚醛环氧树脂取代普通环氧树脂,赋予了抗静电涂层更好的耐盐雾腐蚀和耐溶剂性能,大幅延长了石油储罐的使用寿命。
1·实验部分
1.1主要实验材料
酚醛环氧树脂(陶氏化学,环氧当量181~210);E-51型环氧树脂(西安树脂厂);导电云母粉(常州华珠颜料有限公司);乙二胺加成物;聚酰胺;脂环胺;酚醛胺。
1.2实验仪器
数显分散机:IKA;盐雾箱:美国Q-LAB公司;电子万能试验机:岛津;ACL-380表面电阻测试仪:美国ACL(最大量程×1012Ω)。
1.3实验部分
1.3.1涂料的制备
将环氧树脂、分散剂、除导电云母粉外的其他颜填料和部分溶剂混合均匀后,研磨至细度<80μm,加入剩余溶剂和导电云母粉,高速搅拌均匀后即为涂料的A组分。
1.3.2样板的制备
将固化剂按一定比例加入到A组分中,混合均匀。
(1)空气喷涂在聚酯膜上,控制干膜200~250μm,用以测定表面电阻;(2)喷涂在手工打磨的1mm钢板表面,控制干膜200~250μm,用于耐溶剂浸泡实验。
1.3.3耐溶剂试验
将样板浸泡在各类溶剂中,每间隔1周取出晾干,用ACL-380表面电阻测试仪测定涂层的表面电阻。
1.3.3耐中性盐雾试验
将制备好的未刻槽的干膜(220~250μm)涂层放入中性盐雾箱中,每隔500h取出,表面用水冲洗干净,观察涂层表面状况,待涂层表面干燥后用表面电阻仪测定表面电阻,测定后将样板再放入盐雾箱中重复进行试验,直至涂层失效。
1.4测试标准
耐中性盐雾试验按照GB/T1771—2007《色漆和清漆耐中性盐雾性能的测定》进行测试;
耐溶剂试验按照GB/T9274—1988《色漆和清漆耐液体介质的测定甲法》进行测试;
涂层导静电性能按照GB13348—2009《液体石油产品静电安全规程》进行测试。
2·结果与讨论
2.1导电云母粉用量对导静电性能的影响
本研究中导电云母粉的导电性能主要是通过片状导电云母粉相互搭建、链接形成的允许静电电子传输的导电网络,以及电子能够穿越聚合物薄层形成的导电通道所共同决定的,这种导电网络和导电通道的形成与导电填料含量紧密相关。实验中制备了导电云母粉在A组分中的添加量分别为5%(质量百分比,下同)、10%、15%、20%、21%、22%、23%、24%、25%、30%、35%和40%的一系列涂料,测试了各种涂料的导电性,结果如图1所示。
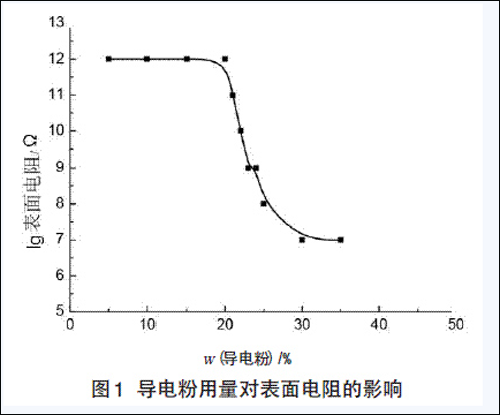
从图1可以看出,导电云母粉添加量在20%以下时,随着添加量加大,涂层表面电阻变化不大,这是因为电云母粉用量少,还无法在涂层中相互搭建、链接形成允许静电电子相互传输的导电网络;当添加到21%时,表面电阻开始有所下降,说明此时导电网络和导电通道逐步建立,电子传输效率逐步提高;随着导电云母粉添加量的进一步增大,表面电阻下降幅度增大;但当导电云母粉添加量达到30%时,表面电阻达到最小值,再提高添加量也无法降低表面电阻,这说明添加30%时,导电网路和导电通道的建立已经达到了该导电云母粉电导率的极致。根据GB/T13348-2009的要求,表面电阻率应为108~1011Ω,在酚醛环氧树脂体系中导电云母粉用量占A组分的22%时,涂层的导静电性即能满足国标要求。
2.2不同固化剂对涂层导静电性能的影响
本研究选择了聚酰胺、脂环胺、乙二胺加成物和酚醛胺分别作为酚醛环氧树脂的固化剂。将制备的样板分别浸泡在甲基异丁基酮、二甲苯、丙二醇甲醚、93#汽油和97#汽油中,结果见图2。
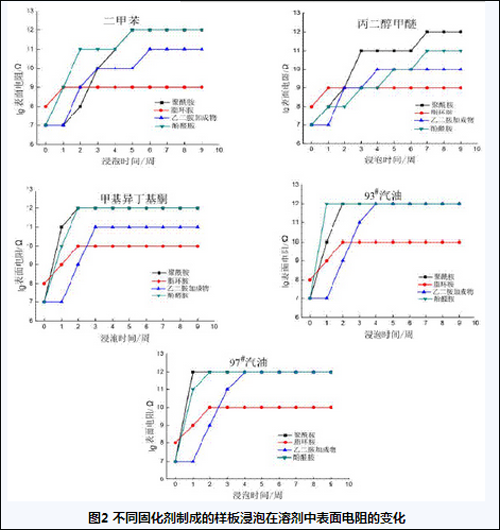
从图2可以看出,各类固化剂耐溶剂的能力排序是:脂环胺>乙二胺加成物>聚酰胺>酚醛胺。脂环胺固化的涂层在第一周表面电阻增大后,随时间增加表面电阻基本不再变化,耐溶剂效果最佳。这几类溶剂中,93#汽油和97#汽油对涂层表面电阻的影响最大,甲基异丁基酮次之,丙二醇甲醚是对表面电阻影响相对较小的溶剂,聚酰胺和酚醛胺在除丙二醇甲醚外的其他3种溶剂中表面电阻很快就达到>1012Ω,失去了抗静电功能,在保持表面电阻效果上,这两种固化剂耐溶剂性能较差。根据结果选择脂环胺作为酚醛环氧树脂体系的固化剂。
2.3不同环氧树脂对涂层导静电性能的影响
用普通E-51型环氧等量替换其中的酚醛环氧树脂(环氧当量181~210),固化剂种类和用量一致,制备样板做耐溶剂浸泡试验,与高耐性抗静电涂料进行对比。由表1可以看出,普通环氧树脂涂层在丙二醇甲醚中与酚醛环氧差不多,但在甲基异丁基酮中则出现差异,第3周后普通环氧树脂涂层表面电阻急剧升高,抗静电功能失效,在93#和97#汽油中抗静电有效时间更短,2周后基本失效。可以看出脂环胺固化酚醛环氧树脂体系的耐溶剂效果明显优于脂环胺固化普通环氧树脂体系,长时间浸泡在溶剂中的涂层表面电阻满足要求。

2.4中性盐雾对抗静电涂层的影响
本研究的防腐性能主要是通过涂层的耐中性盐雾性能来确定的。相对于E-51型环氧树脂,酚醛环氧树脂分子链段中羟基含量较少,在钢铁表面附着力稍差,但当与脂环胺固化后,能形成更小、更致密的交联网络,对涂层的耐盐雾性能有所提高。从表2可以看出,添加导电云母粉后涂层耐盐雾性能有所下降,可能是导电云母粉在形成导电网络时,电子更容易在涂层中移动,使得底材更易受到电化学腐蚀。此外,脂环胺固化酚醛环氧抗静电体系能够耐2000h盐雾后不起泡,表面电阻仍可以达到1010Ω,能满足防腐蚀的使用要求,而脂环胺固化E-51型环氧树脂耐2000h盐雾后表面电阻大于1012Ω,导静电性能基本失效。因此该酚醛环氧树脂和脂环胺固化剂体系能同时满足实际应用中的抗静电、防腐蚀使用要求,具有很高的应用价值。
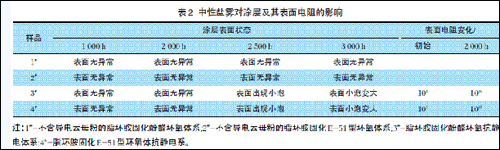
3·结语
本研究研制了一种以导电云母粉为导电填料、脂环胺固化酚醛环氧树脂体系的高耐性抗静电涂料。导电云母粉添加量在22%时,导静电性能最佳。通过对不同固化剂固化的酚醛环氧涂层在二甲苯、丙二醇甲醚、甲基异丁基酮、93#汽油和97#汽油中的浸泡实验,确定了脂环胺固化剂在溶剂浸泡条件下导静电效果最优异。与普通环氧相比,酚醛环氧树脂制备的涂料耐溶剂效果更好,耐盐雾性能也不差,尤其是在耐溶剂和盐雾腐蚀后的导静电性能仍能满足实际抗静电、防腐蚀的使用要求。
参考文献
[1]刘冬梅,程振炎,刘文慧。抗静电涂料的应用及其发展[J].上海涂料,2007,45(9):35-37.
[2]李公权,傅大海,郭铭,等。油罐抗静电耐油防腐涂料的选材[J].涂料工业,2000,30(2):18-19.
责任编辑:班英飞
《中国腐蚀与防护网电子期刊》征订启事
投稿联系:编辑部
电话:010-62313558-801
邮箱:ecorr_org@163.com
中国腐蚀与防护网官方 QQ群:140808414
相关文章
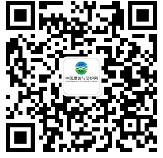
官方微信
《中国腐蚀与防护网电子期刊》征订启事
- 投稿联系:编辑部
- 电话:010-62313558-806
- 邮箱:fsfhzy666@163.com
- 中国腐蚀与防护网官方QQ群:140808414
点击排行
PPT新闻
铝合金LDH自修复自抗菌膜层构建
点击数:466
碳钢及合金钢应用与区别
点击数:393