由于CO2具有良好的驱油效果和广泛的适应性,并且CO2驱能够实现温室气体的地下封存,具有环保效益,国内各油田相继开展了规模不同的先导试验,探索了不同类型油藏CO2驱的可行性,现场试验表明,国内适合CO2驱的储量丰富,应用前景广阔。腐蚀控制是油田CO2驱的关键技术,国内外都开展了有针对性的腐蚀机理与腐蚀控制技术研究。国外自上世纪八十年代就进入了规模应用,腐蚀控制技术成熟。国内目前还处于探索阶段,现场实验取得了良好效果。从国内外CO2驱的腐蚀控制技术来看是基本一致的,但对于腐蚀速率的控制,国内外做法具有明显的不同。开展腐蚀控制研究,确定合理的腐蚀速率控制值对于降低油田开发成本,保证CO2驱油田生产顺利进行具有重要意义。
图注:CO2驱油田注采井油套管腐蚀速率控制值的探讨
1 CO2驱油田腐蚀速率控制值现状
国内外CO2驱油田普遍采用普通碳钢(J-55、N-80等)油套管通过添加缓蚀剂的措施来控制腐蚀。中石油的吉林油田在黑59、黑79试验区在油层部位还使用了不锈钢套管。
通过公开发表的文献检索分析以及与国外资深专家交流情况来看,在使用缓蚀剂控制碳钢腐蚀速率方面,国外并无统一或明确的腐蚀速率控制标准值,他们的做法是通过实验选择最优的缓蚀剂。
与国外不同的是,我国在腐蚀速率控制方面普遍采用了0.076mm/a作为开发方案设计控制值、缓蚀剂筛选评价值或腐蚀控制效果评价值。这一数值从工程安全和成本上是否是最优的,仍需要进一步探讨。
2 关于腐蚀速率0.076mm/a的探讨
平均腐蚀速率0.076mm/a来自于《碎屑岩油藏注水水质推荐指标及分析方法》(SY/T5329-2012)中的推荐注水水质的控制指标。这一指标的确定方法是,当水质满足了其它指标后,检测试样水对现场用钢(一般选碳素钢如Q235)的腐蚀速率,测试时间为30±2天,得出最大腐蚀速率小于0.076mm/a。该数值是基于水质的其它控制指标达到标准后的一个必然数值。
上述标准中主要考虑的腐蚀源不同于CO2驱油田的实际。标准中CO2是辅助性控制指标,是腐蚀的次要因素。一方面,水中的细菌作为主要腐蚀因素在标准中是主要控制指标,而CO2浓度是作为辅助性控制指标。另一方面,标准中规定CO2浓度为-1.0≤ρCO2≤1.0㎎/L,且在早期的标准版本中规定PH值为7±0.5,研究表明,CO2腐蚀依赖于PH值,在注入水为中性的条件下,CO2引起的腐蚀基本是可以忽略的。
上述标准中的腐蚀环境与CO2驱油田的腐蚀环境也是大不相同的。CO2驱油田的注入井在气水交替初期,或采油井产出液中含水和CO2较高的井,其水中溶解的CO2浓度往往达到饱和状态。研究表明,在常压下,油田水中CO2的饱和浓度约为270㎎/L,注采井随井深的增加,温度和压力上升,虽然温度升高会降低CO2的溶解度,但压力升高又提高了CO2的溶解度,因此,井下环境中CO2浓度远远超过1.0㎎/L。另外,标准中的腐蚀速率0.076mm/a是未加缓蚀剂条件下产生的,而油田井下一般通过添加缓蚀剂来控制CO2的腐蚀。
从测试环境、主要考虑的腐蚀源和腐蚀环境来看,将《碎屑岩油藏注水水质推荐指标及分析方法》中规定的0.076mm/a这个数值直接作为CO2驱油田腐蚀环境下的选材与腐蚀控制衡量指标是不合理的。
3 合理的CO2驱油田腐蚀控制速率探讨
3.1 通过强度计算反推平均腐蚀速率控制值
通过加注缓蚀剂减缓CO2对碳钢的腐蚀或选择耐腐蚀材料,其目的是保护井下油套管,保证采油设施和各种采油作业的正常、安全运行,只要井下油套管的剩余强度达到需求,其寿命期间的控制腐蚀速率就应该是合理的。
下面分析找出注采井的危险工况,然后计算其所需强度,进而计算出合理的控制腐蚀速度。由于CO2驱大多应用于低渗透油藏,下面的分析以低渗透油藏为例。
油井完井后的套管强度,对于采油井来说,低渗透油藏的压裂改造作业是最危险的工况。实际上,低渗透油藏开发井一般在投产时或投产初期即进行压裂,进行重复压裂的井是很少的,且压裂也不会安排在20年末进行,况且,为了防止低渗透油藏CO2驱开发井发生气窜,油井可能不进行压裂,对于腐蚀后的剩余强度来说,压裂作业并不是最危险工况。采油生产过程中,套管最危险处是水泥返高处,当动液面低于这个深度时,套管就受到了管外地层静压力的挤压,此为工况Ⅰ;对于注气井来说,最危险的工况莫过于出现井口失控,注入气气化喷出后井筒掏空,此时套管的危险井段是油层部位,套管需要承受地层的静压力的外挤,此为工况Ⅱ。
根据以上的分析进行计算条件假设:油层中深H=3000m,水泥返高h=2000m,套管外径D=139.7㎜,套管壁厚δ=9.17㎜,油层部位套管钢级P110(758MPa),其它部位套管钢级N80(552MPa)。油层静压Pr=40MPa,沿井筒平均地层压力系数1.2,油井寿命20年。
套管抗外挤强度经验计算公式为:
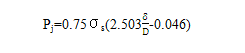
式中:
Pj—套管的抗外挤强度,MPa
σs—屈服应力,MPa。
假定腐蚀仅从内部发生,抗挤毁强度安全系数取1.125 。首先计算以上二种危险工况下套管的允许极限剩余壁厚,然后求出20年平均腐蚀速率,计算结果见表1。
表1 二种工况下套管允许腐蚀速率计算结果
工况 | 原始壁厚 mm |
剩余壁厚 mm |
被腐蚀厚度 mm |
20年平均腐蚀速率 mm/a |
工况Ⅰ | 9.17 | 6.22 | 2.95 | 0.1475 |
工况Ⅱ | 6.99 | 2.18 | 0.109 |
3.2 现场使用缓蚀剂取得的控制腐蚀速率值
为了控制CO2腐蚀,科学工作者针对不同油田的腐蚀环境,开发出了多种类型缓蚀剂,包括通常采用的油溶性、水分散剂型缓蚀剂(常用长链脂肪酸),如胺类、酰胺类、亚胺类、咪唑啉等有机长链化合物,还有有机磷酸盐。缓蚀剂全面地减缓了CO2对碳钢的腐蚀,缓蚀率一般达到80%以上,优选的缓蚀剂的缓蚀率可达90%以上。
缓蚀剂在现场应用中也表现了较好的效果。
草舍油田泰州组油藏于2005年7月开始CO2驱试验,注入方式为水气交替注入,综合含水率51%。通过室内实验,评价出HS-20型CO2高效缓蚀剂并在现场应用,浓度为50~200μL/L。监测结果表明,井下油管腐蚀速率为0.01~0.001mm/a。
吉林油田黑59块CO2驱试验区,注CO2前产出水对碳钢的腐蚀速率就达到0.5~0.7mm/a,通过缓蚀剂优选和加注工艺优化,现场应用的FRD-10型缓蚀剂将CO2腐蚀速率控制在了0.0067~0.0125mm/a 之间。
四川气田是典型的含硫气田,其几个主力气田均存在较为严重的腐蚀,其天然气中含CO2 0.1%~ 4. 69%,通过井下加注缓蚀剂防腐,监测腐蚀速率为0.0066~0.0081 mm/a。
现场应用表明,通过优选、复配适用的缓蚀剂,配套优化缓蚀剂加注工艺,CO2对碳钢的腐蚀速率一般可控制在0.01 mm/a左右。
3.3 腐蚀速率控制值的讨论
对于发生均匀腐蚀的材料来讲,通过选取最危险工况条件下油套管的强度计算,所获得的20年寿命周期内允许的平均腐蚀速率,完全可以满足安全生产需要,可以作为选材依据。
对于发生非均匀腐蚀的普通碳钢来讲,不能把获得的20年寿命周期内允许的平均腐蚀速率来作为选择缓蚀剂的依据。实验研究表明,CO2对碳钢的腐蚀形态主要是点蚀、台地腐蚀和全面腐蚀,在腐蚀较严重的环境,点蚀的平均腐蚀坑深是平均腐蚀速度的10倍以上,台地腐蚀的平均腐蚀坑深是平均腐蚀速度的2倍以上。即使使用缓蚀剂,也不能阻止点蚀或台地腐蚀的发生。按照上述实验成果并结合表1中的计算结果,点蚀的数学累积深度分别会达到29.5mm(采油井)/21.8mm(注气井),这显然会造成油套管的早期腐蚀穿孔。
如前所述,现场科学地使用缓蚀剂能够使CO2对碳钢的腐蚀速率控制在0.01 mm/a左右。这一数据仅是强度计算所获得的20年寿命周期内允许的平均腐蚀速率的10%左右,显然满足生产过程对油套管的强度需求。按照点蚀坑深是平均腐蚀速度的10倍来计算,20年的最大坑深的数学累积深度为2mm,也不会造成管材腐蚀穿孔。实验室筛选缓蚀剂,模拟现场腐蚀最严重的工况,由于实验时间短,所获得的腐蚀速率会较现场实际应用的真实腐蚀速率高。因此,就CO2缓蚀剂优选来讲,没有一个合适的、可以作为标准的控制腐蚀速率值,从经济性、技术性和安全性三个方面综合考虑,优选出最优的缓蚀剂更为恰当。
4 结论
0.076mm/a 来自于标准SY/T5329-2012《碎屑岩油藏注水水质推荐指标及分析方法》,它是基于水质的其它控制指标达到标准后的一个必然数值,直接把它作为CO2驱油田腐蚀环境下的选材与腐蚀控制衡量指标是不合理的。
对于发生均匀腐蚀的材料,通过最危险工况条件下油套管的强度计算所获得的寿命周期内允许的平均腐蚀速率可以作为选材依据。
没有必要设定一个平均腐蚀速率标准值来作为CO2驱油田腐蚀环境下优选、评价缓蚀剂的衡量指标。从经济性、技术性和安全性三个方面综合考虑科学选用缓蚀剂,更具有实际意义。
责任编辑:田双
《中国腐蚀与防护网电子期刊》征订启事
投稿联系:编辑部
电话:010-62313558-801
邮箱:ecorr_org@163.com
中国腐蚀与防护网官方 QQ群:140808414
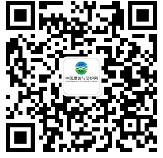
官方微信
《中国腐蚀与防护网电子期刊》征订启事
- 投稿联系:编辑部
- 电话:010-62313558-806
- 邮箱:fsfhzy666@163.com
- 中国腐蚀与防护网官方QQ群:140808414