海底管道与岸上或海上平台的生产设备之间的连接管路或挠性软管称为管道立管,区别于连接海底井口与平台或浮体之间的钻井隔水管立管。立管系统包括立管管段和支承构件两部分,立管管段由海底管段、过渡段、垂直管段、甲板管段及膨胀弯管等组成。海底管段是与海底完全接触或完全埋入海底的部分,它是完全固定的管段,作为立管系统的边界嵌固点。过渡段是从嵌固点到平台垂直立管间的管段,包括膨胀弯,它可以沿轴线移动。甲板管段是平台甲板上的管段,它可加强立管端部的刚度。本文检测和研究的对象主要针对于管道立管的垂直管段,目标垂直管段如图所示。
目标垂直管段图
工业生产中应用各种各样的无损检测(NDT)技术对立管系统进行检测。虽然检测技术不能够提供实时检测信息,只能提供检测那一时刻或者时间段立管的动力响应或者结构损坏程度,但有计划间断性的检测数据却能为立管完整性管理提供评估基础数据。目前,挪威船级社标准DNV-RP-F206是立管完整性管理的指导性文件,标准对检测方法有较为系统的描述,通常使用的检测方法有:直观检测技术(VIT)、超声波检测(UT)、电磁场检测、电场测试、磁场检测和放射线检测(RT),在具体使用中,可根据下表各种检测方法特性选择检测方法,以达到预期效果并能够满足完整性管理要求。
笔者采用的是远场涡流检测方法(RFT)对立管进行腐蚀缺陷检测,也是国内首次对在服役的立管进行RFT。为了给立管的完整性评估提供可靠的数据,还用有限元方法对立管腐蚀缺陷进行三级评价。综合考虑了环境影响因素和功能施加载荷对管道的作用,除了传统分析方法考虑的内压外,还需对管道有限元模型施加一定的轴向力,对于特殊管段还需施加弯矩。现实中管道的腐蚀缺陷形状不甚规律,用实际几何模型模拟几乎不可能,在建立有限元实体模型需对其进行简化处理,在ANSI/ASME中,腐蚀缺陷通常理想化成半椭球状。根据B31G准则,应对短缺陷用椭圆抛物线形模型进行模拟,对长缺陷应用长方形模型进行模拟。
对于缺陷深度,ASME中规定,当腐蚀最大深度小于壁厚的20%时,含该缺陷的腐蚀区的管道仍可使用。当腐蚀最大深度大于壁厚的80%时,含该缺陷的腐蚀区的管道必须更换或者修复,而在实际工程中,缺陷深度一般小于70%。对于腐蚀环向宽度,在内压作用时,环向宽度对极限载荷影响很小。而在有弯矩作用时,环向宽度对极限载荷有较大影响。由此,对腐蚀立管进行模拟有限元分析,首先需要对立管进行简化,以方便进行计算。以下是笔者用有限元建立的长/短缺陷网格及Mises应力云图。
有限元建立的长/短缺陷网格及Mises应力云图
立管与普通长输管线,海底埋地管道所研究侧重点略有不同,现有的标准规范并不能对径厚比小,高强度钢材,甚至具有一定不直度的立管尤其是管道立管,进行准确的评价。需要运用有限元仿真模拟的计算方法,准确的施加环境载荷和功能载荷共同作用产生的内压,轴向力和弯矩,才能较为客观的反映出管道的疲劳强度和剩余寿命,对腐蚀管道做出3级评价,为立管完整性管理提供确实可靠的数据。
责任编辑:田双
《中国腐蚀与防护网电子期刊》征订启事
投稿联系:编辑部
电话:010-62313558-801
邮箱:ecorr_org@163.com
中国腐蚀与防护网官方 QQ群:140808414
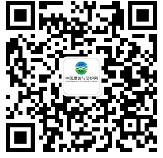
官方微信
《中国腐蚀与防护网电子期刊》征订启事
- 投稿联系:编辑部
- 电话:010-62313558-806
- 邮箱:fsfhzy666@163.com
- 中国腐蚀与防护网官方QQ群:140808414