近些年来,我国在材料领域的基础研究取得了非常大的进步。据不完全统计,我国在2019年的论文数就超越了美国,遥遥领先于其他国家。但是,论文数量仅仅是材料领域进步的冰山一角,解决重大工程的掐脖子问题并将其应用在大国重器上才是一个国家进步的根本体现。在国家最新的十四五规划中,科技部和工信部已经把解决“卡脖子”技术列入了重要研发项目之中。同时,清华大学,上海交大,西工大等全国985著名高校正式将 “破五唯”体制列入规划。由此可见,以论文论英雄的时代即将结束,取而代之的则是代表作、成果转化以及科技产业经济化。其实,近些年来,我国在“国之大器”,“卡脖子”等技术问题上还是取得了不少突破,有些打破了国外垄断,有些则是首创,达到了国际先进或者领先水平。笔者今天给大家分享的正是这些花费科学家无数心血,但可歌可泣的技术以及背后的故事。
1)中国科学院金属研究所李依依院士,李殿中和孙明月等人在国际上率先制备无焊缝整体不锈钢大环
第四代核电具有许多优点,例如安全可靠,能源利用效率高且可持续性发展,许多国家,如美国、法国、日本等正在加快第四代核反应堆的建设。建造超大型核反应堆的需要相应地结构材料,其中一个关键问题是用于制造反应堆部件的重型工程结构的实用性。支撑环是反应堆的关键重型结构部件,可支撑整个反应堆容器和内部的7000多吨重量。此外,它也是反应堆容器的边缘,在工作条件下会承受高压,高温以及其他飓风荷载,地震荷载和静荷载。因此,支撑环的安全性和稳定性对于核反应堆至关重要。由于支撑环的最大直径可达15.6 m,因此理论上将消耗200吨以上的不锈钢。但是按照目前的冶炼技术,要实现他的一体成型技术,做出不含成分偏析、缩松和缩孔等缺陷的大环材是不可能的。以前,最常用的方法是制造焊接类型的支撑环,但是由于多次纵向焊接,支撑环的安全性和稳定性将大打折扣。这会造成材料的寿命缩短,严重造成资源浪费,给四代核电的发展形成空前的挑战。中国科学院金属研究所李依依院士,李殿中和孙明月研究员等人独辟蹊径,在全球率先发明金属构筑成形技术。该技术以多块小尺寸均质化板坯作为基元,通过表面活化 、真空封装、高温形变等手段,使构筑界面与基体完全一致,进而获得大锻件所需均质化母材,实现“以小制大”的新型制造。实现了世界上最大的整体式无焊支撑环(φ= 15.6 m)构筑成型。与必须通过较大的毛坯进行重型锻造的传统观念形成鲜明对比的是,该技术的核心思想是通过建造更小,更便宜的金属板来制造大型的高质量零件。在这个巨型环上,根本不存在所谓的焊缝,整体性能得到了显著提升,已经成功的运用于我国的第四代核电站反应堆制造,取得了显著的经济效益。得到了多位院士专家及企业的认可,并被评价为大构件制造领域的一项变革性技术。该技术具有低成本、高品质、质量稳定及绿色环保等优势,成为当前大环件制造的一种重要新兴技术。然而,虽然金属构筑技术能够制造高品质大型锻件钢坯,但由于该技术需要采用真空电子束封焊,对于一些难焊、不可焊金属,采用构筑技术则不能实现。该技术入选“共和国成就发展巡礼”,在央视多次播出。未来,这项技术有望解决舰船、核电、航天等战略性装备核心部件制造的难题,使我国工业发展实现质的飞跃。

图1 采用多层热压粘结法制造无焊缝不锈钢锻造环的工艺。首先对316不锈钢铸坯表面进行清理、整齐堆放,然后用电子束焊机进行真空封装。然后对整个包体进行热压粘合,界面完全愈合后成型为初始坯料形状进行二次热压粘合。接下来,两个初始的钢坯再被电子束焊机真空包装,然后热压结合成环轧制所需的大钢坯。随后进行冲孔、拉削、轧制,最终得到一个完整的支撑环[1]。
2)金属所杨锐教授突破TiAl航空发动机叶片一体成型技术
航空发动机是飞机的心脏,而涡轮叶片又是发动机的心脏。这款心脏的动力往往取决于制备它的材料是否过关。目前,航空发动机的压气机和低压涡轮轮叶片采用的是镍基高温合金。这种合金在600-1000℃范围之类具有较高的强度和耐蚀性,但镍的密度大,质量重。众所周知,减重是航空工业一直追求的目标。我国首款五代机歼20总师杨伟曾说过,减重飞机一克价值一两黄金。由此可见,减重在航空工业是多么的重要。相较而言,钛铝合金的密度仅为镍基高温合金的一半,而且在650-850℃的服役温度范围内,具有更优异的力学性能,让其替代镍基高温合金则会大幅度的实现发动机的减重,提高飞机能源利用率(约为30%)。因此,用钛铝合金做发动机叶片一直是国内外航空发动机生产商的追求。为了降低成本,还要求叶片一体成型。而钛的活性极强,只有氧化钇一种材料可以作为制作叶片的容器,可这种材料表面是粉末状的,会影响叶片精度,德国科学家甚至通过计算机模拟得出结论,这是不可能完成的任务。中国科学院金属研究所研究员杨锐带领多个学科的科学家,历经10年的时间,经过无数次失败之后,终于成功调制出一种粘结剂,解决了钛铝合金叶片的容器问题,成功了实现叶片一体浇筑成型,完成了这个不可能完成的任务。他们终于破解让氧化钇不再掉渣的难题,一体成型的钛铝合金叶片也随之诞生。虽然这只是一个开端,但让中国人有勇气展望未来属于自己的航空发动机。
3)西工大刘东团队强力旋轧技术(PTR)破解国内高端轴承钢难题
从汽车、高铁、飞机到仪器仪表、机械装备,你几乎能从所有旋转的机械中寻找到一个共同的核心部件——轴承。而制造轴承所需的材料——轴承钢,被誉为“钢中之王”。一直以来,高质量的轴承钢的生产技术被国外巨头卡脖子。很多国内企业无法从国内厂家寻求到符合高使用需求的轴承钢,不得不花高价进口,这使得他们叫苦连连。拥挤自主产权的核心技术,摆脱对国外的依赖,一直是人们的愿望。虽然我国很早就已经成为了“钢铁大国”,但是距离“钢铁强国”的梦想还有一段路要走。一直以来,我国所生产的轴承钢质量与国际先进水平有较大差距。以夹杂物为例,国外产品夹杂物尺寸完全小于等于10微米,而国内最大粒径达到50-52μm,大小相差五倍之多。轴承的工作环境严峻而复杂,不仅需要高速稳定的旋转,而且还要承受强力的挤压、摩擦,甚至超高温的历练。因而对轴承钢的质量和可靠性提出了更为严苛的要求。就在今年,西北工业大学材料学院刘东教授和其团队研发的强力旋轧技术(PTR),打破国外巨头技术垄断,突破我国轴承钢“卡脖子”技术,成功了破解行业难题。如何生产高质量的轴承钢?一是内部足够纯净,夹杂物质越少越好;二是足够均匀,材料内的颗粒物尽量细小、弥散。“强力旋轧技术”利用曼内斯曼效应,在径向轧制的同时施加强力旋转,依靠连续局部压扭复合变形,实现轴承管材碳化物均匀细小弥散。就像在揉面的时候让面的3个方向都变形,而且变形数值非常大,这样就可以把面揉的又透又劲道。刘东教授和团队“十年磨一剑”,经过不断攻关测试,终于突破技术瓶颈,研究出3个世界首创,申请到66项发明专利,强力旋轧技术就是其中一项。运用强力旋轧(PTR)技术,晶粒尺寸可由原来的50μm细化至10μm,碳化物尺寸仅为原先的1/10。首次将100年来,一直徘徊在600-700HV的GCr15轴承钢硬度提高至900HV以上,处于世界顶尖水平。除此以外,采用该技术后轴承寿命和可靠性得到大幅度提高,平均寿命达到计算寿命的26倍,可靠性达99.9%。更令人惊喜的是,本技术可以显著提高材料利用率,且生产流程可缩短2/3,真正在绿色发展上见实效。通过这项技术改性后的轴承钢已在多个项目中得到运用,完全能够满足高端质量要求,将该技术运用到其他材料中,也取得了非常良好的效果,运用于钛合金和高温合金中属于世界首创。
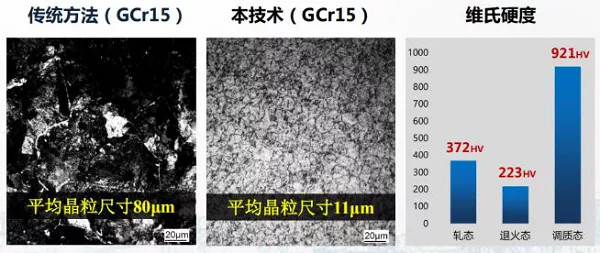
图2 较于传统技术,PTR技术单道次晶粒细化程度高[2]
另外,经过长期的科研攻关,刘东教授团队还先后突破近10项关键技术,极大地提升了航空发动机性能,让着颗现代工业皇冠上的明珠更亮、更耀眼。出于保密原因,这些关键技术叫什么名字,通过哪些工艺实现,笔者在这里不得而知。唯一知晓的是在2020年1月,因为这项贡献,团队负责人刘东教授在人民大会堂,从国家领导人手中,接过国家级获奖证书。
4)由西南铝牵头研究开发的5m级铝合金异形环试制取得重大突破;
铝合金在生活中非常常见,同时高质量的铝合金在航空航天等工业有着非常重要的应用。到目前为止,铝合金的大规格棒材,板材均已经成熟,但是大规格铝合金异形环件在国内研究尚为空白。大规格环材在航天事业上可谓要求迫切。但要突破这项技术,需从锻造开坯、异形环轧制、热处理方面开展系统的研究工作,技术难度非常大。现阶段的工业中大型环件多为矩形环件,厚度大,稳定性差,不能满足高性能轻质火箭要求,而一体成型的异形环件,材料利用率高,且在性能和流线上都具有较大优势。为此,西南铝通过仿真模拟辅助轧制成形技术,设计出了6种坯料的形状尺寸、模具,在建立环件轧制仿真过程中,应用单一变量原则对驱动辊转速、芯辊进给速度、抱辊运动曲线等参数进行优化设计,制定合理的生产工艺。经过3年的反复攻关,西南铝根据试制结果不断调整优化方案,解决了异形环件在生产过程中产生振动、爬辊等问题,获得了成形效果良好、性能稳定的环件,为后续生产奠定基础。此异形环件为某重点型号工程用关键构件--贮箱过渡环。相比传统矩形环件,此异形环件投料节省40%左右,大大减小投料铸锭直径,增大变形程度和提高热处理效果。
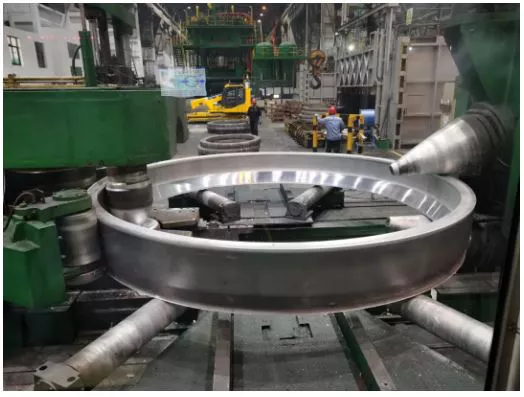
图3 西南铝牵头研究开发的5m级铝合金异形环[3]
5)金属所钛合金团队在“奋斗号”万米全海深钛合金取得突破;
全海深载人潜水器是难度极高的工程装备,尤其是在潜入海深10000米时,材料将受到巨大的水压,这就要求其具有非常高的强度,另外为了成型,材料还必须要有良好的塑性。另外,材料的焊接性必须良好,且焊接后的焊缝必须要具有良好的性能。要开发出这样综合性能优异的材料,对材料专家来说,挑战难度非常大。由金属所牵头,联合宝钛股份有限公司和中国船舶集团公司洛阳船舶材料研究所,发挥三家单位的技术优势,组建了全海深钛合金载人舱研制国家队,开发并集成应用了多项钛合金材料技术和焊接加工技术,攻克了一系列关键技术瓶颈,填补了多项国、国际技术空白,整体达到了国际领先地位水平,揭开了深海材料的划时代意义。其研制Ti62A钛合金,其韧性和可焊性与Ti64相当,强度提高20%。成功解决了载人舱材料所面临的强度、韧性和可焊性等难题。
6)潘锦功成功研发碲化镉太阳能发电玻璃,发明34项自主专利
说起钱学森,在科技界恐怕无人不知,无人不晓。他为我国的两弹一星事业做出了极大地贡献,具体涉及到航天、导弹以及火箭。可以说,他的回归,直接让中国的航天事业提前推进20年。对于这样一位爱国的科学家,笔者心里由衷的敬佩。其实中国又出了一个“钱学森”,他就是“发电玻璃”的创始人潘锦功。
煤、石油为不可再生资源,随着社会的发展,他们的储备早已入不敷出,逐渐枯竭,寻找可再生能源已是迫在眉睫。太阳能是一种取之不竭,用之不尽的能源,是目前为止最为安全、高校以及环保的资源,超越了风能和核能。目前所用的太阳能电池板价格高昂,而且转化率也不高。
在潘锦功博士及其团队的努力下,2017年他们制作出具有中国完全自主知识产权的“发电玻璃”。这项技术领先国际,可以为未来的能源问题提供一条坦途。可以毫不夸张地说,这项发明足以改变世界。这种发电玻璃制备工艺简单,只需要在普通普通玻璃上,均匀涂抹4微米厚的碲化镉光电薄膜。而且生产一块面积1.9平方米的发电玻璃,只需要55秒。它可以用于可导电,可发电的半导体材料。同时,这块玻璃的光电转化率达到17.8%,足以媲美传统太阳能板。1.92平方米的“发电玻璃”,每年产生260度到270度的电,只需两三块就能供一个家庭的全年用电,三四千块玻璃的发电量堪比一口普通油田一年产油所转化的电量。
现代的城市生活可谓是灯红酒绿,各种商业活动,居民用电等严重消耗着世界的能源。如果将建筑物中的玻璃,全部改为发电玻璃,就可以大大节煤炭发电厂的能源,而且很方便的给用户提供电力保障。有人统计过,中国将近有400多亿平方米的建筑,如果全部改为发电玻璃,其发电量相当于建设30个三峡水电站。如此一来,每年将节约的资源堪称天文数字,除了用在建筑上之外,这种玻璃还能用于军事。在野外,只需要带上一小块玻璃,就能够保障军区通讯基站的用电需求。它甚至还能被铺在路面上,如果用于电动汽车,那么这样的路面可以别随时用作移动充电站。甚至于将汽车玻璃改造成“发电玻璃”。能够直接为汽车提供能源。看完这些,大家恐怕就知道这款发电玻璃有多魔性了吧。
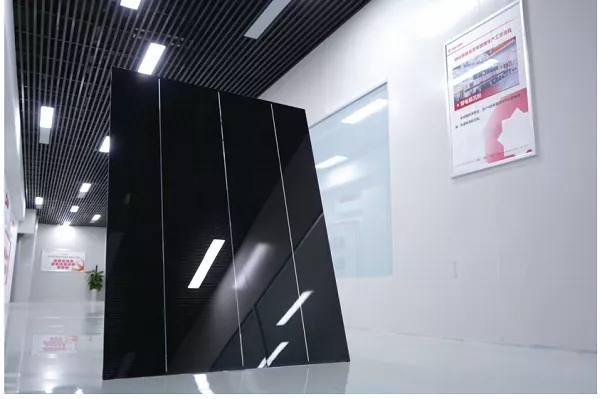
图4 普通发电玻璃展示 [4]
参考文献:
[1] Mingyue Sun, Bin Xu, Bijun Xie, Dianzhong Li, Yiyi Li. Leading manufacture of the large-scale weldless stainless steel forging ring: Innovative approach by the multilayer hot-compression bonding technology. Journal of Materials Science & Technology 71 (2021) 84–86.
[2] 西北工业大学公众号,2021.03.31
[3] 中铝西南铝业官网。
[4] 叶涛,周书婷, 四川省创新专家、 成都中建材光电材料有限公司总经理潘锦功:用材料革命推动产业革命。《产城》,2019.
免责声明:本网站所转载的文字、图片与视频资料版权归原创作者所有,如果涉及侵权,请第一时间联系本网删除。
相关文章
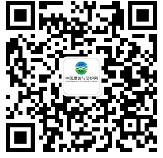
官方微信
《中国腐蚀与防护网电子期刊》征订启事
- 投稿联系:编辑部
- 电话:010-62316606-806
- 邮箱:fsfhzy666@163.com
- 中国腐蚀与防护网官方QQ群:140808414
点击排行
PPT新闻
“海洋金属”——钛合金在舰船的
点击数:7130
腐蚀与“海上丝绸之路”
点击数:5741