导读:本文开发了新研制非等原子Fe40Ni20Co20Cr20(at.%)高熵合金(HEA),发现断裂伸长率大于70%的强韧性协同效应是由位错活动和纳米孪晶介导的。浸泡试验表明,与等原子铁镍钴合金相比,该合金的耐蚀性显著提高,在0.1M H2SO4溶液中的电化学耐蚀性高于316L不锈钢。除钝化膜中Cr3+含量高外,Co与其它元素的相互作用有可能导致Co(Fe,Cr)2O4的形成,提高钝化膜的稳定性。
高熵合金的概念为合金设计提供了新的思路。它打破了传统的一元或二元合金的限制,因为多个主元素在HEA体系中起作用。最初,以稳定的单相固溶体构型熵最大化为出发点,等原子多主元被主要考虑在HEAs的设计中。近年来,发展具有单相、两相或多相固溶体的非等原子HEA是一个新的趋势,这增强了HEA设计的灵活性。这种非等原子高温合金极大地拓宽了高温合金的成分空间,因此为了进一步提高其性能,即比等原子高温合金具有更高的强度和延性、更好的耐腐蚀性能和更高的耐磨性,人们对新型非等原子高温合金的探索也越来越多。
在以往面心立方(FCC)结构HEAs的设计中,Mn对调整HEAs的微观结构以提高其力学性能起着非常重要的作用,如通过降低HEAs的层错能(SFE)来产生TWIP或TRIP效应。然而,HEAs中的Mn通过抑制钝化行为和降低钝化膜的稳定性而显著阻碍了其耐蚀性。这可能与Mn3O4的不稳定性有关,它通常在表面形成保护性Cr2O3之前形成。因此,尽管已经报道了一些含锰的高强度和/或高延展性HEA,但它们中的大多数在防腐性能方面会受到限制。文献综述表明,在以往的研究中,对新型HEAs的研究很少能达到耐蚀性与力学性能之间的平衡。例如,AlxCoCrFeNi(x=0.3、0.5和0.7)在3.5 wt.%NaCl中表现出良好的耐腐蚀性,但由于脆性BCC共晶相,延展性较差。在掺Mo的FeNiCoCr合金的情况下也报告了类似的情况。此外,FeCoNiCrCux系统(x?=?0、0.5和1)中Cu的合金化不仅加速了局部腐蚀,而且由于富Cu枝晶间相的形成而恶化了塑性。事实上,机械性能和防腐蚀性能的良好结合对于在恶劣环境中使用的结构材料是必不可少的。因此,探索具有优良力学性能的耐蚀合金具有重要意义。
中南大学李志明教授团队研制了一种新型耐腐蚀非等原子Fe40Ni20Co20Cr20 (at.%) HEA。该成分来源于FeMnNiCoCr体系,其中Fe、Cr和Ni成分是耐腐蚀316L不锈钢(SS)的基本成分,而Mn则恶化了耐腐蚀性能。在本研究中,为了追求更好的耐腐蚀性,去除了锰,并将铁含量提高到40%,与等原子铁相比,降低了成本。Co的合金化可以有效地调节合金的结构。多个机构协同工作,实现了良好的强度延展性协同。 新研制的非等原子HEA在浸泡试验中的耐蚀性明显高于等原子FeMnNiCoCr HEA,在0.1 M H2SO4溶液中的耐蚀性也明显高于316L不锈钢。相关研究成果以题“A non-equiatomic FeNiCoCr high-entropy alloy with excellent anti-corrosion performance and strength-ductility synergy”发表在腐蚀顶刊 Corrosion Science 上。
论文链接:
https://www.sciencedirect.com/science/article/pii/S0010938X21001074
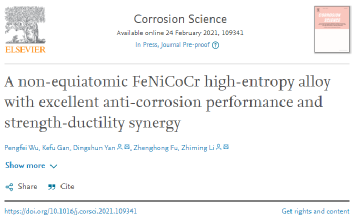
图标题:
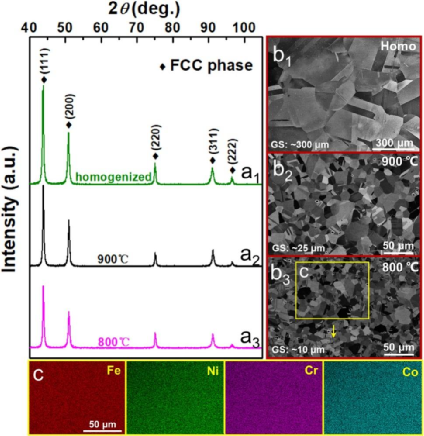
图1.(a)不同加工条件下HEA样品的XRD图谱和ECC图像。(a1,b1)均质化;(a2,b2)900℃退火30分钟;(a3,b3)800℃退火30分钟。(c)四种元素对应于(b3)中黄色矩形标记的相同样品区域的EDS图。“GS”和“Homo”是指晶粒尺寸和均质化条件。
图2a展示了通过各种加工路线获得的HEA样品的代表性工程应变-应力曲线。均质的900℃和800℃退火的HEA样品的屈服强度(YS)值分别为?161 MPa,?208 MPa和?281 MPa,表现出明显的Hall-Petch关系。在900℃(?71%)退火的HEA样品的断裂伸长率比在800℃(?65%)退火的HEA样品的断裂伸长率稍高,而极限抗拉强度(UTS)(?560 MPa)降低了约50 MPa。vs.?610 MPa)。值得注意的是,所有HEA样品均显示出非常高的延展性,且伸长率值大于65%。特别是,均质样品的伸长率约为80%。在后面的部分中将揭示造成当前HEA高延展性的机制。
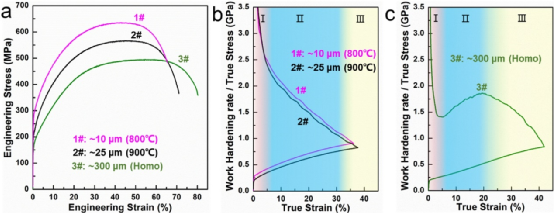
图2.(a)不同加工条件下试样的工程应力应变曲线;(b)和(c)是与(a)中工程应力应变曲线相对应的真应力和加工硬化率。“Homo”指的是均匀化状态。
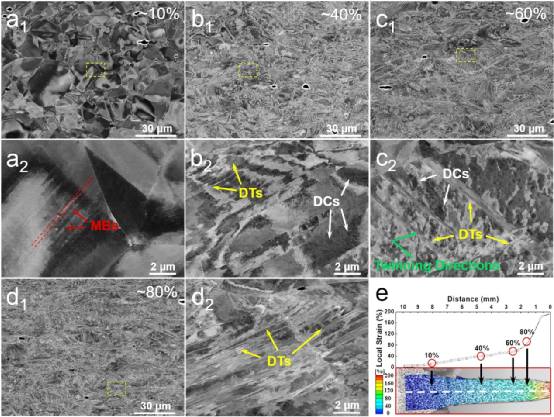
图3. 不同局部应变样本区域的ECC图像。(a1-2)~10%;(b1-2)~40%;(c1-2)~60%;(d1-2)~80%;(e)在900℃退火30min的典型拉伸试样的局部应变分布。“MBs”、“DTs”和“DCs”分别指微带、变形孪晶和位错胞。
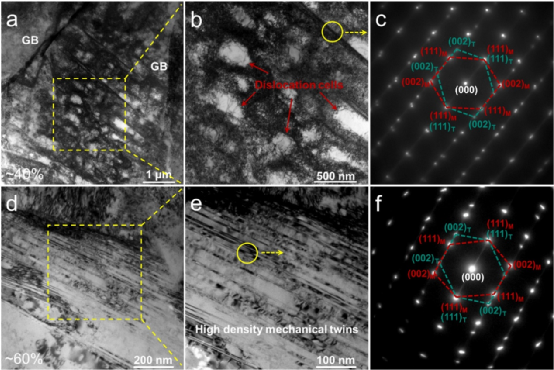
图4. 拉伸试验后900℃退火HEA样品在(a,b)~40%和(d,e)~60%局部应变下显微组织的亮场TEM图像。(c) 和(f)为分别从(b)和(e)中黄色圆圈区域沿[011]区域轴拍摄的SAED图案。“GB”指晶界。
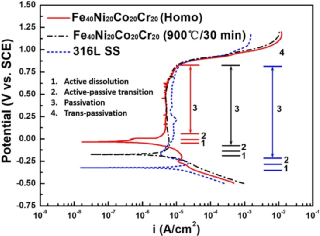
图5. 均匀化HEA、900℃退火HEA和316L不锈钢在0.1M H2SO4溶液中的室温动电位极化曲线。“Homo”指的是均匀化状态。
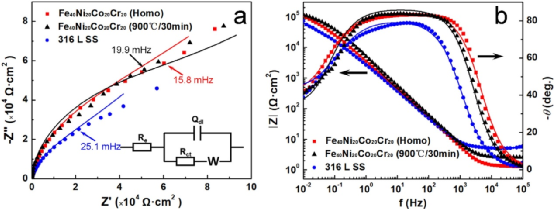
图6.(a)均质HEA,900℃退火的HEA和316L SS在OCP条件下在0.1M H2SO4溶液中的奈奎斯特图和(b)波德图。实线表示拟合结果,“Homo”表示均质状态。
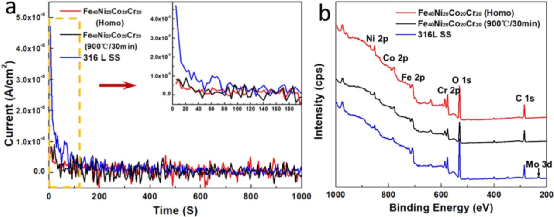
图7.(a) 时间-电流曲线(0-1000 s);(b)恒电位极化后HEA和316L SS的典型XPS测量光谱(在0.1 M H2SO4溶液中在0.5 VSCE下进行5000 s的实验)。“Homo”指的是均匀化状态。
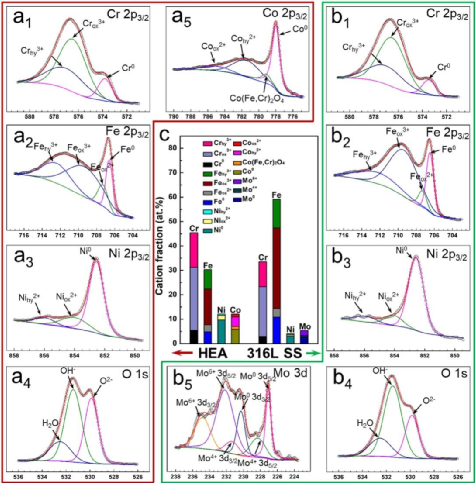
图8.(a1-5)HEA和(b1-5)316L SS钝化膜在室温0.1M H2SO4溶液中经0.5VSCE钝化5000s后的高分辨率XPS光谱(x轴和y轴分别代表结合能(eV)和强度(a.u.);(c)XPS分析所得HEA和316L SS钝化膜中的阳离子组分。
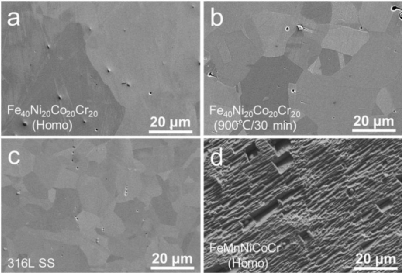
图9.(a)均匀化的Fe40Ni20Co20Cr20(at.%)HEA;(b)900℃退火的Fe40Ni20Co20Cr20(at.%)HEA;(c)316L不锈钢和(d)等原子FeMnNiCoCr HEA在0.1M H2SO4溶液中室温浸泡30天后的表面形貌。“Homo”指的是均匀化状态。
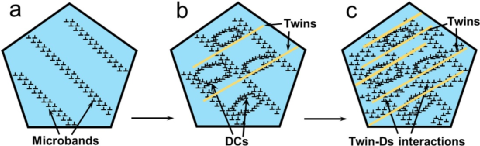
图10. 说明均匀拉伸变形后微观结构演变的示意图。“DCs”和“Ds”分别指“位错单元”和“位错”。
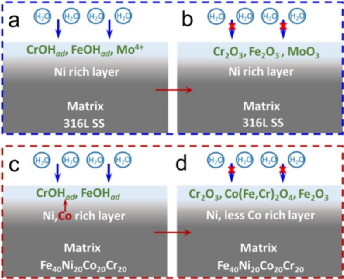
图11.(a,b)316L SS和(c,d)HEA钝化工艺示意图。
在这项工作中,我们开发了一种新的Fe40Ni20Co20Cr20(at.%)HEA,它具有良好的耐蚀性和良好的强韧性协同作用。揭示了拉伸变形后的显微组织,以了解其变形机理。采用电化学方法和浸泡试验对其在0.1M H2SO4中的耐蚀性能进行了评价。主要结论如下
(1)在非等原子Fe40Ni20Co20Cr20(at.%)HEA中可以获得均匀的单相FCC固溶体。在早期拉伸变形阶段,位错滑移是主要的机制。细胞结构和机械孪晶也随着进一步的拉伸而形成,提高加工硬化能力。多个机构协同工作,实现了良好的强度延性协同。
(2) 新研制的非等原子HEA在浸泡试验中的耐蚀性明显高于等原子FeMnNiCoCr HEA,在0.1 M H2SO4溶液中的耐蚀性也明显高于316L不锈钢。HEA中Ni含量高,钝化膜中Cr3+含量高。Co与其它元素的相互作用促进了Co(Fe,Cr)2O4复合氧化物的形成,形成了致密的钝化膜。此外,钝化膜中的结合水对耐蚀性也有重要的贡献。多主元素合金的设计可提供获得稳定钝化膜的方法,以确保高耐蚀性和良好的机械性能。
免责声明:本网站所转载的文字、图片与视频资料版权归原创作者所有,如果涉及侵权,请第一时间联系本网删除。
相关文章
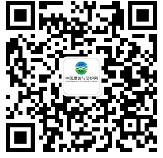
官方微信
《中国腐蚀与防护网电子期刊》征订启事
- 投稿联系:编辑部
- 电话:010-62316606-806
- 邮箱:fsfhzy666@163.com
- 中国腐蚀与防护网官方QQ群:140808414
点击排行
PPT新闻
“海洋金属”——钛合金在舰船的
点击数:7130
腐蚀与“海上丝绸之路”
点击数:5741