随着中国科技实力的大力提升,各个领域都取得了一系列成绩。就材料领域来说,过去一年,不仅电极,催化,能源等功能性质的材料不断有顶刊登上,在结构金属材料的研究也不断有好消息传来。众所周知,相对于生化环材、能源以及催化等的研究,金属材料经过几十年的沉淀,要想登上Nature&Science两大顶刊,难度之大,可谓难于上青天。但金属材料作为最基本也是最具有支柱性的材料,对其进行充分研究,可以极大地促进国民经济和国家综合实力。尽管关于金属材料的研究已经成熟,创新难度非常大,过去一年,还是有学者突破瓶颈,取得了重大原创性成果。今天笔者梳理了过去一年结构金属材料的突破性成果,以启迪大家,看看在金属材料界,什么样的研究可以发世界级顶刊。
1 孙文文博士于2019年3月份在Science期刊上发文,该研究的主要贡献是发现一种新型的沉淀析出强化方法。
本科毕业于中南大学的孙文文博士于2019年3月份发表在Science期刊上发表《Precipitation strengthening of aluminum alloys by room-temperature cyclic plasticity》的论文。该研究的主要贡献是发现一种新型的沉淀析出强化方法。众所周知,固溶强化是金属材料的四大强化方式之一,在铝合金的增强增韧中有着非常重要的作用。100年来,材料科学家通常通过固溶时效的方法在材料基体中引入析出相来强化合金。但固溶时效这种方法存在很大的缺陷。它是一个热驱动力和相析出长大的动态平衡过程。一般来说,相析出的驱动力随着固溶饱和度的增加而增加,析出相需要克服的势磊随温度的降低而降低。这个过程需要成分梯度和空位,又温度提供的驱动力和原子扩散控制。所以传统的固溶时效浪费能量,而且析出相的分布很难均匀,强化效果非常不稳定。孙文文博士的研究结果表明:铝合金可以在室温和几分钟内完成加工,同时获得强度和伸长率相当于或超过热处理相应合金的最高强度状态,如图figure 1 所示。其方法是使用轴向液压疲劳机施加交变应力(CS处理),在室温条件下诱导可控的微尺度往复位错运动。位错偶极子的拖拽产生有利于铝在室温下扩散的空位。同时材料在重复循环变形注入空位,在高驱动力下发生扩散产生溶质聚集,从而大大增强了合金的强度,她们称之为循环强化。
通过对CS处理的铝合金样品进行显微表征(LAADF-STEM以及APR)发现,合金内部存在位错环和1-2nm的固溶团簇,这两种结构形成是由于空穴不断被注入系统,簇在形成过程中不断被移动位错剪切。它们在材料变形时阻止了位错的运动,从而造成材料的强化。
Figure 1 合金在传统热处理和CS方法下的力学性能[1]
2 2019年7月份,西安交大单智伟等在利用锥面位错提高镁的塑性取得重大进展。
西安交大单智伟等人在《Science》期刊上发表名为《Large plasticity in magnesium mediated by pyramidal dislocations》的论文,主要研究了通过锥面<c+a>滑移调节镁合金的塑性;镁合金密度小,是非常典型的轻质合金,其密度是铝的75%,钢的35%,在自动化工业,航空航天工业,汽车车轮等具有广泛的应用。由于质量轻,可以大大减少能源的浪费。但是镁合金非常差的塑性是限制其大规模应用的主要瓶颈。镁合金具有密排六方结构,通常变形情况下,其<c+a>位错难以启动或者容易变为不可动结构,导致其塑性非常低。<c+a>位错能够调节沿着c轴方向的塑性应变和滑移路径,其滑移面为{10-11}和{11-22}。该研究首先使圆柱状的镁单晶与原位透射压柱的偏离角大于5°(以便使得<c>和<a>位错和孪晶难以启动)对其进行压缩,通过来分析位错的柏氏矢量。研究发现位错从柱顶区开始依次产生,并逐渐向柱底扩展。随着柱的进一步变形,由于密度过高,个别位错难以成像;很难分析这些位错的Burgers向量。为此,他们换成梯形样品,试验后发现了<c+a>位错的形核和滑移。实验中观察到的位错呈半圆环和“Z”字形状,包含刃型位错、螺型位错和混合型位错,figure 2。主要分解为如下两类:
1)平行于锥面或者基面且垂直于
这些位错属于刃型位错,可滑动。在循环载荷下,这些位错可以往复运动。这表明<c+a>位错保留他们的特性和可动性而非不可滑动。
2)平行于锥面与基面的交叉面
该类属于直线型的长片段位错,这些长片段的存在是由于c+a刃型位错的低可动性、在锥-基面形成不可动位错锁,以及c+a位错的解离形成不全位错和基面堆垛层错。这种直线形的结构也可能是位错偶极子形成的结果。当位错被钉住时,可以形成一个直的位错偶极子,偶极子及其相邻两段的排列1和2,形成了ε的形状。几何分析表明,该偶极子为纯刃型位错。在进一步的拉伸过程中,1段和2段形成了一个连接处,留下了碎片。位错偶极子和碎片都是固定的,可以作为其他位错的障碍。这种位错偶极子的形成需要两个不同的锥体平面之间的交叉滑移。
研究表明,亚微米尺寸的镁单晶比大块的镁单晶表现出更高的强度和可塑性,出现了“更小、更强、更有延展性”的现象。这种现象可能源于以下因素:1)小晶体通常很少有预先存在的位错,因此,成核位错需要很大的应力。位错一旦成核,就很容易在位错增殖之前逃逸到表面,这就需要增加应力水平来成核其他位错或激活其他位错源来继续塑性。这种尺寸效应导致亚微米尺寸Mg的高应力,从而激活大量的c+a位错以适应更大的可塑性。2)可塑性好的另一个原因是单位体积位错的丰富的表面来源,这是由于较大的表面与体积的比例,这使得大量的位错可以从晶体表面连续产生。
Figure.2 原位透射电镜显示了样品中c+a位错的运动[2]
3 2019年5月,金属所卢柯、李秀艳推动材料素化,促进材料可持续发展[3]。
在金属材料(铁,钛,镁)中添加合金元素,可以起到强化作用,其强化途径可以分为两种:一种是修正微观结构;另外一种是形成强化相,通过阻碍位错的滑动来调节力学性能。然而合金化带来的强化效果是有限的,而且通过加入合金元素强化的贵金属元素很难回收再利用,造成了资源的浪费。有些重金属甚至有毒,不利于环境保护。在资源越来越匮乏的当今时代,人们总是希望尽量节约合金元素的使用,但同时获得较高的力学性能。
沈阳金属研究所卢柯院士及其助理李秀艳提出了材料素化的战略性概念。材料强化可以通过改变晶界来实现,首先可以通过细化晶粒来增加晶界,从而阻碍位错的运动,达到强化效果。另外还可以通过修改晶界在空间的分布状态调整材料的性能,如摩擦、塑性等。当晶粒减小至临界尺寸(纳米级)时,位错的形核受到抑制,堆垛层错能驱使原子运动,材料的塑性变形机制发生了改变,此时晶界的运动主导了变形,材料反而出现了软化现象。因此,纳米材料晶界的稳定化有助于材料的强化。通过创造低能面,例如孪晶面以及小角晶界可以有效的降低晶界面的能量,另外通过晶界隔离也可稳定晶界。当位错进入低能状态时(部分位错释放),晶界出现松弛,释放出能量,从而稳定了晶界。虽然稳定晶界的机制还需要进一步探索,但是其前景确实非常诱人,一旦人们正确掌握了晶界强化,则可节省成千上万的贵金属元素成本,还可使材料具有优异的力学性能。
4 2019年10月, 浙江大学张泽院士团队余倩研究员课题组科研新进展-解码高熵合金既强又韧的关键“基因”。
原则上,高熵合金(HEAs)应该与被认为是各元素随机固溶形成单相,一般具有高强度,良好的塑性以及断裂韧性,很适合做低温结构材料。具有优异力学性能的原因主要与合金的高熵、慢扩散以及晶格畸变有关。一个根本问题是这样的固溶体是否具有多重性主元素涉及非常规的原子结构或元素分布,如局部化学排序或聚类是否会影响缺陷行为从而提高机械性能。多数理论认为它们由不同原子种类的随机分布组成,也有理论认为高熵合金中存在局部元素变化以及短程有序。如果用另一元素代替高熵合金的某一元素,随机合金效应和固溶强化理论会受到怎样的影响?该文作者首先使用能量色散x射线光谱学实验研究了CrMnFeCoNi和 CrFeCoNiPd合金中的原子尺度元素分布。研究表明:在CrFeCoNiPd合金中,通过晶格应变和浓度梯度对系统能量的竞争作用,形成了特征波长为1-3 nm的浓度波。引入Pd不仅促进了Pd的聚合,也促进了其他四种元素的聚合,导致合金中存在明显的化学不均匀性。另外,在CrFeCoNiPd合金中,由于五种成分元素间局部化学键合结构的复杂性增加,使得成分调制的规律性明显降低。
原位透射实验的结果表明:CrFeCoNiPd合金在室温下的塑性变形主要涉及1/2{111}<110>全位错,但CrMnFeCoNi合金的塑性变形则由1/2{111}<110>全位错和1/6{111}<112>不全位错控制。此外,CrFeCoNiPd中位错运动缓慢,表明存在较大的位错滑移阻力(即高晶格摩擦),这可能与CrFeCoNiPd合金中明显的浓度波动的钉扎效应有关。CrFeCoNiPd在塑性变形的早期阶段存在大量螺型位错的交滑移,交滑移主要由位错堆积形成并可以进一步转变为二次交滑移。对力学性能的研究表明,相同晶粒尺寸CrFeCoNiPd合金的强度、塑性都要优于CrMnFeCoNi合金。主要原因为:1)固溶强化在很大程度上是由合金原子和基体原子之间的尺寸和模量不匹配决定的,Pd的原子尺寸大,强化效果更加明显;2)CrFeCoNiPd合金中的Pd原子导致了更多的位错交滑移,在变形中可以阻碍位错的运动,从而提高合金强度, Pd的引入导致了所有五个元素的聚合,不均匀的成分分布修正了位错芯的γsf值,从而有降低了交滑移的能量势磊;3)非均匀的元素分布也改变了晶格摩擦的分布,使得位错运动的阻力更强。
Figure 3 CrFeCoNiPd合金与其它铬镍铁合金的力学性能比较
a. CrFeCoNiPd和CrMnFeCoN合金在室温(293k)和液氮温度下的单轴拉伸应力-应变曲线(77 K) ,平均粒径约130μm;
b. 粒径约5μm时的应力-应变曲线;
c. CrFeCoNiPd合金与其它相关HEAs的屈服强度比较;
d. CrFeCoNiPd与CrMnFeCoNi合金的原子应变分布比较[4]。
5 2019年12月,皇家墨尔本理工大学增材制造中心Mark Easton教授在3D打印超细晶粒高强度钛合金取得突破性进展。
一般来说,控制晶粒尺寸的主要因素有:1)临界形核过冷度△Tn;2)在生长的固体前面的成分过冷,提供了形核过冷ΔTCS;3)成核粒子之间的平均间距xsd;小△Tn,大ΔTCS和小xsd有利于晶粒细化。成分过冷区受生长限制因子Q的控制,Q值越大,形核越多。然而,在增材制造的金属中,激光熔化区域的尺寸,高的热梯度,在很大程度上抑制了成分过冷区的范围,使增材制造的钛合金中实现细晶粒尺寸具有挑战性。通过对钛合金相图的研究,发现Cu的最大固溶浓度c0-max为17%,Qmax = c0-maxm(k – 1) = 110.5 K,m是液相线的斜率,k是溶质分配系数。铜也是一个典型的共析元素钛二元合金系统中β→α+ Ti2Cu在792°C。由于铜在钛中扩散迅速,即使在水淬后也很难阻止这种共析反应的发生。这些特性有利于在增材制造过程中较高的冷却速率,并可能产生非常精细的共析微观结构,从而提高打印试样的强度和延性。该文作者通过单步3D打印Ti-8.5Cu合金,制造出了完全各向等大的β钛晶粒和超细共析组织的钛合金。3D打印态钛铜合金的晶粒细化效率来自于铜溶质在固液界面前形成足够大的结构过冷区,使溶质铜在固液界面周围析出时形成的β钛枝晶。充分的过冷可以有效地抵消高热梯度的负面影响,保证在过冷区可以触发异质成核,实现完全的柱状-等轴过渡。高的冷却速率会限制原子的扩散,从而抑制共析耦合生长,产生马氏体,所以在Ti-8.5Cu合金的等轴组织内发现了马氏体,层间平均间距为46 nm±7 nm。;拉伸性能的测试表明,与传统铸造和后热处理工艺相比, 具有超细原始β晶粒和共析层状结构3D打印钛铜合金的力学性能拥有优越的屈服强度和延展性。
Figure 4 3D打印Ti-8.5Cu合金的组织喝力学性能[5]
6 北京科技大学的赵征志教授和梁江涛博士参与合作的研究成果在《Science》发表,在氢脆研究领域实现重大突破。
尽管氢脆现象已经被发现有100多年了,但对其机理的解释上是一个难题。高强钢具有的高氢脆敏感性,如何解决氢脆问题是高强和超高强钢实现研发应用的重要一关。由于氢原子半径小,容易迁移,采用电镜,热脱附谱等技术难以精确确定氢在材料中的位置,使氢与材料微结构(如晶界、位错等)的相对关系的表征极为欠缺,限制了对材料中形成氢脆现象的机理理解。氘作为氢的同位素,化学性质几乎与氢相同,但由于其质量较大,在钢中的扩散系数略低。氘与低温样品转移相结合,使我们能够获得氢在纳米尺度特征周围分布的精确观测结果。因此,研究人员使用氘同位素标记与低温转移原子探针层析成像技术相集合的方式确定了两种不同基体组织结构钢铁材料中氢原子的确切位置。
研究人员首先对含铌钢进行处理,得到了铁素体和马氏体两种微观组织,使用同位素标记来避免试验环境中的氢所带来的误差,同时利用低温转移原子探针层析成像技术来观察钢中特定微观结构特征下的氢状态。结果表明,氢原子被钉扎在钢中位错、晶界、析出相等位置不同界面。在富集碳的位错和晶界处直接观察到了氢,这为氢脆模型提供了实验证据。在NbC析出相与钢基体不相连的界面处也观察到了氢,这直接证明了不相连的界面处可成为氢陷阱。
该研究成功的表征并分析出了可以作为氢陷阱的位错、晶界和析出相与氢原子之间的关系,改变了氢脆领域只有理论模型而无法直接观测研究的现状。这一研究成果为氢脆领域的研究直接提供了实验依据,同时对抗氢脆钢的研发与应用具有重要意义。
Figure 5 用低温转移原子探针层析成像技术来观察铁素体和马氏体两种微观组织特征下的氢状态[6]
7 2020年1月,金属所钛合金研究部的周刚助理研究员(共同一作)、王皞副研究员在五重孪晶形成机理研究取得重要进展。
孪晶存在于自然界的很多材料之中,如矿物,金属以及陶瓷等。孪晶会使材料形成各种结构与形貌,从而影响其力学性能。多重孪晶在晶体生长、生物医学、光学和催化等领域均有着广泛的应用。五重孪晶作为多重孪晶的一种,已被研究及应用了很多年,但是其形成机理一直未能弄清楚且处于争论中,主要原因是缺乏实验上对其形成过程进行原子尺度的观察。到目前为止已提出的五重孪晶的形成机理只要包括:1)原子逐层添加的形成机理(分子动力学模拟);2)四面体的连续缠绕和生长;3)不全位错的滑移。
该文研究者发现,厚度约为3nm 的Au、Pt和Pd纳米颗粒在聚集生长过程中,首先颗粒间通过沿{111}面取向粘附形成无界面的单晶或者∑3孪晶。二次孪晶界∑32通过取向粘附另一个形成,从而导致两种类型的凹面(夹角分别为94°和150°)。二次孪晶界∑32的夹角分别为109°和70°。另外,通过1/6<112>不全位错的滑动,可以观察到孪晶和去孪晶过程。本文主要提出了五重孪晶的两种形成机制:1)经原子表面扩散和高能晶界形成及分解;2)不全位错的滑移。两种形成机理主要取决于颗粒取向粘附后所形成表面结构。如果经取向粘附后,形成的凹面夹角接近90°,则为机理1;如果形成的凹面夹角接近150°,则为机理2,其具体的形成过程如下:
1)经原子表面扩散和高能晶界形成及分解
首先,经颗粒取向粘附过程形成起始的两个Σ3孪晶界面以及一个90°凹面(figure.6- A和B);这种较大曲率的凹面将促使表面原子的扩散到该处进而形成第三个Σ3孪晶界和Σ27高能晶界(Figure.6- C);最终通过孪晶极附近零应变孪晶的形核及生长,Σ27分解成另外两个Σ3孪晶界并形成五重孪晶结构(figure 6-D~I)。该机理可形成较为对称的五重孪晶结构。
Figure 6 五重孪晶通过取向粘附、原子表面扩散以及随后的高能晶界的形成和分解形成
(A和B)Σ3以及90°凹面形成;
(C)原子向凹面迁移,形成Σ3晶界和两个原子层的Σ32从Ⅲ向Ⅱ迁移;
(D-G)Σ27-(200)以及Σ27-(111)的震荡;
(H)ZST在Σ27孪晶极的形核;
(I)五重孪晶的形成[7]。
2)取向粘附和不全位错的滑移或晶界分解
当取向粘附过程形成的凹面夹角为150°时,通过在表层原子中不全位错的滑移或Σ9晶界的分解即可实现五重孪晶的形成。不全位错的继续滑移可促使孪晶界面向晶粒内部迁移,但也伴随着晶格应变能增大,因此该机理主要形成不对称的五重孪晶结构。在后续的生长过程中,五重孪晶对称性的演化可通过与其他纳米颗粒的聚集长大实现(Figure.7)。
Figure 7 五重孪晶通过取向粘附和不全位错的滑移或晶界分解
(A和B)Σ3以及90°凹面形成;
(C)原子向凹面扩散后形成Σ9;
(D)通过晶界分解和不全位错滑移形成五重孪晶;
(E和F)孪晶界的迁移[7]。
8 重庆大学材料科学与工程学院黄晓旭教授团队在《Nature》上发表最新研究成果,发现了纳米金属的一种新型强化方式—利用高压强化。
根据Hall-Petch关系,金属的强度会随着颗粒尺寸的减小而增加。据报道,当临界颗粒尺寸为10到15纳米左右时,这种关系就会打破。当晶粒尺寸减小超过这一临界值时,变形机制从位错主导的过程转变为晶界(GB)滑动,导致材料软化。之前金属所卢柯等人通过弛豫和钼偏析来稳定晶界,以防止晶粒尺寸小于10纳米的镍钼合金的这种软化效应。另外有研究指出,纳米晶的尺寸软化可能与材料的制备有关。本文采用射线金刚石砧芯(DAC) x射线衍射(XRD)技术,对不同晶粒尺寸镍的屈服应力和变形变形进行了原位跟踪。研究表明,形变强化可以延伸到3nm的晶粒尺寸,这比之前报道的纳米颗粒金属的最强尺寸要小得多。
利用DAC XRD实验对晶粒尺寸为3~200nm的纯金属镍进行单向高压变形,其应力可分为流体静力应力分量和偏应力分量。研究发现:其强度随着晶粒尺寸减小持续提高,纳米晶粒镍的应力应变曲线也表现出较大的斜率/硬化指数,这可能是由于这种较小晶粒尺寸增加了塑性各向异性。原位透射实验表明:晶粒尺寸大于20nm的镍样品即使在低应变条件下也表现出很强的形变织构。晶粒尺寸在20nm以下的纳米镍样品表现出非常弱的形变织构,说明传统的全位错活动不活跃,而强度随着晶粒尺寸的减小而增大。同时,所有的镍样品都呈现出形变织构,说明形变机制可能仍然基于位错滑移和孪晶形成,因为晶界主导的机制维持了初始的随机织构。偏应力引起的剪切应力可能激活GB滑动机制,而压缩的流体静力增加了GB迁移和滑动的临界剪切应力,从而抑制了这些机制。当晶界调节的变形机制被抑制时,材料的强度应主要由晶格应变和晶粒内部的缺陷有关。
利用投射电镜的研究表明:在压缩的纳米颗粒镍中发现了两种与不全位错相关的平面缺陷(即纳米孪晶和堆垛缺陷)和完全位错,在粗晶粒样品中可以看到高密度的位错。值得注意的是,位错普遍存在于所有的平均晶粒尺寸,包括最细的在3nm。所以在纳米晶镍变形的过程中,不全位错和位错主要的变形机制导致了高强度(Figure 8)。
令人吃惊的是,晶粒尺寸越小其强化效果越显著。在所研究的最小晶粒尺寸(3纳米)样品中,获得了4.2 GPa的超高屈服强度,比常规商业纯镍强度提高了10倍。
该研究最为重要的一个贡献是基于不全位错参与的变形,作者修正了Hall-Petch公式,新的公式为:
其中σy和d代表屈服强度和晶粒尺寸,σ0 、k0、k1是常数。
Figure.8 计算仿真结果与改进的Hall-Petch关系[8]
9 金属所首次在块体非晶态材料中实现加工硬化。
不同于晶体材料,非晶本质上具有很高的屈服应力σy,室温下屈服后紧接着软化,导致剪切带的形成和变形不均匀。剪切带产生了不需要的表面标记,削弱了样品,最终演变成裂纹。加工硬化是工程合金力学行为中最重要的现象,因为它保证了金属流动的非局部化,提高了延性,并抑制了灾难性的机械失效。块体非晶(MG)材料的力学行为是没有加工硬化阶段出现的,所以其基本无塑性,这严重限制了其在工程的大规模应用。
对于非晶材料,当截面小于100nm时,在变形中无剪切带形成,流均匀,塑性应变可以达到25%,和显示加工硬化。由于剪切带与偏移量有关,因此也可以通过机械约束来抑制剪切带。通过更快的冷却、辐照或热机械加工可以实现高能量状态的回春。所以首先通过三维压应力的方法使块体非晶合金产生大范围、高程度的回春,开发出最高能量状态相当于冷速为1010K/s的非晶合金。研究发现:在简单单轴载荷作用下抑制大块单相玻璃的剪切带。在MG基非晶材料中,当流变引起分散相的相变时,可以看到应变硬化现象。该文首先单轴压缩切口直径4毫米的MG棒,可使中心区域回春。单轴拉伸或压缩测试发现:高能量状态(回春态)的块体非晶合金在变形时表现出加工硬化现象和优异的塑性变形能力。在加工硬化阶段,观察不到任何剪切带,表明合金发生了均匀流变,这完全不同于传统非晶合金依靠剪切带的变形行为。此外,非晶合金的硬化速率远高于任何常见的晶体金属体系。对比回春态和传统铸态块体非晶合金在变形前后的结构和能量状态变化时发现,回春态非晶合金在加工硬化过程中硬度明显上升,但能量显著降低。非晶合金的径向分布函数结果表明加工硬化后回春态块体非晶合金的结构更加有序化(密度增加),与传统铸态非晶合金形变软化和能量升高的变形过程完全相反(Figure.9)。
Figure.9 MG基非晶材料变形的回春现象
(a)直径4毫米的棒状Zr64.13Cu15.75Ni10.12Al10大块MG经过机加工后具有圆周缺口;
(b)四个单轴压缩的工程应力-应变曲线,对应于一个回春样品的三次卸载-再加载循环[9]。
在晶体金属材料中,加工硬化的原理是变形过程中位错增殖及其相互作用阻碍了彼此的运动。虽然微观结构等其他因素也会影响材料的加工硬化行为,但其最基本原理没有改变,仍然是位错增殖,并导致材料能量增加的过程。然而,此次研究结果表明,块体非晶合金的加工硬化却是伴随着材料缺陷(尤其是位错)的湮灭和减少,即更驰豫状态,是一个由高能态向低能态的转变过程。这与晶体材料的传统加工硬化过程完全相反,表明非晶合金具有完全不同的加工硬化机制(Figure.10)。
Figure.10 诱导的MG能量的变化
(a) 回春态Zr64.13Cu15.75Ni10.12Al10非晶合金在变形前后的DSC和驰豫焓曲线;
(b) 铸态和回春态非晶合金的归一化硬度;
(c)对应的驰豫焓;
(d)主衍射环位置q1与应变力间的关系[9]。
Zr64.13Cu15.75Ni10.12Al10非晶合金在最初变形阶段(<5%)表现出显著的加工硬化,伴随着硬度升高和能量的降低,以及结构的有序化。这完全不同于传统铸态非晶合金应变软化并伴随能量增加的过程。
免责声明:本网站所转载的文字、图片与视频资料版权归原创作者所有,如果涉及侵权,请第一时间联系本网删除。
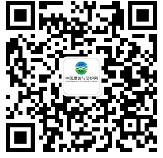
官方微信
《中国腐蚀与防护网电子期刊》征订启事
- 投稿联系:编辑部
- 电话:010-62316606-806
- 邮箱:fsfhzy666@163.com
- 中国腐蚀与防护网官方QQ群:140808414