航空发动机市场主要由民用航空发动机市场和军用航空发动机市场两部分构成。就民用航空发动机市场而言,降低燃油消耗,提高发动机使用寿命是众多发动机制造商关注的焦点。
就军用发动机市场而言,进一步提高发动机推重比,降低服役成本等是现阶段各国研究的重点。现有推重比10一级的发动机涡轮进口温度均达到了1500℃,如M88-2型发动机涡轮进口温度达到1577℃,F119 型发动机涡轮进口温度达到1700℃左右,而目前正在研制的推重比12~15的发动机涡轮进口平均温度将超过1800℃以上,这远远超过了高温合金及金属间化合物的使用温度。
目前,耐热性能最好的镍基高温合金材料工作温度达到1100℃左右,而且必须采用隔热涂层,同时设计先进的冷却结构。因此,现有的高温合金材料体系已经难以满足先进航空发动机,要发展具有更高推重比的航空发动机,必须开发新型轻质、高强度、耐高温、长寿命的发动机热端部件材料。
陶瓷基复合材料和碳基复合材料能够满足上述要求,成为能够替代高温合金在发动机高温部件上应用最具有应用潜力的材料。
陶瓷基复合材料是指在陶瓷基体中引入增强材料,形成以引入的增强材料为分散相,以陶瓷基体为连续相的复合材料。其中分散相可以为连续纤维、颗粒或者晶须。目前,研究较多的主要是连续纤维增强陶瓷基复合材料,主要有碳纤维增强碳化硅(Cf/SiC)、碳化硅纤维增强碳化硅(SiCf/SiC)以及氧化物/氧化物陶瓷基复合材料。
(1)轻质。陶瓷基复合材料密度低(仅为高温合金的1/3~1/4),可用于燃烧室、调节片/ 密封片等部件,能够直接减轻质量50%左右。
(2)耐高温。陶瓷基复合材料的工作温度高达1650℃,能够简化甚至省去冷却结构,优化发动机结构,提高发动机工作温度和使用寿命。在无冷却结构的条件下,可以在1200℃长期使用。
(3)优异的高温抗氧化性能。陶瓷基复合材料能够在高温环境,甚至是有氧环境下保持较高的稳定性,降低了热防护涂层的研制和应用成本。
(4)优异力学性能。通过制备工艺优化,特别是界面层组分和结构设计,陶瓷基复合材料的力学性能相对于单相陶瓷而言,有了质的提升。
碳/碳(C/C)复合材料是碳纤维增强碳基体的复合材料, 具有高强高模、比重轻、热膨胀系数小、抗腐蚀、抗热冲击、耐摩擦性能好、化学稳定性好等一系列优异性能, 是一种新型的超高温复合材料。
C/C复合材料作为优异的热结构-功能一体化工程材料。它和其他高性能复合材料相同,是由纤维增强相和基本相组成的一种复合结构,不同之处是增强相和基本相均由具有特殊性能的纯碳组成。
碳/碳复合材料主要是由碳毡、碳布、碳纤维作为增强体,气相沉积碳做为基体经过复合而制成,但是它的组成元素只有一个就是碳这个元素。为了增加密度,由碳化而生成的浸渍碳或浸渍在康铜树脂(或沥青),也就是说碳/碳复合材料是由三种碳材料复合而制成的。
1. 密度1.65--2.0g/cm3,质量轻,仅为钢的四分之一;
2. 力学特性随着温度的升高而增大,是现在唯一能够在2500℃以上保持高温强度的工程材料;
3. 优秀的耐烧蚀性能,导热系数高、比热容大;
4. 损伤容限很高,具有良好的抗热震性能;
5. 摩擦性能好,摩擦系数比较稳定,具有一定的韧性;
6. 承载水平比较高,过载能力较强,高温下也不会熔化,且不会发生粘连现象;
7. 线膨胀系数较小,高温下尺寸稳定性好,使用寿命长。
陶瓷基复合材料和碳基复合材料作为先进复合材料的代表,其生产制备技术工艺的简单成熟化,标志着其在航空航天制造领域的主导地位。经过近几十年的发展,陶瓷基复合材料的制备工艺已经趋于成熟,部分技术成果已经成功应用到航空发动机热端部件上。
这些工艺主要包括化学气相渗透法(CVI),聚合物浸渍裂解工艺(PIP),浆料浸渍热压法(SIHP)和熔体浸渗工艺(RMI)等。世界各国对陶瓷基复合材料工艺都进行了详细的研究,其中日本拥有聚碳硅烷(PCS)和连续SiC 纤维制备技术,主要开展PIP 工艺制备纤维增强SiC 复合材料的研究, 特别是在SiCf/SiC复合材料制备上具有较高的研究水平;法国以CVI技术为主,且技术水平属国际领先;德国以RMI 和PIP技术为主, 特别是RMI 技术世界领先;美国对PIP、CVI 和RMI 工艺均有研究,且均有较高的研究水平,特别是RMI 工艺,已经成为GE 公司陶瓷基复合材料制备的主流工艺[1]。
而碳基复合材料,特别是高性能的C/C复合材料多采用炭纤维多向编织成型,然后进一步致密化的方法提高密度。通常极具有发展前途的方法有化学气相渗透(CVI)、液相浸渍工艺、化学液-气相沉积(CLVD)等。其中工业化的应用主要集中在CVI和PIP工艺上。
连续相增强碳化硅基体复合材料是陶瓷基复合材料的典型代表,具有高的比强度和比刚度、良好的高温力学性能和抗氧化性能以及优异的抗辐照性能和耐腐蚀性能,在航空航天和核聚变领域都有着广泛的应用前景[2]。高科技领域常用的SiC基复合材料制备方法有化学气相渗透工艺(CVI)、先驱体浸渍裂解工艺(PIP)、浆料浸渍热压法(SIHP)和熔体浸渗工艺(RMI)等。其中PIP工艺与CVI工艺均为制备SiC基复合材料的传统工艺,应用广泛,工艺成熟。
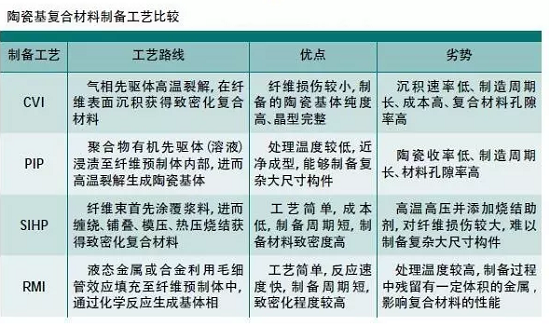
1983 年,Yajima 等[3]提出了聚碳硅烷裂解制备SiC 材料的路线,先驱体转化制备陶瓷材料的巨大潜力逐渐被人们所认识。先驱体浸渍裂解法又称聚合物浸渍裂解法或先驱体转化法,其一般过程是: 以纤维预制件( 三维编织物、毡体等) 为骨架,浸渍聚合物先驱体,在惰性气体保护下使其交联固化,然后在一定气氛中进行高温裂解,从而得到陶瓷基复合材料,重复浸渍-交联-裂解过程可使复合材料致密化。
PIP 工艺的优点是:
( 1) 先驱体分子可设计,进而实现对最终复合材料陶瓷基体组成、结构与性能的控制;
( 2) 制备温度低,设备要求简单;
( 3) 可制备大型复杂形状的构件,能够实现近净成型。程中无需引入烧结助剂,材料高温性能好;
(4)由于先驱体特性与聚合物树脂相似,可以充分利用聚合物基复合材料的成型技术来制备各种复杂形状的CFRCMCs。
除此之外,PIP法对设备要求不高,操作过程简单。若在先驱体中添加惰性或活性增强相,还可以缩短制备周期,甚至只需一个浸渍一固化一裂解周期就可以制备出致密CFRCMCs.
不同研究者所得材料的性能有很大差异,这是因为PIP法CFRCMCs的性能受许多因素影响。除了纤维和基体种类、纤维性能、纤维表面状态、纤维排布(编织)方式和体积分数等因素之外,在很大程度上受到制备工艺的影响。不同的工艺过程会导致复合材料的结构不同,在性能上表现出很大差别。
虽然影响因素众多,但从结构上分析可知,致密度和界面结构是影响CFRCMCs力学性能的两个根本性和关键性因素。因此,许多工作都围绕这两个方面展开以提高材料的力学性能。
提高致密度就要减少材料中的气孔。
PIP法CFRCMCs中的气孔来源于两方面:
一是先驱体浸渍纤维预制件时没能完全排出预制件中的空气,残留空气大部分以闭气孔的形式留在材料中;
二是先驱体裂解时放出许多小分子而在材料中留下的气孔。减少PIP法CFRCMCs中气孔的方法除了增加浸溃一裂解周期和添加活性增强相外,还可在浸溃和裂解过程中采取措施。
PIP法制备CFRCMCs首先要让先驱体浸溃纤维预制件,置换出其空隙中的空气。浸渍效率的高低会影响先驱体填充空隙的程度,从而影响材料致密度。为了提高先驱体浸渍纤维的效率,可对原先的常温常压浸渍进行改进,采取真空浸渍、加热加压浸渍等方法。
在裂解过程中,采用热压(包括热等静压)辅助可以明显降低气孔率,提高基体致密度。但热压不适合制备形状复杂的构件,所以应用前景不大。气压裂解不仅可以抑制小分子气体产生,提高陶瓷产率,减少气孔率,而且适合制备复杂形状构件,是一种比较有前景的裂解工艺。
CVI 是将具有特定形状的纤维预制体置于沉积炉中, 通入的气态前驱体通过扩散、对流等方式进入预制体内部, 在一定温度下由于热激活而发生复杂的化学反应, 生成固态的陶瓷类物质并以涂层的形式沉积于纤维表面;随着沉积的继续进行, 纤维表面的涂层越来越厚, 纤维间的空隙越来越小, 最终各涂层相互重叠, 成为材料内的连续相, 即陶瓷基体。
从某种角度而言, 化学气相渗透是化学气相沉积(CVD)的一种特殊形式, 在CVI 中, 预制体是多孔低密度材料, 沉积多发生于其内部纤维表面;而CVD 是在衬底材料的外表面上直接沉积涂层。
与粉末烧结和热等静压等常规工艺相比,CVI 工艺具有以下优点:
(1)CVI 工艺在无压和相对低温条件下进行(粉末烧结通常2000 ℃以上,CVI 法1000 ℃左右),纤维类增强物的损伤较小,可制备出高性能(特别是高断裂韧性)的陶瓷基复合材料;
(2)通过改变气态前驱体的种类、含量、沉积顺序、沉积工艺, 可方便地对陶瓷基复合材料的界面、基体的组成与微观结构进行设计;
(3)由于不需要加入烧结助剂,所得到的陶瓷基体在纯度和组成结构上优于用常规方法制备的;
(4)可成型形态复杂、纤维体积分数较高的陶瓷基复合材料;
(5)对用其它工艺制备的陶瓷基复合材料或多孔陶瓷材料可进行进一步的致密化处理, 减少材料内部存在的开放孔洞和裂纹。当然CVI 法也存在一定的不足之处, 目前最大的问题是成型周期长,成本高。
用CVI法制备陶瓷基复合材料的目的是获取具有结构完整性和密度均匀性的制件。为实现这一步, 就要协调好气体的输送和反应温度这两个因素, 使不同的沉积区域都能获得良好的沉积效果。从控制气体输送模式和反应温度两个角度出发, 已经发展了五种主要的CVI方法, 即等温CVI(ICVI)、等温强制流动CVI、热梯度CVI 、强制流动热梯度CVI(FCVI )及脉冲CVI。
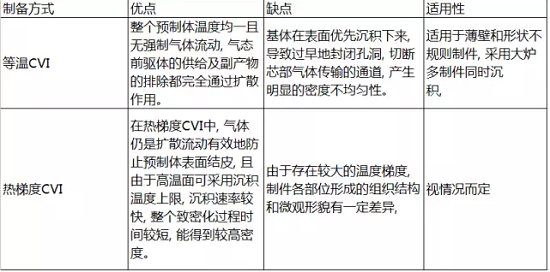
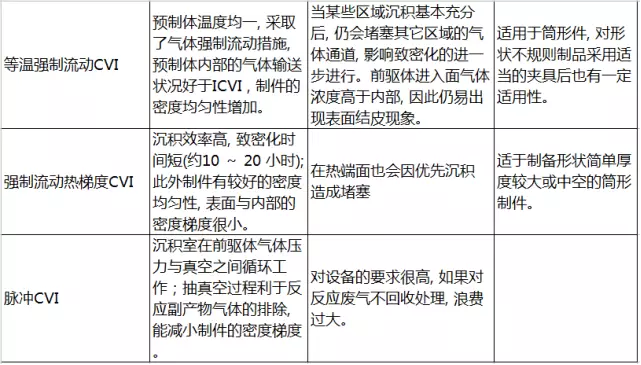
随着科技发展, 碳/碳复合材料的应用预计将更加广泛.然而, 由于其制造周期长,成本高,很大程度上限制了这种优秀材料在国民经济各领域的广泛应用。近十年来,缩短其制造周期,降低成本成为该科研领域主攻方向之一。碳/碳复合材料的制备过程包括增强纤维及其织物的选择、基体碳先驱体的选择、C/C预制坯体的成型、碳基体的致密化以及最终产品的加工检测等[5]。
1)碳纤维的选择
碳纤维束的选择和纤维织物的结构设计是制造C/C复合材料的基础,通过合理选择纤维种类和织物的编制参数,如纱束的排列取向、纱束间距、纱束体积含量等,可以决定C/C复合材料的力学性能和热物理性能[6-8]。
2)碳纤维预制坯体的制备
预制坯体是指按产品形状和性能要求先把纤维成型为所需结构形状的毛坯,以便进行致密化工艺。预成型结构件的加工方式主要有三种:软编、硬编和软硬混编。编织工艺主要有:干纱编织、预浸渍维杆组排、细编穿刺、纤维缠绕以及三维多向整体编织等。目前C复合材料主要使用的编织工艺是三维整体多向编织,编织过程中所有编织纤维按照一定的方向排列,每根纤维沿着自己的方向偏移一定的角度互相交织构成织物,其特点是可以成型三维多向整体织物,可以有效的控制C/C复合材料各个方向上纤维的体积含量,使得C/C复合材料在各个方向发挥合理的力学性能[9]。
3)C/C的致密化工艺
致密化程度和效率主要受织物结构、基体材料工艺参数的影响。目前使用的工艺方法有浸渍碳化、化学气相沉积(CVD)、化学气相渗透(CVI)、化学液相沉积、热解等方法。主要使用的工艺方法有两大类:浸渍碳化工艺和化学气渗透工艺[10-12]。
浸渍碳化是最常用的C/C复合材料的致密化工艺。浸渍碳化是在常压或减压条件下,将碳基体的前驱体浸入编织预制体的内部孔隙,然后在一定气体环境中高温碳化以及石墨化过程,通过多次循环获得致密C/C复合材料,浸渍碳化是最早使用的C/C复合材料致密化工艺,其工艺过程如图所示。
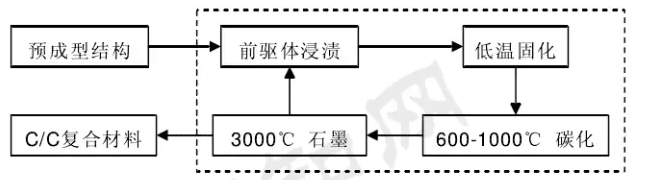
用于液相浸渍的碳基体的前躯体有酚醛树脂、糠醛树脂、煤沥青等,如果前驱体是沥青,浸渍后必须在10MPa以上的高压下进行缓慢碳化才能得到高碳收率。另外,液相前驱体必须具有较低的粘度,对碳基体有较好的润湿性及可固化性以便阻止在碳化之前进一步加热时的液体流失。如果前驱体是树脂,为了提高碳收率,需反复进行浸渍碳化石墨化循环。
树脂浸渍工艺流程是:将预制坯体置于浸渍炉中,在真空下用树脂浸渍预制坯体,再充气加压使树脂浸透预制坯体。浸渍压力逐渐增加至3~5MPa,首次浸渍压力不易过高,以免纤维织物变形受损。浸渍树脂后的样品放入固化罐中进行加压固化。树脂固化后将样品放入碳化炉中,在氩气或氮气的保护下进行炭化,在炭化过程中树脂热解形成碳残留物,发生质量损失和变形,同时在样品中留下空隙。故此需要重新进行树脂浸渍和炭化,以减少空隙达到致密化的要求。
沥青浸渍工艺流程是:常采用石油沥青为浸渍物,先进行真空浸渍,而后加压浸渍。现将盛有碳纤维预制坯体的容器放入真空炉中,同时将沥青放入融化罐中抽真空并加热到沥青熔化,然后将熔化沥青注入到盛有预制坯体的容器中,使沥青浸没预制坯体。之后转移入加压600~700℃进行加压炭化。一般把浸渍、炭化压力为1MPa左右的为低压浸渍炭化,压力几到几十兆帕称为中压浸渍炭化,而压力达到几十到上百兆帕称为高压浸渍炭化工艺。
浸渍碳化工艺大致包括下面几个过程:
(1) C-H和C-C键断裂形成具有化学活性的自由基;
(2) 分子的重排;
(3) 热聚合;
(4) 芳香环的稠化;
(5) 侧链和氢的脱除。
上述的几个反应过程并不是孤立存在的,这些反应往往同时发生,最后在1000℃时形成具有网状三维结构的基体碳。在热处理温度达到1000 ℃时,碳以外的元素己基本消失,这个温度可以认为是获得实质“碳”所必要的温度,化学变化过程在此结束。温度超过1000℃,一直到3000℃,基体碳处于石墨化阶段,其表现形式是碳网平面尺寸增大,且碳网平面堆积层数增多,最终朝石墨化的方向转化,最终制成致密的C/C复合材料。浸渍碳化工艺时间短、成本低,具有高碳收率、低制备成本等优点。
化学气相渗透((CVI)是一种控制条件下在多孔预制体内部进行碳氢化合物(如CH4,C3H6等)热解、沉积的涂层工艺。按照加热方式可以把CVI工艺技术划分为两类。
2.1 热器壁技术(外部热源)
(1) 等温CVI:该工艺是在等温的空间内,在适当的压力下,炭源气体依靠扩散作用进入样品孔隙内热解沉积。由于气体在表而扩散优于内部,热解炭首先沉积在预制体表而导致扩散孔隙封闭,因此只能采用低温、低气体浓度减缓沉积速率。当表而封孔时,需要反复机加工和高温热处理,打开封闭孔隙继续沉积,结果造成沉积周期过长。但该工艺不受样件几何形状影响,工艺简单,易实现批量生产,工艺重复性好。此外,采用大炉沉积可形成规模效益以部分抵消周期长导致的高成本。从等温工艺衍生出的方法有催化CVI.等离子增强CVI、脉冲流动法等方法。
(2) 压差法CVI:该工艺是对等温法的改进,在预制体厚度方向上形成一定的压力差,气体被强行通过多孔预制体。与等温法相比,预制体内部的气体输运状况有所改善,沉积较快,但仍会出现表而封孔现象。此法特别适用于沉积筒状件。
2.2 冷器壁技术(内部热源)
(1) 热梯度CVI:是在预制体的内外表而形成一定的温度差,内部的温度高,沉积由内向外逐渐推移,直至致密。此法能一定程度避免表而封孔现象,沉积速率较快。但随着沉积过程的进行,由于芯部密度增加,辐射到外表而的热量增多,热梯度减小,导致制品密度和组织结构不均匀。
(2) 强制流动CVI:综合了热梯度法和压差法的优点。将预制体上端而加热,下端而冷却,反应气体由下端向上输送,热解炭的沉积由高温而向低温而推进完成致密化,从而提高沉积速率,保证密度的均匀性。此法因沉积效率高,制品性能好,发展潜力很大。
(3) 直热式CVI:该方法是使预制体在电流作用下直接发热,由预制体本身形成热梯度进行沉积。由于预制体是直接通电加热,因而升降温速度快,操作简单且由内向外的沉积一定程度避免了表而封孔现象。但是每炉样品数量非常有限且对电流电压要求高。
(4) 化学液气相渗透 (CLVI) 和快速蒸气CVI。两种工艺的显著特点沉积速率快,几小时就能一次性完成致密化。其区别是将预制体浸入前驱体溶液中,还是置于蒸发气体中。该工艺制得的C/C内部没有大的残余孔隙,致密度高,但是设备复杂,安全性要求高。
(5) 多元耦合场CVI:此工艺由中南大学研发,结合了热梯度法和直热法的优点,制备操作简单,沉积速率快,可一次性完成致密化。该工艺升降温速度快,炭源气体要求低,特别适合于片状预制体,是一种很有前途的低成本快速CVI技术,但单炉样品数有限。
总之,各国科学家已经针对快速低成本CVI技术方而做了很多工作。其中,德国研究者近年来对等温法进行了较大改进,提出了快速等温CVI制备技术。日前,国外生产商如Messier和Dunlop应用于工业生产的技术主要还是采用日臻成熟的等温法,而国内工业规模生产则是等温法和热梯度法等快速致密化工艺并存。
4)C/C的石墨化
根据使用要求,常对致密化的C/C材料进行高温热处理,常用温度为2400℃~2800℃,在这一温度下N、H、O、K、Na、Ca等元素逸出,碳发生晶格结构转变,转化为石墨结构。石墨化处理对C/C复合材料性能有明显的影响。经过石墨化处理后,其强度和热膨胀系数均降低,导热率、热稳定性、抗氧化性及纯度都有所提高。
陶瓷基复合材料和碳基复合材料由于其优异的使用性能,使之成为极其重要的战略材料,各国都投入了大量的人力物力进行研发工作,并且已经在很多重要的领域尤其是航空航天领域得到了应用。但是与其他材料相比,这些材料的成本依旧很高,民用推广存在很大的难度。如何降低成本将会是其研究的重点。
责任编辑:王元