先进轻量化材料制造创新机构(LIFT)依六大技术领域设置项目,即连接与装配、热机械加工、粉末加工、熔化加工、新型/敏捷加工、涂层,每个领域在技术路线图中还有若干主题。项目招标时侧重跨领域的主题,包括集成计算材料工程(ICME)、确认/认证、设计、成本建模、供应链、寿命周期分析、腐蚀和弹道/爆炸。
表1 机构技术领域与路线图项目
注:新型/敏捷加工未提供公开版技术路线图,标*项目为本次介绍内容
项目需求来自所有成员,其中大学提交的占70%,而且授出项目的50%也是大学提交的,但是每个项目都由工业界领导,并指定一家大学辅助。这些项目一般持续1年~2年,投资在100万~400万美元之间,绝大多数项目同时面向航空航天、汽车和军用车辆,以及重型车辆、列车、船舶和近海平台。目前已公布9个项目详细内容:
一、面向轻量化金属结构构建的可靠变形控制手段和实施
当前生产中的复杂结构部件变形控制仍然是以观察或经验为依据的,因为:1)有效的复杂结构变形建模技术必须在一个结构层面上聚焦影响变形的关键参数,以实现计算效率和可靠度;2)详细的材料本构行为——包括焊接中的微结构变化,仅影响穿壁、自平衡的压力状态,对结构变形(即结构层面上的全局现象)影响很小;3)无法有效分开局部和全局效应,使变形建模手段变得太复杂,难以用于结构变形。
项目将开发ICME工具,针对典型结构形式——如复杂焊接结构、加筋壁板等,精确预测与其生产过程相关的变形。这包括开发变形预测模型并确认变形缓解策略,以提高轻量化钢制造过程的最终质量。第一阶段将聚焦ICME模型的开发,并将它们与实际生产变形建立关联;第二阶段将聚焦确认和优化变形控制方法,开发并验证针对每个生产阶段的变形预防策略。项目包括对变形控制手段的一个详细成本分析。
项目主要工业参与方为亨廷顿英戈尔斯工业公司、Comau、ESI、EWI,计划2017年12月完成。对轻量化结构组件的建造来说,实施更好的变形控制预测和流程,将极大减少返工并提升生产率。项目效益预计包括改进的车间操作规程、用于面向生产优化设计的简化的变形估算方程,以及进行工程设计和制造分析的基于有限元的变形分析程序。
二、面向确保大型钛结构性能,将ICME与传统和新型TMP集成
当前,军用系统和商业产品要求更经济可承受、更轻量化和提升的性能,使用钛合金的新型设计和制造工艺可以满足这些需求;在制造中广泛使用钛合金一般被高材料成本和长开发周期所阻碍,因为替代“试错”设计和试验方法的分析仿真工具有限。
项目将聚焦ICME建模的开发和确认,以减少钛组件设计和试验的成本与开发时间。主要是相似或相异材料的固态连接和粉末冶金工艺(如近净成形热等静压),实现坯体的机加和锻造生产。
项目主要工业参与方为GE、波音、科学成形技术公司,计划2018年3月完成。成果将降低钛合金组件的成本并提升其性能:基于计算的工具可将材料开发和组件设计的时间和成本减少50%,这些工具还允许制造出的组件拥有增强的局部性能,并且在某些条件下更加轻质。
三、面向确保铝锂锻件性能的加工,开发、应用并确认基于物理特性的局部粘塑性模型
过去结构应用中的铝锂合金,由于高平面各向异性、不寻常的裂纹路径和缺乏热稳定性,存在很严重的问题。新一代铝锂合金可以减重并且提升性能。为满足商用飞机发动机更高的性能要求,需要改进的分析手段以确定哪些材料性能最合适一个特定结构,以及在材料加工中如何达到所需的力学和损伤容限性能。
项目将开发、实施并确认一个基于局部物理特性的粘塑性有限元模型,以预测锻造铝锂合金的机械变形响应、损伤演进机制和疲劳性能。第一阶段将聚焦铝锂合金铸件预测工具的开发和确认,以预测材料加工参数对零件各向异性力学性能的影响。该阶段目标是:1)开发并执行一个非恒温的多尺度晶体塑性(CP)本构模型,应用于第三代铝锂合金;2)开发并执行一个基于微结构的CP有限元分析框架,预测材料加工和局部形态对组件力学行为的影响;3)实验校准并确认预测模型。
项目主要工业参与方为联合技术公司研究中心、洛克希德·马丁,计划2017年12月完成。成果工具集指导铸造铝锂合金组件的工艺优化,将减少一代飞机发动机开发所需研制硬件和加工试验的数量。通过优化工艺和设计,组件将拥有改进的性能和更轻的质量。
四、面向亚微米增强铝金属基复合材料(MMC)的低成本、先进机械合金炼制和粉末固结工艺开发
铝基亚微米碳化硅增强MMC的应用主要受制于当前热等静压(HIP)固结工艺相对高的成本。这些MMC的开发还包括粉末合成、机械合金化、固结和后热处理,所有这些都增加完成组件的成本。业界需要能够消除或极大减少这些工艺步骤的新型工艺,实现更高的成本竞争力,增强大批量生产能力,以及扩大后续在航空航天应用中减重的潜力。
项目将聚焦由新兴机械合金化粉末衍生的铝-碳化硅MMC。考虑因素包括工艺优化、技术成本建模和新型固结方法评价。机械合金化铝-碳化硅MMC的替代固结工艺展现了减少总制造成本的潜力,通过尽量减小升温时间并且引入伴随的机械变形步骤,实现改进的力学性能。这包括HIP替代工艺以在挤压成形(如选区等离子烧结)之前固结坯体,以及直接粉末挤压成形或近净成形锻造。该方法可以消除HIP装壳和去壳步骤,被认为比基线热等静压方法成本低,但与锻铝对比来说,强质比相似且拥有复合材料的超强刚度。
项目主要工业参与方为Materion、洛克希德·马丁、波音、GKN,计划2018年6月完成。对成本结构、性能预测工具和替代加工路线的一个完整认识将允许材料开发人员减少向未来航空航天平台交付铝基MMC的时间和成本。团队正探索两种潜在应用,提升的性能和更大的减重机遇将针对基线铝合金挤压成形和替代粉末冶金压制成形来评价。
表2 LIFT配备的部分加工设备
五、面向高产量的薄壁球墨铸铁开发与部署
铸造薄壁球墨铸铁铸件的能力对于利用这些材料的高刚度和高强度来说至关重要。由于工艺和材料的限制,当前组件的界面尺寸通常比力学要求规定的更厚,从而使组件变得更重。
项目聚焦大批量生产薄壁、垂直湿砂型铸造球墨铸铁铸件所需的制造工艺开发。这需要集成几项近期开发的技术:1)高精度铸模机;2)利用珠光体和高硅铁氧体球墨铸铁合金减少碳的形成,铁氧体球墨铸铁合金已经生产但未应用于薄壁组件;3)流内和模内培养实践以控制微结构;4)“轻触”落砂和精整操作。
项目主要工业参与方为Grede、Comau、伊顿,于2016年6月完成。通过集成并实施改进的手段以及合金,有潜力降低球墨铸铁铸造零件的壁厚达50%,实现运输组件轻量化30%~50%(依据组件载荷)。
六、薄壁铝的模铸开发
薄壁铝高压模铸(HPDC)铸件领域的技术空白创造了三个改进机遇:1)对拥有大表面区域的零件来说,将模铸的最小壁厚减小到不足3mm,同时仍达到完全的模内填充;2)减少HPDC铸件的波动,增加其最小力学性能,当前这些限制了其在航空航天工业中的结构应用;3)建立为模铸定制的工艺设计。当前铸造设计实践对整个铸造统一应用铸造合金最小力学性能,这通常造成铸造工艺的超安全标准设计,特别是使用了一个大的安全系数时。
项目将聚焦生产高质量薄壁铝模铸组件的铝合金HPDC技术。面向300系列(基于AlSiMnCu)模铸合金,集成关键工艺技术(超真空模铸和短时热处理)和ICME工具,减少质量波动,提升力学性能。
项目主要工业参与方为波音、美铝、Comau、伊顿,计划2017年6月完成。项目效益包括:减少零件的最小壁厚以降低质量;使用HPDC替换组合的薄铝板组装件,降低制造成本;建立一个力学性能试验数据库和设计/ICME手段,在模铸供应基础内是可复制的,从而增加美国本土铝产品制造的竞争力。
七、确保性能的钣金组件敏捷制造
往往因需要几个零件,数百万美元的航空航天资产停止运行,而只能使用陈旧技术制作新零件。能够快速创建精密尺寸的组件是一个现实商业需求,在航空航天是修理和小批生产。这项技术是新兴的,但是主要实施障碍是商业化工艺还不存在,包括经证实的设计手段、仿真和确信的设计许用值,以用于失效关键的应用中。
项目面向不使用匹配模制造钣金零件,开发可以确定最佳成形路线的工具,满足性能设计许用值和尺寸规范。敏捷钣金成形的许多组成技术已经达到高制造成熟度等级,比如液压成形通常是商业化实践并且是许多军事生产规范的一部分;单点增量成形(SPIF)有限用于商业应用中的验证,因为其缺乏尺寸精度;双点增量成形(DPIF)因为需要专用机床还未广泛应用,但是已经在刀具路径编程和演示以高精度成形特定组件的能力上扩展了工作。项目将开发现有工艺的已确认工艺链,以及相关的设计方法,从而在估算成本内以精度可控的尺寸和确信的性能生产组件。增加的新方面有:为给定零件设计工艺和演示这些技术以评价商用就绪度,特别关注仿真、确信的认证性能和成本建模。
项目主要工业参与方为波音、洛克希德·马丁、Comau,计划2018年8月完成。项目面向飞行器和车辆应用,开发认证军用和民用敏捷钣金成形的路径,允许在钣金产品的小批量和定制生产中实施创新。
八、面向防腐微结构设计的综合数据库和计算模型
航空航天工业选择材料和制造工艺主要着眼于确保可接受的力学性能,复杂微结构金属材料的腐蚀性能可能在组件进入服役时才会完全认识到,使用计算模型预测并管理腐蚀敏感性将节省时间和成本。
项目将开发一个综合的材料性能数据库和计算模型,基于合金组成、热机械加工、热处理和服役条件的规范评价局部腐蚀敏感性。项目将开发ICME框架和最初的试验案例,以评价高强铝合金组件的腐蚀性能,识别进一步开发和评价铝合金改性所需的工具。工作聚焦2XXX(AlCuMn)系列——包括含锂的合金,以及传统7075(AlZnCuMn)合金——拥有可观的背景数据,它们的微结构不均匀性主导着局部腐蚀响应。项目技术方案将包括微结构和宏观建模,表征生产过程中的变形如何影响腐蚀,以及对腐蚀样品的快速评估。这些技术将确认在组件设计中加入腐蚀预测的方法。此外,力学性能预测模型也将被评估。
项目主要工业参与方为联合技术公司研究中心,洛克希德·马丁,DNV GL公司,计划2018年1月完成。成果完全部署后,腐蚀设计和力学性能设计模型可一并使用,为制造商在设计阶段制定合金规范时提供支撑,减少超越规范出现大腐蚀裕度的风险,以及加工导致非期望敏感性从而未达到规范的风险。
九、使用离子液体的金属电化学沉积
由于耐摩擦和防腐的表面处理已经用了数十年,六价铬电镀硬铬的可接受替代工艺仍包含电镀液,环境法规要求消除六价铬电镀液及其它包含六价铬的表面处理化学品。预计使用离子液体的新型电镀技术,以更环境友好的方法从三价前体成形金属铬层,提供接近传统硬铬特性的可能,尽管在电镀效率和成本上有些折衷。未来的开发,需要优化离子液体电镀工艺,并且面向最终应用优化表面层性能。同时,离子液体电镀液也可用于沉积铝,主要是耐摩擦和防腐应用,涉及诸如紧固件和基础金属(一般是高强钢)防护。针对物理气相沉积工艺或现有Sigal工艺(采用有害有机金属前体和有机溶剂,如甲苯)来镀铝,业界渴望有一个合适的和环境友好的替代方案,比如以离子溶液电镀铝金属。
项目将探寻以选择的离子液体增强铬和铝金属层电镀,用于耐摩擦(如硬铬替代)或防腐层(镀铝),并且通过评价制造成熟度(MRL)的提升确认这一涂层的性能。1)铝基板——目标是形成一个表面层作为合金化和回火铝基板的保护涂层,用于普惠为发动机开发的新型铝锂合金。预想的性能与2000系列基板高纯铝镀层的Alcald家族相对应。2)高强度钢基板——从离子液体镀铝,首要目标是替代钢上的电镀铬用于耐摩擦和防腐应用,并可替代物理气相沉积或Sigal工艺的铝涂层,从甲苯中溶解的有机金属铝盐电镀生成铝层。预计用在高强钢紧固件和组件,诸如起落架轮轴。减少硬化钢组件氢脆变的趋势是次要目标。
项目主要工业参与方为联合技术公司研究中心、洛克希德·马丁、Xtalic、伊顿。项目通过以下流程演进MRL的提升:1)为应用到感兴趣组件(如摩擦需要,腐蚀性能)的涂层定义系统级性能属性;2)确认并优化组件或感兴趣替代品的涂层工艺;3)生产原型组件或其替代物(如果实际组件证实无法合理获得);4)使用相关OEM提供的指标确认组件性能;5)为规模化工艺开发参数和指标以试验批产。
更多关于材料方面、材料腐蚀控制、材料科普等方面的国内外最新动态,我们网站会不断更新。希望大家一直关注中国腐蚀与防护网http://www.ecorr.org
责任编辑:王元
投稿联系:编辑部
电话:010-62313558-806
中国腐蚀与防护网官方 QQ群:140808414
免责声明:本网站所转载的文字、图片与视频资料版权归原创作者所有,如果涉及侵权,请第一时间联系本网删除。
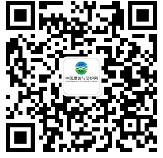
官方微信
《中国腐蚀与防护网电子期刊》征订启事
- 投稿联系:编辑部
- 电话:010-62316606-806
- 邮箱:fsfhzy666@163.com
- 中国腐蚀与防护网官方QQ群:140808414