近年来全球经济低迷,钢铁产能持续过量,但市场对高强钢和先进高强钢板的需求却增长迅速。为提供先进材料,支持汽车制造业的发展,宝钢不断努力,持续开发了多种先进高强钢产品及相关应用技术,包括第一代、第二代和第三代先进高强钢。本文主要介绍了宝钢先进高强钢产品的设计概念、性能和相关应用,并进一步介绍了集成了宝钢先进高强钢和先进成形技术的轻量化概念白车身(BCB)。
1 前言
由于全球经济衰退和钢铁产品的过量供给,中国钢铁市场正在加紧落实去产能政策。但不同于过量供给的钢铁产业,在过去数十年,中国汽车产量每年都大幅增长,并仍未达到发展的顶峰。
2015 年中国汽车产量超过2450 万辆,连续七年位居世界第一。与此同时,汽车行业的燃油法规也愈加严格,到2020 年,中国乘用车燃料消耗量限值标准将是百公里5 升,2025 年百公里油耗进一步降至4 升。汽车产业的迅猛发展导致汽车用钢需求量增长迅速,“节能减排、耐腐蚀和被动安全”性能要求的提高也使汽车钢板的产品结构发生了很大变化。镀锌汽车板、高强汽车板、先进高强汽车板和热冲压汽车板近年来发展势头迅猛。
传统高强钢通过固溶强化、析出强化或晶粒细化来提高强度,而先进高强钢则通过相变强化,其组织包括马氏体、贝氏体和残余奥氏体。先进高强钢包括双相钢(DP 钢)、相变诱导塑性钢(TRIP钢)、复相钢(CP 钢)、马氏体钢(MS 钢)和孪晶诱导塑性钢(TWIP 钢),这些钢种与传统高强钢相比,兼具强度和韧性,因此具有更高的碰撞能量吸收能力,在保证汽车减重的同时仍可以满足安全性要求。
根据国际钢协在过去20 年间所倡导的汽车轻量化项目,如超轻车身(ULSAB)、超轻覆盖件(ULSAC)、超轻悬挂件(ULSAS)、超轻概念车项目(ULSAB-AVC)和未来钢制汽车项目(FSV)的研究结果表明,先进高强钢是汽车轻量化的主要材料。上述汽车轻量化的成果显示出先进高强钢作为较好的汽车减重材料,可以在保证成本和供货的同时提升安全性能。
2 宝钢先进高强钢的研发历程
宝钢从1999 年开始研发双相钢,抗拉强度级别为590MPa 和780MPa,于2003 年实现了DP590的商业供货,并于2006 年开发出DP 和TRIP 钢的镀锌板。为了生产超高强钢(UHSS,抗拉强度≥780MPa),宝钢于2007 年组建了专门生产先进高强钢的产线,并于2009 年投产,显著地促进了先进高强钢的开发和应用。迄今为止,宝钢已开发出多种镀层和普冷的先进高强钢,包括2012年全球首发的淬火-配分钢(QP 钢)、1180MPa 级别的DP 钢、1700MPa 级别的MS 钢、780MPa 级别的TRIP 钢、980MPa 级别的CP 钢、1800MPa 级别的热冲压钢,以及新一代先进高强钢,如中锰钢(Mn-TRIP 钢)和低密度钢(δ-TRIP 钢)。目前,宝钢是全球少数能生产和商业供货全部三代先进高强钢的钢企之一。
3 先进高强钢产品和技术
3.1 先进高强钢组织性能
图1 描述了宝钢生产的先进高强钢(抗拉强度≥780MPa)的典型力学性能。与第一代先进高强钢相比,在相同抗拉强度下,第二代先进高强钢(TWIP 钢)具有更加优异的延伸率,而第三代先进高强钢的延伸率处于二者之间。先进高强钢的扩孔率也彼此不同,在所有1GPa 的先进高强钢中,CP 钢具有最高的扩孔率,但延伸率最低。
先进高强钢不同的微观组织决定了其不同的力学性能。图2 所示是先进高强钢典型的组织形貌。其基本的相组成包括铁素体、马氏体、贝氏体和残余奥氏体。根据不同的性能要求,需要调控先进高强钢的各相比例,例如TWIP 钢为奥氏体单向组织,DP 钢为铁素体+马氏体的双相组织,TRIP 钢则拥有铁素体、贝氏体与马氏体三相组织。
3.2 DP 钢的产品性能稳定性
DP 钢拥有低屈强比,高加工硬化率,高烘烤硬化值,无屈服平台和无室温时效等性能特点,被广泛应用于制造需要高强、高冲击吸收性和高成形性的汽车零部件,例如车轮、保险杠和其他加强件。DP 钢的基本成分是c 和Mn,有时也加入Cr 和Mo 来提高强度。现阶段市场中,DP 钢是主要的先进高强钢品种,宝钢DP 钢的制造已进入成熟期。产品稳定性是制造业的关键技术,高强度钢在成形时回弹比软钢难控制,这主要是由于高强度钢屈服强度波动范围较大造成的,随着钢板强度级别的提高,屈服强度的波动范围也随之提高,对高强钢产品的控制带来了更高的要求。
在当前的控制水平下,冶炼控制尚不能满足在相同退火工艺下获得稳定的力学性能,因此有必要根据主要合金元素的含量(C/Mn 等),设计并采用更加精细的退火工艺。
图3 以冷轧DP980 为例,描述了根据主要合金元素含量(C/Mn 等)设计精细的退火工艺的方法。在通常状态下,合金元素含量的增加会提高屈服强度。如果采用中值控制冶炼将会得到中等的力学性能,而成分位于上限或下限的将会得到较高或较低的力学性能。
但是如果根据主要合金元素的含量(C/Mn 等),采用精细退火工艺控制,那些成分高于上限或低于下限的带钢同样可以将性能控制在中值附近。在这种工艺调控下,退火温度将根据成分的变化量进行调整、控制,以获得符合设计标准的力学性能,如图3 所示。宝钢开发的这一技术使DP980 的波动范围提高了30%。
3.3 高si 钢的选择性氧化
QP 钢的概念首先由JohnSpeer 等人于2003 年首先提出,继而由宝钢在2012 年实现产品全球首发。截至目前,宝钢已经开发出多种强度级别和不同表面镀层的QP 钢,包括抗拉强度在1000MPa 以上、延伸率超过21%的QP980 和抗拉强度在1200MPa 以上、延伸率超过15%的QPll80,如表1 所示。QP 钢由于具有高强度和高成形性,已成为对结构要求复杂、强度要求很高的结构和安全件的优选方案。
通常认为,Mn 和Si 是钢中有效的强化元素,因而在QP 钢中大量使用,其中Mn 含量超过2.0%而Si 含量超过1.0%。但是,经由退火工艺处理,Si 和Mn 都会向带钢表面扩散,因而会导致表面出现选择氧化而形成氧化层。这种表面氧化层会导致较差的磷化效果或带钢表面由于与熔融锌的润湿性较差而脱锌。因此,在早期研发阶段,QP 钢表面常见有各种表面缺陷,极大地限制了QP 钢在汽车行业的商业化应用。
为了解决这些问题,需要避免带钢表面的选择氧化。目前,宝钢已经开发出相应的有效技术来控制退火炉中的氧含量,以抑制表面氧化。通过调节退火炉中气氛的露点温度,带钢表面的氧化程度得到控制,并从外氧化转变为内氧化,且内氧化层的厚度也可以被优化调控至合适水平,如图4 所不。
3.4 Mn-TRIP 钢
Mn-TRIP 钢是第三代先进高强钢中非常有前景的产品之一。先进高强钢由于TRIP 效应而获得的优秀力学性能引发了钢铁研究机构浓厚的兴趣。理解相变诱发塑性及相应的最优力学性能的关键是残余奥氏体的稳定性。
Mn-TRIP 钢通常含有约4%-10%的Mn 和较低含量的c,强塑积超过30GPa%。这种优异的力学性能取决于其成分和退火工艺,以控制残余奥氏体体积分数和稳定性。由于均匀分布的c 和Mn 不足以保证奥氏体在室温状态下稳定存在,Mn-TRIP 钢的热轧组织通常全部转变为马氏体。但通过退火调控,c 和Mn 从铁素体中配分到奥氏体,提高了奥氏体稳定性,从而使奥氏体在室温下稳定存在并具备TRIP 效应,因而为Mn-TRIP 钢提供了优异的力学性能。
宝钢在2014 年成功实现了1000MPa 和1200MPa 级别的冷轧/热镀锌Mn-TRIP 钢的工业试制,并进行了多项性能评估,包括弯曲性、扩孔性、延迟开裂性,成形极限(FLD)、动态拉伸性能、不同温度下的拉伸性能、可焊性等。
许多研究都报道了Mn-TRIP 钢强塑积超过30GPa%的优异的强度和韧性匹配。但是,由于传统Mn-TRIP 钢的组织均是由铁素体和奥氏体组成,因此这些研究中Mn-TRIP 钢的抗拉强度均未达到1500MPa。在退火过程中,在两相区进行的奥氏体稳定元素的配分,如c 和Mn,决定了奥氏体晶粒的稳定程度。通常在室温下出现的马氏体表明奥氏体的稳定性较差,由于没有TRIP 效应,相应的韧性就会变差。如何获得由马氏体和稳定性良好的奥氏体组织将成为获得1500MPa级Mn-TRIP 钢的关键问题。
Mn-TRIP 钢还可以被用于低温热冲压成形工艺,因为其具有较低的Ac3 温度。相关报道指出,与传统的22MnB5 钢相比,Mn-TRIP 钢拥有更好的性能和一些独特的优势,如节能、低成本等。
3.5 低密度钢
铁素体低密度钢通常包含3%-6%的Al,由于其密度较低,兼具极好的强度、韧性和可加工性,因此被视为汽车轻量化的潜力材料之一。Al 的加入会导致铁素体低密度钢晶格点阵扩大,并降低钢的摩尔质量,从而降低其密度。铁素体低密度钢的铁素体-贝氏体-残余奥氏体组织结构也通过TRIP 效应保证了优异的力学性能。在铁素体低密度钢中,一个特征组成相便是凝固过程中形成、并在后续热处理和加工过程中残余的δ-铁素体,由于过量Al 的存在,δ-铁素体不发生相转变。
宝钢从2009 年开始开发铁素体低密度钢,并在最近率先生产出800MPa 级别的铁素体低密度钢。通过铸造、热轧、冷轧和连续退火生产,这种钢的密度能够降低约6%。图5 所示为铁素体低密度钢典型组织的EBSD 照片,其中δ-铁素体晶粒和残余奥氏体岛呈带状分布,并未见到有板条状的残余奥氏体,这可能是由于贝氏体相变被明显推迟。残余奥氏体的平均晶粒尺寸为0.8μm。
由于残余奥氏体的晶粒尺寸和体积分数决定了低密度钢的力学性能,0.8μm 的残余奥氏体晶粒尺寸和20%的残余奥氏体含量可以使低密度钢的强塑积达到30GPa%。为满足该钢种的下游使用,尚需进行多种性能评估。
4 先进高强钢的应用
4.1 宝钢白车身项目
为了提升和展示先进高强钢和先进成形技术的进步和应用,宝钢于2011 年开展了研发钢基白车身项目——宝钢白车身(BCB)。作为B 级车白车身,BCB 自重仅284k,比市场平均水平低10%-20%。测试表明:其扭转模量为23628N/mm,弯曲模量为18868N/mm。BCB 的轻量化系数为2.7,优于市场平均水平20%。C-NCAP 和E-NCAP 分析表明,BCB 的正碰、侧碰都达到了五星标准。
为了满足减重和高性能要求,宝钢白车身77%的部件使用了高强钢,包括几乎全部新研发的先进高强钢产品,如QP1180、MSl500 和TWIP950,以及新研发的先进成形技术,如热冲压成形、液压成形、辊压成形、变厚板和TWB 技术等。图6 标示出这些先进高强钢和成形技术的应用区域,共包括309 个零部件,并不包括车门,车顶和行李箱盖板。这一概念白车身的研究表明,钢铁通过创新,仍有很大的轻量化减重空间。钢铁仍是今后很长一段时间内汽车的主导材料。
4.2 冷成形和热成形BCB 对汽车零部件中强度和安全性能要求最高的零部件之一B 柱进行了系统的评估和方案比较。其中材料方案、侧碰性能和零部件总成本是关键点。BCB 的侧碰评估见图7,在总共11个分析部位中,6 个位于B 柱,5 个位于车门。测试车的限重为1507kg,变形门槛质量是950kg,其中碰撞速度根据E-NCAP 标准控制为(50±1)km/h。
B 柱冷成形和热成形的材料方案如表2 所示,冷成形采用超高强钢QP1180,热成形采用超高强钢PH1500。两种材料的厚度规格都是1.4mm,因此两个零部件的重量相同。
图8 描述了QP1180 和PH1500 两种材料方案的碰撞性能对比,结果表明,二者的性能相差不大,部份测试点QP1180 的性能优于PH1500。
5 结论
1)宝钢开发出多种先进高强钢产品,包括第一代、第二代、第三代先进高强钢和相应的先进制造工艺;2)“节能减排”要求的提高促进了高强度钢的快速发展,先进高强度钢将成为今后汽车轻量化的主导材料;3)宝钢轻量化白车身(BCB)项目研究表明,目前的汽车白车身通过新材料和新技术的应用,仍有10%-20%的减重空间;4)关键零部件及其总成有多种技术解决方案,第三代钢如QP 钢等的出现,为复杂的结构件(如A 柱、B 柱和保险杠)等提供了除热冲压外的另外一种新选择;5)钢铁企业需要来自用户和社会的支持,以促进上述新研发的先进高强钢的应用。
更多关于材料方面、材料腐蚀控制、材料科普等方面的国内外最新动态,我们网站会不断更新。希望大家一直关注中国腐蚀与防护网http://www.ecorr.org
责任编辑:王元
投稿联系:编辑部
电话:010-62313558-806
中国腐蚀与防护网官方 QQ群:140808414
免责声明:本网站所转载的文字、图片与视频资料版权归原创作者所有,如果涉及侵权,请第一时间联系本网删除。
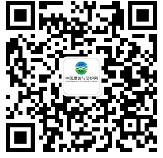
官方微信
《中国腐蚀与防护网电子期刊》征订启事
- 投稿联系:编辑部
- 电话:010-62316606-806
- 邮箱:fsfhzy666@163.com
- 中国腐蚀与防护网官方QQ群:140808414