航空发动机被誉为现在工业皇冠上的明珠,是一个极端复杂的系统,是一个在极端苛刻的恶劣条件下(高温高压高应力)追求长期、稳定、安全的极端性能的尤物,难做自然是一定的。因为航空发动机涉及到一系列高性能涡轮叶片、单晶高温合金制备和冷却、热障涂层防护等先进材料制造、加工技术。路上随便找一个老大爷,聊到航空,或许都会对我国造不出高性能的航发痛心疾首。
1 航空发动机的结构
火箭
小时候,我们都玩过气球。将气球吹大后,一旦松开手指,气球就会飞起来四处乱窜。这是因为气球中的气体在向外泄的同时,给气球一个向前的反作用力。
火箭就是用这个原理,携带大量的燃料来制造气体,再迅速向后排出从而获得推力。
而航空发动机,也是在用这个原理让飞机飞行的。所不同的是,飞机在大气层下飞行,不需要自带燃料制造空气。
要说航发的原理也很简单、巧妙,发动机首先通过风扇吸入空气,然后压气机将空气压缩提高压力,然后压缩空气进入燃烧室与燃料混合点燃,最后将高速气体喷出推动涡轮旋转;涡轮和压气机以及风扇是连在一或者两根轴上的,涡轮旋转又会带动风扇与压气机转动,不断压缩空气产生部分推力,燃气推动涡轮旋转后经尾喷管喷出,又会产生部分推力。这两部分推力共同为飞机提供动力。
更高性能的航发,需要更高性能的涡轮叶片
要想获得在尺寸小、重量轻的前提下获得高性能,也就是通常所说的提高推重比(发动机的推力和自重的比值),主要的措施是提高燃气温度。因为发动机的推力主要是靠燃烧产生的热气体与冷空气混合产生的气压差来产生的。气压差越大,推力越大。要想提高气压差,燃烧温度就要更高。
数据显示涡轮前进口温度每提高100度,在发动机尺寸不变的条件下,推重比可以增加10%.
早在1928年,英国工程师就提出了航空发动机的构想。但是,直到1939年,第一台发动机才问世。因为按照当时的设想,根本没有材料扛得住它的高温。
现在,主流航空设备上采用的是推重比是7-8的第三代航空发动机,如美国的F-15、F-16、F-18,中国的歼10、歼11等战机,民航的各个系列如空客A320、波音737等。涡轮前进口温度大约在1680-1750K.美国普拉特·惠特尼公司研发的F119发动机(准备于美军F-22战机,世界上第一款五代机),推重比10.8,涡轮前进口温度达到了1900K.这个温度,已经超过碳钢的熔点上百度了。
除了高温,涡轮叶片同时还在以极高速旋转。高速旋转导致涡轮叶片必须承担极高的离心力。而在高温下、高加载下,金属材料会发生蠕变。简单来说,蠕变是在一定温度下,材料长期在较小的外力作用下发生形变。蠕变对于叶片来说不是好事,它能使叶片径向伸长 、扭转和弯曲,影响叶片的使用寿命。
另外,材料在使用时会发生疲劳,可能导致疲劳断裂,危及安全。
因此,涡轮叶片材料既要耐高温,又要低蠕变,耐疲劳、力学性能还要好。要说它好造,那恐怕现在也没有其他难造的东西了。
2 涡轮叶片选材
越来越高的标准,涡轮叶片自然不能使用等闲材料。从第三代航发,一般采用单晶或者定向合金制造涡轮叶片。
通常铸造的金属材料都是多晶的,为什么要用单晶或者定向合金?
对于多晶材料,晶粒与晶粒之间有晶界。在某些场合下,晶界对于材料性能提高有好处。但在上个世纪60年代,美国惠普公司发现对于涡轮叶片来说,晶界是个"坏孩子".普通铸造多晶高温合金中与应力轴垂直的晶界是高温应力下产生裂纹的"源头",所以必须减少晶界,由此发展了高温合金定向凝固技术。
3 单晶高温合金
定向凝固高温合金通过控制结晶生长速度、使晶粒按主承力方向择优生长,可以改善合金的强度、塑性、热疲劳性,使涡轮叶片的使用温度达到了 1273K .
进一步,航空业发展了单晶合金涡轮叶片,其耐温能力、蠕变强度、热疲劳强度、抗氧化性能和抗腐蚀特性较定向凝固柱晶合金有了显著提高。
但是,单晶合金涡轮叶片的制造工艺难度可就高了许多。目前,最常使用的用于制造单晶叶片的工艺方法是螺旋选晶法,其基本原理就是利用选晶器的这种狭窄界面,只允许一个晶粒长出它的顶部,然后这个晶粒长满整个型腔,从而得到单晶体。其晶体竞争生长机制是螺旋结构总的攀升走向正好与散热方向相反,致使螺旋体内散热均匀,因此在整个螺旋形生长过程中,位向最适合生长的那个晶粒将其他众多的初生晶粒一一淘汰,不断长出枝晶并最终进入试样本体成为单晶铸件。单向散热看似简单,其实这个过程是极其难控制的,这涉及到材料本身及铸模的热物理特性,并且考虑制造过程中的散热条件等因素的影响,以及晶体的生长速度等,这些都需要经过严格的实验设计以及大量的实验数据,经计算后才能够得出准确的结果,难度非常之大。
此外,高温合金中还添加微量元素提高使用温度。第二代单晶合金与第一代单晶合金相比,通过加入3%的铼、适当增大了钴和钼的含量,使其工作温度提高了30 K.第三代单晶合金Rene N6和CMSX-10加入高达5wt%以上的铼,显著提高高温蠕变强度。第四代单晶合金,通过添加钌,进一步提高了合金微观结构的稳定性,使用温度已达到了1473K.
4 冷却技术
不过采用单晶高温合金材料并不能解决问题。实际上,单靠寻找更耐高温的材料来满足更高涡轮前温度是不切实际的。目前,涡轮前进口温度已达到了 2000K 左右,比高压涡轮叶片金属材料的熔点高400K.而近年来,涡轮前温度以每年平均提高 20K的速度增加,而金属耐温程度仅以每年约 8K的速度增加。
两者之间的缺口就必须依靠航发先进的冷却系统来实现,例如气膜冷却技术。通过喷入冷气,借助高温燃气的压力和摩擦力让其粘附在壁面附近,形成一个较低的冷气膜,将壁面同高温燃气隔离,并带走部分高温燃气或明亮火焰对壁面的辐射热量,从而对壁面起到良好的保护作用。
据数据记载,目前的冷却技术可以实现温降已达400 K-600 K.
随着航空发动机涡轮前温度的不断提升,原有的单通道空心冷却叶片的冷却效果已经不能满足现实需求,发展更为先进更复杂的多通道多路冷却方案成为下一代航发的关键技术。而每一次冷却方案的优化都对涡轮叶片的设计和制造提出了极大的考验!
冷却技术的发展,依然不能完全解决、或者满足材料承载温度与涡轮前进口温度之间的差距。因此,还需要对在涡轮叶片燃气流道表面喷涂热障涂层。
5 热障涂层
热障涂层(简称 TBC)是在零件表面沉积黏接 一层低导热系数的材料,利用其低热传导特性,在其内、 外表面形成温降,用以降低零件表面工作温度(或提高零件的承温能力)的方法。据资料介绍,热障涂层可取得 50K-150 K 的隔热效果。
目前在涡轮发动机上获得实际应用的热障涂层均为双层结构: 表层为陶瓷层,主要起隔热作用, 此外还起抗腐蚀、 冲刷和侵蚀的作用 ; 内层为金属粘接层, 主要起改善金属基体与陶瓷层之间的物理相容性, 增强涂层抗高温氧化性能的作用。
由于是把涂层涂覆在金属基体上,需要考虑涂层的附着力,对金属基体显微组织稳定性的影响以及涂层与金属因热膨胀系数差异而可能导致的剥落问题等,这就需要空心叶片金属材料学科领域联合诸多其他领域的相关专家合力公关、共同研发。
至此,一片单晶空心叶片真正的造价堪比同重量的黄金或许并不为过。甚至高性能的叶片也是有价无市。
同时,我们也能看到。为了能让涡轮叶片正常工作,材料科技工作者们真是无所不用其极。
免责声明:本网站所转载的文字、图片与视频资料版权归原创作者所有,如果涉及侵权,请第一时间联系本网删除。
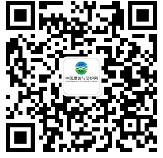
官方微信
《腐蚀与防护网电子期刊》征订启事
- 投稿联系:编辑部
- 电话:010-62316606-806
- 邮箱:fsfhzy666@163.com
- 腐蚀与防护网官方QQ群:140808414