从"人、机、料、法、环"谈港珠澳大桥钢结构防腐施工质量控制
2015-05-08 16:35:16
作者:杨振波来源:=$docheckrep[1]?ReplaceBefrom($ecms_gr[befrom]):$ecms_gr[befrom]?>
港珠澳大桥是由广东省牵头粤港澳三地共同建设的特大型交通基础设施,连接香港、澳门、珠海三地,工程规模宏大,受到三地民众、媒体和社会高度关注。大桥全长49.968公里,其中主体工程“海中桥隧”(含桥梁工程与岛隧工程)长35.6公里,设计使用寿命120年。作为中国建设史上里程最长、投资最多、施工难度最大的跨海桥梁,项目除了在工程建设质量<Quailty>上精益求精,在HSE(健康<Health>、安全<Safety>和环境<Environment>)管理体系上,与国际标准接轨,提出了严格的HSE要求,由此引发了一系列关键技术的创新,包括在桥梁防腐涂装领域,这些都有别于国内以往桥梁工程,在中国桥梁史上具有里程碑式的意义。
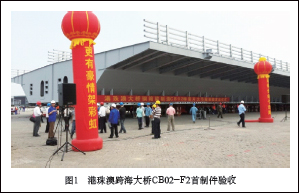
钢结构防腐工程量虽然仅占港珠澳大桥桥梁工程建设的很小比例,但它不仅影响到待涂装工件的涂装质量、成本等,还对钢结构成品件的交验、安装施工、成桥通车工期等都有直接的影响。涂料行业有“三分料,七分工”的说法,涂装过程出现的问题会促使整个大桥流水施工的停滞,造成不可挽回的损失。
接下来将以CB02-F2首制件为例,介绍如何使先进的管理方法与理念与技术相结合,从人员管理(人);涂装厂房与机械设备(机);材料设计选用与检测(料);施工工艺与流程(法);安全、环境与职业健康(环)五个维度进行控制,对我国防腐施工技术与管理能力的提高,改变国内防腐涂装脏、乱、差的现象,与国外工程先进水平接轨,具有现实的意义。
工程腐蚀环境特点与钢结构涂层体系设计
港珠澳大桥位于广东省珠江口外的伶仃洋海域,属亚热带海洋性气候,根据ISO12944-2《色漆和清漆 钢结构的防腐蚀保护涂层体系 第2部分:环境分类》,港珠澳大桥桥梁工程所处的大气腐蚀环境为高盐度的沿海和近海地区,属于最高腐蚀等级的C5-M类型。高温、高湿、高盐度以及汽车尾气中的硫、氮等化合物会对大桥的钢结构造成严重的腐蚀。
根据JT/T 722-2008《公路桥梁钢结构防腐涂装技术条件》,对于C5-M状况下,25年防护寿命的长效防护体系,钢结构外表面一般采用“热喷锌铝+封闭漆+环氧中间漆+氟碳面漆”的设计体系。国内的许多跨海大桥,如厦漳跨海大桥、青岛海湾跨海大桥等都采用了上述钢结构防护体系。
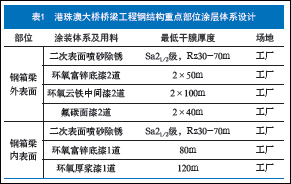
港珠澳大桥桥梁工程钢结构重点部位涂层体系的设计方案请见表1。该体系与以往跨海桥梁工程的最大不同点,主要是采用了环氧富锌底漆来取代热喷锌铝涂层。就底漆的防护性能而言,热喷锌铝涂层(含封闭)是优于环氧富锌底漆。根据JT/T 722,表1的体系通常用于C4或C5-I这些较弱一些的腐蚀环境。
之所以采用这样的设计,是由于港珠澳大桥项目作为一个举世瞩目的国际工程,特别关注于HSE体系。由于热喷锌铝过程中,会产生大量的“锌”、“铝”、“氧化锌”、“氧化铝”蒸汽。“锌与氧化锌”蒸汽可能使工人得“锌热病”;而长期吸入金属铝粉或氧化铝粉尘更会引起肺部病变,使工人受到“铝肺”这种职业病的危害。所以在防护体系的底涂层选择中,港珠澳大桥采用了“环氧富锌底漆”来取代“热喷锌铝”涂层。
为了执行严格的HSE标准,在涂料的性能要求上,港珠澳大桥也在国内首次提出了针对性的要求。在桥梁涂装工业漆应用领域,溶剂型涂料的使用仍处于主流地位。该类型涂料以其涂层性能好,施工方便,可冬季低温下施工等优点,在重防腐领域还很难被水性涂料、无溶剂涂料所取代。但是,溶剂型涂料的VOC(挥发性有机化合物)造成环境的污染已成为全球关注的重点问题。而国内涂料行业领域,除了在建筑涂料、木器涂料等少数领域之外,对于工业漆的VOC,特别是桥梁领域用溶剂型涂料的VOC指标,还没有相应的国家规范。
而港珠澳大桥国内首次对防腐涂料的VOC、重金属等环保性指标进行了如下规定:
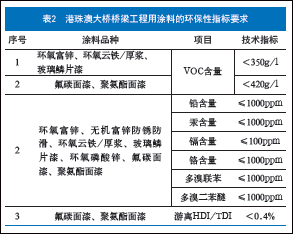
港珠澳大桥涂装工程的创新点
港珠澳大桥桥梁工程钢结构防腐涂装项目,有别于国内众多桥梁工程,在确保工程质量的同时,必须兼顾HSE的高标准要求。因此,项目在建设过程中,提出了多个创新点:
1、国内的杭州湾跨海大桥、青岛海湾大桥等大型桥梁的通航孔桥采用钢箱梁制作,而非通航孔桥为混凝土箱梁构造。而港珠澳大桥桥梁工程全长22.9公里,通航孔及非通航孔桥将全部采用钢箱梁结构,总用钢梁将达到42.5万吨。由于混凝土箱梁可不涂装,但钢结构必须进行防腐保护,这也使港珠澳大桥桥梁工程的防腐施工工程量创下了中国乃至世界桥梁史之最;2、通常在进行桥梁钢结构防腐涂装时,底漆、中间漆及第一道面漆均在工厂进行涂装。而最后一道面漆则是在钢梁吊装到桥址现场以后,对磕碰处及焊缝处进行补涂,然后进行一次全面涂覆,可确保最终的涂装质量与效果。
由于港珠澳大桥所处的地理位置正好位于中华白海豚保护区,为了防止最后一道面漆在涂覆过程中污染相关海域,从而影响白海豚生存环境。项目要求底、中、面三道涂层必须在工厂一次完成,钢梁吊装到桥址现场后,仅进行涂层损伤处与焊缝处的补涂,这样可最大程度的减少施工过程中涂料的污染。但由于没有最后一道面漆的通涂,会减少面涂层的整体性以及保护及涂装效果。这就要求对传统的涂装工艺进行变革,采用新的工艺。
3、港珠澳大桥在HSE方面的高要求,严格规定在工程建设中,必须采用降低能耗、改善环境、提高工效、保障施工人员健康的工艺,这样涂装厂房及涂装环境是制约其要求的关键环节。而以往国内桥梁防腐工程,防腐分包队伍通常是借用相关方的厂房,但这些厂房的设计是根据相关方自身需求定制的,往往不能满足这些桥梁防腐在施工过程中,高效率、高质量的要求。这也使以往桥梁防腐施工的涂装环境较差,严重影响工人的健康及造成环境污染。
而港珠澳项目国内首次将涂装厂房设计及安装连同其报价,交由防腐分包队伍根据招标文件要求进行实施,从而确保各类除湿加温系统、通风除尘系统、漆雾过滤系统最终形成的环境条件与港珠澳大桥工程量匹配,达到国家标准要求。
4、项目国内首次对防腐涂料的VOC指标进行了规定。严格意义的VOC指标,既包括涂料中的VOC,也包括施工过程中添加的VOC。这就要求必须采用高固体含量的涂料;同时在施工过程中,必须少添加涂料稀释剂以及清洗用的稀释剂。涂料的VOC低,固含量高,必然导致涂料的粘度增加,施工难度加大,特别是氟碳面漆规定涂装工艺为2×40m。以往工程中,为了确保1道涂装厚度为40m左右,在采用高压无气喷涂设备施工时,稀料的添加量往往超过8%,而不考虑VOC的要求。但在港珠澳项目中,这样做已经违背了HSE的要求,必须采用新工艺来解决这个问题。
除上述几个创新点,港珠澳大桥管理局也希望防腐施工队伍主动采用一些新技术,来确保质量与HSE同步,让港珠澳项目成为防腐涂装领域的一座里程碑。
首制件涂装质量控制
人员管理(人)
同以往工程类似,港珠澳大桥防腐涂装工程CB02-F2标段首先成立一个项目管理团队,由项目经理,技术总工,项目副经理,质量管理工程师,试验检测管理人员,计划进度及界面管理人员,技术人员,HSE管理人员,财务预算人员及其他人员组成。有别于以往工程,项目专门设置了项目总协调人,由可充分调动公司资源的承包人副总经理及以上级别人员担任,主要负责与发包人进行项目重大事宜的沟通以及与第三方的外部协调工作,解决工程中出现的非技术性问题,确保工程顺利实施。
国内以往防腐涂装工程,仅有少数特种工种如高空作业、电工、焊接等有执业资格要求。而对于专门从事喷漆涂装作业的具体操作施工人员确没有相应要求。喷漆涂装是一个劳动力密集工种,技术工人的技术水平决定了大桥的最终涂装质量与防腐寿命。涂装工国家职业资格认证已经启动,国内汽车等行业已经要求喷漆工需取证上岗作业,这是涂装行业未来发展的趋势,项目部也要求重点喷漆岗位持证上岗,走在了桥梁涂装行业前沿。
涂装厂房与机械设备(机)
港珠澳大桥在HSE方面的高要求,严格规定在工程建设中,必须采用改善环境、提高工效、保障施工人员健康的工艺,这样涂装厂房及涂装环境是制约其要求的关键环节。项目国内首次将涂装厂房及设备安装连同其报价,交由防腐分包队伍根据招标文件要求进行实施,从而确保各类除湿加温系统、通风除尘系统、漆雾过滤系统最终形成的环境条件与港珠澳大桥工程质量要求匹配。CB02-F2标段的涂装厂房与机械设备的建设包括:
标段二次涂装厂房(分段喷砂房、喷漆房);
喷砂系统;
钢砂输送回收处理系统;
通风除尘系统;
漆雾及有机废气处理系统;
除湿系统;
送风风管系统;
涂装工场照明系统。
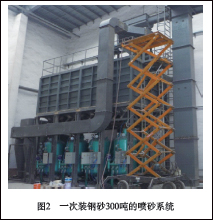
材料设计选用与检测(料)
港珠澳大桥桥梁工程选用的主要涂料品种为环氧富锌底漆、环氧云铁中间漆及氟碳面漆,其他使用的涂料还包括无机富锌防锈防滑漆、环氧玻璃鳞片漆、环氧磷酸锌、聚氨酯面漆。
港珠澳大桥要求涂料供应方必须提供执行JT/T722-2008《公路桥梁钢结构防腐涂装技术条件》以及招标文件规定的权威第三方检测报告。在施工过程中,涂料供应商除了提供产品合格证、出厂检验报告、产品说明书以外,还要求监理与施工方对到厂的每批涂料进行现场的三方见证取样送第三方进行复检。因此,在首制件制作过程中,CB02-F2标段结合首制件工程量编制涂料采购计划,提交总包方审核采购,然后三方见证对每批涂料进场按规定进行抽样复检,送已批复的检测单位进行检验,检测合格后用于首制段涂装施工。
复检项目包含:富锌底漆的附着力、金属锌含量、干燥时间、不挥发分含量;环氧云铁中间漆、无机防滑、玻璃鳞片漆的附着力、干燥时间、不挥发分含量;氟碳面漆的氟含量、附着力、不挥发分含量、干燥时间、耐冲击性。
施工工艺与流程(法)
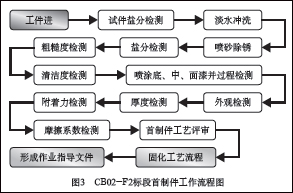
图3为CB02-F2标段首制件工作流程图,可以有效指导整个流程有序可靠的实施。详细的控制流程如下:
喷砂前的准备
(1)盐份检测及墩位处理
首先将首制节段B642采用平板车运至存梁厂进行盐份检测,并采用高压淡水对梁段的内外表面进行了清洗。在施工环境条件满足施工要求时,采用环保型自动回收喷砂机对钢箱梁6个墩位进行喷砂除锈处理,检测合格后涂装第一道富锌底漆;(2)表面净化处理
进行梁段的内外表面喷砂前的清洁及除油污施工,并对梁段的自由边、飞溅、焊缝等处理情况进行检查,发现问题及时通知制作方进行处理,复查合格后梁段转运至喷砂房;(3)脚手架搭设及泄水槽保护
脚手架的搭设采取固定脚手架与移动脚手架相结合,在喷砂房,钢箱梁内全部采用固定脚手架,箱梁外在钢砂回收系统地坑处采用固定脚手架,两侧采用移动式脚手架;在喷涂房,为防止碰撞产生火花,箱梁内的脚手架采取门式脚手架+木跳板,门式脚手架底部与箱梁接触区域全部用柔性橡皮包扎,箱梁外全部采用可移动楼梯式脚手架,底部滚轮是橡胶带刹车式的万向滚轮,可以有效的保证脚手架的稳定性。
为防止下斜腹板U肋在喷砂时钢砂进入,U肋端头使用封堵板将其密封保护;泄水槽等镀锌件采用帆布外衣对其进行包扎保护。
二次喷砂除锈
(1)环境条件及压缩空气检查
首制件上道工序报检合格后转运至喷砂房。检测喷砂房环境条件(环境温度、相对湿度、露点、梁段基体温度等)、空气压力及空气洁净度,均满足技术规范要求。开启通风除尘、除湿设备,将施工厂房的环境条件控制在技术规范规定的范围内。
(2)二次喷砂除锈及清砂
环境条件、空气压力和清洁度检测结果满足喷砂施工要求后,开始进行喷砂施工。
喷砂完毕后,进行清砂、清灰处理。首先人工将箱梁内部的大量存砂清理干净,然后用压缩空气将残存的砂子吹净,再用真空吸砂机将表面的灰尘及细砂吸净,最后用铲砂车将箱梁外部的钢砂铲运至自动收砂系统,回收至砂箱。清砂施工完成后,表面粗糙度、清洁度报检,合格后方能将首制件转运至喷涂房。
涂料涂装
(1)涂料配制与调控
配置专职涂料领用员和调配工,并在质检员及涂料供应商技术服务人员的指导监督之下进行配料,通过多方控制,有效的避免了涂料调配时可能出现的偏差及错误。
(2)预涂及端口的保护
对首制节段构件粗糙表面、不平整焊缝表面、板边、弯角、过焊孔、流水孔、其它孔眼以及喷涂不易的死角处进行环氧富锌底漆手工预涂。并安排专人对首制梁段对接环焊缝区域、纵向结构嵌补区域、内小车轨道端头采用胶带纸进行阶梯保护,保护区域满足大节段拼装施工要求。
(3)摩擦面的涂装及保护
首制节段各个部位保护完成后,采用空气喷涂机对摩擦面喷涂无机富锌防锈防滑涂料,漆膜固化后采取三夹板进行遮挡保护,避免其它涂料对其污染。
(4)内外表面环氧富锌底漆涂装
开启通风除尘、除湿设备,将施工厂房的环境条件控制在技术规范规定的范围内。预涂处理完成后,用压缩空气吹净钢箱梁表面的灰尘,然后,将箱梁内底板用塑料布铺设保护,最后使用高压无气喷涂机对节段内外表面喷涂环氧富锌底漆。每道底漆涂装前,均对上道涂层缺陷修复彻底、清理干净,使表面无灰尘,并采取先预涂再喷涂的工艺。
(5)桥面防护及环氧磷酸锌底漆涂装
待桥面的路缘石、立柱垫板采取胶带纸保护完成后,采用高压无气喷涂机喷涂环氧磷酸锌底漆。
(6)泄水槽环氧中间漆涂装
首先对泄水槽的镀锌层进行脱脂、拉毛处理,测量、记录镀锌层厚度后,将泄水槽周边用胶带纸进行保护,然后采用高压无气喷涂机喷涂环氧中间漆,待检测合格进入下道工序前对泄水槽涂层进行防护。
(7)外表面环氧云铁中间漆涂装
首先对底漆涂层缺陷修补、磨平,待报检合格后,将表面灰尘除净采用高压无气喷涂机喷涂环氧云铁中间漆。
(8)内表面环氧厚浆漆涂装
对内表面底漆涂层进行修补和清理,清理完毕并报检合格后,对内表面不易喷涂的部位进行预涂,再采取高压无气喷涂机进行环氧厚浆漆的涂装。
(9)外表面氟碳面漆的涂装
首先对中间漆的涂层清理修磨,表面灰尘除净并报检合格后,采用高压无气喷涂机进行氟碳面漆的喷涂。
重点工序控制措施
(1)梁段表面清理工序控制
a.钢结构表面锐角边磨圆及焊缝缺陷检查:钢箱梁交接时对钢箱梁结构焊缝缺陷及清磨情况进行自查,当发现问题时,立即通知钢结构制造单位进行处理。
b.可溶性盐份的控制:可溶性盐份的控制主要分梁段清洗前、梁段清洗后、梁段喷砂后三个阶段,这三个阶段对盐份含量进行全面监测,保证梁段盐份含量在可控范围内。
c.油污的检查:箱梁表面的油污需作为控制重点,将其表面清洗干净、彻底,防止磨料污染,影响涂装施工质量。
(2)喷砂施工控制
a.喷砂施工顺序遵循先下后上、先里后外、先难后易的原则。
b.对于焊缝、自由边等部位喷砂顺序遵循先焊缝、后自由边。
c.对于狭小、难喷部位重点喷砂、检查,并适当增加喷砂次数。
(3)预涂质量的控制
预涂是涂装施工质量的关键,在这道工序前期必须准备充分。
a.施工人员选择经验丰富、技术娴熟的预涂工人。
b.根据具体施工部位,合理选择预涂工具。
(4)喷涂质量控制
a.喷涂施工中,控制预涂涂层的厚度,在焊缝处采用刷涂工艺,避免预涂范围过大。
b.控制每种涂料第一道涂层的漆膜厚度及与预涂搭接部位的覆盖范围。
(5)涂层厚度的控制
a.根据梁段的施工面积制定配料定额,即通过涂料的用量,控制涂层的干膜厚度。
b.在涂料喷涂施工过程中采用湿膜卡随时对膜厚进行监测,并及时调整。
c.对喷涂施工人员进行专门的涂料技术参数、调配、使用知识的培训与交底,使之熟悉掌握涂料性能。
d.采用“双90”原则(90%的测量值不得低于规定干膜厚度,其余10%的测量值不能低于规定膜厚的90%)进行涂层厚度的最终控制。
(6)外观的控制
a.钢箱梁面漆涂装前,对喷枪难以喷涂到位的阴角部位进行预涂,其他部位采取喷涂施工,这样大大减少了预涂工作留下的刷痕,使得外观更加平整、美观。
b.在每一道涂料喷涂干燥后测量漆膜厚度,将图层较薄或较厚部位进行标记,为第二道涂料喷涂施工提供参考。
c.重点加强施工人员喷涂流挂、收枪工艺的技术培训,确保涂层外观质量。
安全、环境与职业健康(环)
项目部设置专门的HSE管理组织机构,责任层层落实到位;项目施工前进行涂装作业危险源与环境因素辨识,制定防范控制措施;编制报审HSE涂装专项方案及应急预案;组织全员进HSE教育培训,加强全体人员的管理及操作指导,提高职能人员的防范意识和技术水平;根据HSE相关管理制度加强现场管理。
结语
港珠澳大桥国内外首次在钢结构防腐涂装领域实施首制件制作及评审,体现建设方对防腐涂装质量的关注又上了一个新的台阶。
通过CB02-F2标段首制件涂装施工,验证了首制件施工工艺方案、施工工艺流程、HSE专项方案的合理性,最终首制件质量经评审后合格。
从“人、机、料、法、环”五个维度进行首制件流程梳理,并进行相应的质量与工艺控制,摸索出适合本工程钢箱梁涂装施工工艺,质量及HSE控制措施,并经过完善、改进、优化,为防腐涂装施工提供技术工艺参数、注意事项、材料和设备使用的可靠性、有效性,为未来大桥钢箱梁防腐涂装批量生产提供依据。
杨振波,1978.8,男,高级工程师,一级建造师,注册造价师,现任中航百慕新材料技术工程股份有限公司技术研发中心(北京市环保型防护技术功能涂料工程实验室)主任,中国腐蚀与防护学会防腐蚀施工与技术委员会委员,美国腐蚀工程师协会(NACE)会员,从事工业防腐涂料的研发工作。
相关文章
无相关信息
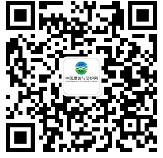
官方微信
《中国腐蚀与防护网电子期刊》征订启事
- 投稿联系:编辑部
- 电话:010-62313558-806
- 邮箱:fsfhzy666@163.com
- 中国腐蚀与防护网官方QQ群:140808414
点击排行
PPT新闻
铝合金LDH自修复自抗菌膜层构建
点击数:466
碳钢及合金钢应用与区别
点击数:393