刘安强1,肖葵1,董超芳1 ,邢士波1,2,李晓刚1,魏丹3
1北京科技大学腐蚀与防护中心,北京,中国,100083
2河北工程大学机电学院,邯郸,中国,056038
3中国科协学会服务中心,北京,中国,100081
Email: liuaq509@yahoo.cn
作者简介:
刘安强,男,汉族,1979年5月出生,甘肃省平凉市人,北京科技大学在读博士研究生。
2004年毕业于昆明理工大学机械系,获得学士学位,2007年毕业于昆明理工大学材料加工专业,获得硕士学位,2007.3 ~2009.8在攀枝花钢铁研究院工作,主要从事钒产品技术研发工作。
2009年9月考入北京科技大学材料科学与工程学院,攻读博士学位,师从李晓刚教授。主要研究方向为材料腐蚀与防护、材料腐蚀寿命评估及预测。
刘安强
摘 要:采用电弧喷涂技术在Q235钢板表面制备出了纯锌及锌铝伪合金涂层,并对涂层的性能进行了测试。考察了两种涂层在盐雾实验中的耐蚀性能,利用扫描电镜和X射线衍射仪分析了涂层组织结构及涂层表面腐蚀产物的相结构,测试了涂层在3.5%NaCl溶液中的电化学特性。结果表明:涂层均匀致密、孔隙率小,与基体结合良好。盐雾实验768 h后,纯锌涂层表面腐蚀产物主要为羟基氯化锌(Zn5(OH)8Cl2H2O),锌铝伪合金涂层表面腐蚀产物主要为羟基氯化锌(Zn5(OH)8Cl2H2O)、碱式碳酸盐化合物(Zn0.71Al0.29(OH)2(CO3)0.145∙xH2O)及尖晶石结构的氧化物 (ZnAl2O4);极化曲线测试结果表明:锌铝伪合金涂层的自腐蚀电流密度小于纯锌涂层,表现出更优越的防腐性能。
关键词:电弧喷涂;锌铝伪合金涂层;盐雾实验;耐蚀性
1 引言
对钢铁结构件进行长期保护,特别是对那些要求在服役期内不维护或少维护的特大型、重要的钢铁构件,热喷涂技术是最有效和最经济的长效防腐方法。近20年来,电弧喷涂因具有生产效率高、能耗少、成本低、操作灵活方便等特点[1],而获得了迅速发展,目前国际上已部分取代火焰喷涂和等离子喷涂,成为最热门的热喷涂技术[2]。电弧喷涂技术应用范围十分广泛,涵盖了防腐、耐磨、高温冲蚀及绝热等领域[3,4]。
Zn是热喷涂防腐蚀施工中使用最早且最多的涂层材料,Zn涂层具有电化学活性的优点,对钢铁基体能够提供有效的阴极保护,又具有阻挡腐蚀介质的隔离防护作用。但其腐蚀产物稍溶于水导致Zn涂层的腐蚀率较高,使涂层消耗较快[5]。Al涂层因在大气中极易形成致密的Al2O3薄膜而具有很好的钝化保护作用[6],且腐蚀产物不溶于水而使均匀腐蚀速度大大降低,但喷Al涂层组织是由许多保护性的氧化物薄层包覆的片状物组成,它对点蚀和机械损伤比较敏感[7,8]。目前,Zn-Al合金涂层是研究较多、应用广泛的金属复合涂层。但当Al的质量分数大于15%时,将导致合金材料的脆性增大,使合金丝的加工非常困难,影响其应用。本文采用电弧喷涂技术制备了纯Zn及Zn-Al伪合金涂层,通过盐雾实验及电化学研究,并结合涂层腐蚀后表面形貌及腐蚀产物X-射线衍射分析,对Zn及Zn-Al伪合金涂层在含Cl-环境中的耐蚀性能进行了评价。
2 实验材料及方法
2.1 实验材料
基体材料采用Q235钢板,喷涂材料为Φ3mm的Zn丝材和Φ2mm的Al丝材。喷涂前,将基体表面用丙酮清洗,然后对基体表面进行喷砂处理。
2.2涂层制备及表征
使用SFT-12A型电弧喷涂成套装置制备涂层,喷涂工艺参数为:电压30 V,电流160~220 A,喷涂距离160~200 mm,空气压力0.65 MPa;涂层厚度约为50 μm。采用FEI Quanta250环境扫描电镜(ESEM)观察涂层试样横截面的显微组织形貌及盐雾实验后涂层试样的表面形貌,并结合EDS能谱仪定量分析腐蚀产物的化学成分;利用日本理学Dmax-RC旋转阳极X射线衍射仪分析涂层盐雾实验后腐蚀产物的相结构。
2.3涂层性能测试方法
采用Nicon-300型立式金相显微镜和TCI金相图像分析系统软件,以灰度法测定孔隙率。涂层显微硬度测量在Leica VMHT 30M型显微硬度计上进行,测量时施加的载荷为50 g,持续时间15秒。
盐雾实验按照ASTM B117-97 标准进行,试验设备为美国Q-Panel 公司的Q-Fog CCT1100 型循环腐蚀盐雾箱,试验条件为:5%±0.5%中性NaCl 溶液连续盐雾,pH 范围为6.5~7.2,箱体温度控制在(35±1)℃。取样周期设定为48、96、192、384和768 h,盐雾实验后的试样用去离子水冲洗、干燥后进行表面形貌观察和电化学测试。
极化曲线测量在PrincetonVMP3电化学工作站上进行,采用三电极体系,以涂层试样为工作电极,有效面积为10 mm×10 mm,饱和甘汞电极(SCE)为参比电极,铂电极为辅助电极。测试温度为室温,腐蚀介质为3.5%NaCl溶液,测试前试样在溶液中浸泡30 min,待电位稳定后开始测量,电位扫描速度为0.6mV/s。
3结果与讨论
3.1涂层组织观察
图1为电弧喷涂纯锌和锌铝伪合金涂层的横截面SEM形貌。从图中可以看出,涂层呈现出典型的层状结构特征,组织致密,无粗大孔隙或夹杂,变形颗粒之间咬合较好,相互交错成波浪式堆叠,涂层与基体结合良好。EDS分析表明:纯锌涂层由单一的纯锌相组成,锌铝伪合金涂层由深色区域的富Al相、浅色区域的富Zn相交替组成。由Zn-Al二元相图可知,Zn-Al伪合金涂层组织为富Al的α相和富Zn的β相两相组成,其中α为Al基固溶体,β相为Zn基固溶体。
图1. 涂层横截面SEM形貌 (a) 纯锌涂层 (b) 锌铝伪合金涂层
3.2 涂层性能测试
3.2.1涂层孔隙率
涂层的孔隙率测试结果如表1所示。从表中可以看出,相比较于纯锌涂层,锌铝伪合金涂层的孔隙率较小。这是由于锌铝伪合金涂层在喷涂过程中Zn和Al的熔化温度不同,锌熔滴会填充到铝颗粒熔滴撞击时引起的缺陷中,降低了涂层的孔隙率。对于防腐蚀涂层来说,涂层孔隙率越小,意味着涂层越致密,其耐腐蚀性能越好。#p#副标题#e#
表1. 涂层孔隙率测试结果
涂层 | 试样1 | 试样2 | 试样3 | 平均值 |
纯锌 | 5.8% | 5.2% | 4.9% | 5.3% |
锌铝伪合金 | 4.5% | 3.9% | 4.8% | 4.4% |
3.2.2涂层显微硬度测试
表2为纯锌及锌铝伪合金涂层显微硬度测试结果。从表中可以看出,纯Zn涂层平均显微硬度为17.8 HV,锌铝伪合金涂层平均显微硬度为44.2HV,前者明显低于后者。这主要归因于锌铝伪合金涂层中存在大量富Al相,从而强化了整个涂层,使得涂层的整体硬度提高。因此其硬度要高于纯Zn涂层。
表2. 涂层显微硬度测试结果
涂层 | 显微硬度/HV | 平均值/HV | ||||
纯锌 | 18.1 | 18.5 | 15.4 | 20.2 | 17.0 | 17.8 |
锌铝伪合金 | 42.8 | 44.9 | 41.7 | 39.1 | 52.4 | 44.2 |
3.3涂层在盐雾环境中腐蚀行为
盐雾实验加速腐蚀过程中,纯锌和锌铝伪合金涂层样品的腐蚀结果见表3.结果表明:纯锌涂层样品暴露96 h时,涂层表面出现了少量的白锈;暴露192 h时,表面被白锈覆盖;暴露768 h时,样品表面上生成了疏松、多孔的胞状腐蚀产物,同时局部出现了红色锈点。锌铝伪合金涂层样品暴露48 h时,表面无明显变化;暴露192 h时,表面出现了少许白色腐蚀产物;当暴露时间延长到768 h后,涂层表面形成了致密的白色腐蚀产物层,没有观察到红色的锈点。
表3. 涂层盐雾实验不同时间后表面腐蚀状况测试结果
时间/h | 纯锌涂层 | 锌铝伪合金涂层 |
48 | 稍有变色 | 无变化 |
96 | 表面出现了少量白锈 | 表面变暗、涂层变模糊 |
192 | 表面出现100%白锈 | 表面出现了少量白锈 |
384 | 表面白锈层逐渐变厚 | 表面出现50%~60%白锈 |
768 | 局部出现了红色锈点,锈层疏松多孔 | 无红锈,表面形成较致密的白色锈层 |
图2和图3分别为纯锌和锌铝伪合金涂层样品盐雾实验768 h后的表面形貌与EDS分析。从图2(a)中可以看出,纯锌涂层表面形成了一层厚厚的胞状腐蚀产物,腐蚀产物层疏松多孔。EDS分析表明:纯锌涂层表面腐蚀产物由Zn、O、Cl 和Fe元素组成(图2(b)),表明明基体已经开始腐蚀,纯锌涂层作为单独的防护层在盐雾环境中的防腐蚀能力是有限的。从图3(a)中可以看出,锌铝伪合金涂层表面生成了较致密的白色腐蚀产物层。EDS分析表明:锌铝伪合金涂层表面腐蚀产物由Al、Zn、O 和 Cl元素组成(图3(b))。由于锌铝伪合金涂层中存在大量富Zn的β相和富Al的α相,而这种组织特征在一定程度上对Zn-Al伪合金涂层的耐蚀性能产生有利的影响,α相和β相交替存在,协同发挥了Al的钝化保护作用和Zn的牺牲保护作用,提高了涂层的防腐蚀性能。
图4为纯锌和锌铝伪合金涂层盐雾实验768 h后腐蚀产物的XRD图谱。从图中可以看出,纯锌涂层表面生成的腐蚀产物主要为羟基氯化锌(Zn5(OH)8Cl2H2O)、氧化锌(ZnO)及碱式碳酸盐(Zn5(CO3)2(OH)6),这些腐蚀产物微溶于水,使得涂层的耐蚀性能降低;锌铝伪合金涂层表面除生成羟基氯化锌外,还有碱式碳酸盐化合物(Zn0.71Al0.29(OH)2(CO3)0.145∙xH2O)及尖晶石结构的氧化物(ZnAl2O4),在涂层表面形成致密的保护层,有效地封闭涂层中的孔隙,切断腐蚀介质渗透到基体,进一步提高涂层的耐蚀性。
图2. 纯锌涂层盐雾实验768 h后的SEM图片及EDS分析结果
(a) SEM图片 (b) EDS分析谱线
图3. 锌铝伪合金涂层盐雾实验768 h后的SEM图片及EDS分析结果
(a) SEM图片 (b) EDS分析谱线
图4. 涂层盐雾实验768 h后的XRD图谱
3.4极化曲线测试结果
图5是纯锌和锌铝伪合金涂层样品在3.5% NaCl溶液中的极化曲线。从图中可以看出(图5(a)),二者极化曲线的形状相似,锌铝伪合金涂层的自腐蚀电位为-1.03V(vs SCE),纯锌涂层的自腐蚀电位为-0.988V(vs SCE),根据腐蚀热力学可知在相同条件下前者具有更活泼的腐蚀倾向,能提供更好的阴极保护;锌铝伪合金涂层的腐蚀电流密度(1.85×10-2 mA∙cm-2)小于纯锌涂层(5.43×10-2 mA∙cm-2),说明其具有良好的耐腐蚀性能。盐雾实验768 h后样品的极化曲线可以看出(图5(b)),两种涂层自腐蚀电位明显正移,锌铝伪合金涂层自腐蚀电位达到-0.61 V(vs SCE),纯锌涂层自腐蚀电位达到-0.6695V(vs SCE)。锌铝伪合金涂层腐蚀电流密度为1.2×10-2mA∙cm-2,小于纯锌涂层(2.57×10-2mA∙cm-2),说明前者生成的腐蚀产物层较致密,减缓了涂层的腐蚀速率,起到了更有效的保护作用。
图5. 涂层在3.5% NaCl溶液中的极化曲线 (a) 原始涂层 (b) 盐雾实验768 h后的涂层
4结论
(1)采用电弧喷涂技术制备出纯锌及锌铝伪合金涂层,涂层均匀致密、孔隙率小,与基体结合良好,涂层厚度约为50 μm。
(2)盐雾实验768 h后,纯锌涂层表面生成的腐蚀产物主要为羟基氯化锌(Zn5(OH)8Cl2H2O);锌铝伪合金涂层表面腐蚀产物主要为羟基氯化锌(Zn5(OH)8Cl2H2O)、碱式碳酸盐化合物(Zn0.71Al0.29(OH)2(CO3)0.145∙xH2O)及尖晶石结构的氧化物(ZnAl2O4)。与纯锌涂层相比,锌铝伪合金涂层腐蚀产物层更加致密。
(3)动电位极化测试结果说明,锌铝伪合金涂层可以为基体提供良好的阴极保护,其腐蚀电流密度小于纯锌涂层,表现出更优越的防腐蚀性能。
References(参考文献)
[1]Dongxing Fu, Binshi Xu, Qingfen Li, et al. Research Status of High Velocity Arc Spraying Technology in Anti-corrosion Engineering Field[J]. Materials Review, 2007, 21(3): 94-96 (Ch)。
付东兴,徐滨士,李庆芬,等。 高速电弧喷涂技术在防腐工程领域的研究现状[J]. 材料导报,2007,21(3):94-96.
[2]Qi Zhu, Zhenping Lu, Quan Liu, et al. The Research on the Properties of High Corrosion-resistant Alloy Coating Prepared by Electric Arc Spraying Technique[J]. China Surface Engineering, 2008, 21(3): 22-25 (Ch)。
朱琦,陆振平,柳泉,等。 电弧喷涂法制备高耐蚀合金涂层及其性能研究[J]. 中国表面工程,2008,21(3):22-25.
[3]T Nakayama, H Wake, K Ozawa, et al. Electrochemical prevention of marine biofouling on a novel titanium-nitride-coated plate formed by radio-frequency arc spraying[J]. Appl Microbiol Biotechnol, 1998, 50(4): 502-508.
[4]Liuho Chiu, Chunchin Chen, Chihfu Yang. Improement of corrosion properties in an aluminum-sprayed AZ31 magnesium alloy by a post-hot pressing and anodizing treatment[J]. Surface and Coatings Technology, 2005, 191(2-3): 181-187.
[5]Irving Bob. Thermal-sprayed zinc coatings defend steel and concrete bridges[J]. Welding Journal, 1993, 22(9): 119-124.
[6]Yongxiong Chen, Binshi Xu, Yi Xu, et al. The Development of Thermal Spraying Zn-Al Alloy Anticorrosive Coating[J]. Materials Review, 2006, 20(4): 70-73 (Ch)。
陈永雄,徐滨士,许一,等。 热喷涂Zn-Al合金防腐涂层技术的研究进展[J]. 材料导报,2006,20(4):70-73.
[7]T Lester, D J Kingerley, S J Harris, et al. Thermally sprayed composite coatings for enhanced corrosion protection of steel structures[C]. Proceedings of the 15th Thermal Spray Conference. France, May. 1998: 49-55.
[8]Qinghua Ma, Jianping Yin, Zuojing Dong. Anticorrosion Mechanism of Thermal Spraying Aluminum Composite Coating in Marine Environment[J]. Materiais Protection, 2006, 35(6): 14-15 (Ch)。
马青华,尹建平,董作敬。 海洋环境热喷涂铝复合涂层保护机理分析[J]. 材料保护,2002,35(6):14-15.
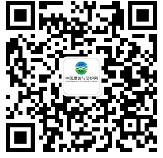
官方微信
《中国腐蚀与防护网电子期刊》征订启事
- 投稿联系:编辑部
- 电话:010-62313558-806
- 邮箱:fsfhzy666@163.com
- 中国腐蚀与防护网官方QQ群:140808414