刘道新,王振亚,张晓化,刘国华
西北工业大学腐蚀与防护研究室,西安,中国,710072
Email: liudaox@nwpu.edu.cn
个人简介
刘道新,男,1962年生,博士,教授,博士生导师。西北工业大学腐蚀与防护研究所所长,学科带头人。
学术任职:中国腐蚀与防护学会理事,中国腐蚀与防护学会航空航天专业委员会副主任委员,中国腐蚀与防护学会涂料涂装及表面保护专业委员会副主任委员,中国航空表面工程专业委员会委员,中国船舶材料学术委员会委员等。主持国家自然科学基金、国家973项目、国家863高技术研究发展计划项目、省部级基金和国际合作项目等15项,主持其他科研课题40多项,发表学术论文130余篇,被SCI、EI收录70余篇。主编国防重点建设教材“材料的腐蚀与防护”.获省部级科技奖6项。
研究方向:等离子体表面工程技术和现代表面工程新技术;材料腐蚀理论与防护技术;材料摩擦磨损、微动损伤、冲蚀损伤与预防技术;材料与工程结构的力学环境耦合失效理论及控制技术等。
刘道新
摘要:采用离子辅助磁控溅射沉积技术在Ti811钛合金表面制备了不同调制周期的Cu/Ni多层膜,采用静态氧化方法对比研究了Cu/Ni多层膜和Cu、Ni单金属膜层及CuNi合金膜层在350℃的氧化行为,用扫面电镜和能谱仪分析了氧化膜层形态和化学成分。结果表明调制周期小于600nm的Cu/Ni多层膜均具有良好的抗氧化性能,其抗氧化能力显着优于Cu膜,但不及Ni膜,在350℃温度下能够对钛合金基材起到较好的保护作用。Cu/Ni多层膜的抗氧化性能随着膜层调制周期的减小而提高,调制周期为20nm的Cu/Ni多层膜抗氧化性能最优。成分1:1的CuNi合金膜层的抗氧化性能与调制周期为200nm的Cu/Ni多层膜相近。Cu/Ni多层膜具备良好的抗氧化性能的原因主要归于多层膜中Ni子膜层良好的屏障作用。Cu/Ni多层膜的抗氧化性能随调制周期的减小而改善的主要原因归于随着膜层调制周期的减小,氧原子扩散障Ni层的数量增加,同时Ni子膜层晶粒细化,易于形成致密的氧化膜,有效阻碍了氧原子和金属原子的相互扩散。
关键词:Cu/Ni多层膜;高温氧化;钛合金;离子辅助磁控溅射沉积
基金项目:国家自然科学基金(50671085),国家863高技术研究发展计划(2007AA03Z521)。
1 引言
钛合金耐磨性差,对微动疲劳(Fretting Fatigue,FF)损伤十分敏感[1]。为此,利用表面涂镀层改善钛合金FF性能成为提高发动机寿命和可靠性的研究热点之一[2,3]。Cu/Ni多层膜不仅能显着提高金属材料的耐磨性能[4],而且在改善钛合金的抗微动磨损与FF性能方面展示出独特的优势[5]。Cu/Ni多层膜提高钛合金FF抗力的原因归于其特殊结构实现了膜层的强度与韧性的合理配合,以及膜层良好的减摩润滑作用与止裂作用[5]。由于目前航空发动机压气机高温端部件工况温度通常在350℃左右,尽管Ni在该温度下有良好的抗氧化性能,但是Cu在300℃时就会发生严重的氧化,那么Cu/Ni多层膜能否在350℃长期使用是制约其用于压气机钛合金叶片抗FF损伤的关键因素之一,为此,探讨Cu/Ni多层膜的高温氧化行为十分必要。
离子辅助沉积技术(Ion Assisted Deposition,缩写为IAD)将离子注入与物理气相沉积技术有机结合,在保持较低的工艺温度条件下,能够显着地提高膜基结合强度,且不会明显损害基材的力学性能[6]。磁控溅射膜层结晶细致、致密性好,是制备多层膜的优势方法。为此,本研究将上述两种方法联合,即通过离子辅助磁控溅射沉积技术制备Cu/Ni多层膜,并与Cu、Ni膜及其合金膜进行抗氧化性能对比研究。基材选择发动机用典型钛合金Ti811。
资助信息:请根据信息量的大小调整文本框的高度。确保资助信息的内容不会超过页面的下边距并占用下方空白。
2实验方法
2.1多层膜的制备
Ti811钛合金的化学成份(wt%)为:7.9Al,V0.99,Mo1,Fe0.05,C0.01,N0.01,H0.001,O0.06,其余为Ti。热处理制度:910℃保温1h,空冷 + 580 ℃保温8h,空冷。组织为等轴α+晶间β。试样尺寸为20mm×20mm×0.8mm。试样镀膜前机械抛光,丙酮超声清洗。
镀膜利用离子辅助磁控溅射设备,靶材为纯度99.99%的Cu和Ni靶。膜层沉积之前,通入氩气,采用轰击能量1200V、束流300mA的Ar+离子轰击清洗试样表面约15min。Cu/Ni多层膜的制备过程为先沉积1μm的Cu底层,然后交替单独开启Ni靶、Cu靶电源,沉积Cu/Ni多层膜,多层膜的调制周期通过磁控电源的开启时间长短进行控制。多层膜的总厚度为10μm,表面为Ni层。同时制备了10μm厚的纯Cu和纯Ni膜层以及成分1:1的CuNi合金膜层用于对比研究。工艺参数:电流1A,偏压-200V,氩分压0.5 Pa。加热温度200℃。
2.2膜层高温氧化实验
膜层的高温氧化实验按照标准ASTMG54-77(简单静态氧化试验标准推荐方法)进行。试样放置在箱式电阻炉的坩埚中,加热到350℃,恒温氧化,每隔一定的时间取出称重,Cu膜的氧化时间为5小时,其他试样的氧化时间均为100小时。试样质量利用SHIMADZU-AUW220D型高精度电子分析天平(精确到0.01mg)测量,通过增重法表征试样的氧化速率。
图1 Cu/Ni多层膜的XRD谱#p#副标题#e#
3 实验结果及讨论
3.1膜层的特征
对Cu/Ni多层膜的扫描电镜分析表明,多层膜结晶细致,表面致密性高。膜层厚度均匀,膜层之间结合紧密,膜层与基体结合良好。膜层的X射线衍射分析结果表明(图1所示):所有膜层均以原子密度高和表面能低的(111)晶面择优生长。在大调制周期(1200nm和600nm)时,Cu/Ni多层膜的衍射峰呈现为Cu和Ni两个单层膜的衍射峰叠加的结果。随着调制周期的减小(200nm、120nm、20nm),Cu和Ni两个单层膜的衍射峰逐步形成单峰。Cu的晶格常数大于Ni,以Ni调制层晶面间距变大来与Cu的晶格进行匹配形成外延生长。CuNi合金膜的衍射峰位与小调制周期的Cu/Ni纳米多层膜相同。应该指出,Cu/Ni纳米多层膜与CuNi合金膜产生相同衍射峰的原因并不同,CuNi合金膜的衍射峰产生于Cu、Ni单相置换固溶体,而Cu/Ni多层膜的单衍射峰则是由Cu、Ni调制层在外延生长中分别受到拉、压应力而使对应晶面的间距相互接近所致。Cu/Ni多层膜的衍射峰的峰形较CuNi合金膜更为宽化,说明Cu/Ni多层膜的晶粒尺寸更小,这是由于纳米多层膜的多界面对晶粒生长的阻碍作用的缘故。
3.2高温氧化规律
图2所示为不同试样的氧化增重与随氧化时间的变化曲线,图3对比了各试样的氧化速率测试结果。可以看到,在350℃高温环境下,各试样的氧化动力学曲线均较好遵循抛物线规律。Ni膜抗氧化性能最优,Cu膜氧化速率最大,较Ni膜高3个数量级,因此,Cu膜不能在350℃高温环境下长期使用。Cu膜层氧化5小时后,氧化皮大片剥落,Cu膜氧化时位错从镀层/氧化物界面向氧化层内攀移[7,8],增加氧原子扩散的通道,因此氧化速度快。
图2 Ti811合金和膜层的氧化增重曲线
以增重为评价指标来看,1200nm的大调制周期的Cu/Ni多层膜的氧化速率高于Ti811合金基体,但明显低于Cu膜的氧化速率,这与多层膜中Ni组元良好的抗氧化性能密切相关,在Cu/Ni多层膜中Ni层及Ni与氧结合形成的氧化膜阻止了氧原子向膜层内部的扩散。600nm调制周期的Cu/Ni多层膜的氧化曲线与Ti811合金基体较为接近。氧化初期几小时内,CuNi合金膜和200nmCu/Ni的氧化增重比Ti811合金大,但在氧化25个小时后,两膜层的氧化速率明显低于Ti811合金。纳米化增加了Ni膜层的晶界密度,因此增加了NiO的形核率;纳米化不仅增强了Ni在膜层中的扩散,而且通过使氧化膜晶粒细化增加了氧化物膜中的晶界扩散,纳米Ni氧化后生成的NiO的晶粒比较细小,以上因素促使纳米晶Ni在氧化开始阶段的氧化速率快,随着氧化膜逐渐变厚,使Ni向外的扩散速率减慢,氧化速率也随之减缓下来[9]。Ti氧化时形成的TiO2氧化膜多孔且容易破裂[10],使得Ti氧化规律接近直线规律,因此氧化实验的后期,Ti基体氧化增重大于CuNi合金膜和调制周期200nm 以下的Cu/Ni多层膜。小调制周期的Cu/Ni多层膜氧化速率低是因为在膜层厚度一定的情况下,多层膜调制周期愈小,多层膜的晶粒愈细化,同时氧原子扩散障Ni层数量愈多、分布愈密集,对氧原子向膜层内部扩散的阻挡作用越显着和有效,因而多层膜的抗氧化性能愈好。CuNi合金膜的抗高温氧化性能与调制周期为200nm的Cu/Ni多层膜接近。需要指出的是上述以增重法评价Cu、Ni及Cu/Ni多层膜的氧化行为较为合理,因为其密度接近。然而,对于这些膜层与Ti811合金基材的比较,因后者的密度约为前者的1/2,近似简单地换算,钛合金在相同的失重下其体积损失则是膜层的2倍左右。
图3 Ti811合金和膜层的氧化速率
3.3微观形态特征和能谱分析结果
各膜层试样氧化后除Cu膜出现大面积破坏外,其他膜层均完好。扫描电镜分析表明Cu膜氧化后呈分层剥落方式失效(图4(a)所示),在外层的Cu膜充分氧化后,产生大量的氧化物堆积,致使膜层内应力增大,应力达到临界值时导致膜层开裂和脱落,显露出内层膜,进而开始新的氧化历程。图4同时对比了调制周期分别为600nm、200nm和20nm的Cu/Ni多层膜和CuNi合金膜氧化100h后的微观形貌,可以看出,氧化后膜层表面的结晶颗粒均有不同程度的增大,其中调制周期600nm 的Cu/Ni多层膜表面有大颗粒出现,结合较为疏松。调制周期200nm的 Cu/Ni多层膜表面结晶颗粒细小、且较为均匀,但致密性较低。调制周期20nm的 Cu/Ni多层膜氧化后颜色变化最不明显,结晶颗粒均匀而致密,原因归于晶粒细化的镍膜层具有更高的表面能,容易氧化而在表面形成一层非常致密的氧化膜,能有效阻挡氧原子向内扩散和膜层中Cu2+、Ni2+沿短路如晶界、位错等从镀层/氧化物界面向氧化物/气相界面的传输,因而有较强的抗氧化性。CuNi合金的氧化层主要分为两个区域[11],外部是铜的氧化物,内部是除铜的氧化物外还有多孔结构的镍氧化物。外部氧化层形成是由铜原子经空位扩散形成的,而内部的多孔区域是由铜的外扩散以及氧的内扩散形成的。这种多孔内氧化层的存在不仅降低了CuNi合金膜层的抗氧化性能,还破坏了膜层的力学性能。因此,CuNi合金膜层的抗氧化性能不及较小调制周期的 Cu/Ni多层膜。
图4 Cu膜、Cu/Ni多层膜和合金膜氧化后的形貌#p#副标题#e#
图5中所示为几种典型调制周期的Cu/Ni多层膜和CuNi合金膜氧化100h后的能谱分析结果,调制周期为600nm、200nm和20nm的Cu/Ni多层膜及CuNi合金膜表面的氧原子比例分别为48.65%、46.61%、43.08%和44.59%,即氧化程度与各膜层的氧化增重一致。调制周期为200nm和20nm的Cu/Ni多层膜对基材保护性更好,基材中的Ti元素不明显。
图5 Cu/Ni多层膜和合金膜氧化后的能谱
4 结论
(1)调制周期小于600nm的Cu/Ni多层膜均表现出良好的抗氧化性能,350℃时能够较好地保护Ti811合金。Cu/Ni多层膜的抗氧化性能随着调制周期的减小而提高,调制周期为20nm时抗氧化性能最好。CuNi合金膜抗氧化性与调制周期为200nm的Cu/Ni多层膜接近。
(2)Cu/Ni多层膜良好的抗氧化性能主要归于膜层中Ni子膜良好的屏障作用。多层膜的抗氧化性能随着调制周期的减小而改善是由于调制周期愈小,氧原子扩散障Ni层愈多,Ni子膜层晶粒细化,易于形成致密的氧化膜,有效阻碍了氧原子和金属离子的相互扩散。
References(参考文献)
[1] Ray A K, Das G, Ranganath V R. Failure of Connecting Pins of a Compressor Disc in an Aero-engine [J]. Engineering Failure Analysis, 2004, 11: 613-617.
[2] Hutson A L, Niinomi M, Nicholas T, etal. Effect of Various Surface Conditions on Fretting Fatigue Behavior of Ti-6Al-4V [J]. International Journal of Fatigue, 2002, 24(12): 1223-1234.
[3] Daoxin Liu, Jiawen He. Comparative Study on the Fretting Fatiugue and Fretting Wear Behaviors of Titanium Alloy Subject to Various Surface Modifications[J]. Tribology, 2005, 25(1): 13-17
刘道新, 何家文。 经不同表面改性处理的钛合金的微动疲劳和微动磨损行为对比研究[J]. 摩擦学学报, 2005, 25(1): 13-17.
[4] Ghosh S K, Limaye P K, Bhattacharya S, et al. Effect of Ni Sublayer Thickness on Sliding Wear Characteristics of Electrodeposited Ni Cu Multilayer Coatings [J]. Surface and Coating Technology, 2007, 201: 7441-7448.
[5] Xiaohua Zhang, Daoxin Liu, Guohua Liu, et al. Effects of Multilayer Film on Fretting Wear and Fretting Fatigue Resistance of Ti811 Alloy [J]. Rare Materials and Engineering, 2011, 40(2): 294-299.
张晓化,刘道新,刘国华等。 Cu/Ni多层膜对Ti811合金微动磨损和微动疲劳抗力的影响[J]. 稀有金属材料与工程, 2011, 40(2): 294-299.
[6] Ruset C, Grigore E, Collins G A, etc. Characteristics of the Ti2N Layer Produced by an Ion Assisted Deposition Method[J]. Surface and Coatings Technology, 2003, 174 -175: 698-703.
[7] K.H. Kim, D.P. Norton, D.K. Christen, Formation of Oxidation-resistant Cu-Mg Coatings on (001) Cu for Oxide Superconducting Tapes[J], Surface and Coatings Technology, 2008 (202) :5136~5139
[8] Ming-Sheng Leu, Shen-Chuan Lo, Jin Bao Wu, Microstructure and Physical Properties of Arc Ion Plated TiAlN/Cu Thin Film[J]. Surface & Coatings Technology, 2006 (201) 3982~3986
[9] Shujiang Geng, Shenglong Zhu, Fuhui Wang. High Temperature Oxidation Behavior of Pure Ni and its Sputtered Nanocrystalline Coating[J]. Journal of Chinese Society for Corrosion and Protection, 2003,23(6):335~339.
耿树江,朱圣龙,王福会。 纯Ni及其溅射纳米晶的高温氧化行为[J]. 中国腐蚀与防护学报, 2003,23(6):335~339.
[10] Unnam J, RN Clark R K. Oxidation of Commercial Purity Titanium[J]. Oxidation of Metals, 1986, (26):231~235.
[11] R. Haugsrud, P. Kofstad. On the High-temperature Oxidation of Cu-rich Cu- Ni Alloys[J]. Oxidation of Metals, 1998, (50): 189~213.
-
标签: Cu/Ni多层膜, 高温氧化, 钛合金, 离子辅助磁控溅射沉积
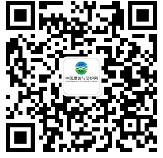
官方微信
《中国腐蚀与防护网电子期刊》征订启事
- 投稿联系:编辑部
- 电话:010-62313558-806
- 邮箱:fsfhzy666@163.com
- 中国腐蚀与防护网官方QQ群:140808414