为了提高先进核反应堆的发电效率,在第四代超临界水冷堆(SCWR)中,冷却剂出口温度被提高到550℃,压力提高到25Mpa,其热效率由目前第二代轻水反应堆(LWRs)的33%提高到44%左右。SCWR运行在水的临界点(374℃,22.1Mpa)以上,此时冷却剂对金属材料的腐蚀性极强,现有的LWR堆芯构件和包壳材料已不再适用,结构材料的腐蚀已成为开发SCWR的一个关键问题[1] 。
对应用于超临界火电站和压水堆燃料组件等高温环境中的材料进行了初步筛选与评估,提出了一系列SCWR候选材料,其中包括铁素体-马氏体(F/M)钢、奥氏体不锈钢、镍基合金及氧化物弥散强化(ODS)钢[2] 。其中,奥氏体不锈钢因具有优良的耐蚀性、加工性能、可焊性和高温力学性能,在核电站结构件中被大量应用[3,4] 。
304NG奥氏体不锈钢(简称304NG钢)是使用最广且价格相对低廉的一种奥氏体不锈钢,常用于反应堆的堆内构件中,铬含量约为20%(质量分数,下同),镍含量约为9%。与普通的低铬奥氏不锈钢相比,铬含量超过18%的304NG钢具有更加优良的耐均匀腐蚀性能。为了研究304NG钢在SCW中的均匀腐蚀性能以及温度对其腐蚀性能的影响,本工作分别在550℃和650℃的低容氧(<10μg/L)SCW中对304NG钢进行腐蚀增重试验。
1 试验
1.1 试样
试验选用304NG,其化学成分(质量分数)为:wCr19.41%, wNi9.35%, wMn1.21%, wSi0.58%, wN0.089%, wCu0.062%,wCo0.028%, wP0.018%,wC0.018%, wS0.0072%,wB0.0015%,余量为铁。试样尺寸见图1,并且通过在试样表面打钢号对其进行编号,避免发生混淆。采用180~2000号SiC水砂纸逐级打磨试样表面,以消除加工硬化层对材料腐蚀性能的影响,之后在机械磨抛机上用氧化铝抛光剂对试样表面进行抛光处理,抛光期间用金相显微镜观察抛光的效果。试样抛光后用乙醇超声清洗并烘干,之后用游标卡尺测量试样的原始尺寸,并且采用高精度天平(精度为0.01mg)对试样进行称量。本工作采用腐蚀增重的方法研究材料在SCW中的腐蚀速率随腐蚀时间的变化关系,取样周期设定为100,300,600,1000,1500h,每个试验周期结束后对所有试样进行称量。
图1 均匀腐蚀试样尺寸(mm)
Fig.1 Dimension of specimen in general corrosion test(mm)
1.2 试样方法
均匀腐蚀试验在高温高压循环水回路腐蚀系统中进行。如图2所示,该设备主要包括一台容积为1.5L的高压釜,高压釜的最高设计使用温度为700℃,压力为35Mpa,并且为了降低试验过程中其他物质由于氧化释放出杂质离子对试验产生干扰,所用高压釜釜体、釜盖、热电偶套管以及釜内配件等均采用625镍基合金作为原材料,设备的低温管路部分则采用316L不锈钢,设备中的温度测量单元和压力测量单元分别为K型热电偶和4~20mA输出的高精度的压力传感器。本工作中的所有均匀腐蚀试验均在控制水化学环境的循环水条件下进行,其中高压泵给水流量大约为0.9L/h。
试验条件如下:试验介质采用超纯水,采用H2除氧,溶液中溶解氧≤5μg/L,试验温度(550/650±0.5)℃,试验压力为(25.0±0.1)MPa,回水电导率≤0.1μS/cm。试验结束后对材料在不同温度下的腐蚀增重数据进行拟合,以得到材料的腐蚀增重规律,并且对其进行氧化动力学分析。同时采用SEM和EDS对试样表面氧化膜的形貌、结构和成分进行研究,以得到材料在SCW中的腐蚀机理。
图2 动态SCW腐蚀系统示意图
Fig.2Schematic diagram of SCW experimental apparatus
2 结果与讨论
2.1 氧化动力学
由图3可见,腐蚀初期材料增重明显,随后腐蚀增重随着腐蚀时间的延长而减小。由图3还可见,相同腐蚀时间条件下,试样在550℃时的腐蚀增重低于在650℃时的。304NG钢在550℃和650℃的低溶氧SCW中的腐蚀增重曲线可以用式(1)拟合。
式中:k是氧化速率常数,mg/(dm2·h);t是腐蚀的时间,h;n是时间指数; ΔW代表增重,mg·dm-2。拟合结果见图3,其中R2为拟合精度。
图3 304NG钢在550℃和650℃低溶氧SCW中的腐蚀增重曲线
Fig.3 Weigh gain curves of 304NG steel exposed to deaerated SCW at 550℃and 650℃
由拟合结果可知,304NG钢在550℃和650℃的SCW中的氧化速率常数分别为0.35和4.66,表明304NG钢具有良好的耐蚀性,尤其是在550℃条件下,材料的腐蚀速率极低。当温度升高至650℃时,试样的腐蚀速率明显加快,1500h后腐蚀增重由550℃的18.50mg/dm2升高到143.05mg/dm2,腐蚀速率大约升高了8倍,这表明温度对304NG钢在SCW中的均匀腐蚀性能影响显著。试样在550℃和650℃时腐蚀增重所对应的时间指数分别为0.55和0.47。时间指数主要反映材料的腐蚀增重速率同腐蚀时间的关系,数值越小表明腐蚀增重的速率随腐蚀时间的变化越快。试样在SCW中的腐蚀速率随着腐蚀时间的延长而下降,这是因为一旦表面形成氧化膜,会降低离子的扩散速率,因此时间指数越大表明腐蚀增重速率在腐蚀后期越快。304NG钢在两种温度下的腐蚀增重虽然存在着巨大的差别,但是其时间指数类似,表明腐蚀过程中腐蚀速率的变化趋势是类似的,而试样的腐蚀增重变化规律反应其表面氧化膜的变化规律。总体来说,304NG钢在550℃SCW中具有较好的耐蚀性,但是当温度升高到650℃时,其腐蚀增重急剧升高。
2.2 氧化膜表面形貌
304NG钢在550℃的低溶氧SCW中腐蚀1000h内,其表面氧化膜形貌没有明显变化,试样表面仍然呈现出金属光泽,表明试样表面氧化膜的厚度很低。腐蚀1500h后,在试样表面的局部区域观察到了少量的疖状腐蚀,见图4。腐蚀1500h后材料表面的氧化膜依然很薄,并且能清楚地看到材料表面的划痕,见图4(a),同时在试样表面还零星分布着少量疖状腐蚀岛,这些腐蚀岛的尺寸较小,直径约为20μm。为了更清楚地观察材料表面疖状腐蚀以及非疖状腐蚀区的微观形貌,分别对A、B区进行了局部形貌分析,见图4(b)和图4(c)。观察发现,试样表面非疖状腐蚀区的表面氧化膜极其致密,并且零星分布着尺寸很小的Fe3O4晶粒,因此该区域的氧化膜具有很好的保护性能;而疖状腐蚀区域表面氧化膜形貌同F/M钢表面氧化膜形貌类似,由大量的氧化物颗粒堆积而成,并且在这些颗粒物中还观察到了少量的孔洞缺陷。在304NG钢表面还观察到了白色物质,分别对表面氧化膜的不同特征区进行EDS分析,结果见表1。由表1中不同区域的元素含量分析结果可知,区域1为疖状腐蚀岛,其主要成分为氧和铁。疖状腐蚀岛是由基体材料内部的铁扩散到材料表面被氧化后所形成的,由此可以推断同其他金属元素相比,铁元素能够以更快的速率通过疖状腐蚀的形核区,扩散到表面被氧化后形成了腐蚀岛。区域2为非疖状腐蚀区,对比可知区域2中的铬含量明显高于区域1中的,表明该区域氧化膜的成分为铁、铬氧化物的固溶体,该结构比单纯的铁的氧化物更加致密,因此对基体材料具有更好的保护性。区域3的白色物质中含有大量铁以及少量的铬和氧,因此该白色物质为铁单质和铁、铬氧化物的混合体,这是由于降温过程中原本溶解在SCW中的氧化物和铁单质由于溶解度下降而析出在氧化膜表面。为了更加直观地观察材料表面的疖状腐蚀形貌,对试样表面的一个独立的疖状腐蚀岛进行三维形貌分析,见图5。试样表面疖状腐蚀岛为半球状,是由基体材料内部的铁元素向外扩散然后被氧化所形成的,腐蚀过程中,腐蚀岛的体积会逐渐增大,然后孤立的腐蚀岛之间相互连接,逐渐发展成为形状各异尺寸更大的腐蚀岛。
当温度由550℃升高到650℃时,304NG钢在SCW中的腐蚀过程同550℃时的情况类似,即腐蚀前期材料表面形成薄而致密的富铬氧化膜,该氧化膜能够有效抑制金属离子以及氧的扩散,随着腐蚀时间的延长,材料表面开始出现疖状腐蚀,并且腐蚀岛的尺寸随着腐蚀时间的延长逐渐增大,然后不同的腐蚀岛之间相互连接从而发展成为一个尺寸更大的腐蚀岛。但是试样在650℃的超临界水中,其表面的疖状腐蚀形核以及生长的速率更快,腐蚀100h就能在其表面观察到大量的疖状腐蚀岛,疖状腐蚀岛的平均尺寸也远大于550℃时腐蚀1000h后其表面的疖状腐蚀岛。可见,温度对304NG钢在SCW中的腐蚀性能有着重大的影响。温度≤550℃,304NG钢的耐蚀性良好,当温度升高到650℃后材料表面出现了严重的疖状腐蚀,导致材料的耐蚀性急剧下降。由图6(a)可见,材料表面大部分区域已经被疖状腐蚀所覆盖,在非疖状腐蚀区继续有新的疖状腐蚀形核。650℃时试样表面疖状腐蚀岛的形貌与550℃时的也不同,不仅尺寸更大,并且疖状腐蚀岛表面的氧化物晶粒的形貌也存在着差异。EDS分析表明,650℃时在SCW中腐蚀1500h后,腐蚀产物主要成分为铁的氧化物,与550℃时的情况相同,但是650℃时几乎所有的氧化膜晶粒都发生破裂,见图6(c),从而使氧化膜的保护性能大大降低,并且加速了疖状腐蚀的生长速率。而导致氧化膜晶粒发生开裂的原因可能是因为在腐蚀过程中,疖状腐蚀区域所形成的氧化膜并不具有很好的保护性能,使得基体材料中的铬、镍发生流失,从而导致氧化膜内部的铬和镍的含量极低,见表2,最终在生长应力的作用下发生破裂[4,5] 。对于650℃时的非疖状腐蚀区,其元素含量同550℃时的类似。对650℃时的腐蚀试样进行了三维形貌分析可知,此时疖状腐蚀的密度更大,且腐蚀岛的平均尺寸也更大,这表明温度能够加速304NG表面的疖状腐蚀,见图7。
图4 304NG钢在550℃的低溶氧SCW中腐蚀1 500h后的表面氧化膜形貌
Fig.4 SEM morphology of the 304NG exposed to SCW(1 500h)at 550℃for 1000h:(a)oxidation film;(b)enlarged view of A;(c)enlarged view of B
表1 304NG钢(550℃)表面元素成分
Tab.1 Chemical composition of 304NG steel exposed at 550℃
图5 304NG钢在550℃的低溶氧SCW中腐蚀1500h后表面腐蚀岛3D形貌
Fig.5 3D morphology of nodular island on 304NG steel after exposed to deaerated SCW at 550℃for 1500h
2.3 氧化膜截面形貌
由图8可见,疖状腐蚀氧化膜为典型的两层结构,即外层腐蚀岛以及内层氧化膜,并且通常内层氧化膜的厚度要大于外层氧化膜的。当温度升高到650℃时,材料表面疖状腐蚀的密度急剧升高,并且不同的疖状腐蚀岛之间相互连接,构成一个体积更大的疖状腐蚀岛。在650℃的低溶氧SCW中,当疖状腐蚀岛相互连接到一起之后,不同的氧化膜之间分层不明显,并且氧化膜内部存在大量的孔洞以及裂纹等缺陷,这也导致氧化膜不具有很好的保护性能。对比两种温度下材料表面氧化膜的截面形貌可知,550℃的低溶氧SCW中形成的疖状腐蚀氧化膜结构致密,其厚度在疖状腐蚀的中心处达到最大值,然后依次向两侧递减;650℃时材料的疖状腐蚀严重,并且腐蚀岛之间相互融合,表明当疖状腐蚀向基体材料内部发展到一定深度后,由于氧在深度上的扩散阻力增大,从而选择向两侧扩散,因此在疖状腐蚀的发展后期疖状腐蚀的深度基本不变,转而在平面内继续扩展,最终导致不同的疖状腐蚀区域相互融合。
图6 304NG钢在650℃的低溶氧SCW中腐蚀1500h后表面氧化膜形貌
Fig.6 SEM morphology of 304NG exposed to SCW(1500h)at 650℃:(a)oxidation film;(b)enlarged view of A;(c)enlarged view of B
表2 304NG钢(650℃)表面元素成分
Tab.2 Chemical composition of 304NG steel exposed at 650℃
图7 304NG钢在650℃的低溶氧SCW中腐蚀1500h后表面氧化膜3D形貌
Fig.7 3D morphology of 304NG steel exposed to deaerated SCW at 650℃for 1500h
图8 304NG钢在550℃和650℃的低溶氧SCW中腐蚀1500h后截面氧化膜形貌
Fig.8 Cross-sectional morphology of oxide scales of304NG steel exposed to SCW at 650℃(a),and550℃(b)for 1500h
由图9可见,304NG钢在550℃的低溶氧SCW中所形成的疖状腐蚀内层氧化膜中的铬含量同基体材料类似,没有明显的升高,镍含量略高于基体材料;而外层氧化膜中的成分类似,几乎全部由铁的氧化物构成,铬、镍的含量极低。研究表明,材料表面氧化膜的保护性能主要由内层氧化膜的结构决定,内层氧化膜中的铬含量越高则氧化膜的结构越致密,其保护性能也就越好[5,6,7]。在腐蚀过程中,材料内层氧化膜中的铬会向外扩散,同时基体材料中的铬也会对其进行补充,因此内层氧化膜中的铬含量由这两个过程的速率决定[8]。当铬元素向外扩散的速率大于由基体材料向氧化膜内补充的速率时,氧化膜中的铬含量会逐渐降低,反之则会逐渐升高;如果内层氧化膜中的铬含量同基体材料中的相同时,表明两个过程的反应速率相当,此时氧化膜的结构不够致密,铬会继续向外扩散,并且外界的氧也会继续向基体材料内部扩散,氧化膜的厚度也会进一步增加。当温度升高到650℃时,氧化膜内部的元素分布呈现出典型的双层结构,即外层富铁贫铬,而内层富铬贫铁,并且内层氧化膜中的镍含量也明显高于基体材料中的。可知此时的内层氧化膜结构致密,能够有效抑制金属离子以及氧的扩散,此时氧化膜的厚度基本不变,疖状腐蚀转而向四周扩展,最终导致不同疖状腐蚀区域相互融合。
图9 304NG钢在550℃和650℃的低溶氧SCW中腐蚀1500h后的截面氧化膜元素分布
Fig.9 Cross-sectional composition distribution of 304NGsteel exposed to deaerated SCW for 1500h at 550℃ and 650℃
2.4 腐蚀机理研究
通过对氧化膜的表面以及截面形貌分析,可知304NG钢浸泡在SCW中一定时间后,其表面会产生疖状腐蚀,并且腐蚀温度越高,疖状腐蚀出现得越早,同时发展也越快。在550℃的超临界水中,由于疖状腐蚀的发展比较慢,因此304NG钢在1500h内的腐蚀增重较低,但是疖状腐蚀是一种局部腐蚀,会在后续过程中继续扩展,并且造成非疖状腐蚀区的氧化膜失去保护性能。同时,当温度由550℃升至650℃时,材料表面的疖状腐蚀严重,因此极大地限制了304NG钢在SCW中的应用,因此有必要探讨疖状腐蚀形成的机理。
当前,学界对疖状腐蚀形成机理的研究主要集中在锆合金领域[9,10] ,而对于其他材料的疖状腐蚀却鲜见报道。在疖状腐蚀的形成机理方面,目前主要有Kuwae[10] 所提出的氢聚集模型以及周邦新等人[11] 所提出的形核长大模型。本工作的研究结果表明,疖状腐蚀的成因可能同所处的SCW环境有关。相关研究表明,Fe-Cr合金在含氧的蒸汽环境中呈现出同不含蒸汽的纯氧环境中完全不同的氧化性能[12,13] 。Asteman[13] 的研究表明,304L奥氏体不锈钢在873K纯氧环境中发生氧化反应后会生成刚玉型结构(M2O3)的氧化物,然而在含氧的水蒸气环境中,表面会形成一层相对较薄的(Cr,Fe)2O3氧化物,同时还能在试样表面观察到少量的磁铁矿结构的疖状腐蚀。Halvarsson[14] 的研究结果表明,在高温水蒸气环境中,304L钢表面氧化膜内的铬能够同水发生反应,由于金属离子以及氧在固态氧化物和金属基体中的扩散速率主要由温度控制,因此可用该理论来解释304NG钢在SCW中形成的疖状腐蚀现象,见图10。304NG钢中铬的质量分数约为19.4%,表明该材料的基体内有足够的铬可以用来补偿氧化膜中由于挥发而损失的铬。然而,铬沿着晶界和在晶粒内部扩散的速率不同,通常铬在晶界上的扩散较快,因此能够及时补偿晶界附近的氧化膜中因挥发而损失的铬,而远离晶界的氧化膜中的铬由于得不到及时的补充,导致该区域的氧化膜中贫铬。贫铬的氧化膜通常不具备很好的保护性,外界的氧能够很容易穿过氧化膜同基体材料发生反应,从而在氧化膜表面形成局部腐蚀区。随着腐蚀时间的延长,基体材料内扩散速率更快的铁穿过这个局部缺陷在表面同外界的氧发生氧化反应生成富铁的腐蚀岛,即外层氧化膜,同时外界的氧也穿过这个缺陷进入机体材料内部,形成内层氧化膜,最终导致疖状腐蚀的形成。
304NG钢在SCW中发生疖状腐蚀的过程见图11。在高温高压的SCW环境中,水会发生分解产生氧气,由于304NG钢内较高的铬含量,其表面会迅速生成一层保护性氧化膜。在高温高压的SCW环境中,氧化膜中的铬容易与水发生反应,并且生成易挥发的CrO2(OH)2,从而导致氧化膜中铬含量降低;同时,基体材料中的铬会向氧化膜中扩散,以补充铬来维持氧化膜的保护性。但是由于铬在沿着晶界与通过晶粒内扩散的速率不同,使得晶界附近的氧化膜富铬,而远离晶界的氧化膜贫铬。随着腐蚀过程的进一步发展,远离晶界区域的氧化膜中的铬含量将会进一步下降,最终使得该区域的氧化膜失去保护作用。然后,基体材料中的铁、铬、镍等离子就会沿着这个缺陷处向外扩散,同时外界的氧离子则会沿着缺陷处向内扩散。由于铁的扩散速率要远大于铬和镍的[10] ,使得外层氧化膜主要为铁的氧化物;另一方面,外界的氧进入基体材料后,会在基体材料内部形成铁、铬、镍尖晶石结构,而铬和镍在这种物质中的扩散速率极慢,使得这两种元素在该层堆积,被氧化之后使得该层氧化膜变得更加的致密,直到基体内的金属离子以及外界的氧不再能穿过它为止,使得氧化膜在厚度方向上停止生长。此后,由于在深度方向上扩散的阻力逐渐增大,进入到氧化膜内的氧会向两侧扩散,使得疖状腐蚀向四周扩展,最终同附近的疖状腐蚀岛融合到一起成为一个体积更大的疖状腐蚀岛。
图10 304不锈钢在高温水环境中疖状腐蚀形成机制示意图[4]
Fig.10 Schematic diagram showing the formation of nodular corrosion on 304stain less steel in high temperature water environment[4]
3 结论
(1)304NG钢在550~650℃、25MPa SCW中的腐蚀增重遵循幂指数规律,在550℃的SCW中具有较好的抗腐蚀性能,但是当温度升高到650℃时,其腐蚀增重速率急剧升高。
(2)304NG钢在SCW中出现疖状腐蚀,并且温度能够极大地加剧疖状腐蚀。
(3)304NG钢在SCW中的疖状腐蚀氧化膜为典型的两层结构,外层富铁贫铬,而内层富铬贫铁,并且内层氧化膜的厚度要大于外层氧化膜的。随着腐蚀时间的延长,腐蚀向周围发展,最终导致不同的疖状腐蚀区域相互融合。
(4)304NG钢中铬沿着晶界和在晶粒内部扩散速率的不同,导致疖状腐蚀在远离晶界处形核,并且最终发展为疖状腐蚀。
图11 SCW中304NG不锈钢疖状腐蚀机理模型
Fig.11 Model of nodular corrosion mechanism of 304NG stainless steel exposed to SCW
免责声明:本网站所转载的文字、图片与视频资料版权归原创作者所有,如果涉及侵权,请第一时间联系本网删除。
-
标签: 超临界水, 304NG奥氏体不锈钢, 疖状腐蚀
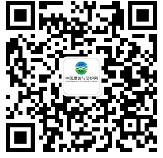
官方微信
《腐蚀与防护网电子期刊》征订启事
- 投稿联系:编辑部
- 电话:010-62316606-806
- 邮箱:fsfhzy666@163.com
- 腐蚀与防护网官方QQ群:140808414