文 | 杜金辉 1 , 吕旭东, 1,2 , 董建新 3 , 孙文儒 4 , 毕中南 1,2 , 赵光普 1 , 邓群 1 , 崔传勇 4 , 马惠萍 1 , 张北江 1
1. 钢铁研究总院高温材料研究所 北京 100081
2. 钢铁研究总院高温合金新材料北京市重点实验室 北京 100081
3. 北京科技大学材料科学与工程学院 北京 100083
4. 中国科学院金属研究所 沈阳 110016
高温合金是指以 Fe、Ni、Co 为基,能在 600 ℃以上高温抗氧化和抗腐蚀,并在一定应力作用下可长期工作的一类金属材料。高温合金既是航空发动机热端部件、航天火箭发动机各种高温部件的关键材料,又是工业燃气轮机、能源、化工等工业部门所需的高温耐蚀部件材料,是国民经济不可缺少的一类重要材料。变形高温合金是指通过铸造 - 变形工艺生产的高温合金,包括盘、板、棒、丝、带、管等产品,该类产品广泛用于航空、航天、能源、石化、核电等工业领域。本文从冶炼、均匀化、开坯、锻造、残余应力控制、探伤几个方面综述国内变形高温合金全流程制备工艺的新进展,并介绍 GH4169G、GH4169D、GH4065 和 GH4068 等新研合金,展望 FGH4096 的变形化、NGH5011 的氮化、In718 合金的 3D 打印等新技术。
1 工艺流程新进展
1.1 冶炼
国内变形高温合金冶炼通常采用真空感应 + 真空自耗两联或真空感应 + 电渣重熔 + 真空自耗三联的熔炼方式。对于用量最大的变形高温合金 GH4169 来说,有害元素与夹杂物的含量严重影响合金的性能,纯净度对其使用可靠性有重要影响。真空感应熔炼过程中,流槽具有缓冲、分液作用。流槽是位于浇注室内用于浇注的过渡装置,经过流槽中的内控装置可将氧化渣上浮,合金液从流槽的出水口流出,再由引流嘴将合金液浇注到模铸室中的钢锭模中。通过流槽可以稳定注流,改善合金液的流动形态,促进合金液中的夹杂物上浮与分离等。目前国内的流槽结构较为简单,只是一个简单的长形包,内控装置只是简单的挡板,基本为真空感应炉自带的流槽结构,远远发挥不出流槽应具备的功能和作用。根据流槽的设计和优化准则,通过水模拟和数值模拟对真空感应炉内流槽进行优化设计,使合金熔液在流槽内的停留时间大于优化前合金熔液停留时间,可增加夹杂物上浮的机会,减小死区的比例,改善流槽内流场分布和温度分布,从而提高铸锭的质量和洁净度,如图 1 所示。其中,图 1a 和 b 为优化前后流槽去除夹杂物能力的对比,图 1c 和 d 为与之相对应的停留时间分布(residence time distribution,RTD)曲线变化。
图1 真空感应熔炼流槽优化前后的对比
流槽内钢水流动状态的研究方法主要有以下 3 种:实际测定、物理模拟、数学模拟。借助水模拟和数值模拟实验,得到了内控装置挡墙、挡坝在流槽中对流场的作用规律,优化出长形流槽。通过对国外、国内普遍采用与自主设计的方形流槽钢液流动数值模拟的对比分析,发现自主设计的方形流槽在夹杂物去除能力上具有优势。
图2 真空自耗过程的传热示意图
真空感应熔炼可以得到确定的合金成分,真空自耗重熔可以保证铸锭的微观组织。国内利用 Procast 软件,对真空自耗过程进行数值模拟,图 2 为真空自耗过程的传热示意图。通过建模和有限元数值模拟,定量地描述了铸锭重熔过程中一次、二次树枝晶的分布状态,见图 3。
图3 铸锭一次、二次树枝晶枝晶间距(PDAS和SDAS)的分布状态
1.2 均匀化
高温合金铸锭在凝固过程中会产生较严重的成分偏析,为减轻和改善成分偏析,提高材质的均匀性,除改进冶炼工艺外,最重要的技术措施是进行均匀化处理,通过高温下的长时间加热,促进溶质元素原子的扩散迁移,达到枝晶干与枝晶间元素浓度差异的最小化 。对于高合金化GH4720Li合金,Al 和 Ti 总含量高达 7.5%(质量分数),铸锭中不可避免地存在着成分偏析和枝晶间共晶相,这对合金铸锭在开坯过程中的热塑性及棒材乃至锻件的组织均匀性都有不利影响 。因此,在热加工前,必须通过高温均匀化处理:(1)消除以 Ti为主的元素偏析;(2)使共晶相回溶;(3)同时保证不出现晶界弱化而影响开坯锻造的热塑性。铸锭经过合理的均匀化后,才能进行锻造开坯。
为满足工业生产需要,需将 GH4720Li 合金铸锭直径由406mm 扩大到 508mm。通过 GH4720Li 合金直径 508mm 铸锭与直径 406mm 铸锭的枝晶分布及 Ti 元素偏析情况的对比分析(见表 1 及图 4)发现,随着锭型的扩大,偏析情况会受到凝固冷速的影响而相应加剧,二次枝晶间距略微增大,枝晶变得稍微粗大、Ti 元素的偏析系数(K)有所增加,但增加幅度较小,尤其是二次枝晶间距分布范围差距也小,直径 508mm铸锭二次枝晶间距范围为 98~161μm,直径 406mm 铸锭二次枝晶间距范围为 80~160μm。
图4 直径406和508mm的GH4720Li合金铸锭中心部位纵向高倍组织
为了优化出 GH4720Li 合金直径 508mm 铸锭最佳均匀化制度,本课题组设计了 3 种不同的均匀化制度:制度 1 为(T-10℃)、30h+(T+10℃)、40h;制度 2 为 T、70h;制度 3为(T-10℃)、30 h+(T+10℃)、60 h (其中 T 为 γ′全溶温度),通过平均偏析系数和析出相对比来研究 Ti 元素的分布。由表 2 可见,经过 3 种不同的均匀化制度处理后其枝晶间和枝晶干的 Ti 元素分布均匀,而且 Ti 元素的 K 都大大减少。3 种均匀化制度中,经制度 3 均匀化后的 Ti 元素的 K 最小,经制度 2 均匀化后的 Ti 元素的 K 最大。由此可以看出,制度3 的均匀化效果最佳。
1.3 开坯
高合金化高温合金普遍具有热变形抗力大、塑性低、可变形温度区间窄等特点。为了提高 GH4720Li 合金铸锭的开坯成材率以及棒材的质量水平,需要从材料本身和工艺条件 2个方面来提高合金开坯时的热塑性:在预处理的基础上,进一步调整、优化快锻机开坯工艺参数,特别是要选择更为合理的火次加热温度及明确每火次变形量分配原则,从而可以从快锻工艺上减少铸锭开裂的倾向。
通过大量热模拟压缩实验研究了不同变形温度、变形量和变形速率下,GH4720Li 铸锭的热塑性、流变应力规律、再结晶规律,建立了热塑性与变形条件的数学模型,获得不同热变形条件下的开裂判据,优化锻造工艺参数。通过实际锻造开坯过程对数学模型进行校验。利用数值模拟方法对快锻开坯过程的工艺参数进行优化(图 5),包括逐级降温及火次变形量合理分配。
图5 GH4720Li合金快锻开坯数值模拟
快锻开坯充分破碎铸锭铸态组织之后,再辅之以径锻,可以改善棒材表面状态,提高成材率。径锻以表面变形为主,更有利于棒材外缘再结晶,会明显提高棒材的表面质量;同时径锻开坯时表面变形量大,会造成一定程度的表面温升,表面温升能补偿表面温降,进而减少表面温降造成的开裂。如果表面温升过大,又会导致已再结晶细化的晶粒发生长大。因此探索 GH4720Li 合金径锻开坯工艺的重点是制定合理的快锻和径锻变形量分配方案,以实现动态再结晶晶粒细化以及棒材表面质量的提升。从而确定合理可行的 GH4720Li 合金径锻加热温度、锤宽、送进速率、下压量以及转角等关键工艺参数,开发出 GH4720Li合金径锻新工艺(图 6)。
1.4 模锻
GH4706合金超大型涡轮盘是当代 E/F 级重型燃机的核心热端转动部件,锻件直径超过 2000mm、重量达 6t,是亟待国产化的最关键部件之一。GH4706 合金是一种 γ‘相与 γ“相强化的 Fe-Ni 基变形高温合金,成分接近于 GH4169 合金,具有力学性能优异、可锻性良好、变形强度适中、可制备大锭型、成本相对低廉等优点 。
涡轮盘的模锻既要实现盘件的热加工成型又要实现组织性能控制,二者均很重要、缺一不可,同时二者又互相影响、互相制约,这一特点随着涡轮盘锻件直径的增大而体现得更为突出。为了实现超大型涡轮盘锻件的热加工成形,对现有锻造设备的潜能已挖掘至极限,涡轮盘锻件的组织和性能随着其尺寸的增大而表现出衰减的趋势,原因在于受设备能力的制约,热加工工艺参数的制定往往无法兼顾组织和性能的最优化。
研制直径大于 2000mm 的高温合金涡轮盘锻件的另一技术关键在于模锻成形过程中的载荷控制,即能否在国内现有最大吨位的锻压机上获得几何尺寸满足要求的模锻件。目前,国内采用一火整体模锻成形,生产成熟度最高的大型高温合金涡轮盘为直径 1200mm 的GH4698 合金锻件,利用的是国内最早装备的 3×104t 水压机。值得指出,此前国内研制的直径 2200mm 的 GH2674合金涡轮盘锻件是利用 4000t 快锻机采用局部成型工艺碾压锻制而成,这一方法在组织、性能均匀性控制上存在不可避免的缺陷,不适合于制备涡轮盘等在长期复杂应力环境下工作的转动件。2013 年,我国自主设计研制的世界最大的 8×104t 模锻液压机投入试生产,并试制成功了直径 1500mm 的 GH4738 合金涡轮盘锻件,为超大型 GH4706 合金涡轮盘锻件的制备提供了一定的参考经验。但是,实现高温合金涡轮盘锻件的直径由 1500mm 向 2000mm 以上跨越仍面临很大的挑战。
张北江等研究表明,提高锻前加热温度可以降低设备载荷,降低压机压下速率也能够降低合金的变形抗力,但会延长总的锻压时间进而加剧坯料热量的散失。因此,要获得最低的锻造载荷,最佳的压下制度是变形初期采用较高的压下速率以缩短总锻压时间,当设备载荷饱和后转入恒压状态,以最大限度地发挥设备潜力。鉴于此,构建了 GH4706合金的本构关系与显微组织演化规律模型,应用数值模拟技术进行热加工工艺优化,在解决超大型 GH4706 合金涡轮盘锻件的载荷控制基础上,最大限度优化锻件组织和性能。最终利用高可靠度的数值模拟技术,充分挖掘我国 8×104t 吨油压机的设备潜力,实现了超大型GH4706 合金涡轮盘锻件的国产化(图7),盘件性能达到了美国 GE-B50A651标准的要求。
图7 直径2100 mm超大型GH4706合金涡轮盘锻件实物照片
1.5 残余应力
变形高温合金盘锻件制备过程中形成的残余应力会在不同工序间不断演化传递,最终对高温合金盘件的加工和使役性能造成重要影响。因此有必要掌握变形高温合金盘锻件全部工艺过程残余应力的影响因素、分布特征、演化规律与内在机制,才能预判其对后续加工变形及使用性能的影响,进而优化、精化制备工艺;这同样也是实现航空发动机正向设计、寿命预测的重要基础。经过深入、细致的研究工作,总结了高温合金涡轮盘锻件内部残余应力的测试方法,阐明了固溶、淬火、时效、零件加工等制备工艺过程中残余应力的演化规律与机制。
对于高温合金锻件而言,表层残余应力与冷加工工艺和喷丸工艺相关,会影响零件的疲劳性能,但是要研究残余应力对盘件整体结构的影响,需要测试分析距离表面 10 mm 甚至更深的内部残余应力,分辨率要求为毫米级。图 8显示,可以满足要求的方法主要包括中子衍射法(neutron diffraction)、轮廓法(contour method)、深孔法(deep-holedrilling)和超声法(ultrasonic)。
图8 各种残余应力测量方法的测量穿透与空间分辨率
为了获得足够的强化水平,高温合金盘锻件在锻造成形后常需要在固溶处理后以一定速率快速冷却,以确保 γ”或 γ’强化相在此过程中不发生粗化。研究表明,影响高温合金锻件中残余应力的最主要工序是固溶处理后的快速冷却过程(或锻后冷却)。淬火应力形成的本质原因是锻件不同区域之间的体积差异,这既包括温度不同引起的热膨胀差,也包括相变引起的体积变化。
综上所述,高温合金盘锻件制备工艺过程中的内部残余应力主要产生于固溶或锻后淬火过程形成的温度梯度,主要以弦向和径向应力为主,沿轮廓呈“内拉外压”特征分布,其量级与淬火态合金的室温屈服强度水平相当。强化相的析出行为会改变合金冷却过程中不同温度下的膨胀系数和强度水平,从而对残余应力分布和量级产生重要影响。
另外,在研究过程中还发现 GH4169合金中 γ“相在服役过程的变体选择粗化现象 。γ”相作为 GH4169 合金的主要强化相,在基体中有 3 种位向关系的变体,其尺寸、形貌和分布状态是决定合金力学性能的关键因素。在一定温度作用下,GH4169 合金中的 γ“相会发生扩散控制的粗化现象。然而前期研究通常只考虑温度和时间对组织失稳的影响,忽略了合金实际制备和服役过程中应力的作用。长时服役后的 GH4169合金涡轮盘中发生的 γ”相粗化存在变体选择现象:1 种或 2 种位向关系的γ“变体被择优保留下来,其余位向关系的变体消失。通过电子背散射衍射(EBSD)结合扫描电镜(SEM)研究发现,γ”相的变体选择行为受到外加应力和晶粒取向的影响,如图 9 所示。经热力耦合作用的 GH4169 合金多晶材料中,多数晶粒内具有γ“ γ位向关系的γ”
相变体会被择优保留,另外 2 种 γ“相变体趋于消失。进一步研究发现,γ”粗化过程中 3 种 γ“相变体均保持圆盘状,并在各自 c 轴方向承受较大但无差异的压应力;热力耦合条件下,外加应力与 γ”相及周边 γ 基体间的内应力叠加,导致不同 γ“相变体的 γ”/γ错配应变发生改变,引起 3 种 γ“相变体的弹性应变能出现差异。从而,弹性应变能相对较低的 γ”相变体尺寸长大的阻力变低,发生择优粗化;弹性应变能较高的γ“相变体尺寸长大受到抑制,会在 Gibbs-Thomson 效应的作用下逐渐溶解于基体。GH4169 合金中 γ”相的变体选择会导致合金高温强度和蠕变抗力降低。
图9 GH4169合金热力耦合作用后γ“相变体选择行为与晶粒取向的关系
1.6 探伤
超声检测作为无损检测的一种重要方法,被广泛应用于航空航天、钢铁冶金等工业领域,用于检查材料内部气孔、裂纹、夹杂等缺陷。变形高温合金是航空航天领域大量采用的转动类零件用材料,其超声检测显得尤为重要。探头发出的超声波进入工件内部进行传播,当工件内部存在声学特性与基体不同的组织不连续或不均匀时,超声波在界面上发生传播方式和信息的改变,由此可以对材料内部组织不连续或不均匀进行分析,从而为无损检测和评价提供定性、定量依据。
GH4169 合金盘锻件组织致密,晶粒尺寸 0.022~0.0078mm,一般要求检出直径 0.8 或 0.4mm 甚至更小当量平底孔大小的缺陷,这对超声检测方法和仪器本身均提出了较高要求。在超声波检测过程中盘锻件因局部组织的差异会呈现不同的杂波显示,而国内标准中未对不超标信号做出规定,因此有必要对盘锻件组织尤其是晶粒尺寸与超声杂波之间的关系进行充分研究,以确定影响检测结果的主要原因和适宜的检测参数。图10 为涡轮盘超声 C 扫图。
图10 涡轮盘超声C扫图
实验结果表明,某种固溶热处理制度的 GH4169 合金试样杂波幅度均在 10% 以下;与锻态试样相比,不同固溶热处理试样底波降低幅度不同,温度越高,底波降低幅度越大,经 1050 ℃热处理的 5# 试样底波降低幅度大于 4# 试样,3# 试样次之,如表 3 所示。因此,在试样表面状态、检测参数一致的前提下,GH4169 合金涡轮盘的晶粒尺寸在一定程度内可通过超声检测进行表征,晶粒尺寸越小,底波降低幅度越大。
综上所述,对于涡轮盘中出现的局部杂波,采用 10 和 5 MHz 探头、0.4 mm 当量的检测灵敏度均可将杂波检出,且 10 MHz 探头信噪比优于 5 MHz 探头,故更适合选用;与 5 MHz 相比,采用 10 MHz 探头进行底波监控,可获得更为精确的底波幅值,可以作为定量比较晶粒尺寸的参考依据。
2 新合金
2.1 GH4169G合金
传统观点认为,P 是高温合金中典型的有害元素 。国内于 1990 年代初期发现了 P 可将 GH4169 等合金持久寿命提高 3 倍以上,并将其稳态蠕变速率降低一个数量级以上。随后又发现 P、B 具有更加强烈的复合强化作用,即 P、B 复合加入可以更加强烈地提高 GH4169 合金的持久蠕变性能。P、B 的复合强化作用直到 750 ℃仍很显著,表明其可以提高合金的工作温度。在对 P 强化以及 P、B 复合强化机理深入研究的基础上,通过进一步研究 P、B 对合金组织、性能以及加工工艺的影响,发展了 GH4169G 合金 。GH4169G 合金在全面保持了 GH4169 合金优异的综合使用性能的基础上,将使用温度提高了30 ℃,达到680 ℃;650 ℃下的使用寿命提高3倍以上,长寿命特点十分突出;同时焊接和热加工等工艺性能与GH4169合金基本相当。因此,它适合于制作对综合使用性能和工艺性能要求比较全面的整体叶盘,以及对寿命和安全可靠性要求较高的部件,具有比较广阔的应用前景。
2.2 GH4169D合金
GH4169D 合金的研制成功填补了世界上 2 个最广泛应用高温合金——650 ℃用GH4169 合金和 750 ℃用 GH4738 合金之间长期存在的空白。GH4169D 合金是在 GH4169 合金基础上,通过降低 Fe 的含量,加入固溶强化元素 W 和 Co,调整 Al+Ti 含量以及 Al、Ti 比,并适当提高 Nb 含量以及调整微量元素含量而研制成功的 。与 GH4169 合金相比,GH4169D 合金主要强化相由 γ“相转变为了 γ‘相,650 ℃以上热稳定性显著增加,因而合金使用温度得到显著提高;与其它 γ’相强化的合金,如 GH4738相比,GH4169D 合金中的 γ‘相析出速率明显减慢,使其热加工性能和焊接性能得到显著改善。因此,GH4169D 合金兼具了 GH4169 合金高强度、良好的热加工和焊接性能,以及 GH4738 合金使用温度高的综合优点,其长期使用温度可达 704 ℃,是未来高性能航空发动机颇具潜力的关键材料,也被称为下一代 GH4169 合金。GH4169D 合金虽然是在GH4169合金成分基础上发展起来的,但与 GH4169 合金相比,GH4169D 合金具有完全不同的相组成。众所周知,GH4169 合金是以 γ”相强化为主,辅以 γ’相强化,晶界由 δ 相组成。而GH4169D 合金则以 γ‘相强化为主,晶界相最初也被认为δ相,后经研究证实,晶界相主要为具有 η-Ni3Ti 的结构的Ni3Al0.5Nb0.5 (或者称为 η-Ni6AlNb)相。所以与 GH4169 合金相比,GH4169D合金无论是化学成分、基体强化相还是晶界析出相,都发生了非常大的改变,是完全不同的 2 种合金,其相析出、溶解规律以及对性能的影响机理也有所不同,GH4169D 和 GH4169 合金的组织对比如图 11 所示。
通过物理化学相分离以及X 射线衍射等实验,Wang 等对 γ’相和η-Ni3Al0.5Nb0.5 的相组成做了进一步确定。结果证实,标准热处理条件下 γ‘相的质量分数可占 GH4169D 合金 的 22%~27%,η-Ni3Al0.5Nb0.5 可占到 1.5%~7%,其质量分数随着热处理制度和化学成分的变化会有所不同。γ' 相 和 η-Ni3Al0.5Nb0.5 相 中均含有一定量的 Nb,其原子分数分别达到 9% 和 13%,由于 Nb 在镍基基体中具有较低的扩散系数,这被认为是GH4169D 合金中 γ’相的析出速率要慢于其它常见 γ‘相强化合金的重要原因。通过调整 GH4169D 合金中 γ’相和 η-Ni3Al0.5Nb0.5 相不同的分配比例,进而得到合金不同的综合性能,可应用于不同服役环境部件的制备。
图11 GH4169D和GH4169合金经标准热处理后的组织
2.3 GH4065合金
在依托铸锻工艺发展高性能涡轮盘材料方面也取得了重要进展,研制了GH4065、GH4079 和 GH4975 等高性能变形高温合金涡轮盘材料,特别是 GH4065合金的综合性能达到粉末冶金材料的水平,有望为我国先进航空发动机热端转动部件的选材提供成熟可靠的解决方案。采用铸锻工艺制备高合金化高温合金大尺寸锻件,需要掌握通过化学成分优化来降低高合金化材料枝晶偏析倾向性的原理与方法;解决大尺寸自耗重熔锭熔铸过程稳定性问题;实现热模锻造条件下的锻件组织和性能高效控制。
针对先进航空发动机对热端转动部件的需求,新型高性能变形高温合金的研制工作充分总结现有涡轮盘材料设计的成功经验及存在的问题,在对一系列模型合金的力学性能和工艺性能进行对比和筛选的基础上,最终以成熟的粉末冶金涡轮盘材料 FGH4096 的化学成分为基础,针对铸锻工艺路线的要求进行全面优化,研制了新型的 GH4065 合金,其典型成分如表 4 所示。作为对照,表中同时列出了国内研制的主要高合金化变形高温合金的化学成分。
时效状态下GH4065合金与FGH4096合金的 γ‘相体积分数均为 42%,低于 GH4720Li 合金的 45%。GH4065 合金的 γ’相平衡溶解温度为 1119 ℃,因此比 GH4720Li 和 GH4975 合金具有更大的热加工温度窗口。在 FGH4096 合金基础上,GH4065 合金针对铸锻制备工艺的特殊要求对化学成分进行了以下几方面的优化:
(1) 主元素方面。在保证 γ/γ‘错配度不变的情况下,优化各固溶强化元素与 γ’相形成元素之间的比例,特别是相对于粉末冶金 FGH4096 合金限制了 Nb 的加入量,以有效降低材料熔铸过程中的枝晶偏析倾向性。GH4065 合金中允许加入质量分数达到 1.0% 的 Fe,一方面可以改进熔炼过程中 Nb 等合金元素的加入方法;另一方面,可以实现与产量最大的 Fe-Ni 基合金 GH4169 共用坩埚,方便返回料的回收利用,因而有助于提高生产效率和降低生产成本。
(2) 间隙元素方面。GH4065 与粉末冶金 FGH4096 合金相比最大的差别是 C 含量大幅度降低,成分上限控制在质量分数 0.01% 的水平,仅为粉末冶金 FGH4096 合金的 1/3~1/5,低于同样采用低间隙元素设计的 GH4720Li 合金。
降低 C 含量可以使钢锭中的一次碳化物尺寸和数量都大幅度下降,同时有效减轻碳化物形成元素 Nb 和 Ti 元素的枝晶偏析倾向性。一次碳化物尺寸和数量的减小可以改善因碳化物不均匀分布导致的奥氏体晶粒尺寸分散性大的问题,同时作为主要的疲劳裂纹源,碳化物尺寸和数量的减少还可以显著提高材料的疲劳性能。GH4065 合金对 B 元素的最大加入量做出了限制以解决大尺寸钢锭熔铸过程中 B 的宏观偏析问题,通过优化Zr 等微量元素的加入量来改善合金高温持久性能。
2.4 GH4282合金
GH4282 合 金 在 保 持 一 定 数 量 的沉淀强化 γ‘相的基础上,通过控制γ’相的结构、组成和析出动力学,解决了高强度时效强化燃烧室合金中由于γ‘相的大量快速析出导致的冷加工和焊接困难的难题 。与 GH4141 合金相比,GH4282 合金在具有相当的热强性能条件下,空冷后合金板材室温塑性达到 50%,其冷加工性能与固溶合金相当;合金焊接性能优异,不需要特殊的焊前焊后热处理;其 700~900 ℃长期时效 1000 h 后没有 TCP 相析出,室温拉伸塑性保持在 20% 以上。可见,合金在 650~950 ℃范围内保持了极佳的高温强度和热稳定性,同时可对焊接和冷加工性能进行很好的平衡和优化 。
表 4 还列出了目前国内外主要的时效强化型燃烧室合金的主要化学成分 。可见,与欧美系列的 GH4738 和GH4141 合金相比,GH4282 合金具有很好的继承性,GH4282 合金主要对 Co、Mo、Ti 和 C 元素进行了调整。其中 Co元素含量一般控制在 10%~20% 之间,主要用于增加基体对 γ’相和固溶强化元素的溶解能力,GH4282 合金中取其下限进行控制;Mo元素作为大尺寸原子,具有强的固溶强化能力和难迁移扩散的特点,在 GH4282 合金中 Mo 元素首先对基体进行固溶强化,同时 Mo 元素参与γ‘相形成,对 γ’相进行强化并影响其形成和长大过程。在低于 8.5% 的范围内,随着 Mo 元素含量增加,合金持久性能增加明显,表明 Mo 元素对基体和γ‘相进行了有效强化,在大于8.5%的范围内,Mo 元素增加,合金持久性能降低,其机制目前还不确定,可能是因为 Mo 元素对基体固溶强化达到极限的同时,影响了 γ’相与基体的共格错配度,进而弱化了 γ‘相的强化效率;Al 和 Ti 元素作为 γ’相形成元素,其含量直接影响 γ‘相数量。从表 4 还可以看出,与 GH4738 和 GH4141 合金相比,GH4282 合金降低了 Ti 含量,进而降低了 γ’相数量,这在一定程度上对合金的加工性能和高温强度起到了平衡作用。
2.5 Ni-Co基合金
自 2006 年,Sato 等发现在钴基合金体系中可析出稳定的L12结构γ‘相,使得发展时效强化钴基高温合金成为可能。由于该类合金具有更高的 γ’强化相体积分数、热加工窗口较宽、凝固偏析倾向较小等优势,国际上已经形成了发展此类合金的热潮。美国 GE、Allvac、英国 R&R 和日本 NIMS 等均对该合金体系开展了大量研究工作,它已成为 750 ℃以上使用的高代次航空发动机涡轮盘选材。近年来,通过自主设计合金成分和小锭型实验,证明该合金 γ‘强化相体积分数达到 50%,热加工窗口明显宽于镍基变形高温合金,同时具有良好的组织稳定性,其性能接近第三代粉末高温合金水平,可以作为具有高的使用性能和良好工艺性的涡轮盘材料。图 12 为时效强化 Ni-Co 基合金的透射电镜(TEM)照片。
图12 时效强化钴基合金在900 ℃退火72 h的TEM像
GH4068 合金是一种新型 Ni-Co 基铸锻变形高温合金,其承温能力可达750℃,接近最强商用粉末变形高温合金(ME3 和 RR1000)的水平。该合金的设计理念为:强化“中温区(服役温度区间)”、弱化“高温区(变形加工区)”,该设计思路(如图 13 所示)解决了难变形合金强化易、变形难的瓶颈问题,在 U720Li 合金(目前承温能力最高的铸锻变形高温合金)基础上,通过对主元素(如 Co 和 Ti)调整,制备出超过 750℃铸锻变形高温合金,使其在低温和中温区的强度比原合金有很大提升,但在高温区低于原合金。
图13 GH4068合金的成分设计思路
研究表明,在低温低应力下,新型Ni-Co 基变形高温合金主要通过位错切割 γ’相形成大量层错;当蠕变温度升高或加载载荷较高时,合金中的位错运动速率提高,合金的变形主要以层错和孪生方式进行;当蠕变温度高于 725 ℃时,合金中的 γ‘相开始发生粗化,并且部分小尺寸的 γ’相溶解,促使 γ‘相之间的基体通道增大,更加有利于位错的绕过;因此,当蠕变温度达到 815℃时,合金的主要蠕变变形方式为位错绕过机制,如图 14 所示。
图14 不同蠕变条件下GH4068合金的变形机制
GH4068合金在中温区蠕变的主要变形机制是位错切割 γ’相形成层错和微孪晶,如图 15 所示。蠕变过程中层错的形成是由于全位错 a/2<110> 滑移过程中遇到 γ‘相时分解成 a/3<12 1>和 a/6<112> 不 全 位 错,a/3<12 1>位错切入 γ’相中,而 a/6<112> 位错则留在 γ/γ‘相界面处,从而形成了层错。由于 GH4068 合金的层错能低,因此变形过程中更容易形成层错。当加载载荷较大时,拖拽位错运动的应力也相应提高。并且,层错的宽度受应力影响,当应力提高时,层错宽度变宽,因此,存在于不同 γ′相中的层错由于被拉宽而连接到一起形成连续层错,所以在中温变形过程中,GH4068 合金变形组织中出现大量在基体和第二相中广泛存在的连续层错。
图15 GH4068合金中温区蠕变变形组织
3 新技术
3.1 FGH4096合金变形化
针对先进航空发动机用高合金化程度的镍基涡轮盘铸锭偏析严重、组织均匀性难控制的特点,开发了电渣重熔连续定向凝固冶炼 +3D 锻造制坯 + 等温锻造制备难变形涡轮盘的新型铸锻工艺技术,该技术已成功用于制备高性能、低成本、零缺陷的变形 FGH4096 合金涡轮盘,其中 3D 锻造制坯是指采用常规锻造设备在坯料三维方向依次完成特定变形量的锻造过程为一个循环的 3D 锻造,在一个锻造循环里每个方向都可以当一次锻造端面,两次锻造侧面,最后回到坯料的原始形状,通过多个循环的锻造解决高合金化合金坯料因变形量不足和冷模组织造成的组织均匀性问题,为后续模锻提供组织完全均匀的坯料。
电渣重熔连续定向凝固铸锭无大尺寸 η相、大尺寸硼化物偏析以及碳氮化物条带,铸锭具有优异的热加工塑性;锻坯采用 3D 锻造工艺制备,大幅度消除变形过程中接触锤砧的表面变形死区,坯料微观组织无各向异性,晶粒尺寸范围10~16 μm;涡轮盘锻件采用等温锻造,锻件不同部位晶粒组织均匀细小,超声波检测的可探性高。
图16 FGH4096电渣重熔连续定向凝固铸锭(直径270 mm)中部宏观低倍组织
FGH4096 合金定向凝固铸锭中部宏观低倍组织如图 16 所示,定向柱状晶轴向取向偏离度≤ 20°。合金凝固后的枝晶间距是衡量偏析程度的重要参数,枝晶间距越小即枝晶干排列越紧密,合金偏析程度越低,而且凝固过程中枝晶间区域的减小也使得枝晶间析出相尺寸减小,其中二次枝晶间距是衡量微观偏析的重要参数。从铸锭中间 R/2 (R 为铸锭的半径)处截取试样观察铸态微观组织,如图 17 所示,FGH4096 合金定向凝固铸锭中二次枝晶排列紧密,枝晶间距约 100μm。
图17 FGH4096合金定向凝固铸锭R/2处微观组织(R为铸锭半径)
变形 FGH4096 合金涡轮盘采用等温模锻,模具温度接近坯料温度,材料流动性和充填性好,同时坯料为晶粒尺寸10 μm 的细晶坯料,热变形抗力小,锻件的残余应力较低。目前制备了数批件直径 630 mm 涡轮盘及挡板锻件、涡轮轴等,锻件超声波可探性较好,超声波水浸检验杂波水平控制在低于昺0.4-21dB,锻件探伤一致性和稳定性好。图18 为变形 FGH4096 合金等温锻造涡轮盘锻件(直径 630 mm)纵剖面微观组织。
3.2 NGH5011合金
氮化现有的高温合金体系和强化原理下,燃烧室合金长时耐温能力(以 100h、40 MPa 持久温度表征) 在近 30 年内无法突破 1000 ℃的服役温度。开发新型燃烧室合金,显著提高燃烧室用高温合金的长时耐温能力,需要突破现有合金体系或创新强化技术。目前可用于燃烧室的新材料主要有氧化物弥散强化合金、陶瓷、难熔金属合金和复合材料等新材料,这些合金在 1100 ℃以上都表现出较高的高温强度。但是上述材料都有诸多不可克服的问题,距离部件的成熟制备还有很大距离。
新型内生弥散氮化物强化高温合金采用 TiN 作为强化相,其 1100 ℃、100h 持久强度比传统高温合金高 2~3 倍,可满足未来 1100 ℃以上航空发动机主燃烧室、加力燃烧室和喷口等部件用合金的选材。该合金实现内生氮化物弥散强化是在部件制备成型后,因此在获得高温强度的同时,还兼顾了部件的加工、焊接性能,解决了目前燃烧室合金中使用性能和高温性能对立的矛盾。内生弥散氮化物强化合金的相关研究在 1970年就见报道,其中 Kindlimann 和 Ansell在不锈钢基体中首次进行了内生弥散氮化物强化技术。随后 Petrova 对高温合金内生氮化物强化技术进行了深入广泛的研究,其研究一直持续到 2000 年后,涉及 Fe、Ni 和 Co 3 种基体,研究了不同氮化物形成元素的氮化物强化效果,最终研制出比较成熟的合金 ВЖ155。
国内开发了氮化物强化高温合金NGH5011,在该合金基础上针对内生弥散氮化物强化高温合金的氮化工艺流程中涉及的 N 在表面的吸附溶解、N 在基体的均匀扩散、反应界面上氮化物的析出等关键物理化学过程,开展了高温合金内生氮化物弥散强化技术的系统研究工作。
将 NGH5011 合金氮化后的力学性能与其它燃烧室用高温合金进行比较,以评估其力学性能。表 5 所示是各种合金的室温拉伸、1100 ℃高温拉伸及1100 ℃和 30 MPa 下持久性能的对比。
可见,新型内生氮化物弥散强化高温合金相对于传统高温合金的高温性能优势明显。相对于氧化物弥散强化高温合金 MGH956,NGH5011 合金在瞬时拉伸性能上表现出一定优势,其 1100 ℃、30 MPa 持久寿命不及粗晶条件下的MGH956 合金,但略高于细晶 MGH956合金。综上所述,氮化后的 NGH5011 合金在室温拉伸、高温拉伸和高温持久等方面表现出优异的综合性能。
3.3 增材制造3D-In718
激光增材制造是基于“离散 - 堆积”、“添加式制造”的基本概念发展起来的金属零件全密度快速直接制造技术。各种类型的激光增材制造技术,如激光熔覆沉积技术(laser engineerednet shaping,LENS)、选择性烧结技术(selective laser sintering,SLS)、直接激光成形技术(direct laser forming,DLF)等,本质上都是利用送粉或铺粉方式逐点逐层添加沉积,实现三维任意形状高性能金属零件的近净成形。作为一项短周期、低成本的绿色数字制造技术,激光增材制造技术具有快速、柔性、高性能等诸多优势,在航空、航天、核电、石化、船舶等高端装备制造中有巨大的发展潜力和广阔前景。
它将先进材料技术与先进制造技术融为一体,既能保证零件的形状和尺寸精度,又能保证零件的表面光洁度、成分、组织和性能达到使用要求。
钢铁研究总院高温材料研究所利用增材制造技术,成功制备出 3D-In718 合金的燃气涡轮盘(直径 150 mm)和整体叶轮(直径 220 mm),如图 19 所示,直接成形零件致密度达到 99.9%,组织和性能均远优于铸件,室温、高温拉伸强度和塑性、持久性能均可满足锻件标准,燃气涡轮盘力学性能如表 6 所示,其中解剖部分包含2 组实验数据。
图19 增材制造3D-In718燃气涡轮盘和整体叶环
4 结束语
高温合金既是航空发动机热端部件、航天火箭发动机各种高温部件的关键材料,又是工业燃气轮机、能源、化工等工业部门所需的高温耐蚀部件材料,是国民经济不可缺少的一类重要材料。变形高温合金通过铸造-变形工艺生产,包括盘、板、棒、丝、带等产品,广泛用于航空、航天、能源、石化、核电等工业领域。本文主要介绍了变形高温合金的制备工艺流程、新合金研制以及新技术 3 个方面在国内近 10 年的最新进展。
航空、航天动力系统和燃气轮机需要变形高温合金的高温力学性能和耐蚀性能实现稳定、高效的动力输出;而随着海洋工程装备、石化装置、核电设施等高端制造业进入新的发展阶段,也需要国产耐温、抗蚀性能优异的变形高温合金保证装备的可靠运行。为此,国内需要构建重点牌号变形高温合金的全方位成分 - 工艺 - 组织 - 性能谱,揭示出合金性能及生产工艺的共性和特性;在成规模、批量生产中研究提高航空、航天动力系统和燃气轮机用关键变形高温合金的工程化技术水平和质量稳定性;针对海洋工程装备、石化装置、核电设施等重大需求,研究开发变形高温合金的适用性能和生产技术,并逐步得到应用。因此,伴随绿色制造、智能制造技术的方兴未艾和装备升级,在国民经济中占据重要地位的变形高温合金产品必将向低成本、高均质、近成形、长寿命的方向迅猛发展,全面提升我国变形高温合金产业技术进步是大势所趋。
免责声明:本网站所转载的文字、图片与视频资料版权归原创作者所有,如果涉及侵权,请第一时间联系本网删除。
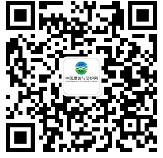
官方微信
《腐蚀与防护网电子期刊》征订启事
- 投稿联系:编辑部
- 电话:010-62316606-806
- 邮箱:fsfhzy666@163.com
- 腐蚀与防护网官方QQ群:140808414