21世纪以来,航空航天事业的发展进入新的阶段,将会推动航空航天材料朝着质量更高、品类更新、功能更强和更具经济实效的方向发展。航空材料与航空技术的关系极为密切,航空航天技术的发展必然离不开与其相对应的航空航天材料的发展,航空航天材料在航空产品发展中具有极其重要的地位和作用。用于航空航天材料制造的许多零件往往需要在超高温、超低温、高真空、高应力、强腐蚀等极端条件下工作,有的则受到重量和容纳空间的限制,需要以最小的体积和质量发挥在通常情况下等效的功能,有的需要在大气层中或外层空间长期运行,不可能停机检查或更换零件,因而要有极高的可靠性和质量保证,不同的工作环境要求航空航天材料具有不同的特性。优良的耐高低温性能、耐老化和耐腐蚀、适应空间环境、寿命和安全是航天航空领域里材料研究的几项重要课题。
01 舰载机的腐蚀失效及其预防
航空母舰舰载机是航母最为主要的攻击武器。舰载机在海洋环境下服役,它不同于陆基飞机,不仅受到海洋气氛、海水及持续的干 / 湿交替循环的侵蚀,还会受到舰艇燃烧废气、舰载机发动机废气等的腐蚀,特别是这些废气与海洋盐雾组合成 pH 值达到 2.4 ~ 4.0 范围的高酸性潮湿液膜,使得其受到的环境腐蚀问题相当地严峻。如我军某舰载直升机的服役寿命不及陆上的 20%; 某型飞机由于不适应海南的高温湿热环境,出勤率低于 20%,这些充分说明海军航空舰载机遭受腐蚀的严重性。
腐蚀问题给装备带来重大的经济损失,资料表明,美国海军估计每年用于腐蚀防护及研究的费用在 20 ~ 30 亿美元,其中飞机部件的防腐费用占到全年维修费用的 1/3。腐蚀不仅造成巨大的经济损失,同时也影响到装备的安全使用。如美海军 F14 飞机前起落架汽缸支柱上发生腐蚀导致一等事故,从而造成F14 雄猫飞机全面停飞。
舰载机腐蚀失效常见模式及其特点
舰载机在实际工程应用中,主要的腐蚀失效模式包括点蚀、丝状腐蚀、晶间腐蚀、应力腐蚀和氢脆 5 种。
点蚀
点蚀是腐蚀表面呈点坑状,腐蚀点多、比较浅,但发生在表面有限面积上的腐蚀,其腐蚀很深、成巢穴。
发生点蚀损伤与金属构件表面组织结构的不均匀性,尤其与表面的夹杂物、表面保护膜的不完整性有关。点蚀坑的扩展不仅包括金属的溶解过程,而且包括通过已溶解的金属离子的水解使腐蚀坑底部具有较高的酸度使坑底扩展这一过程。
点蚀坑边沿基本比较平滑,因腐蚀产物覆盖,坑底呈深灰色,很多时候由于腐蚀产物覆盖,从表面无法看到点蚀坑的存在。垂直于蚀坑表面观察,蚀坑多呈半圆形或多边形,螺栓长期使用后表面出现腐蚀坑,即为典型的皮下变形闭口蚀坑。很多腐蚀坑由于腐蚀产物覆盖其特征不明显,清洗后则清晰可见。
点蚀并不一定择优沿晶界扩展。菊花形点蚀坑往往外小内大, 犹如蚁穴般,所以点蚀损伤对金属结构件的危害很大。
点蚀多发生在与表面生成钝化膜的金属材料上(如不锈钢、铝、铝合金)或表面有阴极性镀层的金属上(如碳钢表面镀锡、铜、镍)。点蚀导致的失效大多都是氯化物或含氯离子的氯气所引起的,特别是次氯酸盐的腐蚀性更强。
溶液中的氯离子浓度越高,合金越易于发生点蚀。而舰载机正是处于氯离子浓度很高的环境中,F/A-18 飞机即存在点状腐蚀。
丝状腐蚀
丝状腐蚀是一种在氧浓差控制下的电化学腐蚀,一般发生在涂漆的铝底层。
丝状腐蚀先以涂膜的破损处(如从舰载机的紧固件周围和涂覆层已经破裂的蒙皮边缘)开始,首先形成点状腐蚀,在点蚀处,由于凝结水膜、氧及腐蚀介质的作用,腐蚀向周边膜下扩展,凝点在扩展中形成了氧浓差电池致激发丝状腐蚀的形成。
丝状腐蚀的产生主要与环境、表面涂料、金属基表面处理工艺等因素有关。
如环境因素中,相对湿度较大有利于丝状腐蚀产生。研究表明,铝合金在相对湿度大于 80% 时,丝状腐蚀的丝迹随着相对湿度的增加而加宽。此外,腐蚀介质中的氯离子、二氧化硫等对丝状腐蚀的产生和发展起着促进作用。
舰载机机身蒙皮出现不同程度的丝状腐蚀, 不但增加了飞机的防腐维修费用,而且,丝状腐蚀可能会导致点腐蚀和晶间腐蚀,甚至会危及飞机的飞行安全。
晶间腐蚀
晶间腐蚀是腐蚀沿晶界发生并扩展。晶间腐蚀不仅降低材料的机械性能,而且由于难以发现,易于造成突然失效。
大多数的金属和合金,如不锈钢、铝合金,由于碳化物分布不均匀或过饱和固溶体分解不均匀,引起电化学不均匀,从而促使晶界成为阳极区而在一定的腐蚀介质中发生晶间腐蚀。金属构件的晶间腐蚀损伤起源于表面,裂纹沿晶扩展。
晶间腐蚀的一种常见的形式是剥落腐蚀,也称为层状腐蚀。这类腐蚀大多出现在平面状的铝合金中。
应力腐蚀
应力腐蚀是指金属构件受拉应力作用并在特定介质中,由于腐蚀介质与应力的共同作用所导致的腐蚀。飞机结构中,铝合金、钢等结构件(如框梁、紧固件、卡箍等)大多数都承受拉应力的作用,并且均在一定腐蚀气氛环境下服役,因此,应力腐蚀导致开裂也是飞机结构,特别是舰载机结构中常见的一种失效模式。由于应力腐蚀开裂是典型的滞后破坏形式,对于结构的安全危害很大。
金属构件发生应力腐蚀开裂需具备3 个条件:材料的应力腐蚀敏感性、特定腐蚀环境和拉伸应力。应力腐蚀是一种局部腐蚀,而且腐蚀裂纹常常被腐蚀产物所覆盖,从外表很难观察到。裂纹源处常有腐蚀产物或点蚀坑,表明应力腐蚀裂纹源于点蚀、晶间腐蚀等化学损伤缺陷。应力腐蚀断口的微观形态可以是解理或准解理、沿晶断裂或混合型断裂。应力腐蚀裂纹扩展过程中会发生裂纹分叉现象。影响构件发生应力腐蚀开裂失效的因素是多方面的,包括材质因素、环境因素和受力状态等。
氢脆
由于氢渗入金属内部导致损伤,从而使金属零件在低于材料屈服极限的静应力作用下导致的失效称为氢致损伤,亦称氢脆。氢脆是飞机结构中高强度结构件(如紧固件等)的重要失效的形式之一。由于氢脆多为脆性断裂,失效无法预先判知,危害很大。
氢脆根据氢的来源不同,可分为内部氢致损伤和环境氢致损伤。内部氢致损伤是指材料在冶炼、电镀、酸洗等工艺过程中,由于氢渗入金属内部,同时在工作应力或残余应力的作用下出现的氢致损伤。环境氢致损伤是指在紧固件在使用环境下氢渗入金属内部,并在拉应力作用下出现的氢致损伤。
氢脆断裂多发生在应力集中处,断口微观形貌一般显示沿晶断裂,也可能是穿晶断,断裂具有延迟性,并且其工作应力主要是拉应力,特别是三向静拉应力。高强度钢氢脆沿晶断裂晶面上典型的“鸡爪痕”特征。影响紧固件氢致延迟开裂的因素较多,包括氢含量、工艺因素,材料组织状态、材料强度、应力因素等。
舰载机腐蚀失效及其预防
由腐蚀导致飞机构件失效的微观机理包括晶间腐蚀、应力腐蚀、氢脆、腐蚀疲劳等。产生腐蚀的原因主要是:
①构件结构设计存在缺陷;②制造构件材料的工艺状态不合理;③制造构件的材质选择不当。根据因飞机构件腐蚀失效造成事故的几个具体案例,阐述飞机构件腐蚀失效的预防措施:
设计
案例 1:某型外贸机机身 25 ~ 27框接头耳片裂纹埃及空军对某型机定检时发现 25 ~ 27 LD5 铝合金框接头耳片裂纹, 普查发现大量飞机存在类似裂纹。25 ~ 27 框采用表面阳极化处理。失效分析结果表明,接头耳片裂纹性质为应力腐蚀裂纹,接头耳片螺栓孔与钢衬套的过盈配合量过大导致耳片受到较大的拉应力,以及耳片厚度大于钢衬套配合段长度,导致在耳片内侧的螺栓孔内表面有长 0.5 ~ 1mm 暴露在空气中失去保护,这是导致应力腐蚀裂纹产生的主要原因。此外,螺栓孔打孔是在接头阳极化处理后再进行的,导致在耳片内侧表面产生金属卷边和阳极化膜局部破裂,这也促进了应力腐蚀裂纹的产生。
类似的故障在我国歼 8 飞机也出现过,这类故障一方面是由于海洋恶劣的腐蚀性环境等外部因素,更主要的是在结构设计中存在缺陷。在设计中没有充分考虑对导致腐蚀的因素进行有效控制。主要是过大的过盈配合导致拉应力、衬套与孔配合导致金属裸露、打孔工艺不合理等多个不合理的设计因素。
飞机的腐蚀控制是一项系统工程,其控制过程总的来说包括补救性控制和预防性控制 2 个主要方面。补救性控制是指当发现飞机结构产生腐蚀后设法消除,显然这是一种被动的办法。预测性控制是指预先采取必要的措施,最为关键的是从结构方案设计开始,根据飞机将来可能的使用环境和功能要求来制定腐蚀控制方案。与设计相关的一些防腐技术主要有:①采取密封的结构形式,防止海水、雨水、盐雾、潮湿空气等进入结构内部;②控制和消除残余应力、装配应力和应力集中,防止应力腐蚀;③尽可能避免不同金属,特别是电势相差较大的金属互相接触,不可避免时需增加防护层;④采用排水设计,对不可避免的雨水渗入或冷凝水汇集,应有导流通道排除;⑤在机体其他便于检查的部位应适当地设置排水孔、放油孔等,确保机内腐蚀积液能顺利排出;⑥采用通风设计,全机结构应设置必要的舱门、口盖,以便通风排气;⑦在紧固连接中,可采用涂润滑油( 脂)或涂底漆,如安装螺栓、螺母及对铆钉墩头时,涂底漆等防腐蚀密封技术。
工艺
案例 2:某型飞机 1Cr17Ni2 不锈钢螺栓应力腐蚀失效某沿海机场使用的1Cr17Ni2 飞机卡箍螺栓发生断裂失效,磁粉检查发现更多的螺栓存在裂纹,裂纹位于 T 型卡箍螺栓光杆部位,呈周向分布。失效分析结果表明,卡箍螺栓失效性质为应力腐蚀,卡箍螺栓的回火处理是在脆性区进行的,这种回火工艺会导致表面脱碳致使材料耐蚀性下降,是螺栓发生应力腐蚀的主要原因。
案例 3:Cr13Mn9Ni4 不锈钢卡箍钢带应力腐蚀失效某型飞机用不锈钢卡箍钢带使用一段时间后表面出现大量的裂纹,钢带使用状态为冷硬态。失效分析结果表明,钢带裂纹性质为应力腐蚀裂纹。金相组织分析表明,2Cr13Mn9Ni4钢带在冷硬态状态下使用,具有明显的晶间腐蚀倾向,而该钢带经过重新固溶处理后晶间腐蚀倾向消失,说明该钢带选用了不合理的工艺状态(冷态)是导致其发生应力腐蚀的主要原因。
上述案例表明,在合理的防腐设计基础上,还需要对材料采用合理的防腐工艺措施,包括:①金属表面选择合适的涂镀层,通常选择在钢制零件上镀锌、镉,在铝制构件上进行表面氧化、化学镀镍,选择镀覆时应考虑零件与零件之间,镀层金属与基体金属之间的接触电偶;②在制造过程中,所采用的工艺应不损伤材料固有的耐腐蚀性能;③在满足设计强度的条件下选用耐蚀性好的热处理工艺;④通过对金属材料采用相应的表面强化技术,如喷丸强化、激光冲击强化、挤压强化等;⑤采用低温消应力退火;⑥合理地提高对构件表面粗糙度的要求。
选材
案例 4:БΦ-2 胶致 30CrMnSiNi2A结 构 钢 螺 栓 在 雨 水 环 境 中 断 裂30CrMnSiNi2A 结构钢螺栓在使用中多次断裂,失效分析结果表明,螺栓断裂性质为应力腐蚀,主要原因是螺纹部位接触БΦ-2胶, 并有雨水环境。 试验表明,БΦ-2胶中除含有大量的酒精和水外,还含有游离酚(石碳酸)。这种游离酚对多种合金尤其是高强度钢具有腐蚀作用,说明选材不合理是导致螺栓发生应力腐蚀的主要原因。
同样由于选材问题,某型飞机 42框也发生过由于软油箱涂层浸泡液呈碱性,腐蚀作用较强,在其它多种因素联合作用下导致该型飞机 42 框发生严重的晶间腐蚀,飞机大面积停飞。材料的选择,需要根据其工作环境,包括外界环境和飞机局部环境进行选择。为满足防腐要求,飞机选材一般需注意:①在满足技术指标的前提下,尽可能选用耐蚀性好的材料;②承受高载荷的结构件,选用对应力腐蚀、腐蚀疲劳、氢脆等敏感性小的材料;③高强度结构钢在满足技术指标的前提下,尽可能使强度值处于技术条件的中下限,降低氢脆敏感性。
结语
舰载机在恶劣的腐蚀性海洋环境条件下长期工作,腐蚀问题十分突出。我国舰载机的应用时间较短,对于舰载机的腐蚀规律及其控制技术的掌握还不够深入和全面,需要全面调研、跟踪和研究舰载机在全寿命过程中的腐蚀失效模式及其形成机理,搞清舰载机全寿命期间不同阶段腐蚀失效规律及其演化机理,并不断地从防腐设计、工艺和材料选择等多方面深入摸索。在此基础上,形成舰载机腐蚀控制技术体系和标准体系,将腐蚀控制技术贯穿于舰载机的设计、制造、使用和维护的全过程。
(资料来源:知网)
02 航空表面涂层技术的研究进展
航空表面涂层技术是航空制造技术的重要组成部分之一。采取一定的表面工程手段在飞行器零部件表面制备具有特定防护或功能涂层,可以使零部件表面具有隔热、减摩可磨耗封严、耐磨防腐蚀、抗高温氧化、吸波隐身等功能。
目前,航空表面涂层技术发展最快也是最重要的涂层,包括热障涂层(TBCs)、超高温复合材料(C/C、C/SiC、SiC/SiC)部件表面环境障涂层(EBC)、高温可磨耗封严涂层、WC-Co 及氧化铝钛等耐磨涂层、吸波及红外隐身涂层等技术,涂层的应用大幅度提高了航空产品的性能、可靠性、经济性、服役寿命及战机的生存能力。涂层新材料、新技术的出现在推动表面工程科学发展的同时,也节约了资源、减少了有害物质排放,促进了环境友好型绿色制造、可持续发展战略的落实。
航空表面涂层技术的发展现状
航空表面涂层的成熟运用对欧美F-22、F-35、波音 787、空客 A380、A400M 等新型飞机的商业化起到了重大推动作用。热障涂层、高温可磨耗封严涂层的应用提高了发动机涡轮进口温度、工作效率,节省了燃油。MCrAlY、PtAl 等高温抗氧化涂层的成熟应用提高了发动机高温部件服役寿命,降低了维护成本。飞机起落架超音速火焰喷涂WC-Co-Cr 涂层代替传统硬铬电镀层,大幅度提高了起落架耐磨性能,寿命成倍延长。
热障涂层是发动机高温部件最重要的防护涂层之一,具有隔热功能,同时具备抗冲蚀、抗高温氧化、防熔盐腐蚀等功能,可大幅度提高燃烧室及涡轮高温部件耐久性、可靠性。
美国 NASA 有成熟的高温封严涂层可磨耗性能试验系统,开发的 MCrAlY基合金型高温可磨耗封严涂层可提高涡轮机匣的寿命。国内发动机高温部件用超高温热障涂层、高温抗氧化涂层技术及可磨耗封严涂层技术近年来得到了快速发展,取得了很多实验室成果,但与国外先进技术相比,仍有很大差距,主要是热障涂层、高温抗氧化涂层、高温可磨耗封严涂层可靠性、使用寿命不足。
近年来国内多家大学、科研院所及发动机主机厂开发了多种稀土锆酸盐及稀土铈酸盐类超高温热障涂层,微观上大多呈烧绿石结构或萤石结构,其导热系数明显低于 Y 2 O 3 -ZrO 2 传统热障涂层,但其关键技术指标——抗热冲击性能还有待提高。
虽然国内高温封严涂层早已实现工程化应用,但没有建立起高温封严涂层可磨耗性能及可靠性评价标准体系,而涂层发动机试车考核成本高昂,时间漫长、致使高温可磨耗封严涂层新材料及其涂层制备新工艺研究进展缓慢,涂层使用寿命仍然明显低于国外同类产品。
在飞机耐磨涂层方面,近年来最大的进展是飞机起落架广泛采用超音速火焰喷涂 WC-Co-Cr 涂层代替传统硬铬电镀层,耐磨性及使用寿命大幅增长,并消除了电镀污染。美国纳米集团(USNANOGROUP,INC.)开发的纳米碳化钴、纳米氧化铝钛涂层推广应用于航空轴类、环类部件,用于耐磨及篦齿封严,涂层具备高硬度、高韧性、高抗弯强度,其耐磨性能远超传统同类涂层,应用前景十分广阔。
航空表面涂层技术的新进展
超高温热障涂层
航 空 发 动 机 现 广 泛 采 用 的3.5 ~ 4.5mol%Y 2 O 3 部 分 稳 定 ZrO 2热障涂层的长期工作温度不能超过1200℃,否则在随后冷却过程中将发生四方相向单斜相相变,该过程中材料体积膨胀约 4%,使涂层开裂剥落失效。为进一步提高燃气涡轮发动机工作温度、延长相关高温部件热循环寿命,新型超高温热障涂层材料成为业界研究热点。由于氧化钇部分稳定氧化锆涂层在1200℃以下表现出优异的热学及力学性能,氧化钇稳定氧化锆理所当然成为研究和开发新型超高温热障涂层材料体系的基础。北京航空制造工程研究所开发的 Sc 2 O 3 、Gd 2 O 3 、Yb 2 O 3 三元稀土氧化物复合稳定 ZrO 2 及 Sc 2 O 3 、Y 2 O 3 二元稀土氧化物复合稳定 ZrO 2 热障涂层,工作温度可达 1500℃,为单一四方相结构,长期工作无相变,使热障涂层承温能力提高了 200℃,有望实现工程化 应 用。Sulzer Metco( 现 为 OerlikonMetco)开发的 Gd 2 O 3 、Yb 2 O 3 、Y 2 O 3 三元稀土氧化物复合稳定 ZrO 2 工作温度1500℃仍可保持相稳定,涂层热导率明显低于一般热障涂层。多元稀土氧化物复合掺杂 ZrO 2 是超高温热障涂层材料重要发展方向。
国 内 近 年 开 发 了 系 列 锆 酸 镧、铈酸镧或铈锆酸镧热障涂层材料,如 La 2 Ce 2 O 7 、La 2 Zr 2 O 7 、Sm 2 Zr 2 O 7 、La 2(Zr 0.7 Ce 0.3 ) 2 O 7 。为消除热收缩现象还研制了一些成分更为复杂的改性材料,如 La 1.8 W 0.2 Ce 2 O 7.6 、La 2 Zr 1.7 Ta 0.3 O 7.15 等,这些稀土锆酸盐类化合物大多数呈烧绿石结构、萤石结构或者缺陷萤石结构,其导热系数明显低于稀土氧化物稳定 ZrO 2 热障涂层材料,但抗热冲击性能还有待提高。如将这些锆酸盐类化合物与传统 3.5 ~ 4.5mol%Y 2 O 3 部分稳定的 ZrO 2 组成双陶瓷层结构热障涂层,则可发挥传统材料热膨胀系数大、断裂韧性高的优点,明显延长热障涂层热循环寿命,同时保留稀土锆酸盐类化合物不发生相变、抗烧结、热导率低、抗腐蚀的优点,这是未来发展使用温度超过1300℃的超高温热障涂层的重要途径之一。需要特别强调的是,不管是采用等离子喷涂(PS)还是电子束物理气相沉积(EBPVD)制备稀土锆酸盐类化合物热障涂层,涂层最终组成往往不同于粉末喂料或靶材,为保持制备的涂层组成符合设计的化学计量比例,粉末或靶材成分设计、沉积工艺过程精确控制十分重要,并将决定最终涂层性能及使用寿命,而使用寿命是其能否成功应用于航空产品的关键所在。
研究表明,CMAS 严重影响热障涂层耐久性及最高使用温度。CMAS 为CaO、MgO、Al 2 O 3 、S i O 2 等组成的硅酸盐类物质,CMAS 在约 1250℃熔化,它可熔解热障涂层材料,还会浸润热障涂层、通过毛细作用沿孔隙及柱状晶之间间隙渗入热障涂层内部,使热障涂层表面变粗糙、内部变疏松,并在发动机停车冷却循环过程中,CMAS 熔盐凝固成玻璃态物质,其贯穿层模量会上升,热障涂层应变容限将骤降,随后热循环中热障涂层将可能大范围剥落,大幅降低发动机涡轮叶片耐久性,甚至造成涡轮叶片烧蚀而出现灾难性后果。预防 CMAS 腐蚀的方法一般是在热障涂层表面制备一层与 CMAS 熔盐反应形成固态致密层的物质,资料报道含大直径稀土阳离子的萤石或烧绿石结构材料能与CMAS熔盐反应形成高熔点固态致密层,可有效阻止 CMAS 进一步贯穿侵蚀。
高温复合材料表面环境障涂层
C/C 复合材料在高温条件下存在严重的氧化和烧蚀问题,C/SiC、SiC/SiC 陶瓷复合材料部件在高温水蒸气环境下存在性能退化及易受 CMAS 熔盐侵蚀问题。环境障涂层(EBC)是为提高C/C、C/SiC、SiC/SiC 高温复合材料部件环境稳定性的表面防护涂层。EBC 为多层结构,如 C/SiC 复合材料基体表面制备 Si+ 莫来石 +BSAS 复合 EBC。
EBC 顶层材料至关重要,一般采用 BaO-SrOAl 2 O 3 -SiO 2 材料(BSAS)。但 BSAS在 1300℃以上环境工作仍然存在化学稳定性问题,BSAS 会与 S i O 2 反应生成一种低熔点玻璃相(熔点低于 1300℃),导致 EBC 在工作温度超过 1300℃时过早剥落失效,这就限制了其在更高温度下的使用。
NASA Glenn 研究中心研究表明,一 些 稀 土 硅 酸 盐 Re 2 Si 2 O 7 (Re 为 Sc、Lu、Yb、Tm、Er 及 Dy 等)有良好的高温化学稳定性,1500℃长期无相变,在 1400℃与莫来石化学相容性好,其在 1500℃下抗水蒸气腐蚀能力优于BSAS。 但稀土硅酸盐作为EBC面层材料,与莫来石热膨胀系数匹配不如 BSAS,易在热循环过程中产生裂纹,而影响涂层可靠性和防护性。现也有在 BSAS 涂层上再沉积稀土硅酸盐Yb 2 SiO 5 涂层的,Yb 2 SiO 5 涂层可提升 EBC 抗 CMAS 侵蚀能力。总之,稀土硅酸盐作为 EBC 涂层组成材料应用研究还不够成熟,但具有作为新一代 EBC 面层材料的应用开发潜力,值得深入研究。
高温可磨耗封严涂层
高温可磨耗封严涂层用于发动机涡轮气路密封,可减小涡轮叶片叶尖与涡轮外环之间的间隙,进而减少气体泄漏、提高发动机效率。一般设计要求在涡轮叶片与封严涂层发生接触刮擦时涂层被刮削而叶片磨损甚小,并且摩擦系数要小,以免刮擦产生的高温造成涂层或叶片烧蚀开裂,因此高温可磨耗封严涂层需具有一定的减摩功能。一般来说,金属基可磨耗封严涂层抗气流冲蚀性能优良,而氧化物陶瓷基可磨耗封严涂层抗气流冲蚀能力相对较差,因此在材料组成及涂层制备工艺参数控制方面必须予以高度关注,以保证涂层使用寿命。近年来,等离子喷涂 MCrAlY 高温合金型(如 NiCrAlY、CoCrAlY、NiCrAlYSi 等)可磨耗封严涂层及陶瓷基(如稀土氧化物稳定 ZrO 2 、Al 2 O 3 等)可磨耗封严涂层获得了明显进展,涂层可磨耗性能和抗冲蚀性能明显提高。MCrAlY 具有高温抗氧化和抗热腐蚀作用,一般添加聚苯酯作为造孔剂,聚苯酯加热去除后在涂层内留下大量细小均匀分布的孔隙可以降低涂层硬度、增强涂层可磨耗性、减轻涂层对涡轮叶片的磨损。添加六方 BN或氟化物作为减摩自润滑材料,降低摩擦系数。高温可磨耗封严涂层厚度一般超过 1.5mm,必须采用机器人自动喷涂技术,喷涂参数计算机闭环控制、涂层厚度在线监测,这样才能保证涂层组织结构及厚度均匀性及再现性。采用纤维增强涂层技术可明显提高封严涂层热循环寿命。
Oerlikon Metco 研制的 Dy 2 O 3 -ZrO 2 -hBN- 聚苯酯高温可磨耗封严涂层用于航空发动机高压涡轮气路封严工作温度可达 1200℃,工作寿命比普通 Y 2 O 3 -ZrO 2 -hBN- 聚苯酯高温封严涂层提高 4倍以上。对于 SiC/SiC 陶瓷复合材料(CMC)涡轮部件,在 EBC 的基础上制 备 多 孔 Yb 2 Si 2 O 7 及 Yb 2 O 3 、Sm 2 O 3 或Gd 2 O 3 等掺杂ZrO 2 涂层作为可磨耗涂层,目前取得了积极进展。热喷涂陶瓷涂层代替硬铬电镀层技术因电镀硬铬对环境有持久的危险性,电镀废液中的六价铬更是严重危害人体健康,减少直至取消电镀硬铬工艺意义重大。近年来超音速火焰喷涂(HVOF、HVAF)WC-Co、WC-Co-Cr、Cr 3 C 2 -NiCr 金属陶瓷涂层、等离子喷涂 Cr 2 O 3 及 A1 2 O 3 -TiO 2 氧化物陶瓷涂层在工业上获得广泛应用,全面取代电镀硬铬工艺已是必然。HVOF 喷涂 WC-Co-Cr 涂层在空客、波音、洛克希德·马丁等生产的先进军民用飞机(包括空客 A380、波音 787、F-35 等)已成功应用,结果表明 HVOF 喷涂的 WC-Co-Cr 涂层在耐磨、防腐蚀、抗疲劳等关键性能指标明显优于传统硬铬电镀层。
Cr 3 C 2 -NiCr 涂层广泛用于高温摩擦磨损环境,涡轮导向器篦齿封严采用 HVOF喷涂 Cr 3 C 2 -NiCr 硬质涂层(主动磨削涂层)或等离子喷涂 A1 2 O 3 -TiO 2 陶瓷硬质涂层,具有耐蚀、高温抗氧化、耐磨损等能力。等离子喷涂 Cr 2 O 3 陶瓷硬质涂层在发动机动密封及飞机运转部件磨损防护方面应用广泛,其耐磨性及防腐蚀性比传统硬铬电镀层提高数倍。
纳米涂层
纳米材料技术是 20 世纪 80 年代诞生并仍快速发展的新技术,受到世界各国高度重视。PVD(物理气相沉积)、热喷涂、 CVD (化学气相沉积) 、 MBE (分子束外延)、化学沉积、电沉积等方法是获得纳米涂层或薄膜的典型方法。近10 年来研究人员利用 PVD(包括磁控溅射、离子束溅射、射频放电离子镀、等离子体离子镀、EB-PVD 等)在制备纳米单层膜及纳米多层膜方面取得很多成果,如纳米 Ti(N,C,CN)、(V,Al, Ti、 Nb、 Cr) N、 SiC、 β-C 3 N 4 、 α-Si 3 N 4 、TiN/CrN、TiN/AlN、WC-Co 薄 膜 或 涂层可用于飞机轴类零件耐磨防腐,等离子喷涂纳米 A1 2 O3-TiO 2 涂层已用于航空发动机气路封严,纳米 Y 2 O 3 -ZrO 2 涂层已用于涡轮叶片隔热防护,添加石墨烯、碳纳米管复合涂层具有雷达隐身功能。总之,近年来在基础研究和应用开发方面纳米涂层已取得巨大进展,有的已在航空、舰船等产品的防腐、耐磨、隔热、吸波隐身、防海洋生物附着、自清洁等功能涂层上获得应用。
热喷涂是制作纳米涂层的极有竞争力的方法之一,与其他技术相比,具有许多优越性,如工艺简单、涂层材料和基体选择范围广、可制备厚涂层、沉积速率高、涂层成分易控制、容易形成复合功能涂层等,适用于大型零部件。采用纳米团聚粉末作为热喷涂喂料,通过严格控制工艺参数,缩短纳米材料在焰流中的停留时间、限制原子扩散和晶粒长大,可制备纳米涂层。美国纳米集团英佛曼公司(Inframat Co.)开发的等离子喷涂纳米 A1 2 O 3 -TiO 2 复合涂层与传统 A1 2 O 3 -TiO2 涂层相比,耐磨损能力提高 5 倍、抗疲劳能力提高 10 倍、弯曲 180°无裂痕(传统 A1 2 O 3 -TiO 2 涂层弯曲 180°后开裂剥落)、涂层附着力提高 4 倍,纳米涂层表现出极其优异的性能。
表面涂层设备重要进展
冷气动力喷涂
冷气动力喷涂,简称冷喷涂,根据不同喷涂材料及零件基体,冷喷涂中工作气体可为 N 2 或 He,工作气体 1 将固态粒子加速至 300 ~ 1200m/s,与零件基体碰撞发生剧烈的塑性变形而沉积形成涂层,粒子沉积主要靠其动能来实现。冷喷涂可有效避免喷涂粉末材料的氧化、分解、相变、晶粒长大,对基体几乎没有热影响,可用来喷涂对温度敏感的易氧化材料、纳米材料。需特别注意的是冷喷涂对喷涂粉末材料粒度、形态及纯度(如含氧量)要求十分严格,国际上只有少数几家粉末材料供应商可提供冷喷涂粉末货架产品,且价格昂贵。
冷喷涂制备 Al、Cu、Cu 合金、Ti、Ta、TiAl、 FeAl、 AlNi、 Ni合金等涂层非常成功,通过真空扩散热处理可实现冷喷涂涂层与零件基体间冶金结合,结合强度可达200MPa 以上。
超低压等离子喷涂
超低压等离子喷涂(PlasmaSpray-Physical Vapor Deposition,PSPVD),是在低压等离子体喷涂(LowPressurePlasma Spray,LPPS,喷涂时压力为几千帕)基础上,进一步降低真空室的工作压力至几百帕甚至 100Pa 以下,同时大幅度提高等离子喷枪功率,将粉末加热熔化、并有部分气化,在等离子射流中同时存在气液两相,沉积形成涂层的过程。通过粉末颗粒加热状态控制可获得气相沉积与颗粒沉积的混合组织,既可制备薄膜,也可制备厚度数百 μm 的涂层。制备的 MCrAlY 涂层孔隙率低,结合强度可达 80MPa 以上,通过扩散处理可进一步提高结合强度。制备的 YSZ 陶瓷涂层呈现类似 EBPVD 的柱状晶结构。
溶液等离子喷涂
溶液等离子喷涂根据液体喂料不同,分为前驱体溶液等离子喷涂(SolutionPrecursor Plasma Spray,SPPS)和微纳米颗粒悬浮液等离子喷涂(Suspension PlasmaSpray,SPS),将液体喂料直接送入等离子焰流在零件表面沉积形成涂层。采用前驱体化合物液体直接喷涂制备纳米结构热障涂层,简化传统纳米氧化锆粉末喷涂涂层制备的复杂工序,可降低材料损耗和工艺过程成本。并且溶液等离子喷涂制备纳米结构热障涂层能有效避免纳米晶粒长大,涂层孔隙细小、分布均匀。美国英佛曼公司采用前驱体化合物液体喂料,采用大气等离子喷涂设备成功制造带垂直裂纹结构的纳米热障涂层,其热冲击寿命超过 EB-PVD 工艺制备的热障涂层,比传统粉末等离子喷涂工艺制备的热障涂层寿命提高 1 倍以上。
结语
表面涂层技术是制造技术重要组成部分,以个人技术经验为主的传统表面涂层技术已不能满足现代航空工业发展需要。现需抓紧建立大型表面涂层应用数据库,以大数据技术、传感技术、计算机自动控制技术、机器人技术、网络技术为基础,根据零部件外形与功能、服役环境与使用寿命需求,实现涂层材料与涂层结构设计、涂层制备加工方法选择与工艺实施、涂层质量检测与评价等整个涂层制备过程自动化、智能化,促进航空表面涂层技术又好又快的发展。(本篇资料来源:航空制造技术)
03 波音飞机腐蚀防护要点分析
波音飞机由于长时间使用,腐蚀现象会日益严重。因此,机务工作者的重要任务之一是对机体结构腐蚀防护。腐蚀的预防工作不但是对波音飞机采取技术手段防治腐蚀,而且与飞机制造厂密切相关。因此,飞机制造厂也应当做好飞机腐蚀防护。一方面,波音飞机腐蚀发展带来飞行安全问题,不利于乘客安全。另一方面,腐蚀会提升波音飞机维护成本,造成资金浪费。下面从波音飞机腐蚀防护的几大要点进行解读。
波音飞机腐蚀原因分析
潮湿的空气
潮湿的空气是造成波音飞机腐蚀的主要原因。一般来讲,潮湿空气和地理环境具有十分密切的联系。我国的地理环境非常复杂,并且受到季风影响明显。
一般来讲,我国大部分地区处于潮湿东南季风以及西南季风控制下。因此,东南、西南地区降水量以及湿度比较大,从而造成这些地区机场的波音飞机的腐蚀问题严重。
海洋大气腐蚀
海洋大气的主要特点是含盐量高以及湿度相对较高。海水中含有大量氯离子,氯离子通过海洋大气接触波音飞机,从而引起波音飞机腐蚀,海洋大气中的氯离子对飞机具有很强的腐蚀作用。
工业大气腐蚀
由于工业发展,工业排风气体中含有腐蚀性气体。腐蚀性对金属具有很强腐蚀作用。例如工业大气中的二氧化硫气体,一般来讲,二氧化硫在大气中含量超过百分之一,就能明显腐蚀金属,因此,工业大气能够造成对波音飞机的腐蚀。
飞机内部腐蚀
主要包括两点:首先,乘客在乘坐飞机过程中会排出水分,其次,湿度较大时候,波音飞机处于水分饱和状态。
因此,当波音飞机上升,飞机内部温度下降,从而造成水分凝结,由于水分大量存在,促使波音飞机结构部件等腐蚀。
此外,厕所污水流入飞机结构之上或者厨房饮料等留在飞机结构上,同样引起波音飞机结构性的腐蚀。
波音飞机腐蚀防护要点
对机务人员防护要点
作为机务人员,波音飞机腐蚀防护要点主要包括以下几点:
第一,腐蚀防护培训。应当加强对相关波音工作人员的培训以及教育,促使每个工作人员重视波音飞机腐蚀防护工作,自觉做好飞机防腐工作。只有全体工作人员对波音飞机腐蚀防护工作负起责任心,才能保障波音飞机腐蚀防护工作顺利开展。
第二,保障排水系统通畅波音飞机工作人员应当经常性检查飞机内部的排水管道,从而保障排水系统通畅。此外,波音飞机的货舱以及客舱等区域应当经常通风,从而保障飞机内部水分排出。
第三,定期清洁污染区域飞机工作人员应当经常性清洁飞机污染区域,对于电解质污染区一级强腐蚀介质区域应当喷涂防腐剂。
第四,确保地板密封性。相关工作人员应当时常检查厕所厨房的地板十分密封,如果没有密封或者损坏,应当采取有效措施修复地板。
第五,加强装卸管理。波音飞机装卸货物过程中,应当注意避免装卸货物造成飞机地板损坏或者腐蚀性物质进入地板,避免飞机结构性腐蚀。
第六,防止微生物滋生飞机相关人员应当防止飞机油箱的微生物蔓延,确保油箱排水通畅,飞机油箱内应当定期加入杀虫剂,从而减少细菌滋生。
第七,严格防腐工艺应当严格防腐工艺。确保飞机质量,避免飞机腐蚀。
针对飞机设计防护要点
针对波音飞机结构方案设计而言,应当根据飞机使用环境以及功能要求制定从而进行波音飞机防止腐蚀工作,一般来讲,主要做到以下几点:
第一,针对波音飞机进行合理地结构设计。第二,波音飞机设计中,应当选用耐腐蚀的材料,不合格的材料应当杜绝使用。第三,建立合理的防护体系,对飞机防腐蚀设计层层把关。第四,设计中,应当对波音飞机上异种金属零件腐蚀加强控制。第五,波音飞机表面设计,应当确定强化型的飞机表面,从而减少腐蚀。第六,采用密封剂进行波音飞机的防腐密封设计。 第七波音飞机的设计图纸应当明确防腐蚀要求。制造部门对飞机图纸进行性严格的审查,包括飞机的外部构建以及结构零件等的审查。设计图纸中,明确防腐蚀的要点区域,从而方便相关工作人员日常维护。
有机防护涂层防护要点
首先,外部油漆以及颜色应当符合飞机热稳定设计具体要求。此外,根据飞机的零件材料、部位、环境条件要求选择优秀有机涂层, 不但底漆以及面漆相互配套,而且底漆与密封胶相互配套,暴露外部环境内表面视为外表面。
经常处腐蚀环境的内表面视为外表面进行涂层。最后,确保各零件防护性能前提下,应对各零件涂层厚度进行严格的控制。
表面强化处理防护要点
波音飞机的超高强度钢以及超高强度的铝合金加工锻炼过程中,应当按照飞机制造相关标准进行喷丸处理,此外,喷丸处理后,波音飞机的零件不能进行其他机械加工或者校形。如果一定要对已经喷丸处理的飞机表面进行加工或者校形,应当根据加工量严格按照相关规定实施操作。
结构防腐设计改机
结构防腐设计改机主要是根据飞机的不同以及不同材料,从而采取不同的防护方法,制定科学的防腐蚀方法。首先,应力腐蚀。就是不改变波音飞机的接头材料,消除接头装备应力,并且减少孔轴之间的干涉量,增加飞机防护涂层从而防止应力腐蚀。其次,电偶腐蚀。
主要是在相对较湿的腐蚀环境下。将飞机金属部分与腐蚀介质进行隔离处理,从而消除腐蚀介质,防止波音飞机电偶腐蚀现象的发生。最后,缝隙腐蚀。波音飞机缝隙腐蚀应当清楚缝隙之内的腐蚀产物以及封堵缝隙的方法阻止缝隙之处形成腐蚀。此外,均匀腐蚀。波音飞机的前墙腹板以及油箱壁板等部分容易出现均匀腐蚀现象。应当在涂上防护底漆。针对油箱壁板腐蚀现象,在喷涂底漆之后,应当再喷涂一层面漆以及喷涂一层多功能的密封胶,从而保障均匀腐蚀问题能够得到彻底解决。提高波音飞机质量应当从以上几个方面采取有效措施,增加飞机安全性以及稳定性。
控制腐蚀等级
一级腐蚀
所谓一级腐蚀,是腐蚀属于局部性的。腐蚀程度较为轻微,然而,根据实践表明,主要是轻微腐蚀,以后会演变为大面积的腐蚀。因此,应当在发现轻微腐蚀后,采取相关措施清除腐蚀区域,保障波音飞机质量。
二级腐蚀
二级腐蚀是腐蚀面积较大,属于大面积腐蚀,采取一般手段修复或者清除损伤依旧超出相关标准的极限,应当采取相关措施补救,从而保障波音飞机的健康与安全。
三级腐蚀
三级腐蚀对于飞机飞行影响比较严重,是关键结构件出的腐蚀。三级腐蚀是程度最高的腐蚀,直接影响飞机性能以及安全性。腐蚀面积大并且集中在关键部件位置。应当立即采取相关措施进行补救。
结语
波音飞机腐蚀防护工作对于飞机的安全性以及延长寿命具有重要意义。相关工作人员应当加大力度进行波音飞机腐蚀防护工作。认真总结腐蚀原因以及控制腐蚀等级,做好波音飞机维护保养工作,保障飞机以及乘客安全,从而促使波音飞机向高可靠性、高安全性方向发展。
04 国际新型高速飞行器热防护涂层前沿技术
新型高速飞行器(如可重复使用天地往返运输系统、飞船返回舱、近空间高超声速飞行器等)在穿越或飞行于大气层过程中表面受到强气动加热的作用,温度可达 1327 ~ 2727℃甚至更高,因此对飞行器表面热防护系统提出异常苛刻的要求,同时高速飞行器表面不同部位在往返过程中将承受不同的热腐蚀环境, 其表面须采用不同功能的热防护材料。 其鼻锥、前缘、垂尾等部位采用的是高温 / 超高温防热材料,而飞行器表面其它部位则主要采用可重复使用的非烧蚀防隔热材料,外加热防护涂层。于是,热防护涂层成为了防隔热材料能否成功运用于飞行器外部防隔热的关键环节,它解决了防隔热材料在高温环境下的抗冲蚀、抗热裂、辐射和抗氧化等瓶颈问题。
新型高速飞行器
高速飞行器表面热防护研究进展
非烧蚀防隔热层可分为刚性隔热瓦和柔性隔热毡。刚性隔热瓦表面经历了 RCG、TUFI、HETC 为代表的3代涂层发展历程,而柔性隔热毡表面热防护涂层也经历了 DC92、D-9、PCC 三代涂层的演变。在这些涂层的研发过程中,不断提高耐温性和辐射率成为了科研者一直追求的目标,通过不断的创新和努力,新一代涂层 HETC 的耐温性被提高到 1600℃以上,而辐射率被提高到 0.9 以上。
美国航天飞机挑战者号、X-34、X43A、X-51A 高速飞行器表面非烧蚀防隔热材料的应用分布情况如下图所示。
美国挑战者号、X-34高速飞行器表面热防护材料应用
刚性隔热瓦是高速飞行器迎风面主要采用的热防护材料,经过多年研制,刚性隔热瓦由一元朝多元材料体系发展,通过结构上的组合成功实现了多元体系两元结构的防隔热一体化设计, 其典型代表有:LI (Lock heed insulation) 、 FRCI (Fibrousrefractory composite insulation)、AETB(Alumina enhancedthermal barrier)、BRI(Boeing reusable insulation)几代陶瓷纤维隔热瓦以及新型防隔热一体化材 TUFROC(Toughened uni-piece fibrous reinforced oxidization-resistant composite)。
刚性隔热瓦表面热防护涂层也分别经历了:RCG(Reactioncured glass)、TUFI(Tougheneduni-piece fibrous)、HETC(Highefficency tantalum based ceramic composite structures)三代涂层的升级改进。
柔性隔热毡是高速飞行器背风面主要使用的热防护材 料, 典 型 代 表 有:FRSI(Flexible reusable surface)、AFRSI(Advanced flexible reusable surface)、LHB(Lowheatblanket)、HHB(High heat blanket)、TABI(Tailorableadvanced blanket insulation)、CFBI(Composite flexible blanketinsulation)、CRI(conformal reusable insulation)、OFI(Opacifledfibrous insulation) 。
柔性隔热毡表面热防护涂层也主要经历了:DC92、D-9、PCC (Protective ceramic coating)三代涂层的升级改进。
刚性隔热瓦热防护涂层
双层梯度涂层
最早由美国宇航局 James.C Fletcher 提出,该涂层由阻挡内层和辐射玻璃外层组成,内层为 SiO 2 ,其作用是将辐射玻璃层和基体材料分开,防止二者可能发生的反应,另外它也可以很好地匹配基底材料的热膨胀系数,使整体材料具有很好的抗热震性。其外层由难溶辐射剂(SiC、CrO 2 CoO 2 NiO 2Si 3 N 4 CrO 2 等其中一种或几种) 、 高硅玻璃和硼硅酸盐玻璃组成,使涂层拥有高硬度、极高的辐射率以及抗热震裂纹性能。
固化玻璃涂层RCG
该涂层是美国航天飞机刚性陶瓷瓦上首次得到使用的高辐射率涂层,它成功地被运用在 LI-2200、LI-900 等第一代陶瓷隔热瓦上。RCG 采用 SiB 4 作为辐射剂,以特别制备的高硅玻璃粉和硼硅酸盐玻璃粉为粘结剂。最终使涂层具有低的热膨胀系数、高的力学强度和高的辐射率等优异性能,具有较高的抗热冲击强度和表面硬度,其高温下的流动性可以很好地使涂层达到高温自愈合的作用,且可在 1480℃高温下成功实现抗氧化。
增韧单层纤维隔热涂层TUFI
TUFI 涂层被成功运用到 FRCI、AETB、BRI 为代表的陶瓷隔热瓦上。以高温结构材料 MoSi 2 作为辐射剂,以硼硅酸盐玻璃作为粘结剂,以 SiB 6 作为烧结助剂,使涂层具有高的熔点、极好的高温抗氧化性。
高性能钼基涂层
主要由 MoSi 2 和 MoB 2 组成,可以在低温下流动,且可以起到抗氧化作用。钼基涂层的熔点在 1949℃左右,软化点在1593~1649℃, 这说明钼基涂层具有比硅基涂层更好的耐温性,同时钼基涂层拥有高的辐射率、良好的抗冲击性和抗氧化性。
难熔金属相超高温热防护涂层
该涂层由硼硅酸盐玻璃作为内层,硅酸盐玻璃(如 SiC、HfC 等)作为外保护层,再添加一定量的难熔金属相(如 Ti、Hf、Zr、Mo、Ni、Ta 等及其硅化物,氧化物,硼化物或碳化物等)。掺杂难熔金属相复合材料可以在 1650℃下很好地保护基底材料, 起到很好地抵抗腐蚀、潮湿、高温热载荷等作用。
防隔热一体化梯度涂层TUFROC
2010 年美国成功发射并返回的 X-37B 临近空间飞行器的翼前缘、垂尾等部位首次使用了整体增韧抗氧化复合结构材料TUFROC。其双层结构的内层采用低热导率的 AETB 或 FRCI,其表面涂覆了 TUFI 涂层,而外层则采用耐高温的 ROCCI 材料。
内层作为过渡层可缓和涂层和基底的热膨胀不匹配,外层起到高辐射抗氧化抗冲刷作用。ROCCI 表面涂覆了高效钽基陶瓷复合涂层 HETC,中间过渡区域采用成分为 TaSi 2 、MoSi 2 、WSi 2等高辐射剂和含醇盐的有机硅组成的高效粘结剂,这种设计将隔热和防热问题耦合起来研究,真正实现了防隔热一体化的梯度设计理念。
柔性隔热毡表面热防护涂层
柔性隔热毡主要有 FRSI、AFRSI、LHB、HHB、TABI、CFBI、CRI、OFI,被广泛运用在飞行器机身表面大部分面积,如上翼、尾翼侧面, 升降舵辅助翼, 刹车装置中, 如美国OV-099航天飞机。
美国OV-099航天飞机柔性隔热毡表面涂层应用
其发展历程包括:
DC92型热防护涂层
该涂层由 50% ~ 55% 的胶态硅溶胶和 45% ~ 50% 的石英陶瓷颗粒组成。其中石英陶瓷颗粒作为增强相,胶态硅溶胶作为粘结剂,另外为了判断涂层涂覆情况, SiB4 作颜料剂,通过气相沉积混合气体方式制备疏水涂层表面,可运用到柔性隔热毡 FRSI 刚性隔热瓦 LI-900 和 FRCI 上。
D-9型热防护涂层
该涂层由胶态的硅溶胶和不定形的 SiC 或 SiB6 组成,以异丙醇为溶剂,它具有低的热膨胀系数,耐高温性和抗热震性能相比 DC92 提高。
PCC型热防护陶瓷涂层
该涂层以氧化硅粉末和胶态的硅溶胶为混合物,以六硼化硅、四硼化硅、碳化硅、二硅化钼、二硅化钨、氧化锆中的一种或几种为辐射剂。高比表面积凝胶粒子与大尺寸 SiO 2 和硼化硅粘附在一起形成一个整体,使涂层粘度和热稳定性相对于 RCG、C-9 增加,六硼化硅在加热过程中在硼硅酸盐玻璃表面慢慢发生氧化形成表面薄膜,阻止涂层表面的挥发和进一步氧化。PCC 不仅能耐受 1650℃高温条件,同时具有高辐射率、高粘性和高稳定性、低表面能等诸多优点。
结语
未来的热防护涂层的研究需改变以往涂层各功能单独分开设计的理念,需将涂层耐温性、抗氧化性、高辐射率、抗冲刷性等多种有益性能综合起来考虑,以实现多种功能一体化设计。
05 国内外海运及沿海发射期间航天产品的腐蚀风险与应对策略
继酒泉、西昌和太原发射场后,我国正在海南省文昌市建设第四个航天发射中心,即海南发射场。文昌纬度低、靠近赤道,在此发射航天器可最大限度地利用地球自转离心力提高火箭的运载能力(对于地球同步卫星)和延长卫星在轨寿命。此外,海南发射场将成为我国新一代大型运载火箭的主要发射基地,火箭尺寸的大小不受铁轨的限制,可以通过水路运至海南。因此,海南发射场是保障我国航天可持续发展战略的重要里程碑, 建成后, 将主要承担地球同步轨道卫星、大质量极轨卫星、大吨位空间站和深空探测卫星等航天器的发射任务。在具备上述优势的同时,海南发射场也给中国航天带来了一个陌生的课题,即航天器在海运、储存、综合测试和发射准备期间的腐蚀问题。
腐蚀风险分析
文昌是我国少有的严酷大气腐蚀性地区 , 在气候类型上属于热带季风岛屿型气候,具有高温、高湿、多雷暴、强降水、有热带气旋登陆和高盐雾等气候特点。该地区环境是典型的热带海洋大气环境:年平均气温 24.1℃;大气年平均相对湿度> 86%,远高于 GB/T 19292.1《金属和合金的腐蚀 大气腐蚀性分类》规定的最高湿度 τ5 等级;大气中的盐雾含量很高,氯离子的质量浓度在 0.01 ~ 0.05mg/m 3 之间,氯离子的沉降速率在 0.0006 ~ 0.0137mg/(cm 2 ·d)之间。而我国的酒泉、西昌和太原发射场都属于内陆发射场大气环境,大气的腐蚀性很弱,不存在像海南发射场那样严酷的腐蚀环境及潜在的腐蚀失效问题。(海南发射场与内陆发射场的大气环境和腐蚀等级见表 1。)
表1 海南发射场与内陆发射场的大气环境和腐蚀等级
沿海发射场热带海洋大气环境及其效应
1)高温与太阳辐射
热带海洋大气环境的高温环境会使电子设备的工作状态、工作点发生变化,技术性能指标下降,可靠性降低,工作寿命缩短;对运载火箭和航天器的推进剂储运、加注不利。强太阳辐射会使暴露在自然环境的设施和设备加速老化、变质,令表面涂层开裂、脱落,使某些塑料物质变形、破损,缩短其使用寿命。
2)空气湿度
当相对湿度大于 80% 时,易使绝缘材料受潮而导致产品电气绝缘性能下降,甚至漏电或短路;高湿对运载火箭推进系统、阀门等需要保持干燥部位不利;高湿促使霉菌孢子发芽生长,使金属及其他材料部件腐蚀,当湿度超过金属的临界腐蚀湿度时,腐蚀速度将成倍增长。总之,高湿环境对发射场、运载火箭、航天器的光学仪器、设备以及太阳电池的工作有较多不利影响。
3)风与热带气旋
地面大风使火箭发射前的地面载荷加大,对火箭地面测试和平稳、安全起飞不利;超过火箭设计载荷的地面风将导致火箭不能正常瞄准、点火发射;地面大风使发射场建筑物、构筑物载荷加大,对结构稳定、安全不利。热带气旋则由于其生成快、移动速度快、风速高、破坏力强,因而对发射场和运载火箭、航天器的影响和危害更大。
4)降水
火箭转运、发射时暴露在自然环境中,降水将导致系统绝缘下降、漏电甚至短路,影响火箭、航天器的正常测试、加注、发射。降水会直接接触发射场地面设施或室外设备,也可能进入发射场地面设施内部,对设施、设备的工作状态、性能产生影响。长时间或大量降水会使环境湿度上升,对发射场地面设备设施、运载火箭、航天器产生腐蚀,影响设备可靠性与工作寿命。
5)雷暴
发射场地面设备设施、运载火箭和航天器如直接受到电闪雷击,轻者会损坏,重者则严重损毁;加注推进剂后的火箭、航天器,以及推进剂生产、储存、运输、加注设备可能会因遭受雷击而起火爆炸,从而导致发射任务失败。雷击电磁脉冲和雷电感应会对处于其影响范围的火箭、航天器、测试发射设备产生影响,使某些电子仪器设备性能参数发生改变或失效, 甚至是绝缘击穿, 引燃或引爆外泄可燃推进剂、 气体等。
6)海潮与海浪
海潮与海浪在与海风的综合作用下, 会使沿海区域盐雾浓度大大增高,影响运载火箭、航天器海上运输安全,影响运输船在港口的停泊、进出和装卸载。此外,还会对近海、低海拔的发射场设施安全构成威胁。
7)盐雾
空气含盐(盐雾)后:一是产生导电性,会使长期处于盐雾作用区域的电子设备、仪器、电缆等。绝缘性能下降、工作可靠性降低,甚至导致漏电、短路; 二是具有腐蚀性,尤其对金属物质的腐蚀最为严重。盐雾对金属的腐蚀是以电化学方式进行的,腐蚀机理基于原电池腐蚀。盐雾腐蚀是热带海洋大气环境的重要特征。腐蚀的结果使地面设备、设施性能变差,可靠性降低,工作寿命缩短,维护成本增加。
NASA 肯尼迪航天中心的航天器腐蚀案例分析
对于海南发射场严酷的大气腐蚀环境是否会造成航天器的腐蚀,我国尚无实操经验,但发生在 NASA 肯尼迪航天中心(KFC)的航天器腐蚀案例或许可以带给我们一些启示:KFC位于美国东部佛罗里达州东海岸的梅里特岛,濒临大西洋,靠近赤道,是美国地球同步轨道卫星、 航天飞机、“阿波罗”
飞船、“天空实验室”及各类行星际探测器的主要发射场。
无论是地理位置、气候条件还是发射任务,KFC 都与我国海南发射场极为相似。前期调研发现,KFC 的海洋大气环境给航天发射活动带来了严重的腐蚀问题。
1993 年,NASA 针对航天飞机轨道器的腐蚀问题专门成立了“轨道器项目腐蚀控制评估委员会”,对航天飞机轨道器在 12 年间的腐蚀历史进行了调查。调查发现:轨道器的腐蚀主要发生在发射任务期间航天飞机停留的运载装配间和发射台,在轨道器在发射台停留的近 1 个月时间,来自大西洋的高浓度盐雾、高湿的大气给轨道器造成了严重的腐蚀问题;轨道器的腐蚀区域共有 926 个,正式详细记录的腐蚀问题有26 个,包括与机械分系统相关的腐蚀问题 13 个,与主、次结构相关的腐蚀问题 13 个,其中 12 个是由发射场大气中的高浓度盐雾导致的。
肯尼迪航天中心
调研发现,海洋大气对 KFC 的航天器的腐蚀影响范围主要有:
1)结构与材料类。航天器的各类金属结构和材料;密封件和密封材料;绝缘材料;各种涂层和镀层等。
2)电子设备类。航天器的各类电子仪器、设备、电力与信号电线、电缆及连接器、接插件等。
3)光学设备类。航天器的光学敏感器、光学相机、光能电池等。
4)机械电气设备类。航天器的各类机械电气设备。
5)推进剂与火工品类。星上发动机火药启动器、电爆管、电爆阀。
海南发射场航天产品腐蚀风险分析
海南省文昌发射中心
海南发射场是我国少有的严酷大气腐蚀性地区,其大气腐蚀性显著高于我国酒泉、西昌和太原发射场,甚至高于KFC。从上面的腐蚀案例来看,虽然 NASA 在材料和工艺的选用和产品保证中有严格的腐蚀控制要求,但海运和沿海发射场带来的航天产品腐蚀问题仍时有发生;所以将来在海南发射场发射的航天器,在海上运输和发射场的储存、综合测试、发射准备期间,材料、元器件、零部件甚至组件发生腐蚀的风险是存在的。腐蚀的发生虽然不足以引起航天器结构强度的降低,但腐蚀对航天器的危害是巨大的,主要体现在:
1)腐蚀产物是一种隐性的多余物,且成分较为复杂,往往是金属、氧化物和盐的混合物。其中的金属多余物易导致航天器元器件(如电连接器、继电器等) 发生短路、 击穿、绝缘不良等致命失效;非金属多余物易则导致航天器元器件、零部件发生阻塞、触点不通或接触电阻过大等失效。
2)腐蚀会导致航天产品表面的光学、电、热控和磁性能等退化。
3)腐蚀危害具有延时性。虽然腐蚀主要发生在海运和发射场的储存、综合测试、发射准备等地面阶段,但腐蚀的危害性会延伸至航天器的在轨运行阶段。
此外,我国现行的航天器包装技术要求主要适用于以往内陆发射场的公路、铁路、飞机运输及测试、发射过程,包装箱、星(船)衣是否能够满足海运和文昌发射中心高腐蚀性大气的防护需求是未知的。
国外应对腐蚀风险的策略
为避免和降低海运和沿海发射场海洋大气环境对航天产品的腐蚀风险,NASA 和 ESA 制定了多项应对措施,主要包括:
1) 颁布各类技术标准, 针对航天器的设备、 组件、 元器件、材料和工艺推行以盐雾和湿热试验为主的环境适应性评价和保证工作NASA/TP-1999-209263《Multilayer Insulation MaterialGuidelines》 (多层隔热材料指南) 指出 : 多数发射场都建在沿海,虽然多数航天器在运至发射塔和安装至运载火箭的过程中都是在净室或环境密封舱内操作,并且在发射塔期间还处于有恒温恒湿空调保障的隔离间内,但盐雾等海洋性大气依然能够通过空调与航天器接触,因此,在多层隔热材料的设计中,要考虑材料在盐雾等海洋大气环境下的腐蚀问题,进行有关盐雾试验评价。盐雾试验要求按照美国材料与试验学会标准ASTM B117《Standard practice for operating salt spray(fog)apparatus》(盐雾试验设备标准操作规程)的规定进行。
2)航天器与沿海运输、装卸的兼容性设计与防护在 NASA 航天器设计准则 SP-8000《NASA Space VehicleDesign Criteria SP-8000》系列中,NASA SP-8104《StructuralInteraction with Transpor- tation and Handling Systems》(结构与运输和装卸系统间的相互作用)介绍了航天器结构与运输、装卸系统间的兼容性设计准则与防护策略。值得注意的是,其中与环境的兼容性设计和防护同海运中的海洋气候环境相关。下面将介绍 NASA SP-8104 中航天器与运输环境的兼容性设计的相关内容。
①航天器与运输、 装卸环境兼容性设计的必要性。 在运输、装卸过程中,包括暂时性储存中,航天器将一定程度地暴露于自然环境中,由此给航天器结构带来一些潜在的有害影响。因此, 需要通过运输和装卸系统, 或者适当的航天器结构设计,对航天器结构施加保护来避免这些有害影响。一种确定航天器在运输和装卸过程中关键性环境因素的方法是使用物流流程图。物流流程图能够详细说明运输和装卸过程中的各个阶段及与之相关的自然环境,并最终确定环境的严酷性、作用频率和各环境因素间的组合。
②兼容性设计中需要考虑的自然环境及其效应。下表给出了航天器在运输过程中最经常暴露于其中的环境及其主要的破坏作用。其他的自然环境(包括太阳辐射、臭氧、沙 / 尘、电磁和粒子辐射、闪电和静电放电等)并不是运输和装卸过程中航天器结构的主要危害。
3)航天器与运输、装卸系统间兼容性设计的建议措施要识别并量化航天器在运输、装卸包括暂时储存过程中遇到的自然环境因素,就要判断这些环境因素的量值是否超过了航天器对这些环境的抗力进而决定是否需要控制或完全消除这些环境因素对航天器的影响。根据需要,这些自然环境因素及其控制方法可单独或整体考虑。下表列出了通常需要考虑的自然环境因素及建议的防护措施。这些自然环境因素来自于沿海发射场和一些与发射场连接的船运水路。
结论及建议
海南发射场地处我国少有的严酷大气腐蚀性地区,未来在此发射的航天器在海运和发射场期间存在腐蚀风险。为降低、防范这些腐蚀风险,提出以下建议:
1)提高航天产品的表面处理工艺水平,提升海运和海南发射场期间产品的抗腐蚀能力。
2)加强航天产品的腐蚀控制管理。在相关原材料、元器件、 零部件和工艺的选用中以及批次产品的复验中,将抗盐雾、 湿热等耐腐蚀性能作为主要的验收技术要求。
3)积极开展航天器关键材料、元器件、零部件在海南气候环境下的环境适应性评价研究,逐步完善、健全我国关于航天产品腐蚀控制的技术要求、选用准则和技术标准体系。
4)对现在使用的航天器用包装箱、星(船)衣能否满足航天器在海洋运输及海南发射场期间高腐蚀性大气的防护需求,进行试验验证。
5)识别并量化航天器在海运及海南发射场期间的自然环境, 评价这些环境的量值是否超过了航天器的抗力,进而决定是否需要控制或完全消除这些环境对航天器的影响。(资料来源:知网)
免责声明:本网站所转载的文字、图片与视频资料版权归原创作者所有,如果涉及侵权,请第一时间联系本网删除。
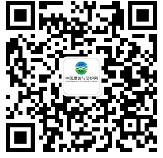
官方微信
《腐蚀与防护网电子期刊》征订启事
- 投稿联系:编辑部
- 电话:010-62316606-806
- 邮箱:fsfhzy666@163.com
- 腐蚀与防护网官方QQ群:140808414