为了达成美军的长远战略目标,在新型耐蚀轻质材料的使用和研发上,美军制定了明确的短期、中期和长期目标。并制订了明确的技术要求和规范。
文/ 知止 编译
现代战争是信息比拼、材料比拼的战争。快速、精准、低伤亡是现代战争的特征。虽然在战争中,空军和海军的作用越来越大,但最终还要靠地面部队来结束战争,维护战争成果。在这之中,对军事车辆的性能提出了更高要求。本文编译自多个国外相关资料,特别以美军新材料在军事车辆上的应用策略以及构思为主,供国内同行参考。
美军现役保持着大约25万辆轻型、中型和重型卡车,以及11万辆拖车,这些车辆维系着美军的整个物流系统。随着战争模式的改变,这些车辆的性能必须满足美军未来的作战构想以及战略目标,满足特定的军事需求。这些需求包括快速部署, 运输和机动性。这就要求美军车辆要具备更低的能耗,消减车辆自重,更高的耐蚀性能,提升免维护性能。
增加燃料效能就需要采用更轻质的材料,而不是传统的钢铁。一般情况下(非战时),每加仑燃料的运输成本是13美元,但是在战区,由于没有建立起输油管线、道路或其他基础设施,每加仑燃料的输送成本高达100至400美元。这意味着,如果降低军事车辆的能耗,可以大幅图降低战争成本,增加战争的胜率,更高效地保障后勤补给。换句话说,军事车辆对能耗的要求比民用车辆的要求更加严格和关键,从而消减车辆自重成为一个重要课题。
新型轻质材料主要考虑在车辆的以下的几个主要方面进行应用:首先,是汽车发动机、传动机构、悬挂系统已经承重车身;其次是那些结构化的部件,用于运输人员或货物的拖车等。美军的研究人员试图通过更加结构化的设计来保障车辆部件使用的通用性,以消减维护成本和需要运输的备件数量。
为了达成美军的长远战略目标,在新型耐蚀轻质材料的使用和研发上,美军制定了明确的短期、中期和长期目标。并制订了明确的技术要求和规范。
当然,新型材料在军事车辆上的使用,将面临一系列问题需要认真对待:车辆的组装、维护和报废,都会与传统的钢结构车辆不同。组装新型结构的军事车辆或者对既有车辆进行改装,需要确保在不同部件之间保障电绝缘性,而这些部件的制造材料是不同的。新型车辆的检查、维护和修理过程也比传统军事车辆复杂得多;而报废车辆的回收也面临着一些新挑战。
由于轻质材料的选择范围相对传统钢铁材料来得大,不同材质的车辆部件给车辆的维修、部件置换带来新问题,情况会比以前复杂得多。例如,复合材料现在已经在美军车辆中得到应用,其维修程序与传统金属材料显著不同,车辆的维修技师需要进行新的培训,特别是要对材料性能上进行培训。事实上,美军车辆维护手册需要不停地进行更新,以满足新材料应用。
在新型轻质材料在军事车辆的使用上还有一些其他壁垒需要克服,包括得到组织化的认知、如何降低单件产品的设计周期以及如何应对低产量而形成的高生产成本等。但毫无疑问的,采用新材料、新工艺已经在美军高层达成共识。不仅在材料上,而且在能源供应上,美军也不断进行革新,力图将燃料电池等新技术应用到军事车辆上。
美军有个“军事后勤革新”(RML: Revolution in Military Logistics)计划,该计划要求美军车辆在未来要降低75%的燃油消耗,这就迫使他们必须在新型材料上有更加积极的选择。但新型轻质材料的选择极大地增加了车辆采购成本,尽管这些车辆在生命周期中的维护成本降低,耐蚀性能极大提高,燃油效能也极大提升。因此,任何大的变革都需要极大的决断力、深远的思考以及更加全局性的战略企划。但无论从哪个方面讲,美军都走到了世界前列。
后期维护成本的降低以及能耗的降低能否抵消初期的采购成本是一个问题, 但关键的问题是:谁能赢得未来战争的胜利。显然,新材料战场在战场的机动性更高、对后勤的要求更低,从地面战争的硬件上,美军已经跑到了世界的前面。
美军在未来战车上给出了明确的技术要求,包括对整个后勤保障的规模、车辆使用年限,车辆自重,维护成本,燃油消耗,生命周期管理等等。虽然很多数字还不被外人所知,但这种精确化的要求无疑是科学和明智的。
一般来说,现役军事车辆都超出了它的经济使用期限,其结果是增加了运维和支持成本,并降低了可维护性。这里存在一个效能比的问题。目前美军整个轮式车辆的这个效能比是0.63。而如果采用新型轻质材料,这个效能比可以提高至1。也就是说,8辆目前的军事车辆所干的活只相当于未来5辆车辆干的活。此外,目前美军轮式车辆的年运维成本(O&M)高达15亿美元,也就是说每辆车每年需要6000美元, 这个成本每年还以3000万美元的速度递增,而美军的车辆总规模实际在消减,大约从此前的25万辆消减到22万辆。
腐蚀部件修理成本呈现出越来越高的态势。由于腐蚀问题,军事车辆的经济使用期限一般在13年至16年。超过这个年限,车辆的使用效率就会大幅降低。
消减车辆自重是关键
美军80%的车辆属于这三个等级: 2B级,即8500~10000磅;6级,即19501 至26000磅;和8级,即33001磅以上。大约10万辆美军车辆属于高机动性轮式战场(HMMWV),即大家熟知的所谓悍马(Humvees)战车。另外10万辆属于中型车辆,载荷能力在2.5吨到5吨之间, 即6级以下。还有2万辆属于重型车辆, 低于8级,其中包括越野卡车和特殊用途的车辆,例如托盘化装载系统(PLS: Palletized Loading System),重型增程机动战术卡车(HEMTT: Heavy Expanded Mobility Tactical Truck),70吨载荷的重型装备运输系统(HETS:Heavy Equipment Transporter System),以及三个型号的拖车。11万辆拖车包括货运拖车、平板拖车、低架载重车、供弹拖车、厢式拖车、油罐车和特殊用途拖车。
一辆美军车辆平均每年要跑2000-3000 英里,其中80%是在公用路面上,余下时间在战区或野外。美国陆军坦克及机动车辆司令部(TACOM)对这些车辆进行整体性负责。
目前,美军70%的燃油通过船舶输送到战区;一个机械化师每天要消耗60万加仑的燃油,而一个攻击型空军师每天要消耗30万加仑的燃油,这是美军燃油消耗的大户。美军燃油的采购成本每加仑只有1.01美元,在非战时的最后应用成本为每加仑13美元,战时则增加至每加仑100-400 美元。美军军事研究机构认为,采用轻型材料,至少可以降低燃油消耗50%以上, 这意味着一旦大型战争打起来,轻质战车可以保障美国经济不会被拖垮。
一个轻型步兵师有11520名作战队员, 总载荷量为18122吨,这包括士兵的体重、个人装备重量,以及1天的弹药量,5天的食物,帐篷等材料以及个人用品,用于15 天的燃油、药品和配件等。如此“轻型” 部队就需要3841台车辆以及83架飞机。为了运输这些部队,需要动用C-141运输机816架次,或者C-17运输机61架次。
与此相对比的是,一个重型装甲师, 总载荷高达102052吨,包括17186名作战人员、8125台车辆。运输如此庞大的部队需要C-130运输机这样的庞然大物。
如此“沉重”的现代化部队再不同于以前“小米加步枪”的时代。而如何降低如此多军事车辆的自重也成了军队后勤保障的关键。美军认为,通过新型材料的使用,消减整体作战载荷10%-20%是可能的。而由于作战车辆自重降低而带来能源消耗的降低,还可以整体降低军事运输载荷的30-50%。这是一个非常可观的数字。它意味着在同样作战能力下,采用轻质材料车辆的部队比传统的“钢铁”部队至少提高机动性30%以上。对于战争来说,这足以致胜。
新材料和新工艺的机会
为了满足军事车辆消减自重的需求, 从车身到部件都有广泛的新材料可以选择。但在这之前,是需要一个新的设计流程。因为这些新材料的物理性能以及可加工性毕竟与钢铁材料不同,因此对这些材料进行合理设计以及充分实验是保障能否应用的关键环节之一。这并非本文的重点,但需要提及。美国军事车辆在设计方面不仅有军事研究单位的参与,更有传统军工企业的大力贡献。在中国,非军事企业参与设计也是非常关键的。
显然,在设计过程中要考虑材料成型以及制造成本问题。不考虑成本的军事策略一定会把本国经济拖垮,前苏联的垮台是很好的反例。
由于军事车辆,特别是特殊军事车辆的产量不高,因此必须采用一些新工艺来解决低产量带来的成本压力。这些新技术包括:
超塑性成型,特别适合于某些商用超塑性合金,如5083;
热固性高分子复合材料的压缩成型;
薄片部件的橡皮囊液压成型(Rubber-pad hydroforming );
管件液压成型;
管件和薄板的电磁成型工艺;
管件和薄板的爆破成型工艺;
薄壁精密铸造;
用于热固性高分子复合材料的其他快捷成型方式;
接口和焊接技术。
在军事车辆上,置换钢铁最重要的备选材料是铝镁合金。商用飞机制造商对此轻车熟路,因为典型的商用飞机上70-75% 是铝。铝镁合金取代钢铁的问题也是明显的,一是成本比较高,二就是如何禁得住炮火的打击。
除了铝镁合金,高强度钢也是用于消减军事车辆自重的有力材料,有资料表明,采用高强度钢的车辆比一般设计的车辆自重可以降低20%作用。超轻型钢质汽车车身(ULSAB)可以达到350-420MPa 的强度,而一般钢材只有140MPa。在美国, 回磷钢材和固态加强无空隙钢(solution-strengthened interstitial-free steels)、双相钢(dual-phase steel)、相变诱发塑性钢(TRIPS)也在研究之中。
日本NKK公司开发了一种用于汽车的薄板钢材,拉伸强度高达780 -980 MPa, 并具备高可成型性。该公司名为“Nano Hiten”的新钢材,基于nano-obstacle技术, 其强度比传统强度高10倍。Nakayama钢铁公司推出一种细晶粒钢,其铁素体颗粒只有2到5个微米大小,而传统钢材的铁素体颗粒大小为10-20微米,这种钢材的拉伸强度可以达到500-600 MPa。
在提升传统碳钢耐蚀性能上,有一系列方法,例如镀锌。在军事车辆上,常用的称为化学耐蚀涂层(chemical-agent-resistant coatings)。但无论怎样,在严酷环境下,钢铁材料还是没有其他轻质材料更加耐蚀。换句话说,从耐蚀性上,军事车辆选择其他轻质材料似乎是没有选择的选择。
铝合金 2519 (Al-Cu-Mg) 是一种高性能合金,可以很好地满足军事车辆在强度和重量上的需求,它是美国铝业公司和美军联合开发的材料,其抗弹道穿透性能远远超过铝镁5000系列合金,这种合金也被考虑应用到海军两栖战车上。
免责声明:本网站所转载的文字、图片与视频资料版权归原创作者所有,如果涉及侵权,请第一时间联系本网删除。
-
标签: 腐蚀军事
相关文章
无相关信息
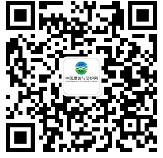
官方微信
《腐蚀与防护网电子期刊》征订启事
- 投稿联系:编辑部
- 电话:010-62316606-806
- 邮箱:fsfhzy666@163.com
- 腐蚀与防护网官方QQ群:140808414
点击排行
PPT新闻
“海洋金属”——钛合金在舰船的
点击数:8135
腐蚀与“海上丝绸之路”
点击数:6475