原料的补加(主盐)
补充原料时应少量高频。并且加强补加时的搅拌,相对降低主盐的局部浓度。这是因为后期镀液,由于亚磷酸根的浓度较高,如果镍盐浓度过高,会产生亚磷酸镍的沉淀,引起镀液混浊,这时就应把络合剂、缓冲剂同期同步添加;另外次磷酸盐水溶液的pH值较高,补加过快,会导致镀液局部pH值过高,形成Ni(OH)2沉淀,这时应把缓冲剂、促进剂(乳酸、丁二酸等)一起补加。
当槽液体积过大,施镀工件面积也过大(如镀热交换器)原料消耗量大速度快,应设计“体外循环”、“连续补加”、“连续位移”的工艺。投资设计建设自动分析控制补加系统最好,这样就会使镀液稳定,稳定镀速和镀层质量,提高生成效率。
降温结晶处理
镀液随着使用周期延长,镀液里面不参与反应的Na+、S042-、AC-、柠檬酸根、乳酸根、丁二酸根)及反应的副产物H2P03ˉ,激剧富集,一旦温度降到10℃以下,溶解度较小的Na2 S04·10H20、NaH2P03、NaAC就会结晶出来。
有条件的化镀厂家可将使用多次后的镀液进行冷冻降温处理,没有条件的厂家特别是我国北方的厂家可将镀液贮存到冬季进行自然降温结晶处理,待Na2S04、NaH2P03、NaAC结晶后,进行倒槽过滤,根据分析检测结果将其它相应成分调整、补加,便可得到再生的新镀液。但进行生产施镀前要进行镀速对比试验,有必要对镀液中某些成分进行微调。
分析检测方法
在实际操作中,应适当改变分析检测方法。
首先取样分析时间的间隔要缩短,因为主要原料的补加已改成了少量多次,所以主盐浓度的检测次数要相应增加。
其次测试时间也要缩短,只有这样才能增加测试次数,可只测Ni2+或H2P02_ ,根据测得的结果在事先根据计算的理论量或者试验消耗量绘制的曲线图上找出补加量。
试剂的用量也要改变,镀液多次使用后,其中的副产物和添加剂的浓度逐渐提高,在不进行掩蔽的情况下,按常量检测会造成检测结果不准,甚至无法检测,a.Ni2+滴定时等效点颜色变化不明显,应相应添加紫脲酸铵和氨氯化铵缓冲溶液(或水)。由于亚磷酸根的浓度过高,在测次磷酸根时加高铁氧性时,会直接产生沉淀,所以要减少镀液的采取量(以常量的一半为好)。
镀液温度
对镀速和镀层的质量影响较大,除应具备自动温控设备外,操作人员应随时用水银温度计测量槽内温度,随时校正温控仪误差。随着镀液周期数的增加,镀速将逐步下降,特别在三周期后,下降较为明显,这时可采用逐步少量提高温度的办法,以维持正常的镀速,一般情况下,三周期后的每次入槽温度要相应提高一点。
最后应随时观察槽液稳定剂情况,应少加或不加对镀液稳定性敏感的添加剂,以免对镀层质量产生波动,甚至造成镀液分解,必要时用PdC12测定镀液的稳定性。
免责声明:本网站所转载的文字、图片与视频资料版权归原创作者所有,如果涉及侵权,请第一时间联系本网删除。
-
标签: 维护化学镀液多周期
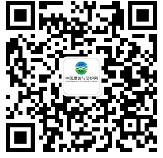
官方微信
《腐蚀与防护网电子期刊》征订启事
- 投稿联系:编辑部
- 电话:010-62316606-806
- 邮箱:fsfhzy666@163.com
- 腐蚀与防护网官方QQ群:140808414