优化镍磷镀工艺的有效途径
前处理是保证镀层质量的前提。电镀产品质量问题的80%以上都出在前处理工序。镍磷镀前处理则显得更加重要,特别是石油机械产品的镀,一般选用钙钢,经调质处理27~31HRC,渗碳0.05~0.1mm。工件形状复杂、多孔和内、外有螺纹及盲孔等;多数零件采用20~40CrMo的合金钢,均经过不同工艺的热处理,为保证镀层与基材的结合,各道工序之间必须彻底清洗,镀件在冲洗槽中停留时间不少于2min己成为获取质量良好镀层的重要条件。
按前面叙述的典型前处理工艺外,要注意有些镀件上有残磁,要用消磁机消除材料上的磁性。除油后,要在大于80℃热水中清洗,把粘附的氧化钠(碱液遇到盐酸生成物)除净;在保护非镀面和中心孔时,严禁用裸手操作,以防手脂油的污染;清理好的工件,要妥善存放好、防止第二次污染,待生产用;生产前仍要再次加强清洗,并用80℃以上热纯水,把粘附脏物、油污再次彻底清洗干净;要在配制1:1活化液中,浸蚀1~3min,再经冷水洗→热纯水浸后,方可入专用的镀槽,并搅拌、循环镀液,要始终保持镀液的流动性和稳定性。
另外,做好中心孔保护是需第二次磨削的关键。在高压管汇元件中,旋塞的非镀面保护,特别是中心孔的保护是夫系到镀件施镀尺寸达到要求,保证质量的难点。在实践中我们采用了多种办法,涂阻镀液、用环氧树脂材料堵塞、金属夹具等等,仍然未完全解决中心孔的保护,使厂家在第二次磨削中尺寸偏位造成镀件返修、甚至报废。
在前处理过程中,增加了一道专有的清洗、保护工序,先要将中心孔除油,彻底清洗干诤。在工件经热水清洗后,将“三和”牌密封胶滴入,经数小时干燥、固化后再使用;这种密封胶镀前、镀中耐碱、耐酸、耐温,镀后完整无损,而且也很易取下。工件经热处理后的第二次磨削加工,中心孔的位置和尺寸都保证了加工质量。
镍磷镀层的磨削加工,要正确对待。要选用绿色碳化硅或白刚玉砂轮,粒度60~80#,硬度中软,组织状态中等,其尺寸和形状视零件而定;同时要计算好磨削用量,确定砂轮和工件的转速及切削深度和走刀量。同时,要注意镍磷合金镀层磨削时无火花,加工时,镀层表面应涂上红丹油,以便对刀。否则,容易将镀层磨损。
镍磷镀层在85℃左右的温度,厚的镀层施镀时间在6~7h条件下进行,石油机械零件,内外有管螺纹、连接头的端面、内孔尺寸精度要求高,而且,都要保护。选用的保护材料,要耐高温、耐酸、粘结力强、镀后易撕下,工件表面无残留胶;我们在生产中选用鸿富达特种胶粘带(苏州)公司生产的T×75电镀胶带及定制生产的专用尺寸胶片。使用非常方便,耐高温、耐溶剂、粘性佳,又便于撕下,确保了用户对镀件非镀面的尺寸要求。
镀液质量是保证镀层质量的基础。
化学镀镍的反应过程是一个自催化的氧化-还原过程。以次磷酸钠作还原剂的酸性镀液,次磷酸钠被氧化生成亚磷酸盐悬浮于镀液中或沉淀在镀件上。因此,生产过程中,要适时补充浓缩液,以维护镀液的稳定性。
在生产过程中,对镀层≥0.06mm的镀层,由于施镀时间一般要五个小时左右,无论采用何种循环、搅拌,甚至对工件移动或振动,若润湿剂未达到一定的比例,在镀件的上端面或者经第二次磨削加工后,镀层上的针孔,显而易见。
为防止针孔,要在镀液中添加润湿剂十二烷基硫酸钠。一般资料上介绍,添加量在0.05~0.1g/L之间,超量将影响镀层的质量。经多年的生产、实验和验证,配方量要达到0.75g/L,并在镀液升温到≥80°C时,在搅拌或循环条件下缓慢加入;因生产过程中消耗和带出量较大,每次开缸时,仍要按0.025g/L的量再补充。
生产前,取一根Φ2mm的铁丝,做成Φ90mm的圆环,垂直放入镀液中,然后轻轻提起,如圆环内液膜当即破裂、说明溶液中润湿剂含量少、可按0.02g/L十二烷基硫酸钠再补充。按此办法施镀的工件表面,光洁如镜,无针孔,保证了产品的质量。
在应用中,镀液的维护和控制是非常重要的。
化学镀镍时镍离子消耗,还原剂浓度减少等问题,随时影响化学镀镍液的稳定性。可以说这是化学镀镍工艺难以掌握的主要原因。一般情况下,要按化验室分析结果,按比例添加浓缩液和稳定剂、光亮剂。对镀层厚度大于0.06mm,定时分析Ni2+离子浓度和调整pH值非常重要,生产过程中每镀一小时或槽液有异向时,要分析硫酸镍的浓度,根据化验结果计算所需添加的补充液,维护镀液的稳定。
镍离子浓度的调整和控制是化学镀镍工艺最基本的管理项目,它决定了镀层的沉积速度和镀层质量。同时,要控制好温度和pH值。温度对沉积速度影响极大,一般控制在85~90℃,新配镀液先取下限,以维持沉积速度的稳定。由于pH值的高低将会影响镀液的稳定性,必须加强控制。
在实践中逐步摸索做镀层厚0.06~0.09mm,Ni2+含量取上限,温度和pH值低一点的操作办法。即:Ni2+含量≥25g,温度83±1℃,pH值4.4±1,镀速控制在10~12μm/h;镀液在生产中要过滤,镀液中的沉积物、镀槽、加热管和挂具表面的镍层及杂物,应及时清除或用褪镀液退除;当发现镀液生成气泡,颜色变淡,这就显示了镀液已发生自然分解,应尽快进行处理,一般补加2g/L苹果酸、2m1/L乳酸等络合剂。按以上维护和控制办法,加工的镀件光洁一致,产品质量稳定、深受用户好评。镀液一般可用6~8个周期。
扩宽化学镀镍的优势
用镍磷镀层代替镀硬铬在工业中应用己非常成功,特别是形状复杂的工件、如油田抽油泵筒、管套、泵体、液压管件等,不仅可以消除六价铬对环境的污染,而且可以省略镀后的研磨、大大提高了生产效益。
化学镀镍与电镀硬铬的比较、存在的不足和差距,主要是镀态的硬度;镍磷合金硬度500~650HV,硬铬硬度800~900HV;镍磷镀层需经过热处理后,才能达到900~1100HV;而在施镀的方法上,结合力、孔隙率和均匀度上优于硬铬。从市场上反馈的信息来看,选择热处理的镍磷镀层的潜力很大。
提高镍磷镀层硬度的热处理工艺;热处理温度400℃,处理时间1h;为防止工件表面产生有色的氧化物,热处理工序要在惰性和还原性气氛或真空环境下进行。
一般电镀企业,受生产条件和技术限制,不能满足用户的要求,均放弃了加工厚的镍磷镀层和需要热处理的加工业务,使化学镀镍技术的推广和发展受到一定的影响和制约。
提高硬度和耐磨性的热处理采用铸铁粉末,放入专用铁盒里,将镀件完全保护好的办法,可替代需用保护气体或使用真空炉的要求。按以上热处理工艺升温到400℃,处理1h后,再缓慢随炉温自然冷却到室温,取出工件、清理,镀层外观光泽一致、无变色。多年来,热处理的产品,经石油机械厂的检测中心和机械工业表面覆盖层产品质量监督检测中心,采用M型显微硬度计和MVD一1000JMT2型微氏硬度计,检测的结果,镀层硬度未经热处理时为(500~600)HV0.918,经热处理后达到(921~1017)HV0.918。
结论
对石油机械产品中镍磷镀层的特殊要求,在生产实践中,探索新的途径,确定最佳工艺条件,全面满足用户需求。
在镍磷镀层0.07~0.09mm施镀中,优化镀液配制,加强前处理,做好中心孔和非镀面的保护,提高硬度的热处理办法和第二次磨削需正确操作等工艺控制要素。
化学镀镍磷合金的溶液十分敏感,因其浓度、温度、pH值控制范围较窄,使用和生产中要特别关注每一个环节的变化,操作中要加强控制、跟踪分析、严格执行工艺。同时,随着工艺的广泛应用,在工业化实践中要进步的创新、发展和提高。
免责声明:本网站所转载的文字、图片与视频资料版权归原创作者所有,如果涉及侵权,请第一时间联系本网删除。
-
标签: 化学镀镍石油机械
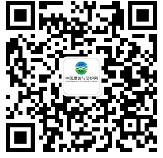
官方微信
《腐蚀与防护网电子期刊》征订启事
- 投稿联系:编辑部
- 电话:010-62316606-806
- 邮箱:fsfhzy666@163.com
- 腐蚀与防护网官方QQ群:140808414