液化天然气(LNG)作为一种清洁、高效、优质的能源,其燃烧产生的CO2排放量最高可减少20%[1]。我国明确提出2030年前碳达峰、努力争取2060年前碳中和。《中华人民共和国国民经济和社会发展第十四个五年规划和2035年远景目标纲要》中指出,要大力发展清洁可再生能源,推进LNG接收站规划建设,尽可能用非碳能源替代化石能源,加快能源绿色低碳转型,持续提高清洁能源利用水平[2]。
天然气在-160℃下液化后,体积缩小为原来气态时的1/625左右,密度也较低,仅为同体积水的45%左右,非常便于运输[3]。天然气中含有85%~95%的甲烷,且在LNG中甲烷纯度更高。相较于包括石油在内的其他化石燃料,LNG在减少排放方面效果更显著,据有关数据表明[4, 5],全球LNG平均排放强度为0.35% CO2/吨。目前常用的LNG储罐材料为9%Ni钢,其合金成本昂贵,在加工及运输过程中易被磁化,焊接困难[6]。为节省成本,浦项钢铁公司与韩国科学技术院联合研发出新型LNG储罐超低温奥氏体高锰钢,该钢在-196℃下的韧性、抗疲劳性及耐腐蚀性相当于广泛使用的9%Ni钢,但其塑性约为9%Ni钢的3倍[7]。此外,Mn的价格为Ni的1/10左右,高锰钢的成本价格比因合金、9Ni钢、不锈钢低70%~80%,极大降低了制造LNG储罐成本[8],并具有强度高、加工方便等特点。因此,高锰钢在用作LNG储罐方向上具有极大应用前景与价值,其塑性、耐蚀性以及抗疲劳性引起许多低温钢研究者关注[9]。
合金化处理是改善钢铁各项性能的有效方法之一,在处理钢样过程中通常加入少量合金元素,都会对钢铁的组织和各项性能产生显著影响[10]。Li等[11]通过低温拉伸试验研究了Fe-20/27Mn-4Al-0.3C(20Mn、27Mn)钢的力学性能,表明20Mn钢在低温下存在变形诱发马氏体效应,伸长率为77.4%;27Mn钢未形成变形诱发马氏体,且伸长率为68.3%,相对较低。Mn影响了钢样的加工硬化率和伸长率。Tang等[12]研究表明,高锰钢中少量的Al能够影响钢样的微观组织,通过改变样品表面氧化膜的成分,提高Al2O3膜的完整性,从而提高耐蚀性。Fajardo等[13]研究表明,TWIP奥氏体钢Fe-Mn-3Al-3Si中,Mn含量越高,腐蚀敏感性越强,耐蚀性越差。张丹丹等[14]研究表明,Mn含量为12.5%的固溶高锰钢达到最大电荷传输电阻,表现出优异的耐蚀性,证明了过高过低的Mn含量在高锰钢中均对耐蚀性不利。Su等[15]对中锰钢在NaCl溶液喷雾中形成的腐蚀产物层分析表明,腐蚀产物中存在Cr增加、Mn减少的现象,这些合金元素有利于形成腐蚀防护层,从而优化耐蚀性能,因而钢材自身受元素影响的耐蚀性能对于服役稳定性至为重要。
此外锈层结构、形貌还受外界环境和处理工艺的影响,例如:温度[16]、离子浓度[17~19]及种类[12,20]、冷轧[21]、焊接[22]等,锈层结构不同导致钢样耐蚀性的差异。明男希等[23]研究表明,温度通过影响X70钢表面FeCO3膜的过饱和度、晶粒形核率和长大速率,进而影响其腐蚀速率。Cheng等[24]研究表明,高锰高氮奥氏体钢(QN1803)在激光焊接后,由于高锰阻碍了相变,过饱和氮导致氮的流失,使QN1803残留更多的
-铁素体,从而整体耐蚀性降低。Yan等[25]研究了高锰钢在模拟海洋飞溅区环境中的腐蚀行为,腐蚀速率与腐蚀过程中形成的氧化物有关,研究证明腐蚀产物膜的保护作用逐渐显著。腐蚀初期生成的Mn氧化物促进了腐蚀进程,后期腐蚀产物中Fe3O4、
-FeOOH和FeCr2O4的稳定性和致密性抑制了锰铁氧化物的腐蚀作用,减缓了腐蚀速率。Zhang等[26]探讨了7B04铝合金在酸浸和盐雾环境(pH = 3.5)下的初始腐蚀行为,认为盐雾环境下腐蚀产物层生成速率比酸浸环境下大,腐蚀电流密度显著低于酸浸环境下试样,证明了腐蚀产物层越厚,对腐蚀反应的抑制作用越强。Wang等[27]研究表明,新型含Al奥氏体耐热钢(AFA)在氧饱和的铅铋共晶(LBE)中,形成分层且不具保护性的氧化层,而在低氧浓度的LBE中,形成完整且具有保护性的富Al氧化层。降低LBE中的氧浓度会减缓界面向内通氧量,使更多的Al向外扩散,这有利于形成富Al氧化层,提高耐蚀性。因而钢材服役环境也影响着其耐蚀性能。
本文选用添加了微合金化元素的高锰钢和普通25Mn高锰钢,通过酸性盐雾试验探究其在模拟海洋大气中的腐蚀行为,利用扫描电子显微镜、白光干涉仪、失重法分析两种高锰钢锈层以及腐蚀形貌的差异,同时通过动电位极化和交流阻抗谱分析钢样的腐蚀过程,研究Cr、N、Al等微合金化元素对高锰钢耐蚀性的影响,为进一步提升高锰钢耐蚀性提供支持。
1 实验方法
实验材料为国内某钢厂生产的两种25Mn高锰钢(HMS),使用湿法分析测得微合金化处理后的高锰钢实际化学成分(质量分数,%)为:C 0.45、Si 0.33、Mn 23.82、P 0.016、S 0.003、Cr 3.53、Cu 0.51、B 0.002、N 0.023、Al 0.032;未处理高锰钢化学成分(质量分数,%)为:C 0.46、Si 0.23、Mn 24.31、P 0.021、S 0.003、Cr 4.04、Cu 0.46、B 0.007、N 0.01、Al 0.005。可将微合金化处理后的高锰钢命名为WH-HMS,未处理的高锰钢命名为PT-HMS,采用电火花线切割(EDM)设备分别从两种高锰钢切割50 mm × 20 mm × 16 mm、10 mm × 10 mm × 3 mm的块状试样用于失重分析和电化学分析,进行电化学测试的样品使用环氧树脂与固化剂呈1∶1比例进行混合,将铜导线在10 mm × 10 mm钢材背面焊接并使用环氧树脂密封。每个腐蚀周期使用3个平行试样以确保实验的可靠与客观。所有试样的工作面,依次使用水磨砂纸180#、400#、800#、1200#、1500#及2000#对钢样6个面进行逐级打磨,除去钢板原始锈层,接着用2.5 μm金刚石膏抛光至镜面,使用酒精超声清洗3 min,去离子水冲洗后低温干燥2 h封存备用。
对钢样抛光处理后,采用4% HNO3和96%无水乙醇(体积分数)配置金相腐蚀液对高锰钢进行刻蚀。使用去离子水、无水乙醇洗净后干燥,采用Leica DM2700M型金相显微镜观察钢样金相组织。图1a为WH-HMS金相组织,其中可见部分晶粒较大,晶界较直,少量析出碳化物在晶界和晶内,呈弥散分布,对其耐蚀性影响不大,所得组织为奥氏体和少量的沿晶网状碳化物。图1b为PT-HMS的组织形貌,大量析出碳化物分布在晶界和晶内[28, 29]。
图1 微合金化处理后高锰钢及未处理高锰钢金相形貌
Fig.1 Metallographic photos of WH-HMS (a) and PT-HMS (b)
根据ASTM B117标准,酸性盐雾试验在YWX/YH-60盐雾试验箱中进行,溶液配置为50 g/L NaCl溶液,实验温度为(35 ± 2)℃,沉降量为1.65 mL/(80 cm2·h),盐雾沉降的速率应在连续喷雾至少24 h后测量。为了模拟酸性大气环境,用稀盐酸将溶液的pH调整为3.1~3.3,实验时间持续12、48、96、168和240 h后,分别取出3个失重试样和3个电化学试样。实验前需清除试样表面的沉积盐,以减少对腐蚀产物的影响。
将腐蚀后试样用去腐蚀液(500 mL HCl + 500 mL H2O + 3~10 g六次甲基四胺)超声波清洗1 min去除腐蚀产物,再用去离子水、无水乙醇清洗、充分干燥后,最后使用高精度天平测量酸性盐雾腐蚀不同时间的失重试样质量。每组失重数据均取3个平行试样的平均值。
采用HV-1000STA场发射扫描电子显微镜(SEM)观察盐雾腐蚀不同时间后试样表面形貌及清除腐蚀层后试样表面形貌。使用Bruker Contour GT-1型白光干涉仪对试样进行三维形貌拍摄,截取其腐蚀轨迹,3D腐蚀形貌通过Vision64 Bruker 软件进行分析。
电化学测试在CHI660电化学工作站上进行,采用三电极测试系统,工作电极(WE)为盐雾腐蚀后的高锰钢、参比电极(RE)为Ag/AgCl电极、铂片(Pt)为辅助电极(CE)。连接接通后,为保证测试体系稳定,先将钢样放在3.5%(质量分数) NaCl溶液中分别静置30 min,稳定后依次测量开路电位(OCP)、电化学阻抗谱(EIS)和极化曲线(PC)。EIS测量在OCP下进行,测量频率为105~10-2 Hz,振幅为5 mV。动电位极化曲线测试范围为-300~500 mV,电位扫描速率为1 mV/s。点蚀电位(Ep)是在正向扫描期间电流密度突然增加的点测定的。测试结束后使用ZsimpWin软件对相关数据进行分析。所有测试均在环境温度(25 ± 1)℃下进行,并重复至少3次以确保数据的可靠性。
2 结果与讨论
2.1 腐蚀行为及形貌分析
图2为两种高锰钢在酸性盐雾环境腐蚀不同周期后腐蚀产物的SEM像。WH-HMS在腐蚀12 h后(图2a),腐蚀产物较少,较薄的腐蚀产物疏松分散在基体表面,表面仍有裸钢露出。48 h(图2c)后腐蚀产物呈棉球状,腐蚀96 h(图2e)时腐蚀产物呈棉球状和团簇状。在腐蚀168~240 h后(图2g和i),腐蚀产物呈团簇状和针状,且存在大量孔洞,有利于Cl-穿过锈层进入基体与锈层界面,促进钢基体的腐蚀,使腐蚀产物逐渐变得均匀、致密。PT-HMS腐蚀12 h后(图2b),表面腐蚀产物呈疏松的团簇状,有较多的孔洞存在。腐蚀48 h(图2d)时,腐蚀产物主要呈棉球状,大块腐蚀产物不再出现,腐蚀较为均匀。腐蚀96 h(图2f)时,“棉球”形态的腐蚀产物变得细小,且呈团簇状,存在大量孔洞。腐蚀168~240 h (图2h和j)后,腐蚀产物逐渐均匀,呈棉球状和针状。随着腐蚀时间的增加,锈层逐渐加厚,腐蚀产物特征显著。研究表明[30~32],γ-FeO(OH)通常呈棉球状、不规则颗粒状和团簇状,α-FeOOH通常呈针状或须状。研究[33, 34]普遍认为高锰钢表面优先形成γ-FeO(OH),随着腐蚀产物的积累,活性的γ-FeOOH转变为稳定的α-FeOOH,二者相互依附,使锈层更加致密。
图2 两种高锰钢盐雾腐蚀不同时间后表面锈层微观形貌
Fig.2 Surface morphology of WH-HMS for 12 h (a), 48 h (c), 96 h (e), 168 h (g), 240 h (i) and PT-HMS for 12 h (b), 48 h (d), 96 h (f), 168 h (h), 240 h (j) after salt spray corrosion
对比两种高锰钢的腐蚀产物形貌,可以看出经过微合金化处理后的高锰钢表面腐蚀产物的致密性得到明显提高,显著减小了其腐蚀程度。WH-HMS在初始时腐蚀程度就相对较轻,腐蚀240 h后锈层更加致密,这说明适量的Cr可在钢表面细化锈层结构,形成更致密的氧化膜。Cu的添加可有效促进α-FeOOH稳定化锈层的形成[35],钝化膜中Si和Cr的分布几乎同步,这种协同作用增强了钢样表面膜的钝化能力[36],进而提高钢样耐腐蚀性能。经过盐雾不同腐蚀时间后三维轮廓图如图3和4所示。两种高锰钢腐蚀产物随着腐蚀时间增加,腐蚀产物逐渐积累,在初始阶段WH-HMS的腐蚀产物厚度最高约20.4385 μm,略大于PT-HMS。腐蚀240 h后,多处点蚀连接形成不规则形状的腐蚀区域,且WH高锰钢相较于PT高锰钢腐蚀得更加均匀,与观察到的表面形貌结果一致,表明WH高锰钢在腐蚀后期,腐蚀产物更加均匀,耐腐蚀性更好。
图3 微合金化高锰钢盐雾腐蚀不同时间后的三维轮廓图
Fig.3 3D morphologies of WH-HMS after salt spray corrosion for 0 h (a), 12 h (b), 48 h (c), 96 h (d), 168 h (e) and 240 h (f)
图4 普通高锰钢盐雾腐蚀不同时间后的三维轮廓图
Fig.4 3D morphologies of PT-HMS after salt spray corrosion for 0 h (a), 12 h (b), 48 h (c), 96 h (d), 168 h (e) and 240 h (f)
图5为两种高锰钢去除腐蚀产物后表面微观形貌。由图(5a, c, e, g和i)可见,WH高锰钢试样表面形成了少量局部点腐蚀坑,在腐蚀48 h后,有析出物质生成。腐蚀96 h后,出现一些凸起的线状奥氏体型组织,而并没有出现明显的点蚀坑,局部腐蚀并未加剧,这也进一步证实了点蚀特征不会随着腐蚀时间的增加而发生显著变化。同样,PT高锰钢出现类似现象,在腐蚀48 h后,出现线状奥氏体组织,且有大量析出物生成。在腐蚀168和240 h后,出现裂纹,点蚀坑变多,局部腐蚀加重,如图5g和j所示。结果表明,高锰钢表面均表现为局部点腐蚀、有析出物生成和局部裂纹形貌,且PT高锰钢的表面腐蚀更为严重,说明微合金化元素的添加大大提升了高锰钢的耐蚀性能。
图5 两种高锰钢盐雾腐蚀不同时间后去除锈层表面微观形貌
Fig.5 Surface morphology of the rust removal layer of WH-HMS for 12 h (a), 48 h (c), 96 h (e), 168 h (g), 240 h (i) and PT-HMS for 12 h (b), 48 h (d), 96 h (f), 168 h (h), 240 h (j) after salt spray corrosion
2.2 动电位极化曲线
经过不同盐雾腐蚀时间的两种高锰钢在模拟海水溶液中的动电位极化曲线如图6所示。结果表明,不同腐蚀时间后,两种高锰钢锈层的阴极极化曲线基本相似,阳极极化曲线表现出不同的腐蚀行为。阳极极化曲线显示,在-0.6~-0.4 V范围内,各个腐蚀阶段的锈层都有不同程度的钝化,即随着电位的升高,电流密度基本保持不变。微合金化高锰钢在腐蚀240 h后出现的点蚀电位明显升高,这也与研究[37]得出的结论一致,随着N含量的提高,试样的腐蚀没有明显变化,但是点蚀电位显著提高,表明N含量的提高改善了腐蚀产物膜层的保护性能,耐点蚀性能增强。
图6 微合金化高锰钢、普通高锰钢盐雾腐蚀不同时间后极化曲线
Fig.6 Potentiodynamic polarization curves of WH-HMS (a) and PT-HMS (b) after salt spray corrosion for different time
对极化曲线进行Tafel曲线拟合可以得到腐蚀电位(Ecorr)、腐蚀电流密度(Icorr),进而判断工作电极的腐蚀速率,拟合结果如表1、2所示。从表中可以看出,盐雾240 h后,WH-HMS腐蚀电流密度由5.328 μA/cm2降低至1.962 μA/cm2,腐蚀速率由5.230 × 10-3 mm/a降低至1.925 × 10-3 mm/a;PT-HMS腐蚀电流密度先由5.310 μA/cm2降低至2.754 μA/cm2,又逐渐增加到4.038 μA/cm2,腐蚀速率也先减小后增加,由5.212 × 10-3 mm/a降低至2.703 × 10-3 mm/a,再增加到3.964 × 10-3 mm/a。这些数据进一步证明微合金化处理后的高锰钢的耐腐蚀性最好,与形貌表征分析出的结果相符。
表1 微合金化高锰钢极化曲线拟合结果
Table1 Polarization curve fitting results of WH-HMS
表2 普通高锰钢极化曲线拟合结果
Table2 Polarization curve fitting results of PT-HMS
2.3 EIS分析
图7为经盐雾各腐蚀周期下两种高锰钢在3.5%NaCl溶液中的电化学阻抗谱测试结果。耐腐蚀性能可以通过电容性半圆弧直径来体现,半圆弧直径的增大表明耐腐蚀性能的提高[38]。随着腐蚀时间的增加,WH-HMS的容抗弧半径腐蚀96 h后略微增大,在腐蚀240 h时容抗弧半径达到最大。PT-HMS在腐蚀96 h时达到最大容抗弧半径,后随着腐蚀时间延长而逐渐减小,且PT-HMS的最大容抗弧半径远小于WH-HMS,表明WH-HMS的耐蚀性更好,说明Cr、N、Al等微合金化元素的添加明显提高了高锰钢的耐蚀性。Bode图频率与阻抗的关系表明,随着腐蚀时间的增加,低频总阻抗模量逐渐增大。结果表明,在腐蚀过程中,锈层的耐蚀性逐渐增强。
图7 微合金化高锰钢、普通高锰钢盐雾腐蚀不同时间后的电化学阻抗谱图及等效电路图
Fig.7 EIS of WH-HMS (a, c,e) and PT-HMS (b, d, f) and electrochemical equivalent circuit (g) after salt spray corrosion for different time
为了评估腐蚀产物在不同腐蚀时间后在试样表面形成的保护膜的阻抗能力,采用图7g所示的等效电路(EEC)模型拟合阻抗谱,其中,Rs表示溶液电阻,Rf和Qf为腐蚀产物膜层电阻和恒相元件(CPE),Rct和Qdl为双电层间的电荷转移电阻和恒相元件,n为弥散指数,表示“弥散效应”的偏离程度,当n = 1时,Q相当于纯电容。得到的最佳拟合参数如表3和4所示。从表中拟合结果可知,腐蚀240 h后WH-HMS的Rct值远大于PT-HMS,说明微合金化处理的高锰钢耐蚀性更优。
表3 盐雾腐蚀不同时间后微合金化高锰钢等效电路拟合结果
Table 3 Equivalent circuit fitting results of WH-HMS after salt spray corrosion with different corrosion time
表4 盐雾腐蚀不同时间后普通高锰钢等效电路拟合结果
Table 4 Equivalent circuit fitting results of PT-HMS after salt spray corrosion with different corrosion time
2.4 腐蚀动力学分析
高锰钢酸性盐雾腐蚀不同时间后单位面积失重曲线及拟合曲线如图8a所示。已有研究表明,金属材料的腐蚀失重ΔW与腐蚀时间t之间存在幂函数关系,公式如下[39,40]:
式中:A和n为常数,反映锈层对金属基体的保护作用[41]。若n < 1,锈层起保护作用;若n > 1,锈层加速腐蚀。由表5的拟合结果可知,两种高锰钢的n值均 < 1,说明随着腐蚀时间的增加,两种高锰钢的锈层厚度逐渐增加,均具有保护作用。而ΔWWH-HMS = 4.44202 × 10-4t0.9618 < ΔWPT-HMS = 8.74985 × 10-4t0.67759,说明微合金化后高锰钢锈层的保护性高于普通高锰钢。
图8 两种高锰钢盐雾腐蚀不同时间后腐蚀失重拟合曲线和腐蚀速率变化趋势
Fig.8 Variations of mass loss fitting curve (a) and corrosion rate (b) of WH-HMS and PT-HMS with time
表5 两种高锰钢腐蚀动力学拟合结果
Table 5 Fitting results of corrosion kinetic curves of two experimental steels
根据钢样的原始质量与去除腐蚀产物后的质量之差来测定高锰钢的质量变化(Δm)。通过确定平均腐蚀速率值,如表6所示,表征了腐蚀动力学曲线,如图8b所示。根据 式(2)[40,42]计算平均腐蚀速率ACR:
其中,Δm为质量变化(g);t为腐蚀时间(h);ρ是被测试钢材的物理密度(0.8 g/cm3);S为钢板最大表面的面积(cm2)。两种高锰钢腐蚀曲线均呈不断下降的趋势,其中PT-HMS在初始阶段,平均腐蚀速率有急剧下降的趋势,在下一个浸泡时间节点后,平均腐蚀速率略有下降。80~240 h的腐蚀曲线较为稳定,腐蚀速率的相对稳定值为0.3745 × 10-3 mm/a;WH-HMS平均腐蚀速率下降相对较为显著,腐蚀240 h后稳定值不明显。微合金化后高锰钢的腐蚀速率整体均小于未处理高锰钢,且失重量相对较大,说明微合金化后高锰钢的耐蚀性更优。
表6 两种高锰钢盐雾腐蚀不同时间后平均腐蚀速率及失重量
Table 6 Average corrosion rate and mass loss of two experimental steel
3 结论
(1) 微合金化工艺通过致密化钝化膜有效提升了高锰钢的耐蚀性,两种高锰钢在腐蚀初期,疏松锈层为腐蚀的发生提供了通道,腐蚀速率较快,腐蚀电流密度较大;随着腐蚀时间的增加,锈层覆盖率、致密度逐渐增加,腐蚀速率也逐渐减缓,腐蚀电流密度减小,耐腐蚀性提高。WH-HMS在腐蚀240 h后,其EIS谱线形成最大容抗弧半径,且远远大于PT-HMS;腐蚀电流密度也在240 h后达到最小值,且小于普通高锰钢,进一步证明微合金化后的高锰钢耐腐蚀性能优于普通高锰钢。
(2) 普通25Mn高锰钢的腐蚀速率约为0.8982 × 10-3 mm/a,微合金化后约为0.3745 × 10-3 mm/a,两种高锰钢腐蚀行为均由点蚀逐渐发展为均匀腐蚀,且腐蚀动力学特性均符合幂函数规律。其中,未处理高锰钢拟合结果为ΔWPT= 4.44202 × 10-4t0.9618;微合金化后高锰钢拟合结果为ΔWWH= 8.74985 × 10-4t0.67759。
免责声明:本网站所转载的文字、图片与视频资料版权归原创作者所有,如果涉及侵权,请第一时间联系本网删除。
相关文章
无相关信息
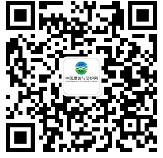
官方微信
《腐蚀与防护网电子期刊》征订启事
- 投稿联系:编辑部
- 电话:010-62316606
- 邮箱:fsfhzy666@163.com
- 腐蚀与防护网官方QQ群:140808414
点击排行
PPT新闻
“海洋金属”——钛合金在舰船的
点击数:9161
腐蚀与“海上丝绸之路”
点击数:7294