海上风电机组矗立在海洋中,而海洋环境是一种极其复杂的腐蚀环境。在这种环境中,海水本身是一种强的腐蚀介质,同时波、浪、潮、流又对金属构件产生低频往复应力和冲击,加上海洋微生物、附着生物及它们的代谢产物等都对腐蚀过程产生直接或间接的加速作用。对于使用钢材料的风电设备而言,“抗腐蚀”成为海上风电运行后最大的考验。
目前,海上风电运维人员对防腐的重视程度认识不高,因为水下钢结构看不见摸不着,觉得离形成重大隐患较远,殊不知危险已悄然存在;另一方面,对海上防腐知识欠缺,两者叠加起来,形成了防腐“说起来重要做起来次要”的局面。但防腐越早治理,对设备的后期运维越好,所以海上钢结构的防腐十分重要。
腐蚀环境
腐蚀是材料在环境作用下发生变质并导致破坏的过程。几乎所有材料的使用过程中,在环境作用下都会发生腐蚀。引起材料腐蚀的环境有两类:一类是自然环境,如大气、海水和土壤等;另一类是非自然环境,如酸、碱、盐及其他工业生产中的介质等,也称工业环境。金属材料在自然环境中的腐蚀过程,实质上就是金属在腐蚀介质中通过电化学反应被氧化成正的化学价态,这也就是金属腐蚀的电化学本质。
海上风机钢结构腐蚀区域划分
海上风机矗立在海上,基础和塔筒是处于海洋环境下的钢结构,在海洋中的腐蚀行为情况随其暴露条件的不同而发生很大的变化。从腐蚀角度上一般将海洋环境自上而下划分为海洋大气区、浪花飞溅区、潮差区、海水全浸区(包括浅海区、大陆架区和深海区)和海底泥土区5个腐蚀区带。风电设备一般运行在海洋大气区内,主要以潮的大气腐蚀为主,不同区域的腐蚀速率存在着明显差别。浪花飞溅区的腐蚀速率最高,潮差区次之。
钢结构在大气中的腐蚀机理
腐蚀机理
整个过程表现为阴极得电子O2+2H2O+4e→4OH-,在阳极铁被氧化成Fe2+,Fe-2e→Fe2+,形成Fe(OH)3,脱水为Fe2O3,这是形成红褐色的铁锈的主要成分。
另一方面,金属表面电解质溶液中会溶有一定量的CO2、SO2、H2S等,加上水的电离便产生析氢反应,即:
CO2+H2O=H2CO3=H++HCO3-
铁及其杂质在H+、OH-、HCO3-等离子溶液中形成腐蚀电池,Fe-2e→Fe2+,Fe2++2OH-=Fe(OH)2,水膜中的H⁺从阴极中获得电子生成H2放出,即2H++2e→H2。产物Fe(OH)2继续氧化形成的Fe(OH)3及脱水后形成Fe2O3。
上述进行的腐蚀表明,金属都是作为阳极发生氧化反应而遭受到腐蚀,整个过程具有由以下三个环节组成:
(1) 在阳极金属失去电子变成金属离子进入溶液,Fe-2e→Fe2+;
(2) 电子由阳极流向阴极;
(3) 在阴极,流来的电子被溶液中能吸收电子的物质接受生成还原物质(2H++2e→H2,O₂+2H2O+4e→40H-)。
影响钢结构大气腐蚀的环境因素
大气的相对湿度:由于大气腐蚀是一种发生在液膜下的电化学反应,空气中水分在金属表面凝聚而产生水膜,和空气中氧气通过水膜抵达金属表面是发生大气腐蚀的基本条件,水膜的形成与大气中的相对湿度相关,故空气中相对湿度是影响大气腐蚀的主要因素之一。金属表面形成水膜所需相对湿度的最低值称为腐蚀临界湿度,当大气的相对湿度超过临界湿度时,其腐蚀速度会快速增加。
表面润湿时间:金属表面能引起大气腐蚀的电解质膜,以吸附或液态膜形式覆盖在金属表面的时间称为表面润湿时间,实际上就是金属表面发生电化学腐蚀的时间。表面润湿时间越长,腐蚀总量就越大。
海洋微生物腐蚀
微生物腐蚀是指微生物附着在金属、合金等复合材料表面形成生物膜,影响金属表面的电化学过程。微生物腐蚀主要是一些细菌作用。腐蚀性的细菌种类很多,但分布广、作用大的腐蚀性细菌都与自然界的硫元素相关,其中主要的是硫化细菌和硫酸盐还原菌。海洋细菌不管在有氧环境中还是无氧状态下,都对金属有腐蚀作用。
耐候钢
耐腐蚀性能优于一般结构用钢的钢材称为耐候钢。工程实践中,耐候钢不涂装就可以使用,是极好的结构用材,并且可以将钢结构(如桥梁)寿命期内的总费用降到最低。
热浸镀锌技术
钢结构热浸镀锌是将表面净化处理后的钢构件浸入460~469 ℃融化的锌液中,使钢构件表面附着锌层,其厚度对5 mm以下薄板不得小于65 μm,对厚板不小于86 μm。钢结构件采用这种保护方式具有耐蚀性好,使用寿命长,且基本不用维护等优点,因而其应用越来越广泛。
防腐涂料技术
海上钢结构防腐涂料喷涂步骤
热喷涂防腐技术
热喷涂是在对钢构件表面作喷砂除锈,使其表面露出金属光泽并打毛的基础上,采用燃烧火焰、电弧等作为热源,将喷涂材料加热到塑态和熔融状态,并用压缩空气将材料呈雾化的颗粒束吹附到基体表面上,随之激冷并不断层积而形成涂层的工艺方法。这种工艺的优点是对构件尺寸适应性强,构件形状尺寸几乎不受限制,同时其热影响区是局部的,热变形较小,但是表面喷涂质量受人为因素、环境因素影响大。热喷涂技术作为长效防腐蚀措施,重点强调在产品设计和制作中采用镀锌、喷铝复合涂层进行长效防护,已成功应用于国民经济的各个部门。
阴极保护技术 8)海上风机水下构筑物采用阴极保护。 电连续性检测 阳极消耗量检测
阳极消耗量的检测可以确定阳极的消耗速度,评价阳极使用寿命。为减少水下作业频次,降低作业安全风险,必要时可将保护形式由牺牲阳极保护改为外加电流保护。
水下牺牲阳极检查的选择,首先整体观察所有阳极组的完好情况,根据现场情况选择两组消耗最大的牺牲阳极进行检查,如果整体相差不大,则上下两层阳极组各选取一块进行检查。
观察牺牲阳极表面溶解状况、腐蚀类型,是否有严重的局部腐蚀乃至断裂的情况,记录牺牲阳极表面的状态。全程水下录像,及关键部位拍照。
下图为常用牺牲阳极示意图,阳极的A方向上选取至少5个测试面,每个测试面测试阳极的B1、B2、C的值,取平均值确定阳极的剩余尺寸,进而推算阳极的剩余质量。
牺牲阳极示意图
阴极保护电位检测
检测钢结构的阴极保护电位,可作为评价该结构所处环境腐蚀性的参数。电位检测利用高内阻数字万用表(内阻大于10 MΩ)、巴氏水下电位检测仪以及参比电极等设备工具进行检测。
牺牲阳极阴极保护电位范围
免责声明:本网站所转载的文字、图片与视频资料版权归原创作者所有,如果涉及侵权,请第一时间联系本网删除。
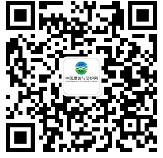
官方微信
《腐蚀与防护网电子期刊》征订启事
- 投稿联系:编辑部
- 电话:010-62316606
- 邮箱:fsfhzy666@163.com
- 腐蚀与防护网官方QQ群:140808414