油气在开采以及运输的过程中,油气管道经常会发生腐蚀现象,如果不加以处理会造成管道破裂,从而引起油气泄漏,更严重甚至会引发爆炸,这不仅会影响油气的安全输送,影响人们的使用,而且会引发安全事故,造成国家的经济损失。因此我们要分析油气集输管道的腐蚀原因,使用科学的防腐措施来防止管道发生腐蚀,保证油气的安全输送,保障国家的经济利益不受损失。
1.1 外腐蚀
油气管道的外腐蚀是指金属管道在与周围物质的长期接触之下,与它们发生化学变化、电化学变化或者物理溶解,从而对油气管道外壁造成损害。对于埋在地下的管道来说主要是由于土壤造成的腐蚀。土壤是由液体、固体、气体三类物质组成的,土壤里含有大量的水和空气,水能够让土壤成为导体,空气中的氧气发生运动会造成氧气的浓度不均衡,进而形成氧浓差电池,这种类型的腐蚀对管道造成的损害会更加严重。土壤腐蚀管道除了微电池腐蚀,还有许多其他类型的腐蚀现象。例如:宏观电池腐蚀、不同种类金属产生的宏观电池腐蚀以及微生物腐蚀。
在海底的油气管道腐蚀主要是由海水所造成的电化学类型腐蚀。海底管道长期浸泡在海水里面,再加上海水是一种电解质溶液,管道是金属材料,管道的表面不同部位的材料、化学成分不一样,这就使得管道外表面上形成了不同的电位。这些电位连接在一起,在有导电能力的海水中形成了一个完整的闭合回路,从而形成原电池。这样造成的腐蚀现象,我们将它命名原电池腐蚀。这种类型的腐蚀会对管道表面造成全面或者局部腐蚀,例如:坑蚀、点腐蚀、晶间腐蚀、应力腐蚀等[1]。
1.2 内腐蚀
油气在运输的过程当中,油气里含有的H2S、CO2、SO2、O2等气体以及气田卤水等,这些气体遇到管道内壁会发生化学反应从而造成管道内壁发生腐蚀。同时多相流对管道的冲击也会造成金属管道内壁发生腐蚀。
(1)H2S腐蚀。硫化氢在遇到水时容易发生分解,在水中形成电离反应(H2S→H++HS-、HS-→H++S2-),在与金属管道接触时会发生化学反应(H2S+Fe→Fe2++H2↑),让管道发生腐蚀,在有氧气存在时,还会产生硫酸(H2S+O2=H2SO4),这样就会再一次对管道造成电化学腐蚀。硫化氢还有一定的可能造成金属管道发生氢脆现象(H2S+Fe→Fe2++H2↑)。有研究结果表明,当钢材的缺陷处存在大量的氢离子时,便会产生出氢气。通过大概计算,产生的氢气的强度大概能够达到300 MPa,这就造成了管道的脆化,引起管道的部分区域发生塑性变形,最终引发管道产生裂纹并可能导致管道裂开。
(2)CO2腐蚀。二氧化碳会与水发生反应产生碳酸(CO2+H2O=H2CO3),碳酸会使PH值下降,造成金属管道发生氢气极化反应(Fe+H2CO3→FeCO3+H2),从而造成金属管道发生坑点腐蚀、片状腐蚀等局部腐蚀现象。
(3)SO2腐蚀。二氧化硫和金属管道铁在氧气的作用下发生化学反应形成硫酸亚铁(SO2+O2+Fe→FeSO4),硫酸亚铁发生水解反应形成氧化物和游离酸(2FeSO4+3H2O→Fe2O3+6H++2SO42-),游离酸又加剧了金属铁的腐蚀,形成新的硫酸亚铁(Fe+SO42-+2H+→FeSO4+H2↑),硫酸亚铁遇到水再次分解,这样就形成一个往复循环,造成管道的腐蚀进一步加速。
(4)多相流腐蚀。多向流腐蚀按腐蚀环境划分为清洁环境(无固体、无腐蚀)、冲蚀环境(有固体、无腐蚀)、腐蚀环境(无固体、有腐蚀)以及冲蚀和腐蚀环境(有固体、有腐蚀)。流动形态也对腐蚀有着很大的影响,例如在油田中存在油、水、气多相流,按照流动形态可以划分为分层流、波状流、段塞流、环状流和环雾流等类型。分层流和环雾流会造成管道顶部产生凝析水从而引起结露腐蚀。当气相和液相速度都比较低时,经常会出现平滑或波状的层状流,尤其是在水平和稍微有点倾斜的管流中,由于重力的作用,相态趋于分层,水层出现在管道底部,油流在它的上面;当气相速度较低而液相速度较高时,会产生段塞流;当气相和液相速度都比较高时,会产生间歇流态的段塞流。在这些多相流形态中,段塞流对管道的腐蚀最为严重,这是因为在段塞流的前面经常会形成高紊流复合区,高速的紊流会造成管道壁出现很大的剪应力,在流体的冲击力和剪应力的共同作用下,缓蚀剂膜和腐蚀沉淀物发生掉落,这样不仅会造成流体直接冲击管道表面造成磨损,而且加剧了管道的腐蚀力度[2]。
2.1 外防腐措施
2.1.1 管道外使用防腐涂层
在管道的外壁上涂上防腐涂层,让管道和腐蚀介质分隔开来,从而能够保护管道不受腐蚀。目前我国使用的涂层一般都是环氧涂层,它是当今国际普遍使用的一种防腐涂层,它的性能远远优于传统的沥青涂层和煤焦油涂层。它是一种热固性类型的材料,成分含有环氧树脂以及固化剂等各种材料,黏结力强,涂层致密,表面光滑并且耐盐碱腐蚀。除了环氧涂层之外,管道外壁防腐有时也会使用三层聚乙烯涂层。它的结构是:底层为FBE,约50~127?m,中间层为共聚物胶,约200?m,外层为聚乙烯,约3 mm。这一结构使它拥有高黏结性、抗氧性、耐化学腐蚀、电绝缘性、耐冲击等特点,而且阴极保护电流密度小,只有1~3?A/m2,降低了阴极保护的成本和规模。有调查研究数据表明三层聚乙烯涂层的使用寿命大概达到40年以上,但是由于它的价格比较昂贵,工艺比较复杂,目前还没有被广泛使用[3]。
2.1.2 应用阴极保护技术
阴极保护技术一种为了防止金属在电介质中发生腐蚀的电化学保护技术。这种技术是将金属当做成阴极,并给它接通阴极电流,使它的阴极极化,从而让金属电位低于设定的电位,这样就会消除金属表面的不均匀性,从而减缓阴极的腐蚀,以此来保护金属。阴极保护技术不仅能防止金属腐蚀,还能够提高经济效益。它的费用约为被保护金属结构物造价的1%~5%,是涂层费用的10%左右,但它却可以延长金属结构物的使用寿命高达几十倍。关于这方面曾经有过报道,海上石油开采平台的建造费用一般都达到上亿资金,如果它不采用阴极保护技术,它的使用年限只有5年,而在使用阴极保护技术的情况下,它的使用年限能够达到20年,然而阴极保护技术的费用才只需要一两百万,大大提升了经济效益。因此阴极保护技术目前在全世界得到了非常广泛的应用,例如:地下输油管道、海底油气管道以及海洋平台都采用了阴极保护技术来提高它们的抗腐蚀能力。
阴极保护经常使用的方法有两种:外加电流阴极保护和牺牲阳极阴极保护。外加电流阴极保护是利用阴极保护原理,将外部使用的直流电源作为阴极保护的极化电源,将电源的负极和被保护的金属管道连接在一起,将电源的正极和辅助阳极连接在一起。通过电流作用,使管道的对地电位向负的方向移动,从而达到阴极保护。牺牲阳极阴极保护是把电极电位比较负的金属材料和电极电位比较正的金属管道连接在一起,将被保护的管道当做腐蚀电池的阴极,以此来实现对金属管道的保护作用,在实际应用中经常使用的牺牲阳极材料有镁、镁合金、锌以及锌合金等[4]。
2.2 内防腐措施
2.2.1 缓蚀剂技术
缓蚀剂是用来延缓金属或者合金被腐蚀并且改变它们的机械性能的化学药剂。它凭借着高效、成本低并且操作简单等优点,目前已经成为防腐蚀技术中应用最为广泛的方法之一,并且经常被用在油田现场。但缓蚀剂的作用机理目前还没有一个大家都认可的说法,现在主要有电化学理论、吸附理论、成膜理论等。缓蚀剂的防腐性能并不是通过改变腐蚀介质中含有的腐蚀成分,而是通过改变金属材料的表面状态或者当作催化剂使用,以此来改变阳极或者阴极的反应过程,使反应速率的常数减小,从而减缓腐蚀速度,以此来达到防腐蚀的目的。
缓蚀剂的使用不仅可以提高设备的使用年限,减少金属材料的浪费,而且可以帮助实现一些先进的工艺流程。随着缓蚀剂技术的广泛应用,缓蚀剂的种类也多种多样。按照化学组成进行划分可以分为无机缓蚀剂和有机缓蚀剂两大类,按照电化学机理可以划分为阳极缓蚀剂、阴极缓蚀剂以及混合型缓蚀剂,按照化学机理可以分为钝化模型缓蚀剂、沉淀模型缓蚀剂以及吸附模型缓蚀剂[5]。
2.2.2 应用内涂层及衬里防腐技术
内涂层防腐技术是指在管道内壁和腐蚀介质之间喷涂隔离层,以此来达到防腐功能。衬里防腐技术是在不同的介质条件下,在金属设备以及管道内衬金属或者非金属材料,将金属表面与工艺介质隔离开来,从而达到防腐效果。对于温度、压力较高的地方,需要衬耐腐蚀金属,如不锈钢、钛、铜等。此外,玻璃钢复合材料也经常用于内衬防腐技术当中,它凭借着自身拥有玻璃钢的耐腐蚀性能和钢管的强度,经常被应用在温度和压力较高的油气集输管道,例如,国内已知的胜利油田就是利用该项技术来进行防腐措施的。内涂层及衬里防腐技术能够有效地防止内腐蚀,因此它被广泛应用于油气集输管道。这样不仅能够有效防止油气管道的腐蚀,避免管道材料的浪费,减少管道的维护费用,而且能够大幅提升油气运输效率,减少对管道的清洗次数,大大节约成本,提高经济效益[6]。
2.3 加强对管道腐蚀问题的检查维护
加强对油气集输管道腐蚀问题的检查维护能够及时发现腐蚀对管道造成的危害,及时保护管道的安全,避免造成安全事故,保护国家的经济效益。
首先,要制定管道防腐蚀计划。例如:在管道建设的初期阶段,就要针对管道的内外腐蚀问题进行处理,利用涂层技术、阴极保护技术、缓蚀剂技术等来对管道内外进行防腐措施,避免管道发生腐蚀。
其次,要制定检查、维修、保养计划,根据计划定期对管道进行检查、维修、保养,如果检查时发现管道有腐蚀问题,就要及时进行维修处理,避免由于腐蚀问题造成管道破裂,引起油气泄漏,从而造成安全事故。
最后,要制定紧急应急计划,万一遇到油气泄漏,工作人员能够根据应急计划进行紧急处理,及时采取有效措施,降低油气对环境的污染,避免油气泄漏引发火灾,造成安全事故[7]。
综上所述,在油气的运输过程中,油气管道可能会发生外腐蚀和内腐蚀这些问题,进而影响到油气的安全输送,造成国家经济损失。因此我们要重视油气管道的腐蚀问题,定期对油气管道进行检查、维修、保养,通过应用涂层技术、阴极保护技术、缓蚀剂技术这些措施来解决管道的腐蚀问题,以此来保证油气的安全输送,保障国家的经济利益。
免责声明:本网站所转载的文字、图片与视频资料版权归原创作者所有,如果涉及侵权,请第一时间联系本网删除。
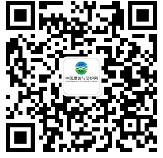
官方微信
《腐蚀与防护网电子期刊》征订启事
- 投稿联系:编辑部
- 电话:010-62316606
- 邮箱:fsfhzy666@163.com
- 腐蚀与防护网官方QQ群:140808414