腐蚀是气井油、套管在使用过程中伴随存在的主要问题,也是影响气田安全开采的制约性因素,失效统计分析表明,气井油管70%的失效与腐蚀相关。针对井筒腐蚀问题,国内外主要采用优选管材、降服役环境低氧含量,添加缓蚀剂、内衬防腐等。 国内某气田气井的主要腐蚀防护措施是周期性加注缓蚀剂。气田进入生产中后期,气井的压力与产能下降,用于增产和腐蚀防护的工艺措施和化学助剂都需要配套实施。 为此,技术人员调研了部分气井的服役情况,对这类气井的增产措施和腐蚀防护措施进行了合理规划,精益管理,降低措施间的干扰,以期保证气井安全运行和高效生产,实现气田高质量发展。 气田开发进入中后期,地层压力下降,边水推进、底水上升。气藏出水后,水会分割气藏,形成死气区,降低气相渗透率,而气体在地层和管柱内流动时的阻力增大,气井产量迅速下降,缩短自喷期,提前进入递减期,降低了气井的采收率。地层水中含有Cl-等腐蚀介质,呈两相或多相流,形成有利于CO2/H2S腐蚀的环境,会对井筒、地面管道和设备造成腐蚀。因此,气井的增产措施与腐蚀防护措施需要同期开展。 根据井型分类,气田会同时使用油溶性缓蚀剂与水溶性缓蚀剂,但是随着气田中后期的生产需求,会加入各类泡排剂,两者间缺乏深度配伍性研究,一旦药剂间性能不匹配或使用不当就会发生相互干扰,这两种药剂的能效均会受到影响。柱塞气举等机械排水措施由于自身结构、工作原理,对井筒光滑度、井内介质均有一定技术要求。且气田随着接续区块的滚动开发,新投气井短时间内压裂液返排不彻底,也会直接影响缓蚀剂的应用。 01 化学助剂间的干扰 缓蚀剂与泡排剂是两种功能不同的化学助剂。缓蚀剂受介质环境、金属表面状态及其他表面活性组分的竞争吸附等众多因素的影响很大。泡排剂则是由一种或多种表面活性剂及其他添加剂组成的复配体系。加入不同泡排剂对缓蚀剂的性能有非常大的影响,配伍性好、适当用量的泡排剂可促使缓蚀剂形成气泡,自发径向运动,并在金属表面形成一层致密的吸附膜,促进缓蚀剂成膜作用,强化CO2吸收效果,提升缓蚀剂的能效。反之则两者的使用能效同时会受影响,甚至在井筒内形成污垢。 缓蚀剂尚未在井筒内彻底完成全吸附成膜功能前,若大量泡排剂瞬间加入,泡排剂就会在井筒内反应并将缓蚀剂一并携带出井筒,严重影响其防护功效。由于缓蚀剂密度略低于水,在泡排剂完成携液任务后加入缓蚀剂,则可以使之顺利达到井筒底部,完成管柱末端成膜作用,提升防护效果。 02 助剂与机械措施间的干扰 气田大规模推广柱塞气举等增产措施,20%以上的气井安装了这一系统。柱塞举升相当于冲程很长的气动泵,油管作为泵筒,柱塞作为活塞,利用本井气或补充气源把柱塞连同液柱一起从井底举升到地面。整个柱塞系统要求油管内径一致且光滑畅通,如果油套管内添加黏性化学剂会增加举升过程的阻力,影响排水效果。 另外,柱塞气举系统管道出口由一个薄膜阀控制,极易由于黏堵而失效。在现场应用的过程中,90%薄膜阀的失效都是由黏性化学试剂造成的。因此,选择应用缓蚀剂时,需要充分考虑黏度对柱塞措施的影响,结合现场试验结果确定缓蚀剂的黏度。 03 新井反排不彻底的污染作用 气田新建气井采用陶粒、石英砂支撑剂、压裂液体系包括低浓度胍胶、VSW、生物胶、EM50等,稠化剂包括聚合物、植物胶等。现场返排过程,虽然基本能够遵照压裂返排制度执行,但7~20天内仅能排出浅层压裂液,深层压裂返排液短时间内不能得到有效返排。若新投产气井在较长时间段内未生产,井内会积存大量压裂液,或在初期生产过程中不断有深层压裂液涌出,污染了井筒环境,影响井筒内缓蚀剂的使用效果。 04 频繁更换缓蚀剂种类的影响 结合以往气田缓蚀剂使用效果,经过现场多年比选应用,季铵盐咪唑啉类缓蚀剂的防腐蚀效果好,负面影响少。但气田缓蚀剂目前采用集采模式,气田气水质特征与缓蚀剂性能评价结果不能紧密结合,未对缓蚀剂提出针对性较强的技术要求,这使得缓蚀剂的采购门槛较低,各类符合标准要求的缓蚀剂基本都能使用。且采购过程中,既未对缓蚀剂的分子构成和基本性能进行要求,也未对缓蚀剂选型、用量作详细区分。这大大增加了缓蚀剂与其他化学助剂发生互相干扰,能效下降的风险,也容易造成部分缓蚀剂供给不足或过剩,形成资源浪费。 01 规范缓蚀剂性能技术标准 针对目前缓蚀剂与泡排剂、柱塞等排水采气措施的供给、应用现状,为了更好适应现场,协调好气井生产与腐蚀防护的技术冲突,发挥各自的最佳功效,气田应利用以往现场缓蚀剂评价试验结果,结合相关标准、规定,总结现场适用的缓蚀剂类型,并进一步细化符合现场使用的缓蚀剂基本性能标准,以作为市场采购的技术依据。从源头保证入井的缓蚀剂不与泡排剂、柱塞气举等排水采气措施发生冲突。同时,采用生产厂家直供现场模式,减少中间领取、配送、存放环节,避免缓蚀剂因长期存放或保管不当产生的失效情况,提升使用效率。 02 优化加注模式、制度 按照气井的气、水产量,井筒腐蚀程度,生产情况,现场加注工艺4个主要方面,缓蚀剂加注制度由原先的“首次预膜,少量、短期、站内推送补充”模式调整成“首次预膜,周期井口加注”。 主要做法是根据气井主要生产层位,结合气井气水质分析,井深结构,腐蚀监、检测结果、对气井划分类型,精益管理。同时利用各生产区块配备的泵车,改变以往站内管线推送模式,采取井口直接加注,降低缓蚀剂损耗,提升利用率。对于新投气井,则密切跟踪新井的气、水质变化,完成首次气井预膜后,根据气井交接、投产时间间隔以及液量变化,及时进行排液处置,之后再次预膜以强化防护效果。 03 协调现场管理 随着气田开发时间的推移,柱塞气举、井下节流器、井下涡流工具等气井增产措施的应用范围将不断扩大,各类在气井井筒开展的试验也越来越频繁,这些项目会对井内介质、环境提出要求。因此,现场在执行缓蚀剂加注制度时,需要与此类气井试验要求紧密结合,规避开气井试验开展时间段,提前或推后完成预膜、补加处理。
免责声明:本网站所转载的文字、图片与视频资料版权归原创作者所有,如果涉及侵权,请第一时间联系本网删除。
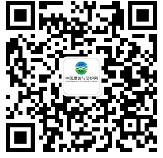
官方微信
《腐蚀与防护网电子期刊》征订启事
- 投稿联系:编辑部
- 电话:010-62316606
- 邮箱:fsfhzy666@163.com
- 腐蚀与防护网官方QQ群:140808414