采用Ansys Workbench有限元分析软件模拟316L不锈钢液控管线在200~350℃下的热应力分布,结合高温腐蚀模拟试验,研究了稠油热采服役环境下液控管线的应力腐蚀行为。结果表明:模拟得到液控管线在200~350℃温度范围内的最大热应力出现在接近油管接箍侧区域,其数值随温度的升高而增大。高温腐蚀模拟后,应力加载状态下液控管线的受拉伸区域出现多条径向裂纹,而无应力加载状态下局部位置存在点蚀坑。液控管线在稠油热采环境中的失效机理是在热应力和腐蚀介质共同作用下,点蚀坑处发生阳极溶解并发展为应力腐蚀裂纹。
1 试样制备与试验方法
试验材料为某海上稠油热采井用316L不锈钢液控管线,管外径为6.35mm,内径为3.75mm,壁厚为1.3mm,其化学成分(质量分数%)为0.03C,0.75Si,2.00Mn,0.045P,0.03S,16.70Cr,10.02Ni,2.03Mo,0.10N,余Fe。为研究应力加载对液控管线在热采服役环境中腐蚀损伤的影响,分别制备应力加载和无应力加载2种状态的试样,其中:应力加载状态下的试样是按照GB/T 15970.3—1995用两步法制作的U 型弯曲试样,其结构如图1所示;无应力加载状态下的试样为长度10cm的直管试样。
采用C276哈氏合金反应釜进行高温腐蚀模拟试验,根据某海上稠油热采井油田采出水的水质分析报告配制腐蚀液,具体组成为9339.8mg·L-1Na+,741.5mg·L-1K+ ,866.5mg·L-1Mg2+,1085.3mg·L-1Ca2+ ,18441.0mg·L-1Cl-,2029.5mg·L-1SO42-,555.4mg·L-1HCO3- 。将2种液控管线试样悬挂于试样架上,试样架通过螺栓固定在高压釜盖上,使液控管线试样完全浸没在腐蚀液中。试验温度为300℃,氧气分压为0.21MPa,试验时间为72h。试验结束后,利用配备有能谱仪(EDS)的扫描电镜(SEM)对试样进行微观形貌观察及腐蚀产物成分分析。采用体积分数10%硝酸溶液对试样进行酸洗后,利用激光共聚焦显微镜对试样表面的腐蚀特征进行观察。
2 有限元模拟
2.1 有限元模型的建立
液控管线通过管线护罩上的限位槽限位在油管接箍上,如图2所示。在高温环境中液控管线受热发生热膨胀,由于油管接箍与液控管线的热膨胀系数不同,且管线护罩对液控管线有限位作用,阻碍液控管线的热膨胀释放,因此在实际生产过程中液控管线会产生沿轴向的热应力,同时也会产生一定的弧度。316L不锈钢在室温(25℃)以及200,260,300,350℃时的屈服强度分别为276,230,215,205,193MPa,泊松比约为0.3。316L不锈钢与N80油管钢(油管接箍材料)的弹性模量和热膨胀系数见表1。油管接箍外壁与套管内壁间距为液控管线在环空中弧的最大变形范围。热采井用套管的内径为205.7mm,外径为219.1mm,通径为202.5mm;油管的内径为100.3mm,外径为120.6mm;接箍外径为141.5mm。由此可以确定,液控管线在环空中弧的最大变形范围为32mm,即模型的最大变形弧的高度为32mm。
表1 316L不锈钢与 N80油管钢的热膨胀系数和弹性模量
根据实际油管长度,定义这段带有弧形的液控管线弦长为10000mm,外径为6.35mm,内径为3.75mm,两端受液控管线护罩约束的部位保持直线,端部直管段长200mm,中部弧的高度为32mm。考虑到液控管线长径比过大,为减小计算误差和提高网格划分精度,按照尺寸10∶1比例建立液控管线模型并利用AnsysWorkbench软件对其热应力进行有限元计算。对模型两端直管段进行完全固定约束,使其自由度为0,对中部位置进行位移约束。由于液控管线的管径较小、管壁较薄,为保证有限元计算结果的准确性及合理性,在网格划分时,采用全局单元尺寸控制网格大小,网格单元为四面体单元,如图3所示。
2.2 有限元模拟结果
目前,国内外许多学者利用 Ansys Workbench软件对管道应力分布进行模拟计算,模拟结果与试验结果吻合较好,有限元模拟的准确性得到验证。在图4中同一温度下的上面模拟结果为液控管线背离油管接箍侧的应力分布云图,而下面模拟结果为靠近油管接箍侧的应力分布云图。由图4可以看出,A1、A2、A3区域为拉应力区域,B1、B2、B3区域为压应力区域,最大拉应力出现在靠近油管接箍侧的A1和A3区域。拉应力是应力腐蚀开裂的必要条件之一。液控管线在200,260,300℃时所受的最大热应力分别为89,127,150MPa,明显低于其屈服强度,因此液控管线维持在较低的弹性变形状态。在350℃时受到的最大热应力为181MPa,约为屈服强度的93%,因此该温度下液控管线整体维持在较高的弹性变形状态。
3 试验结果与讨论
3.1 宏观腐蚀形貌
由图5可见:应力加载状态下的U型试样顶端受拉伸区域出现多条垂直于管轴线的平行分布的裂纹,且被一层稀疏的黑色腐蚀产物所覆盖,而肩部出现少数周向裂纹及腐蚀产物;无应力加载的直管试样整体颜色暗淡,这是由高温氧化所致,同时局部位置发现点蚀坑及腐蚀产物,未发现明显裂纹。这表明,应力对裂纹的萌生和扩展具有促进作用,拉应力可以促使裂纹快速萌生与扩展。直管试样表面腐蚀产物分布不均匀,出现堆积现象。
3.2 微观腐蚀形貌
由图6可以发现:应力加载状态下的U型试样表面腐蚀产物分布均匀,主要成分为金属氧化物,且氧化物间隙夹杂部分矿物盐;无应力加载状态下的直管试样的成分与应力加载状态下的差别不大,但氯离子含量明显较高。这是因为应力加载导致液控管线表面钝化膜出现大面积破损而发生腐蚀,而无应力加载状态下的直管试样仅在局部位置发生点蚀,氯离子在点蚀坑内富集。对比发现,应力加载状态下的液控管线出现大面积的腐蚀,腐蚀程度更严重。
由图7可以看出,在酸洗后应力加载状态下试样表面出现明显的径向裂纹,无应力加载状态下试样表面较平整,未发现裂纹。这表明,应力加载能够促进液控管线表面裂纹的形成,并加快液控管线的腐蚀失效。
3.3 应力腐蚀机理
研究表明:模拟得到U型试样顶端位置的拉应力在279~318MPa,大于300℃时316L不锈钢的屈服强度;肩部位置的拉应力在140~279MPa,由有限元模拟得到的最大热应力处于该应力范围。在高温高压腐蚀模拟试验后,U型试样直管段的腐蚀程度较轻,而顶端和肩部出现多条垂直于管轴线的裂纹。研究表明,在温度低于300℃时,随着温度的升高,316L不锈钢的抗拉强度逐渐降低,但温度升高到550℃后,抗拉强度基本保持稳定,这主要是由动态应变老化导致的。316L 不锈钢在300℃下的抗拉强度约为500MPa,显著高于该温度下U型试样顶端位置的最大拉应力,这说明316L不锈钢液控管线在300℃高温环境中的失效并不是因为高应力导致的纯力学失效,而是应力与腐蚀性介质共同作用的结果。
应力腐蚀机理与腐蚀过程中的阳极反应和阴极反应有关,主要分为阳极溶解机理和氢致开裂机理两大类。阳极溶解机理是指金属局部产生微裂纹后,表面未破损区成为阴极区,裂纹侧面和裂纹尖端组成阳极区,从而形成“大阴极、小阳极”的电化学腐蚀过程。该机理适用于自钝化金属;裂纹两侧受钝化膜保护,造成裂纹尖端溶解速率加快,最终导致金属发生断裂。氢致开裂是指由于金属在腐蚀过程中产生的氢原子在金属内部缺陷处聚集,产生局部压力,使液控管线发生脆化,从而在拉应力作用下发生断裂。由于热采井环空中不含酸性气体,呈近中性,因此热采井下液控管线的开裂机理为阳极溶解机理。不同应力加载状态下316L不锈钢液控管线在高温环境中的腐蚀失效机理如图8所示。在高温高氯蒸汽环境中,无应力加载状态下的液控管线表面钝化膜在氯离子侵蚀下发生破损(高温环境会加剧表面破损程度),破损区露出的新鲜基体发生阳极溶解,逐渐发展成点蚀坑。在拉应力加载作用下,点蚀坑继续发展,点蚀坑内的局部应力逐渐增大,当局部应力等于或大于临界值时,应力腐蚀裂纹从点蚀坑内萌生。一方面,裂纹尖端在自催化作用下继续溶解,腐蚀介质中的氯离子受电荷转移作用在裂纹尖端处富集,形成局部酸化区,促进裂纹的扩展;另一方面,裂纹在拉应力作用下加速扩展,形成径向裂纹。因此,316L不锈钢液控管线在稠油热采服役环境中的失效机理主要是在热应力和腐蚀介质共同作用下,点蚀坑处发生阳极溶解并发展为应力腐蚀裂纹。
4 结 论
(1)模拟得到316L不锈钢液控管线在200~350℃温度下的最大热应力出现在接近油管接箍侧区域,其数值随温度的升高而增大,在350℃时的最大热应力为181MPa,约为屈服强度的93%。
(2)在模拟热采环境中,应力加载状态下316L不锈钢液控管线的受拉伸区域出现多条径向裂纹,表面腐蚀产物分布均匀,腐蚀程度严重。无应力加载状态下液控管线局部位置存在点蚀坑,表面腐蚀产物分布不均匀,腐蚀程度较轻。拉应力加载促进高温环境液控管线表面裂纹的形成,并加快液控管线的腐蚀失效。
(3)316L不锈钢液控管线在稠油热采服役环境中的失效机理主要是在热应力和腐蚀介质共同作用下,点蚀坑处发生阳极溶解并发展为应力腐蚀裂纹。
免责声明:本网站所转载的文字、图片与视频资料版权归原创作者所有,如果涉及侵权,请第一时间联系本网删除。
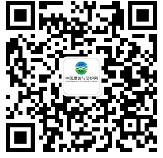
官方微信
《腐蚀与防护网电子期刊》征订启事
- 投稿联系:编辑部
- 电话:010-62316606
- 邮箱:fsfhzy666@163.com
- 腐蚀与防护网官方QQ群:140808414