海洋钢结构包括海上风机、跨海大桥、海洋采油平台和海港码头等,这些钢结构长期暴露在海洋大气中或浸没在海水中,为腐蚀的发生、发展创造了条件。我国是一个海岸线长达3.2×104 km的海洋大国,每年各种海洋工程的维护和防腐花费巨大。2014年,我国各个行业的腐蚀总成本为21 278.2亿元,占GDP的3.34%,人均腐蚀成本为1 555元[1]。因此对海洋工程采取有效、经济、简单长期的防腐措施显得尤为重要,本文根据我国海洋钢结构防腐技术应用现状和各种技术的优劣势和进行阐述,并对海洋钢结构防腐蚀技术的发展提出了建议。
根据海洋钢结构暴露条件的不同,可将海洋腐蚀环境划分为5个区带,分别为海洋大气区、浪花飞溅区、海水潮差区、海水全浸区和海底泥土区。由图1可以看出,浪花飞溅区腐蚀速率最高,是工程防护的关键区域。
1.1 海洋大气区腐蚀
海洋大气区是海洋表层以上的大气部分,该区域的特点是海洋钢结构无法直接与海洋接触,但由于海洋大气的湿度大,氯离子含量高,并且具有干湿循环显著的特点,所以该部分海洋钢结构的腐蚀速率比内陆环境高4倍左右。
高湿度的大气会增强钢结构表面的毛细吸附作用,增加水蒸气的凝聚速率,为电化学腐蚀提供了基本环境,并且空气中的盐分(主要是氯离子)含量高,极易溶解在钢结构表面的水膜里,加上大气中CO2和SO2进入水膜中,形成良好导电性的酸性电解质,这些都为海洋大气区的腐蚀创造了有利条件。另外海洋大气区的钢结构一般都受阳光直射,温度较高,大大加快了钢结构的腐蚀,金属表面真菌和霉菌的繁殖也提供了酸性湿润的环境,因此海洋大气环境下钢结构防腐比内陆环境更为严峻与苛刻。
1.2 浪花飞溅区腐蚀
浪花飞溅区是5个腐蚀区里腐蚀最严重的区域,拥有和大气区类似的外部环境,不同的是浪花区存在海浪飞溅,导致该区域的盐分、湿度都远高于大气区,随着浪花的拍打,自然干燥,实现了频繁的干湿循环,加上该部分钢结构与空气接触密切,提供了丰富的氧气,这些都为钢结构的腐蚀提供了条件。
除此之外,浪花飞溅区还发生气泡腐蚀、任意性腐蚀和均匀腐蚀。飞溅区海浪的冲击压缩产生大量气泡,气泡对钢结构的腐蚀严重,钢结构表面的涂层会在气泡的冲击下加快破损老化,从而进一步加速腐蚀;而任意性腐蚀发生的原因是海浪会带来各种各样的物质,如金属物质、酸性物质,因此浪花飞溅区钢结构的各部分腐蚀程度也不尽相同;该区域还会产生一种难以区分阴阳两极的均匀腐蚀,这些方面综合导致浪花飞溅区钢结构腐蚀最严重。
探究气泡腐蚀的本质对浪花飞溅区腐蚀防护具有重要意义,目前,国内外普遍认为锈层参与了阴极极化这一观点[3],认为这是加快浪花飞溅区腐蚀的关键,但是具体原因仍然是探究热点。
1.3 海水差潮区腐蚀
海水差潮区的特点是随着海水潮起潮落的周期变化,海洋钢结构也进行着浸没、暴露的周期变化,海洋钢结构伴随这一特点进行着稳定的干湿交替,干湿交替的周期变化会形成类似大气区钢结构表面的水膜,氧气的扩散比浪花飞溅区更慢,受温度的影响很大,同时海水的周期变化也不断冲击着钢结构的表面,发生大量气泡腐蚀,破坏钢结构表面涂层,除此之外,海洋生物也能附着在此区域的钢结构上,产生低氧环境形成氧浓差电池,这些都加速了海水差潮区钢结构腐蚀。
1.4 海水全浸区腐蚀
海水全浸区是指海洋钢结构在海水中完全浸泡的区域,不随海水的潮起潮落暴露在大气中。海水全浸区可分为3个区域,这3个区域的腐蚀速率由大到小分别是浅海区、大陆架全浸区、深海区。浅海区的氧气充足,几乎处于饱和状态,存在这一部分的海洋生物更活跃,该区域主要发生电化学腐蚀和生物腐蚀,由于造成腐蚀的因素更多,浅水区的腐蚀比大气区更为严重;大陆架全浸区与浅水区相比水流流速,含氧量水温等都有所下降,这些条件不利于生物的生存,所以该部分生物腐蚀大大减少,海洋钢结构的腐蚀还是以电化学为主,物理化学腐蚀为辅;深海区由于较大的压力,盐分的溶解量变少,钢结构腐蚀以应力腐蚀和电化学为主,属于海水全浸区中腐蚀最轻的部分。
1.5 海水泥土区腐蚀
海水泥土区是指海洋钢结构埋藏于海底沉积物的部分。这部分海洋钢结构由于氧气含量低,是整个海洋腐蚀区腐蚀最慢的部分。海水泥土区的腐蚀环境较为复杂,他具有土壤和海水腐蚀的双重特点,海底沉积物中存在大量的硫酸盐还原菌,这些硫酸盐还原菌产生的硫化物会加速钢结构的腐蚀,细菌产生的NH3和H2S也会促进钢结构的腐蚀,这一部分主要发生电化学腐蚀和微生物腐蚀,是海洋腐蚀区带中腐蚀速率最慢的部分。
海洋钢结构防腐涂料主要包括船舶涂料、集装箱涂料、桥梁涂料以及码头钢铁设施、石油管道、海洋平台等大型设施的防腐涂料。例如,根据大榭第二大桥的防腐措施[4],斜拉索的防腐采取多层防护体系,其索体采用镀锌钢丝,单根拉索包裹双层热挤高密度聚乙烯护套,使用耐候钢并经电弧喷铝防腐,不同部位采用不同涂层或不同技术,体现了现代海洋防腐的高要求。
这些涂料分为有机涂料、无机涂料,他们是保护钢结构不被腐蚀的有效手段,但是作为海洋钢结构表面涂料,应比内地钢结构涂料的标准更为严格,对钢结构表面处理要求更高,还要满足在海水的长期冲刷下,钢结构表面涂层不发生鼓泡破损现象。
目前海洋钢结构防腐涂料的发展已经取得了长足进步,但是在某些方面还需要改进和加强。海洋防腐涂料的种类繁多,基础的环氧类涂料、乙烯类涂料、富锌类涂料等,新兴的石墨烯防腐涂料、纳米涂料等,这些涂料在海洋防腐形势日趋严峻的背景下都具有重要意义。
2.1 环氧类涂料
环氧类防腐涂料以环氧树脂为基础的一类涂料的总称,他通过加入各种填充涂料、添加剂、助剂和改性剂(主要是长效氯磺化聚乙烯橡胶)等,改良环氧涂料的性质,使其附着力增强,强度提升,并提高环氧涂料的耐腐蚀性、耐渗透性,得到符合工程建筑防腐标准的材料。
目前环氧防腐涂料由于其制作简单经济,被广泛应用在桥梁、船舶、海洋平台、水下涂料、港口等钢结构中,是应用最广的海洋重防腐涂料,但应用最广泛不意味着该种材料没有缺点,延展性问题是该涂料的突出问题。针对这一问题,曹慧军等[5]通过改性的高固体环氧涂料,使其具有了良好的延展性,王雪莹[6]也通过向传统环氧涂料中添加不同粒径的陶瓷粒,得到了优良延展性和优良耐海水的环氧陶瓷涂料。现阶段也有将石墨烯添加到普通的环氧防腐涂料中,借此得到类似环氧富锌涂料和玻璃鳞片类涂料优秀性能的涂料,使新型环氧涂料具有阴极保护功能、屏蔽功能和较好的耐腐蚀性能,提高了涂层的耐磨性和附着力,延展性也有了长足的进步,其防腐蚀效果好于现阶段大部分船用重防腐涂层。
除了解决环氧类防腐涂料的延展性问题,还要增强涂料在关键部位的附着力。螺栓、法兰等关键节点的表面处理比较困难,环氧类防腐涂料的附着力不能满足实际海洋钢结构的防腐需求,因此未来此类涂料的发展可以基于材料本身,增强本身的附着力能力,也可以基于表面处理方法,使关键节点的处理得到简化优化。另外,环氧类涂料不再是单纯的环氧材料,添加任何材料都有可能使其具有更优秀的防腐特性,通过大量的实验得到最优秀的配方也是目前的主要方向。
2.2 石墨烯防腐涂料
石墨烯防腐涂料作为一种新型防腐涂料,主要有纯石墨烯涂层和复合石墨烯涂层2种。纯石墨烯防腐涂料由于其性质单一,基本不能满足海洋钢结构的防腐需求,复合石墨烯涂料由于其复合了各种材料,改良了纯石墨烯的防腐特性,能较好适应目前海洋钢结构防腐蚀环境。
但是目前大部分的研究都是将石墨烯添加到其他材料中,作为一种辅助材料。石墨烯具有良好的化学稳定性和热稳定性,可以在海面大气中反射太阳光,避免紫外线对涂料的老化影响,另外,研究表明,在其他涂层中添加适量的石墨烯可以提高涂料的整体防腐蚀性能,具体应用体现在向环氧富锌涂料和水性防腐涂料中添加石墨烯能够有效的降低涂层厚度,增加涂层与基体之间的附着力,提高防腐涂层的耐磨性及抗老化性等。徐菲桐[7]将PF-127加入石墨烯中,制备出分散性良好的石墨烯分散液,将其加入到水性环氧涂料中,得到附着力更强、耐海水腐蚀性能和耐中性盐雾腐蚀性能更好的水性复合石墨烯防腐涂料,具有广阔的应用前景。
石墨烯防腐涂料的研究将是未来的研究热点,不管是将石墨烯作为辅助材料还是基础材料,研制出制造方便、经济的石墨烯涂料显得尤为重要,另外石墨烯作为添加剂的分散方式过于费时费力,合适便捷的分散方法也可以大大提高制作和研究石墨烯材料的效率。
2.3 乙烯基涂料
乙烯基涂料包括乙烯基鳞片涂料、聚乙烯涂料、乙烯基树脂涂料等,在此基础上还有厚浆型的乙烯基涂料,乙烯基涂料具有突出的耐腐蚀性、长期耐候性和优异的疏水性,近几年已被国外广泛应用。目前国外乙烯基涂料在海洋军舰和海洋钢结构上应用很多,但是我国对于乙烯基涂料的研究还停留在用于汽车等结构的防腐,几乎没有应用在海洋防腐领域里。
根据国外研究将乙烯漆涂在钢结构涂层厚度达到300 μm,就能有12年的防腐蚀效果。我国在该领域的研究中,孙超等[8]以酚醛环氧乙烯基树脂为主要成膜材料,优化了耐热填料与玻璃鳞片的配比,使涂层在180 ℃下具有优异的机械性能和良好的耐腐蚀性能,可应用于酸性海洋环境。万浩[9]将其制备的乙烯基丙烯酸聚氨酯疏水防腐涂层浸泡在3.5%NaCl溶液中,浸泡的前24 h内涂层具有较好防护性能,浸泡101 h后介质透过涂层开始对金属基体产生腐蚀,可以发现现阶段增强乙烯基涂料长效保护是主要目标。
乙烯酯玻璃鳞片涂料和酚醛环氧是涂装脱硫塔最合适的选择[10],但是运输储存施工对温度要求严格,如何减少这种运输储存成本与风险也是未来发展的方向。另外乙烯基涂料在我国也具有较大研究价值,利用乙烯基涂料的优异疏水性,广泛应用在海洋钢结构上,实现海洋钢结构防腐涂料的多样化。
2.4 玻璃鳞片涂料
玻璃鳞片涂料以树脂为主要成膜材料,由于主要填充材料为玻璃鳞片,故这类涂料具有较强的耐腐蚀性、优异的耐候性和良好的抗渗性,玻璃鳞片在涂料中的作用过于突出,因此单独将其归为一类。
然而,由于添加了玻璃鳞片,玻璃鳞片与树脂的相容性差,必须对玻璃鳞片进行处理。宋玉强[11]将甲苯-2,4-二异氰酸酯、六亚甲基二异氰酸酯和Y -(2,3-环氧丙基氧基)丙基三甲氧基硅烷作为活性桥接剂,制备了3种表面活化接枝玻璃鳞片,这些材料可以解决玻璃片与树脂相容性差的问题。当然这是解决问题的一种思路,不局限于只处理玻璃鳞片。殷勇[12]通过材料聚氨酯一脲、腰果油改性酚醛胺树脂、刚玉粉,改良原本玻璃鳞片材料,开发出具有良好相容性的高性能玻璃鳞片涂料,该涂料可凭借其优良耐化学介质性能、耐老化防腐性能、平衡的施工性和经济性,完全适用浪花飞溅区和海水潮差区。
目前关于玻璃鳞片涂料改性的研究并不多,但是都反映出玻璃鳞片制备出的涂层差异性较大,如何解决这种差异,合理控制这种差异是制造玻璃鳞片类涂料亟需解决的问题。
2.5 聚氨酯防腐蚀涂料
聚氨酯防腐涂料最突出的特点是优异的耐酸碱盐性,因聚氨酯是由氨基甲酸酯键、轻基、异氰酸酯键等官能团组成,其耐腐蚀能力和耐候性都表现良好,常规力学性能也显著由于其他涂料。聚氨酯涂料目前被广泛应用在海洋钢结构上,海上作业平台,船舶桥梁等工程的防护面漆。
聚氨酯防腐涂料是一种高固型、低VOC含量的涂料。随着涂料的环保绿色化,开发高性能水性、高固型、低VOC含量的聚氨酯防腐涂料是未来的发展方向。此外,改性聚氨酯类重防腐涂料也可以开发和使用在恶劣的环境,如船舶,航空航天,核电设施,发展环保型水性聚氨酯防腐涂料和高固体聚氨酯防腐涂料也将成为未来的发展方向之一。
2.6 富锌防腐蚀涂料
富锌防腐蚀涂料是以环氧树脂和聚氨酯树脂为主的防腐涂料,通过以锌粉为主要填充物,使该类涂料具有优异阻锈性能,较好的附着力和较低的表面能。富锌防腐涂料广泛的应用在桥梁、船舶以及大型的钢结构设备上,富锌防腐涂料是一种优秀的底漆,可以发生电化学反应从而达到防腐蚀的目的。
唐文剑等[13]研究并设计了醇溶性有机/无机复合树脂。通过添加片状锌粉,制备了应用于重防腐领域的醇溶性富锌防腐涂料。这种涂料对环境的影响较小,又具有良好的抗腐蚀效果,符合当下环境保护的潮流。为了克服富锌防腐涂料起泡失效的缺点,赵书彦等[14]制备了纳米SO2复合环氧富锌纳米涂层。该涂层附着力好,前期可作为有机屏蔽层,中期可发挥温和的阴极保护作用,且持续时间长,后期Zn的反应产物可提供良好的屏蔽和耐腐蚀性能。但是富锌类防腐涂层的材料并不是防护的唯一要求,锌粉含量,施工温度,涂层厚度等都是影响防腐蚀效果的重要因素,利用合理的配方设计和合适的施工环境,水性环氧富锌底漆防腐蚀性能就可以达到溶剂型环氧富锌涂料相同的水平[15];锌粉含量越高防腐效果越好,但是柔韧性越差;膜厚度需要试验寻求一个最佳的厚度,过薄过厚都影响涂料的防腐蚀效果;温度越高,涂料的干燥时间越短。
富锌涂料目前已经广泛应用到了海洋钢结构的防腐,各种研究应用已经有了很好的基础,未来的涂料低污染无污染是第一位的,开发环保节能高效的富锌防腐涂料是有效利用其的关键。
2.7 丙烯酸防腐蚀涂料
丙烯酸防腐涂料是一类以丙烯酸树脂为主要成膜物的涂料。这类涂料具有耐水性、耐腐蚀性、绿色环保、固化速度快等性能优点,但是丙烯酸防腐涂料的防腐作用一定要添加合适的添加剂、助剂才能起到较好的防腐蚀作用,利用氧化石墨烯对水性丙烯酸防腐涂料进行改性,使原有丙烯酸防腐涂料的防腐效果得到显著提高[16]。
目前,丙烯酸涂料大多采用丙烯酸改性法制备,制作周期较长,不利于该种涂料的广泛使用,所以通过其他手段高效经济的合成丙烯酸涂料,缩短丙烯酸涂料在海洋钢结构中应用的周期是对其有效利用的关键。
2.8 橡胶防腐蚀涂料
橡胶防腐涂料是一类以合成橡胶或天然橡胶衍生物为主要成膜物的涂料。该类涂料无毒、无味、无刺激性,并具有较好的耐腐蚀、耐磨、耐水、耐候性,且干燥速度快。目前,氯化橡胶涂料和氯磺化聚乙烯涂料是最常用的橡胶防腐涂料。
美国杜邦化学公司还使用氯丁橡胶来防止海上采油平台支柱和套管的腐蚀,使用后耐久性高达15~35年。然而,橡胶防腐蚀涂料的附着力和耐候性不是特别理想,李石等[17]利用环氧树脂、醇酸树脂改性氯化橡胶,附着力和耐候性能得到显著提高。
虽然橡胶涂料具有良好的性能,但目前大部分橡胶涂料仍使用四氯化碳作为溶剂,而四氯化碳并不环保。因此,开发一种新型的绿色环保溶剂是橡胶涂料发展的难点和热点。
2.9 有机硅树脂防腐蚀涂料
有机硅树脂防腐涂料是一类以有机硅树脂或改性有机硅树脂为主要成膜物的涂料。该类涂料具有优良的耐候性、防霉性、耐腐蚀性、电气绝缘等性能,主要用于管道、容器等产品的防护面漆。现有研究都是增强了有机硅树脂的耐热性等特性,没有专门针对海洋钢结构应用方面的研究。庞玉宁[18]利用自制的有机硅聚合物与环氧树脂E-20,孙乾坤等[19]利用有机硅中间体与树脂E-44,都制备出了具有耐热性好,附着力不错的有机硅树脂防腐涂料,可以应用在海洋钢结构中例如海洋石油钻井平台等温度较高的部位。目前该涂料的附着力还有待提高。
2.10 纳米复合涂料
纳米复合涂料是一类由纳米级材料和其他防腐材料复合而成的涂料。通过对纳米级涂料的选择,使新型复合涂料具有高强度、高韧性和高硬度等特点。目前用于涂料的纳米粒子主要有金属氧化物(如TiO2,Fe2O3,ZnO等)、纳米金属粉末(如纳米Al,Co,Ti,Cr,Nd,Mo等)、无机盐类(如CaCO3)和层状硅酸盐(如一维的纳米级黏土)。
纳米粒子填充涂料具有优异的耐候性、装饰性、抗污染和抗菌性能,完全符合当代环保的要求。作为一种特殊的涂料,纳米复合涂料具有很高的应用价值,是21世纪最有前途的涂料之一。选择合适的复合材料需要大量的实验研究。曹祥康[20]通过石墨烯纳米片对环氧富锌进行改性处理,制备出可以提高阴极保护时间和屏蔽效果的材料,添加合适的石墨烯纳米材料可以增强环氧富锌涂层缺陷部位的抗剥离效果。然而,要使纳米技术在涂层中得到广泛应用,还需要解决纳米粒子在涂层中能否稳定分散、纳米粒子添加量等关键技术问题。纳米粒子在涂料中的稳定分散直接关系到纳米粒子能否改善涂料的性能,纳米粒子的加入量也会影响粒子之间的团聚,从而影响腐蚀性[21]。
虽然无机纳米材料改性无机防腐涂料的研究取得了一定进展,但如何更好地改善无机纳米材料与聚氨酯的完全相容性,无机纳米材料的组成与聚氨酯防腐性能的关系,除了无机纳米材料的均匀分散外,还有哪些其他因素可以提高聚氨酯耐腐蚀的防腐性能,这些问题还没有得到明确的解释,因此,如何解决上述问题将是今后聚氨酯防腐涂料发展的重点。
2.11 自分层涂料
自分层涂层明显优于传统涂层。它们利用极性、分子相互作用和在不同树脂介质中溶解度的差异,在干燥固化过程中,随着同一成膜树脂的两相组成和界面的变化,张力的变化导致两相相对流动,进而导致树脂相分离,形成梯度层状结构。
凭借这一特性,自分层涂料可以一次涂装形成多涂层体系,可节约涂料,降低涂装成本;在综合多涂层优点的同时,提高了涂层之间的附着力;能更好地兼顾涂膜的柔韧性和硬度等相互矛盾的特性,增强防腐蚀性能;能选择性地渗透到多孔基体中,提高附着力的持久性;还可以改善表面性能,如提高光泽度、耐磨性、抗流挂、耐化学品性、耐光性、耐候性等。
在水性自分层涂料中,水性氟硅涂料是最具发展前景的海洋涂料之一。随着氟树脂的使用,基层会表现出较好的附着力,且表层具有极低的表面能,这种极低的表面能和极强的疏水性使一般污染物难以附着,一般藻类和细菌难以着床发育繁殖,使得涂层的抗菌、防霉、防藻和抗污染性能大大提高,同时,以氟树脂为主的表面,使涂层具有较高的耐候性。
可见,自分层涂料是一种优良的防腐技术。通过大量的研究数据,可以建立预测涂料分层行为的计算模型,并对适合工程应用的自分层涂料进行合理配置。目前的研究主要集中在热塑性树脂和挥发性有机溶剂为基础的涂料树脂方面。目前对水性聚合物涂料的研究还比较少,还没有涉及对水性电泳涂料的研究。由于自分层涂料可以省去中间层涂料,从而减少施工步骤,获得优异的性能涂料,这是船舶涂料应用的理想效果,这为彻底解决涂料附着力问题提供了一个思路。
金属喷涂保护的方式有很多,包括热喷涂、冷喷涂和电弧喷涂等。金属喷涂技术可以起到物理屏蔽作用,即使破损也可以发生阴极保护,因此金属喷涂广泛被应用在海洋全浸区。
国家标准GB/T 19355-2003《钢铁结构耐腐蚀防护锌和铝覆盖层指南》[22]推荐温带海水中涂层第一次维修寿命要超过20年,采用封闭热质涂铝涂层平均厚度(最低)要达到150 μm,热喷涂锌涂层平均厚度(最低)要达到250 μm。在海洋环境中,喷锌层的使用寿命通常与其厚度成正比,镀锌层的厚度要比铝层厚很多,才能达到相同的耐腐蚀年限。电弧喷涂铝基涂层技术可以解决电化学阴极保护难以有效实施、有机漆膜易老化、贵金属保护层成本过高等问题。铝基涂料具有良好的耐海水腐蚀性能。在未来,该技术可与抗生物污染的封孔涂层结合使用,有望应用于腐蚀和生物污染并存的水下设施和大型海上建筑水下部分的防腐[23]。
我国水利水电行业中几乎所有的钢结构热喷涂防腐工程都使用了涂料。应该指出的是,涂料的使用对孔洞起到了一定的密封作用,但并没有完全封闭金属涂层的孔洞,导致腐蚀介质渗透到基底,从而引起其腐蚀,目前该技术在海洋钢结构的使用上非常苛刻,铝金属的喷涂更为困难,关键部位不能完美喷涂[24],因此衍生出冷喷涂技术,冷喷涂涂层的无氧化、高纯度造就了冷喷涂的发展潜力,大力发展冷喷涂技术,使技术简单方便使现如今的主流。另外需要解决的问题还有降低涂料的粘度和增加涂料本身的密实性。
矿脂胶带包覆防腐体系由防腐膏、防蚀带、外防护剂3个紧密相连的保护层组成。该防腐技术主要应用于港口码头、钻采平台、海上风电、跨海桥梁、埋地管线、船舶设备、混凝土桩、沿海电厂等。包覆技术能被推广应用的原因有很多,矿脂包覆技术凭借其对钢结构表面处理要求低,可以应用在各种复杂结构等优点,已被证实是一种长期有效的针对浪花飞溅区的防腐蚀方法。
侯保荣[25]研制了一种氧化聚合型包覆防腐蚀技术,这种技术主要应用于海洋大气区钢结构的防腐,包括码头、沿海钢结构焊接位置、跨海跨江大桥钢索等。侯保荣等[26]研发的复层矿脂包覆防腐技术对暴露于海洋浪花飞溅区部位的钢铁设施具有广泛的适用性。而陈君[27]一种新思路也值得大家借鉴,他通过吸水材料引入电解质(海水)将牺牲阳极保护法用于浪花飞溅区,得到短期的防腐效果较好,但还需在实海环境中进行更长时间的检验。目前,包覆防腐技术在日本、英国等沿海国家得到成功应用,使用寿命己超过30年。
当然,目前的包覆防腐技术也存在一些缺点:施工工序较多;不易制备防锈油脂;大型、异型玻璃钢模套的预制加工及施工成本较高。美国的CCI防腐套的价格为400美元/m2,英国的DEN-SO防腐蚀缠带和日本的PTC保护修复技术的价格在2 000元/m2左右,这大大超出了我国海洋石油生产部门的承受能力[3]。
所以,从涂料技术层面简化施工工序,研制简便防锈油脂制备方法,包覆技术配套产品的经济化是当前任务的重中之重。
阴极保护技术是海洋钢结构在海水全浸区的主要防腐办法。在我国,铝合金牺牲阳极和外加电流阴极保护技术在海洋钢结构防护中已得到了广泛的应用。阴极保护中应用最广泛的阳极有镁阳极、锌阳极和铝阳极。其中,镁阳极在钢材上的驱动电压较大,多用于土壤介质中;锌阳极的驱动电压比镁阳极低,但电流效率高,故可用于土壤和水介质中;铝阳极主要用于船舶和海洋工程及港口建设领域,但是铝阳极容易污损失效。这些结论都是一种依据经验的估计,这种估计在某种程度上也不能保证选择材料和用量的准确。因此郭宇[28]自主开发了阴极保护电位数值仿真软件,该软件克服了以往商业软件仿真模型建立方式唯一性和模型不通用性的缺陷。仿真结果的输出形式多种多样,可以对多种阴极保护方法的保护电位进行数值仿真,便于操作和工程实际应用。
实际海洋钢结构工程中,铝的使用量非常巨大,制造用于阴极保护合成金属合金时消耗能量巨大,为了可持续发展,高聪等[29]在对平台导管架阴极保护设计中,采用长直翼型阳极或长斜翼型阳极来代替传统的方形阳极,在满足初始阳极电流需求的情况下,可以大大降低实际阳极重量,从而达到节省材料的目的,从而节约能源,节约材料。同样的阴极保护防腐蚀方法,“因地制宜”也不失为之中很好的方法,郭明[30]在原油储罐沉积水侧采用牺牲铝阳极进行阴极保护,而在原油储罐土壤侧采用外加电流进行阴极保护,套管穿越处采用牺牲带状镁阳极进行阴极保护,通过几种方法的局部使用使整体达到了很好的防腐蚀作用。
阴极保护技术现如今已经发展的比较成熟了,我国已经可以通过计算机远程控制阴极保护的参数,继续研究适合海洋钢结构防腐蚀的阴极保护电脑系统,新型阳极研究也将成为研究热点。
我国海岸线长,横跨各个气候区,因此防腐任务任重道远。短效高污染的防腐涂料或技术将会被逐渐淘汰,单一的涂料或技术也无法满足复杂多样的气候条件,因此为了改善我国海洋钢结构的现状和目前的问题,提出几点建议。
长效经济环保发展是海洋防腐的内在要求。涂料普遍30~40年的使用年限已经无法满足日益增长的防腐需求,应该以50年为限,超过50年,且要避免海洋防腐蚀涂料防护性能的单一化,提高防腐蚀涂料的综合性能;发展简单经济的防腐技术,使防腐操作不再专业化;生产、使用符合GB/T 35602-2017《绿色产品评价——涂料》标准的防腐涂料或技术,将无溶剂粉末型、无溶剂常温固化型、低VOC和高固型的海洋防腐蚀涂料作为研发的重点,制定高水准的涂料标准。
另外,多元化的防腐策略也可为我国海洋防腐蚀强国战略提供支持。在涂料的配置和金属的冶炼过程中,资源浪费和能量的过度消耗是主要问题之一,合理利用海洋的可持续能源,如潮汐能等也是解决问题的关键,这也要求我们因地制宜,思维不局限于思维不局限于发展已经存在的技术,同时也要积极开发其他领域,能达到同等甚至效果更好的防护,如冷喷涂技术,将涂刷涂料技术转变成喷涂技术都是可以考虑的方面,通过技术联结或是材料的联结合理有效地发挥海洋钢结构防腐蚀作用,实现我国海洋防腐蚀强国战略。
免责声明:本网站所转载的文字、图片与视频资料版权归原创作者所有,如果涉及侵权,请第一时间联系本网删除。
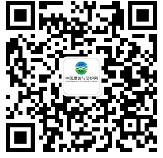
官方微信
《腐蚀与防护网电子期刊》征订启事
- 投稿联系:编辑部
- 电话:010-62316606
- 邮箱:fsfhzy666@163.com
- 腐蚀与防护网官方QQ群:140808414