轻金属通常是指相对密度在4.5以下的金属,主要包括铝、镁、钛等金属。 伴随着国民经济和国防现代化的发展 ,轻金属材料的应用越来越广泛 。镁合金被誉为“21世纪的绿色工程材料”,是目前最轻的金属结构材料,具有密度小、比强度和比刚度高、阻尼减振性好、导热及电磁屏蔽效果佳、机加工性能优良、零件尺寸稳定 、易回收等优点。广泛应用于航空航天、国防、汽车工业、电子通信、医疗及一般民用产品等行业。
我国是镁资源大国,在镁及镁合金工业应用方面拥有得天独厚的优势。然而在国内,镁合金的应用现状和预期仍然存在巨大的差距,这是因为镁及镁合金还存在一些固有缺点,如镁合金化学和电化学活性很高,耐腐蚀、耐磨性较差等,很大程度上制约了镁合金的开发和应用。因而,在目前全球环境恶化和资源短缺问题日益严峻的压力下,加强对镁合金耐蚀耐磨性能的研究,积极探索提高镁合金耐蚀性能的方法途径,对拓宽镁合金的应用范围并充分发挥其性能优势有着十分重要的现实意义。
通常而言,控制镁合金的成分,合理控制材料制备工艺,可以改善镁合金的综合性能,但会使生产成本大幅增加。由于金属材料的腐蚀、磨损和疲劳断裂等材料的失稳多始于表面,因此通过对材料表面处理可进一步提高镁及镁合金的使用特性,具有显著的经济和社会效益。镁合金常用的表面处理工艺主要有电镀、化学转化、阳极氧化、气相沉积、微弧氧化、激光表面处理等。
镁合金:向金属镁中加入少量的其他金属 ,如铝、锌、锰、锆等元素时,形成以镁为基的合金,即镁合金,可以大大提高镁合金的强度,因此用于结构材料的一般为镁合金。密度≈铝的2/3,钢的1/4,是目前最轻的金属结构材料;镁合金还具有比强度高、导热导电性能好、阻尼减振、电磁屏蔽、易于机械加工和容易回收等优点,
由于镁化学性质和电化学活性高,在大气中特别是在潮湿和沿海地区很容易受到腐蚀这限制了镁合金的广泛应用。控制镁合金的成分和形成均匀的组织可以提高镁合金的抗蚀 ,但镁合金的最终腐蚀防护常需要进行表面处理,以便改善镁合金的性能,扩大镁合金的应用领域,提高镁合金材料的使用寿命。
金属镁的应用主要集中在镁合金生产 、铝合金生产 、炼钢脱硫、稀土合金、金属还原、腐蚀保护及其他领域。如很多钢厂都采用镁脱硫,使用镁粒的脱硫效果 比碳化钙好。使用镁牺牲阳极进行阴极保护,是一种有效防止金属腐蚀的方法 ,镁牺牲阳极广泛用于石油管道、天然气、煤气管道和储罐、冶炼厂、加油站的腐蚀防护以及热水器、换热器、蒸发器、锅炉等设备。目前镁合金已成为新型材料的发展方向之一。“十三五”规划指出镁合金材料重点发展方向为:航空航天用高强镁合金大尺寸复杂铸造件 ,高强耐热镁合金大规格挤压型材/锻件,3C产品用镁合金精密压铸件,大卷重、低成本、高成形性镁合金板带材,汽车轻量化结构件用镁合金精密压铸件等。同时,“十三五” 规划预测镁金属年增速7.1%,高于十种有色金属平均增速 4.1%。这是因为镁合金具有良好的轻量性、切削性、耐蚀性、减振性 、尺寸稳定性和耐冲击性,远远优于其他材料。这些特性使得镁合金广泛应用于航空航天、汽车、电子通信、 医疗、军事等领域。
针对镁合金腐蚀的特点,国内外的研究者提出了提高镁合金耐腐蚀性的主要方法:
①开发新的合金或提高镁合金的纯度 ;
②采用快速凝固技术;
③采用表面强化技术。
前两种方法主要是提高整体部件的耐蚀性,而后一种方法是在整体提高的基础上,通过不同方法在表面形成一种很薄的功能层来提高镁合金的耐蚀性。
镁合金的腐蚀形态包括全面腐蚀和局部腐蚀。通常而言,全面腐蚀将会造成局部腐蚀的产生,而局部腐蚀则更容易受到弱电解质和小阳极/阴极相对面积比的影响。局部腐蚀又分为电偶腐蚀 、点蚀 、丝状腐蚀 、应力腐蚀开裂与腐蚀疲劳等。
针对镁合金腐蚀的特点,表面强化技术是目前镁合金防腐蚀最常用的技术。而用于镁合金防护表面强化技术大致有阳极 氧化处理 、化学转化处理 、微弧氧化处理 、表面渗层 、电镀和化学镀处理 、热喷涂 、有机涂层 、气相沉积 、激光处理等 ,这些方法各有其优缺点。
镁及镁合金基体表面状态和清洁程度是保证镁合金强化处理后膜层质量的先决条件。如果基体表面粗糙、锈蚀或有油污存在,将不会得到光亮、平滑、结合力良好和耐蚀性高的膜层。实践证明,当膜层出现鼓泡、脱落、花斑和耐蚀性差等现象时,大多是因前处理不当造成的。因此,要想得到高质量的膜层,必须加强前处理的管理,按工艺要求严格执行。同其他金属前处理工艺相似,镁及镁合金基体前处理工艺一般主要有以下几个方面。 (1)粗糙表面的整平 包括磨光、抛光(机械抛光 、化学抛光和电化学抛光)、滚光和喷砂等。 (2)脱脂包括有机溶剂脱脂 、化学脱脂和电化学脱脂等。 (3)浸蚀包括强浸蚀、电化学浸蚀和弱浸蚀。 镁合金表面强化前处理工艺流程一般为: 由于镁合金表面状态不相同,其强化处理技术不同,对膜层质量的要求也不 一样,所以要根据镁合金基体的特性、表面状态及对膜层的质量要求,有针对性地选择适宜的镀前处理工艺。
在镁合金件成形过程中,工件表面或多或少附着有氧化 膜、脱模剂、离型剂 等杂质,这些杂质会在后续处理如微弧氧化、电镀等处理过程中脱落并进人电解液 ,影响电解液的寿命。此外,镁合金表面的自然氧化物疏松多孔和化学成分不均匀等特性也通常会导致后续表面处理结合力不佳。因而对镁合金表面进行适当的整平,如打磨、喷砂等预处理 ,则能很好地改善膜层的结合力和耐蚀性能等。对于镁合金的表面整平 ,目前应用较多的有喷砂、磨光等。
*由于镁合金硬度不高 ,在机械磨光工序中稍不注意就会破坏镁合金压铸零件表面的致密层,使铸件表层的微细裂纹、气孔外露,造成涂装表面出现起泡 、缩孔等缺陷,因此在对镁合金进行表面整平时 ,一定要严格控制整平工艺,确保不降低其耐蚀性能。此外,由于镁合金粉末燃点低 ,与氧的亲和力高 ,在喷丸、机械磨光过程中容易发生燃烧 ,甚至引起爆炸,因此操作时还应注意安全。
镁及镁合金部件在加工及存放等过程中,不可避免地会黏附各种油污,如矿物油、植物油和动物油等。而这些油污的存在通常会影响后续表面处理的质量。因此在对镁合金件进行表面强化处理前通常需要进行脱脂处理。
镁及镁合金化学性质活泼,只有在 pH>12的碱溶液中生成 Mg(OH):才趋于稳定,在其他水溶液中都不稳定。在纯净的自来水中浸泡也会发生腐蚀 ;在酸中,镁与 H+发生激烈的氧化还原反应,析出大量氢气与热量 ,会引起零件的过蚀 ,甚至发生自燃 、爆炸事故 。因而,目前生产上镁合金化学脱脂一般使用碱性脱脂法。这种方法的实质是依靠皂化和乳化作用 ,前者可以除去动植物油 ,后者可以除去矿物油。碱性脱脂溶液通常含有氢氧化钠 、碳酸钠、磷酸三钠、焦磷酸钠、硅酸钠以及其他表面活性剂等。
表1 镁合金碱性脱脂液组成及工艺
表2 乳化液脱脂工艺
将金属工件浸入酸、酸性盐和缓蚀剂等溶液中,以除去金属表面的氧化膜、氧化皮和锈蚀产物的过程称为浸蚀或酸洗。
镁化学性质活泼,镁合金在各种环境介质中的耐腐蚀性能都比较差 。为了提高镁合金材料的耐腐蚀性能,通常要对镁合金材料的表面进行强化处理,在其表 形成具有一定防腐蚀能力的覆盖层。镁合金常用的表面强化处理方法有化学转化处理、阳极氧化处理、电镀、化学镀 、有机涂层等。在进行这些处理之前 ,必须对镁合金材料进行浸蚀 (酸洗)除锈 ,以除去其表面的氧化物、腐蚀产物以及其他污染物 ,同时浸蚀还可以为后续表面处理提供更多的结合位点,增强镀层的结合力,提高其表面质量 。
表3 镁合金浸蚀液组成及工艺
镁合金自然氧化膜不致密,不能有效保护金属基体。此外,金属镁电负性很强,当与其他金属接触时,易发生电偶腐蚀,引起镁的加速溶解。这些都限制了镁合金的应用。因此,镁合金件出厂时都要经过表面处理以提高其抗腐蚀性能。通常最常用、操作简单的方法是化学处理(化学转化处理)或电化学处理 (即阳极氧化)。
表4 镁合金磷酸盐化学转化工艺
磷酸盐化学转化处理各成分的作用及影响
表5 镁合金磷酸盐一高锰酸盐化学转化工艺
磷酸盐-高锰酸盐化学转化处理影响因素
溶液组成和工艺参数的影响
工艺流程
为了进一步改善膜层质量,促进膜层生长,通常需要向微弧氧化电解液中加 入各种添加剂。目前研究的添加剂大多为可溶性盐或有机物,按照作用主要分为以下几类:
① 抑制试样表面尖端放电,提高电解液稳定性 。
主要有 KF、甘油、C3H8O3, Na2EDTA等。
② 有助于放电,提高溶液的电导率。
主要有 NaOH、KOH、NaF和 NaAl02 等 ;但添加剂的含量过高会抑制放电或引起严重的边缘放电。
③ 减少膜层的孔洞和裂纹,相应地提高陶瓷层的致密性 、耐蚀性能。
如 Na2W04、氢氧化钾、EDTA、蒙脱石、稀土盐、有机酸盐、二氧化硅、硅酸铝等。
④ 调整陶瓷层色彩的成分 ,如 Cu2+呈蓝色,Ni2+呈紫绿色,Cr3+呈绿色 。
表 常见镁合金的酸洗液及工艺 表 镁合金活化液的组成及操作工艺 表 不同主盐体系化学镀镍液配方及工艺条件 图 不同主盐体系的镀层厚度随时间变化的曲线 图 不同主盐镀镍体系所得的镀层的微观形貌 表 不同稳定剂对化学镀镍液稳定性和沉积速度的影响 图 温度对化学镀镍沉积速度和镀层孔隙率的影响
免责声明:本网站所转载的文字、图片与视频资料版权归原创作者所有,如果涉及侵权,请第一时间联系本网删除。
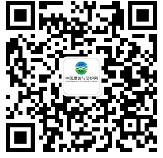
官方微信
《腐蚀与防护网电子期刊》征订启事
- 投稿联系:编辑部
- 电话:010-62316606
- 邮箱:fsfhzy666@163.com
- 腐蚀与防护网官方QQ群:140808414